The State of Bicycle Metal Adaptor Innovation for Performance
The State of Bicycle Metal Adaptor Innovation for Performance - Additive Manufacturing Shaping Metal Adaptor Design
Additive manufacturing is fundamentally altering the possibilities for designing metal adaptors in bicycle components, moving beyond the constraints of traditional fabrication methods. This technology allows for the creation of highly complex internal structures and organic shapes that were previously unattainable, directly impacting areas like weight reduction through advanced topology optimization and enabling a degree of customization specific to performance needs or individual rider anatomy. While promising novel lightweight and integrated designs that can enhance performance characteristics, the practical implementation requires deep understanding of process parameters, as variations can significantly influence material properties and structural integrity. The journey from complex digital design to reliable physical part still navigates challenges related to material consistency, process scalability, and achieving desired surface finishes and tolerances without prohibitive post-processing. Consequently, while AM offers a powerful new tool for designers to innovate, fully capitalizing on its potential for high-performance bicycle adaptors demands continued development in materials science, process control, and the integration of design-for-additive manufacturing principles.
Additive manufacturing is fundamentally reshaping how we approach the design of metal adaptors for performance bicycles. It’s not just about making the same old parts differently; the technology allows for the realization of geometries and functionalities previously confined to theoretical models or simply impossible to manufacture economically.
Consider the internal architecture of these adaptors. The ability to selectively solidify metal powder layer by layer means we can now embed intricate, often non-orthogonal, internal structures or precisely engineered void spaces. This moves beyond simple hollowing and into the realm of creating optimized internal lattices or cellular structures designed to minimize mass while attempting to maintain or even improve torsional rigidity and strength under specific load cases. Validating the real-world fatigue life and failure modes of these complex internal architectures, especially under dynamic cycling stresses, remains a critical area for ongoing research.
Furthermore, the integration with advanced computational design tools, particularly topology optimization, is driving forms that appear alien compared to conventionally machined parts. Algorithms dictate where material is needed based on simulated load paths, resulting in organic, flowing shapes that prioritize structural efficiency over manufacturing simplicity (in the traditional sense). While these shapes can theoretically place material precisely where required, ensuring reliable print fidelity for delicate features and managing the inherent residual stresses in such complex forms presents significant manufacturing and validation challenges.
The consolidation of functions within a single component is another notable shift. Engineers are exploring designs that integrate features like internal hydraulic line routing channels, intricate sensor mounting points with specific orientations, or complex cable stops directly into the body of the adaptor during the printing process. This potential reduction in part count simplifies assembly and eliminates some interfaces, but raises complex questions about ensuring internal channel cleanliness and integrity, as well as the practicality and cost-effectiveness of repairing a single, highly integrated, failed component.
There's also the intriguing possibility of creating parts with non-uniform material properties or structures within a single print. By altering laser parameters, powder composition (in some processes), or internal infill strategies across different regions of the part, designers aim to tailor localized stiffness, damping, or energy absorption characteristics. Achieving precise, predictable, and repeatable transitions between these functionally graded zones, and understanding how these gradients influence overall mechanical performance and post-processing requirements, is still a significant materials science and process control puzzle to solve.
Finally, the geometric freedom inherently offered by AM enables the creation of adaptors meticulously tailored to interface specific, sometimes disparate or legacy, components or to precisely fit unique, non-standard frame geometries. This capability facilitates highly customized, performance-focused builds that would be cost-prohibitive or impossible with traditional machining which often requires specific tooling for each shape variant. However, the engineering effort required for designing, simulating, and rigorously validating each unique custom part, rather than relying on tested standard components, can be substantial.
The State of Bicycle Metal Adaptor Innovation for Performance - Performance Gains Through Metal Adaptors Beyond Frame Structures
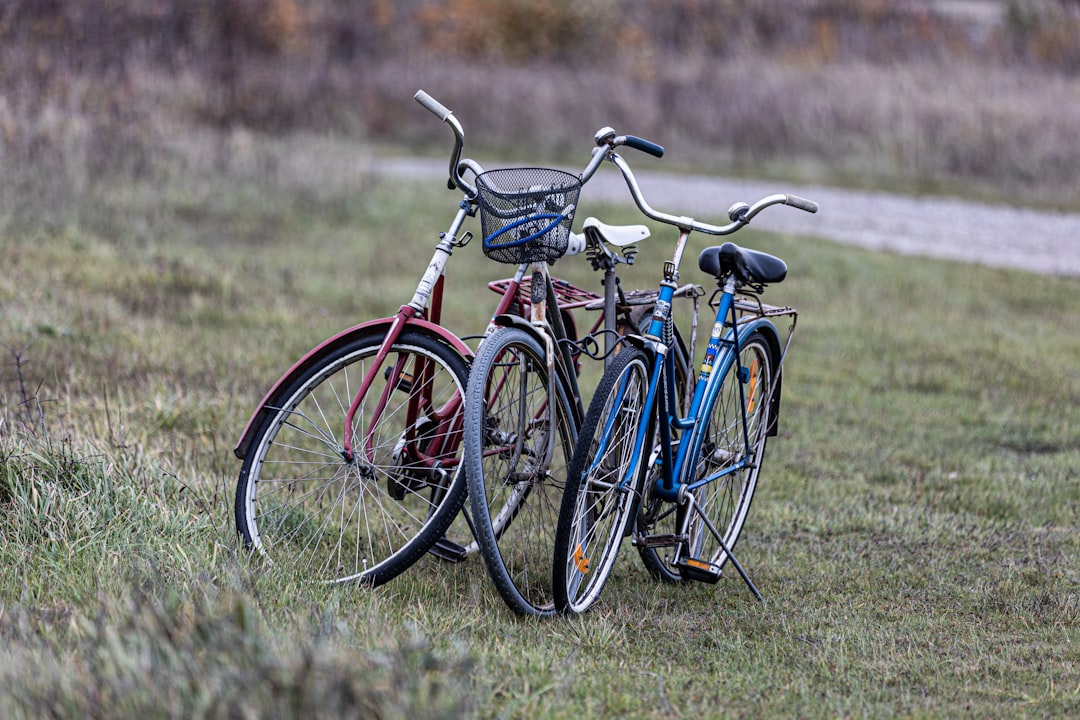
The push for enhanced bicycle performance is increasingly targeting metal adaptors located away from the main frame structure. This innovation leans heavily on advanced materials, particularly engineered metal composites, and sophisticated manufacturing processes, including certain additive techniques. The goal is to precisely tailor material properties and create complex geometries in critical connection points like dropouts, suspension linkages, or component interfaces. By doing so, designers aim to improve local stiffness, manage specific load paths more effectively, optimize weight distribution beyond the main tubes, and potentially even introduce nuanced damping characteristics. However, the path from advanced concept to reliable component in production presents significant challenges. Ensuring the consistency and predictability of novel composite properties, mastering the fabrication of intricate forms, and rigorously validating the long-term performance and durability under the dynamic stresses these peripheral components endure remain critical hurdles. Ultimately, realizing meaningful performance gains in non-frame metal adaptors demands a delicate balance between exploring material and manufacturing frontiers and proving their real-world robustness and effectiveness.
Here are a few observations regarding the potential for performance gains offered by metal adaptors in bicycles, extending their impact beyond primary frame structures, based on current discussions and developments as of late June 2025:
1. In cockpit areas, it appears metal adaptors, often leveraging the geometric flexibility of newer manufacturing techniques, are being explored to create more aerodynamically integrated and complex shapes around stem and handlebar interfaces. The aim is seemingly to smooth airflow in a critical frontal zone, although quantifying the real-world performance benefit for typical riding speeds and conditions remains an area demanding rigorous, independent verification.
2. For full-suspension designs, there's interest in how linkage adaptors, potentially with complex internal geometries, might allow for finer tuning of kinematic curves. The idea is that precisely designed metal components here could influence wheel path and leverage ratios in ways that optimises suspension behaviour for specific terrain or rider inputs, theoretically boosting traction or pedalling efficiency at certain points in the travel, provided manufacturing tolerances are tightly controlled and validated.
3. Beyond mere dimensional compatibility, some novel metal interface adaptors, such as those at the bottom bracket or hub junctions, are being designed with engineered stiffness profiles. The intent is to influence local rigidity and power transfer characteristics through carefully distributed material, moving beyond simple 'strong enough' and into nuanced structural response, though how perceptibly this translates into rider performance on the road or trail is still being assessed in varied real-world scenarios.
4. Reports suggest that engineered microstructures, potentially embedded within metal adaptors for components like seatpost clamps or saddle rails, are being investigated for their capacity to influence vibration transmission. The theory is that such structures could target and attenuate specific frequencies of road chatter, aiming to improve rider comfort and potentially reduce fatigue over long distances, provided the effect is significant and durable under cycling loads.
5. The increased design freedom offered by advanced metal fabrication is facilitating the creation of highly specific adaptors that allow previously incompatible, high-performance component standards to be used together on a single bike. While undoubtedly enabling greater customization and potentially repurposing of desirable parts, labelling this solely as a 'high-efficiency' gain over established, standard interfaces warrants a critical look at the overall system compromises introduced by the adaptor itself.
The State of Bicycle Metal Adaptor Innovation for Performance - Material Properties and Performance Impact of Metal Adaptors
Efforts to enhance the performance of bicycle adaptors are increasingly centred on manipulating material properties. This involves delving into advanced material systems, notably engineered metal composites, to achieve specific performance characteristics beyond simply adequate strength. The goal is to tailor traits like stiffness, weight distribution, and vibration response within components, particularly those situated away from the primary frame structure where localized stresses and dynamic inputs are critical. By carefully selecting materials and integrating sophisticated manufacturing approaches, designers aim to create adaptors with internal structures or property gradients intended to optimise traits such as power transmission efficiency or the absorption of road or trail impacts. However, integrating these novel material systems into production-ready components presents substantial hurdles. Ensuring the consistent mechanical behaviour of complex composites and validating their long-term resilience and predictable failure modes under realistic cycling loads necessitates extensive and rigorous testing. The actual performance advantage derived from these material innovations in metal adaptors will ultimately depend on overcoming manufacturing challenges and demonstrating reliable, repeatable gains in real-world cycling environments.
Here are some considerations regarding the intrinsic material properties and their influence on the functional performance of metal adaptors in bicycles:
1. The fundamental modulus of elasticity inherent to the specific metal alloy chosen sets the ultimate limit on its stiffness. While clever geometry and structural design can optimize how forces are distributed, the material's native resistance to elastic deformation dictates the potential for responsive power transfer or predictable load bearing – a core mechanical performance metric distinct from brute strength.
2. Component fatigue life is often a more critical design factor than static yield strength, especially for adaptors experiencing numerous load cycles. The material's inherent endurance limit, defining the stress level below which it can theoretically withstand infinite cycles, dictates the long-term reliability and safety margin under realistic riding conditions, making material selection based on cyclic performance paramount.
3. Resistance to environmental corrosion, including surface oxidation and galvanic reactions, directly impacts the long-term structural integrity and function of metal adaptors. Despite surface coatings, aggressive environments (road salt, moisture, sweat) can lead to material degradation, potentially weakening load-bearing areas or compromising precise interfaces over time, requiring careful alloy choice and maintenance considerations.
4. Subtle variations and discontinuities within the material's internal structure – such as porosity from casting, non-metallic inclusions, or incomplete fusion in additive processes – can act as stress concentration points. These material imperfections can significantly lower the actual fracture toughness and fatigue strength compared to idealized material properties, posing a challenge for manufacturing consistency and performance predictability.
5. The specific gravity, or density, of the metal alloy fundamentally dictates the baseline mass for any given volume of material. While innovative design aims to use material efficiently, the inherent density of aluminum, titanium, steel, or magnesium alloys sets a lower bound on achievable adaptor weight, forcing critical trade-offs against desired strength and stiffness requirements in performance-driven components.
The State of Bicycle Metal Adaptor Innovation for Performance - Key Players Exploring Metal Adaptor Innovation
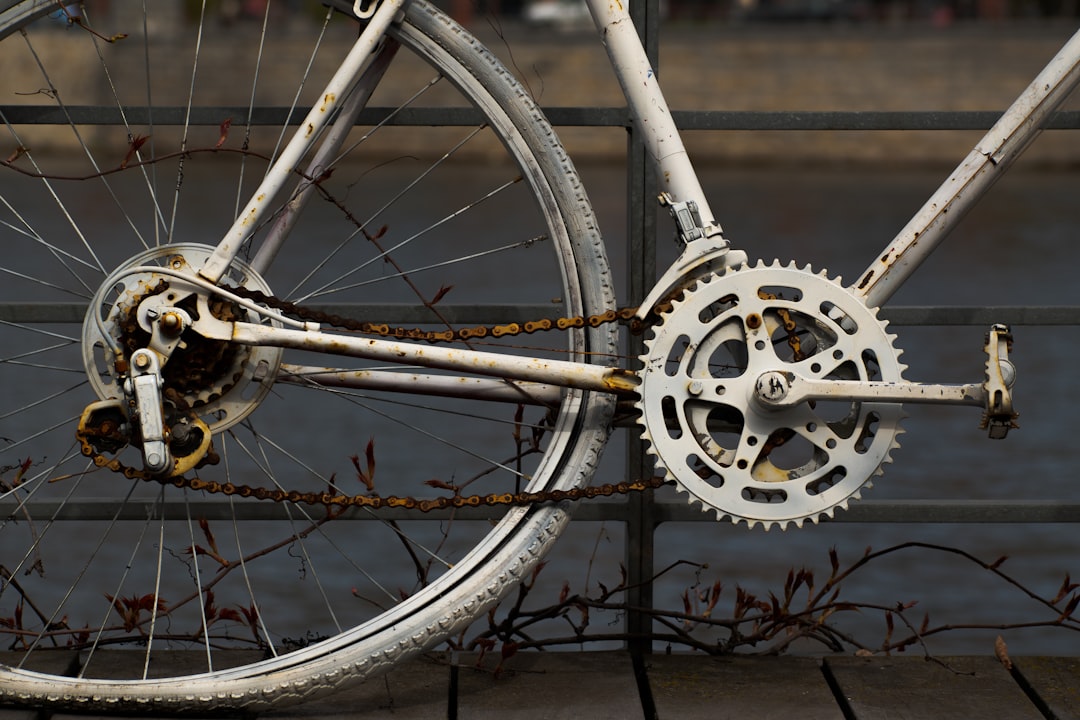
As of late June 2025, the focus within certain parts of the bicycle industry is sharpening on the exploration of metal adaptor innovation, moving beyond the broader adoption discussions. This isn't just about implementing established technologies, but about specific entities actively pushing the boundaries on performance-critical components situated off the main frame. Their efforts often concentrate on refining designs achievable through advanced processes like additive manufacturing, aiming for more precise control over localized stiffness, weight, and stress distribution in areas like dropouts, suspension interfaces, or component mounts. The drive is towards extracting even marginal gains through tailored metal components, although the true impact and reliability of these highly specific designs under diverse real-world conditions remain central points of validation and ongoing critical assessment for those involved.
It is being observed that some significant players in component development are starting to integrate computationally intensive methods, often labeled as AI or machine learning, to explore adaptor geometries. These tools aren't just optimizing existing shapes but attempting to generate forms optimized for specific load cases and property targets (like stiffness or mass reduction) that look quite different from conventionally designed parts. The claim is they explore design spaces a human might miss, though validating the practical performance and manufacturability of these radical, algorithmically derived shapes remains a significant engineering task.
There's a noticeable trend among some established bicycle manufacturers, who previously relied on external suppliers for metal components, to vertically integrate by acquiring and operating additive manufacturing capabilities themselves. This move, particularly involving powder bed fusion techniques like selective laser melting, appears motivated by a desire to compress design-to-prototype cycles for adaptors and other complex parts, enabling quicker iteration on performance concepts directly within their engineering teams. The practical benefits of this integration against the investment and specialized expertise required is an ongoing evaluation for these companies.
Beyond the more visible external adaptors, a substantial amount of development effort is reportedly being directed by some major industry players towards designing and producing intricate internal features within larger components using advanced metal processes. This includes exploring ways to reliably embed mounting points for sensors or integrate complex, clean channels for internal routing of hydraulic lines or other fluids directly during manufacturing, with the aim of achieving small, localized performance or integration benefits at a system level, though ensuring functionality and accessibility for maintenance or repair on these integrated internal elements poses its own set of problems.
Interestingly, tackling one of the persistent challenges with metal additive manufacturing – the required post-processing for critical tolerances and surface finish, especially on complex internal features – is driving collaborations between some bicycle engineering teams and firms specializing in automated handling and robotics. They appear to be investigating tailored robotic finishing methods to address these specific needs for high-performance adaptors, suggesting that manual post-processing is seen as a significant bottleneck for scaling up production of intricate additively manufactured parts.
A particularly interesting line of inquiry being pursued by some innovators involves fabricating metal adaptors that are not monolithic alloys but feature spatially varied material properties. This might involve co-sintering different metal powders in distinct regions of a part or incorporating other materials or reinforcing structures during the additive process. The theoretical goal is to engineer localized stiffness, damping, or strength characteristics within a single component in ways not achievable with a uniform material, presenting complex challenges in process control, material science, and validating the long-term interface stability between different material zones.
More Posts from patentreviewpro.com: