Understanding Petroleum vs Water-Based Lubricants A Scientific Analysis of Material Compatibility in Design Applications
Understanding Petroleum vs Water-Based Lubricants A Scientific Analysis of Material Compatibility in Design Applications - Material Interaction Between Water Based Lubricants and Metal Surfaces at 100 Celsius
At 100°C, water-based lubricants can struggle with metal surfaces, often not working as well as oil-based options. Their low thickness and the tendency to cause rust are frequent complaints. Although they have advantages like low cost and good cooling, water's natural properties aren't well suited for metal lubrication, especially when it's hot. Current investigations focus on mixing additives, including ionic liquids, to make them work better in metal to metal contact. How these mixtures flow and behave under different conditions is crucial. Also, how they interact with metal directly affects corrosion and performance, so that needs to be studied carefully. The rate at which water evaporates at these temperatures, how well it sticks, and its general compatibility with the metal surfaces involved become key factors in evaluating these formulations. Different metals, like steel, react differently to water based lubricants adding another layer of complexity. It is hard for water to form a protective layer due to its low thickness, and these water-based cutting fluids struggle with corrosion when in contact with metal. Ongoing development in additive technology is critical to overcome such limitations, hopefully improving performance in industrial situations.
When water-based lubricants meet metal surfaces at 100°C, a series of events unfold that demand careful consideration. The heightened temperature often sparks hydrolysis, which can break down the lubricant itself, diminishing how well it works. The viscosity of water-based lubricants is also sensitive to temperature changes and this means a significantly different lubrication regime compared to more temperature-stable, petroleum-based options, potentially leading to increased friction and wear. Furthermore, some metals like aluminum and copper, are known to react unfavorably with water-based lubricants, and this can result in unwanted corrosion that compromises both the metal surface and the lubricating film. The additives included in these water-based solutions, designed to improve their characteristics (e.g. thickness, surface tension), also add a variable to how well these lubricants actually work, changing thermal stability and friction reducing capacity at high temperatures. Another thing is the generally lower boiling point of water, which unless engineered to handle the heat, can severely limit their effectiveness due to quick evaporation. The metal surface's own condition plays a part; it's not just the lubricant alone at play, its roughness or level of contamination can make significant changes in how the lubricant interacts with the metal. The decomposition process of water-based lubricants at these elevated temperatures can also create gaseous byproducts; this can bring about localized pressure fluctuations that are bad for lubrication in operation. And then there's the observation that water appears to penetrate the naturally occurring protective oxide layers on some metals, thereby reducing their intended protection and potentially causing greater adhesive wear when a water-based lubricant is in use. Experiments seem to indicate that water-based lubricants do not always perform so well when the metal parts that have lower thermal conductivity is involved; there is not enough heat dissipation which leads to possible overheating and material failure. Overall, it is clear that temperature management is critical when one is using water-based lubricants in these circumstances. Failure to adequately control the temperature can lead to severe problems in the lubrication systems of machinery.
Understanding Petroleum vs Water-Based Lubricants A Scientific Analysis of Material Compatibility in Design Applications - Engineering Constraints of Viscosity Ranges in Petroleum Based Oils from -40 to 200 Celsius
The engineering constraints of viscosity in petroleum-based oils across the -40°C to 200°C range are considerable and affect both lubrication and fluid movement. Crude oil's viscosity is a crucial factor that governs its flow through pipelines and porous subsurface formations, directly impacting extraction and transportation. While lower viscosity at higher temperatures might seem beneficial, predicting the behavior of heavier oils, and especially calculating their viscosity, remains difficult. Current mathematical models and methods are trying to improve viscosity prediction, particularly for mixed heavy oils, which is necessary given different transport requirements. In the end, accurate handling and testing become very important to avoid false measurements and ensure performance.
The viscosity of petroleum-based oils shows a huge range over a temperature span from -40°C to 200°C, with values potentially going from approximately 1,000 cP at the low end to less than 10 cP at the high end. This extreme variability is a major consideration in oil selection for a specific operating temperature. It's not just temperature that is the culprit, though. The exact chemical makeup of the oil, specifically the different types of hydrocarbon chains that form each base stock, also significantly affects its viscosity characteristics. The way these chains are arranged and their size plays a significant role. Some oils have a higher viscosity index (VI), typically from 80 to 140 and above. Oils with a higher VI are preferable if temperature swings are expected because they are better at keeping their viscosity more stable. Engineers also must consider the potential for shear thinning when these petroleum-based oils are incorporated into designs. In conditions with lots of mechanical shearing, like in some bearings, the oils can suddenly become less viscous and that causes problems for load bearing ability and film stability. Also, we have to think about pour point, the low end temperature where the oil becomes too hard to flow. For a lot of oil products this can be anywhere from -15°C to -30°C or even higher. That means they're essentially useless if ambient conditions reach that temperature without proper care. And when you raise the temperature to over 150°C, the constituent molecules of petroleum oil itself start to decompose, usually leading to viscosity drops and eventual failure due to the increase of vapor pressure and the formation of carbon residue. If you push the oil even further then one starts to see "coking." At this point you end up with solid build up. These build-ups clog oil lines, seriously affecting the fluid flow. These oils have to maintain viscosity despite pressure changes. For applications in high-pressure this is critical, as high pressure can sometimes normalize flow, but sometimes may make it hard to keep that lubrication film stable. Finally there is the additives; viscosity modifiers that adjust how viscosity changes with temperature. These compounds can change their effectiveness at different points, further optimizing the fluids' performance in specific conditions. There's also the issue of thermal degradation which might accelerate the growth of acidity and the generation of sludge, and the accumulation of those kinds of byproducts will drastically affect both the viscosity and overall stability of the oil; therefore there needs to be constant monitoring and timely replacements to ensure the lubrication system can work.
Understanding Petroleum vs Water-Based Lubricants A Scientific Analysis of Material Compatibility in Design Applications - Chemical Degradation Analysis of Both Lubricant Types Under High Pressure Applications
In high-pressure applications, the chemical stability of both petroleum and water-based lubricants is seriously challenged, affecting how well they work and how long they last. Oil-based lubricants, particularly, are subject to degradation through oxidation. This process speeds up when high temperatures and humidity are present, potentially leading to the creation of byproducts that can hinder the lubrication process. Water-based lubricants, on the other hand, tend to break down due to hydrolysis, and high temperatures can make them evaporate more quickly. Both these factors lower their viscosity and may cause corrosion of the metals they are supposed to be lubricating. Further, the specific compounds added to these lubricants to enhance their characteristics can interact differently in different environments, sometimes making the breakdown process faster or changing their overall behavior. It is essential that these degradation pathways are taken into account so the right lubricants can be chosen for high-pressure situations while still ensuring the various materials involved will be compatible and without any unintended wear and tear.
When considering how lubricants behave under high pressure, it's apparent that both petroleum and water-based types degrade quite differently. Petroleum lubricants tend to form carbon-based residues under duress, whereas water-based lubricants are more prone to hydrolytic breakdown, creating distinct degradation products, and each path introduces unique concerns that may impact overall performance of systems. High pressure does have a distinct effect on viscosity of petroleum oils. They often become less viscous due to shear thinning and this change impacts how well they lubricate, and the precise behavior we observe seems heavily dependent on the specific oil's makeup. Water-based lubricants tend to struggle more with thermal stability than their petroleum counterparts and with pressure adding another stressor they often degrade much more easily when exposed to the high temperatures coupled with pressure, quickly reducing their effectiveness in a lubrication system. Interestingly enough, additives can play a significant role in how quickly lubricants fail under these high-pressure circumstances. Certain additives in petroleum oils can boost thermal stability but even with clever formulation techniques in water-based solutions, one could merely be shifting the failure mode. The failures due to the lubricant chemistry changes directly lead to unexpected wear patterns on metal surfaces and this shows the need for regular testing in high pressure conditions. The formation of carbon-based residues is typical for failed petroleum based lubricants. However with water-based systems one is often observing more gaseous breakdown products that can impact the overall lubrication and can possibly destabilize the system. Water-based lubricants also bring about an issue, where their reactions with some metals, like aluminum or copper, often worsen when there is high pressure, with corrosion becoming more of a concern compared to petroleum oils. The creation of protective films during lubrication operations seems where the petroleum based oils typically excel at; they often can maintain a stable film under a variety of conditions. In comparison, water-based ones seem to need additives to do that, particularly in pressurized applications. Some studies indicate that water-based lubricants might exhibit something called “false lubrication” under pressure, where instead of reducing friction it actually increases it, particularly in systems that are carrying heavy loads. Furthermore, the degradation itself does not always depend on temperature or pressure alone, the mechanics of wear itself can worsen the chemical breakdown, and whether loading is static or dynamic seems to affect how fast both types of lubricant degrade over time.
Understanding Petroleum vs Water-Based Lubricants A Scientific Analysis of Material Compatibility in Design Applications - Molecular Structure Impact on Wear Protection Between Oil and Water Based Solutions
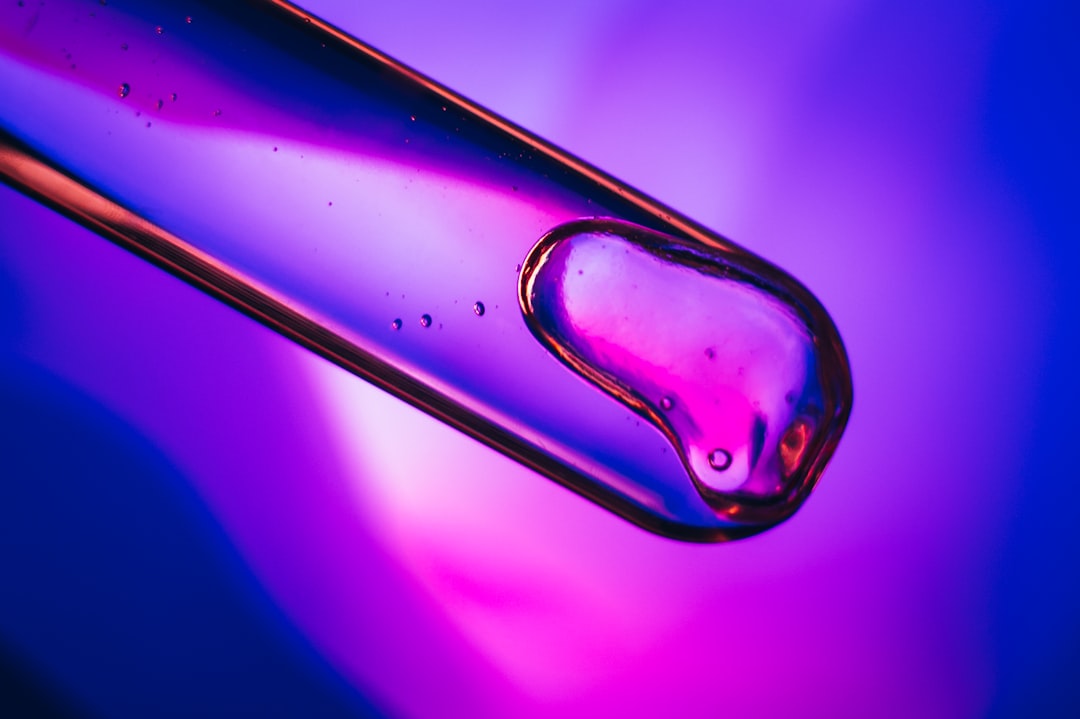
The molecular architecture of lubricants is a key factor in how well they protect against wear, particularly when contrasting oil-based and water-based options. Oil-based lubricants often utilize the structure of their hydrocarbon chains to create stable lubricating films that are resilient across different temperatures and pressures. These chains, through their length and shape, provide a strong and protective interface. On the other hand, water-based solutions, often made up of lighter molecules, struggle to form equivalent protective layers on metal, particularly when it’s hot. These structural differences at a molecular level are a fundamental reason why oil-based lubricants often outperform water-based solutions in high-stress situations. The way surfactants interact with the other parts of a water-based lubricant plays a big role in how stable and effective those emulsions are. This shows how crucial it is to explore how to fine-tune these formulations in order to improve how well they can protect against wear. This difference in molecular structure needs more investigation, as understanding the molecular details is key to developing more efficient and environmentally acceptable methods of lubrication for different uses.
The molecular arrangement within a lubricant is a key factor in its ability to protect against wear, and this is particularly true when comparing oil and water based solutions. The relatively weak cohesive forces of water molecules, when compared to the strong intermolecular bonds of oils, generally result in a much less stable and often thinner lubricating film when water is involved. Consequently, we typically observe water-based lubricants struggle with large temperature changes, often becoming too thin at higher operating points, and thus not providing adequate protection to metal parts. This issue is further compounded as water can encourage the breakdown of some of the lubricants’ components, leading to the degradation of both the liquid itself and also a change of the wear properties of the surfaces it is intended to protect. There can be issues with metals, like aluminum or copper which may react unfavorably in the presence of water. The additives introduced to modify the behavior of these water based lubricants, need very careful consideration as the arrangement of these molecules may affect performance, especially when things get hot or highly pressurized, with the result being a faster breakdown and less protection. Oils tend to keep a more stable protective film, particularly under high load; but the cohesive and adhesive properties of water-based lubricants can make them less effective, resulting in greater wear and higher friction under stress. The inherent nature of water in water based solutions also has further limitation as water readily boils at 100 degrees centigrade. The quick evaporation in high pressure systems can reduce the amount of lubricant available, particularly when metal parts reach extreme temperatures. It has been noted that water-based lubricants do not necessarily reduce friction, and in some cases might increase it, an effect called "false lubrication". Under high pressure the lubricating film cannot be formed sufficiently which makes them less reliable than oil in this aspect. The very chemistry of water-based solutions also contributes to corrosive tendancies which may not only oxidise metals but also create gaseous byproducts, all of which affect both the metal parts and the lubricant properties. While some petroleum based oils may exhibit shear thinning, which increases their lubricating qualities by reducing the viscosity at points of stress, the water-based lubricants, do not appear to benefit from this. They seem to fundamentally lack the same molecular response under duress which oils appear to enjoy. There's the important issue of compatibility which is another point of comparison; the molecular nature of water may interact in very different ways when in contact with metal parts when compared to oils. As oil often creates an expected protective layer, water can at times penetrate these oxide layers leading to more adhesive wear when water based lubricants are used in some systems.
Understanding Petroleum vs Water-Based Lubricants A Scientific Analysis of Material Compatibility in Design Applications - Temperature Stability Comparison Through Extended Duration Testing at 150 Celsius
The temperature stability comparison during prolonged testing at 150°C highlights key performance disparities between petroleum and water-based lubricants. While high temperature resistance is important for both lubricant categories, petroleum-based options typically show superior resilience against heat related degradation; they tend to maintain their viscosity and lubricating properties more effectively than water based choices. At elevated temperatures, water-based lubricants are prone to rapid evaporation and breakdown via hydrolysis, resulting in unpredictable performance and the potential for metal surface corrosion. There have been efforts to boost thermal stability using nanoadditives in water-based solutions but these new combinations often still can't quite match the performance of traditional petroleum lubricants, particularly in high pressure applications. An in-depth understanding of thermal behavior at 150°C is crucial to decide the optimal type of lubricant for specific mechanical and material needs.
Let’s dig into how these lubricants handle things at 150°C, a temperature where we start seeing some critical changes. Many oil-based lubricants start to fall apart here, turning into carbon goo and greatly reducing their ability to lubricate. This is not ideal for a machine that’s supposed to be running smoothly.
Adding more pressure to the mix, things get even more interesting. Both oil and water-based options tend to break down, but they do it in different ways. Oils, they generate these carbon residues. On the other hand, water-based lubricants often face a kind of chemical breakdown through hydrolysis, which tells you right away how important it is to check them under the actual conditions they’ll be working in.
Viscosity, which dictates how thick the lubricant is, shifts significantly as the temperature rises. It becomes critical to measure this properly as a seemingly small shift at high temperatures might have very large impacts. For instance the viscosity of petroleum lubricants can shift from a thick syrup to a very thin oil; almost a liquid with water like qualities.
When looking at water-based options, the simple fact that water boils at 100°C is a big problem. At 150°C, you risk the lubricant evaporating off real quick, which does nothing to protect the metal surfaces against friction and wear. So it is not surprising to see why we have to add so many components to water-based options to help them better keep their lubrication properties, and even with that it does not always resolve the issues.
Another problem with water-based options is their nasty habit of not playing nice with all metals, like aluminum and copper which have a strong tendency to corrode, making material selection a complex endeavor.
Those carefully chosen additives that are often used for improved properties also react differently when things get intense. In water-based fluids they may worsen their performance at high temperature; while in oil-based lubricants they might boost thermal stability at the expense of producing harmful byproducts that might be undesirable for the system.
There is this weird thing called "false lubrication" that water-based lubricants might undergo, where they seem to increase friction under high pressures; rather than reduce it. This unpredictable behavior demands thorough and cautious testing during development, as not much would be gained if one designs a system only to have the lubricant destroy it.
If one looks at things from a molecular point of view, oil-based lubricants appear to have an advantage, as the long hydrocarbon chains can create strong and stable lubricating films. Compare that to the more fragile layers produced by water-based solutions, and one starts to appreciate the inherent limitations of the water-based solutions.
And we also cannot forget the off-gassing. As things heat up, you can get some interesting byproducts appearing in a gaseous form. That also will change how the lubricant performs. So when deciding how long a lubricant will last at such temperatures, these factors need to be carefully evaluated.
Finally, whereas petroleum-based options tend to change their viscosity under shearing conditions— a behavior known as "shear thinning", and a positive quality, allowing for better lubrication, water-based solutions don't usually exhibit the same kind of molecular adaptability. Which all in all highlights the performance ceiling we might expect from the water-based solutions, especially in dynamic loading scenarios.
Understanding Petroleum vs Water-Based Lubricants A Scientific Analysis of Material Compatibility in Design Applications - Corrosion Prevention Capabilities in Marine Engineering Applications
Corrosion is a major concern for marine engineering, since the environment rapidly causes materials to degrade. Preventing it is crucial, so using things like corrosion-resistant alloys and protective coatings is standard practice. Newly developed coatings for marine settings are intended to follow tough rules but still need regular checks after application. It's very important to understand how different materials react to each other in seawater, known as galvanic corrosion. The wrong mix of materials can worsen corrosion in a marine environment. As new materials and approaches are being developed, continued research into how environmental conditions impact these structures is absolutely vital for ensuring they last and are safe to use.
In marine settings, corrosion induced by water-based lubricants isn't solely a surface issue; it involves complex electrochemical reactions. Dissolved salts and impurities turn water into a rather aggressive medium when compared with oil based solutions. Furthermore, when we consider that the presence of two or more dissimilar metals in the system can introduce a galvanic corrosion risk, where water then forms an active electrical cell. The presence of a water-based lubricant between two metal components then further accelerates the wear process and therefore needs to be controlled. Oil-based lubricants do have the ability to generate a kind of shield which we often refer to as a tribofilm, when exposed to high temperatures. However, water-based versions can rarely match that performance; they simply fail to retain their integrity when we load them with pressure or heat, and then they leave the mechanical parts much more open to wear and damage. Even the inhibitors we add to water-based lubricants have drawbacks, as they seem to depend very heavily on both the water's pH balance and its salinity. Certain additives can easily degrade when faced with such variance which introduces yet another source of complexity in how to make them effective in a marine setting. Water when aerated will intensify localized corrosion processes like pitting which is really bad if you have metals like stainless steel and aluminum. And this localized damage can often be worse if you are using water-based lubricants compared to oil versions. Water, while having a very high thermal conductivity, does not help much at high operating temperatures since viscosity drops to a point where heat from metal surfaces is not properly dissipated. And thus can lead to damage when this localized heating is combined with mechanical stress. When these water-based options are exposed to high pressures in marine operations, there's also an increased chance that the lubricants themselves might breakdown in a process called "hydrolysis". It also tends to separate the metal parts, and that then further promotes corrosion and hinders their intended purpose. Water based lubricants have a lower flash point and they are more volatile compared to petroleum versions. This combination might form flammable byproducts at very high temperatures which then poses a risk in confined areas. Furthermore, water-based lubricants when used on rough or imperfect metal surfaces cause increased friction and wear. They simply cannot manage surface irregulaties in the same way that oil based lubricants do. Finally, we also have to worry about how the lubricant itself is breaking down. Often water-based systems produce byproducts which are corrosive, acids which will damage not only the lubricant, but the metal components around it too. All of that means that systems using such lubricants might fail sooner than anticipated in the marine environment.
More Posts from patentreviewpro.com: