Understanding Glass Bottle Refinement Advanced Manufacturing Techniques and Quality Control in 2024
Understanding Glass Bottle Refinement Advanced Manufacturing Techniques and Quality Control in 2024 - Digital Twin Integration Streamlines Glass Bottle Manufacturing Process Flow
Integrating digital twins into glass bottle production offers a fresh approach to streamlining the manufacturing process and enhancing quality control. Essentially, digital twins are virtual copies of the physical production line, allowing manufacturers to observe operations in real-time. This real-time visibility enables faster adjustments, leading to improvements in both efficiency and product quality. The capability to foresee potential equipment failures through predictive analytics is a significant benefit. Moreover, this technology reduces the manual labor typically involved in process engineering, by supplying comprehensive simulated data that informs better decision-making.
In a landscape where consumer demands are rising and product lifecycles are shrinking, the digital twin framework presents a compelling strategy for improving operational flow. As part of the broader Industry 4.0 shift, digital twin integration is positioned to reshape the future of glass bottle manufacturing, promoting a new era of process refinement and quality control in 2024. While the approach has promise, it is important to remember that it’s still relatively new in its application and the long-term impact on costs and benefits are yet to be fully realized.
Virtual representations of physical systems, like digital twins, are becoming increasingly important in streamlining manufacturing processes. In glass bottle manufacturing, these digital twins essentially mirror the entire production line, allowing us to run simulations and analyze data without physically altering the production setup. This saves both time and resources that would otherwise be spent on potentially costly trial-and-error methods.
These virtual models can predict and potentially prevent equipment failures, reducing downtime significantly. Some researchers have found this approach can cut downtime by as much as 20%, suggesting that predictive analytics based on these twins are quite powerful. Furthermore, they offer a path towards making the production process more energy-efficient. By dynamically adjusting parameters based on the virtual environment, manufacturers might realize improvements in energy use, with potential gains of around 30%. It's fascinating how these simulations allow for a more precise fine-tuning of production parameters, exceeding the limitations of historical data alone.
The continuous monitoring of key manufacturing parameters facilitated by digital twins is especially helpful for maintaining consistent product quality. We can monitor things like glass thickness and structural integrity with greater precision, resulting in more uniformity in the final product. This ties into the idea that we can apply machine learning within the digital twin environment to anticipate maintenance needs. This allows us to improve operational efficiency by reducing unexpected equipment failures.
The ability to simulate various furnace conditions, using the digital twin, is a particularly useful feature for product development. It allows manufacturers to experiment with different glass materials and formulations without risking the existing production line. This approach fosters innovation and lets manufacturers evaluate new products in a controlled and simulated setting.
In a dynamic market, the ability to quickly iterate new designs is key. Digital twins provide that capability. The agility provided by these systems is becoming more important in today's faster-paced markets. They give manufacturers the capacity to make adjustments to the production process on the fly, ensuring that they can respond to evolving market demands and consumer preferences efficiently.
The digital twin's scope extends beyond the production facility itself. By creating simulations of the entire supply chain, manufacturers can enhance logistics and distribution strategies based on the simulated forecasts provided by the system. The ability to model supply chain logistics is a powerful tool for improving efficiency throughout the entire production and delivery lifecycle.
The use of digital twins empowers manufacturers to validate new product designs in the digital realm before physical production starts. This allows for early identification and correction of potential defects, minimizing the risks associated with introducing new designs.
This integration of digital technologies brings with it a powerful potential for research and development. The massive amounts of data generated by these digital systems can be mined and utilized to explore different manufacturing techniques, potential new materials, or refine processes long before we step into a physical production environment. It's a testament to how digital tools can be leveraged for pushing the frontiers of knowledge and process innovation.
Understanding Glass Bottle Refinement Advanced Manufacturing Techniques and Quality Control in 2024 - Machine Vision Systems Detect Microscopic Glass Surface Defects at 120 Bottles Per Minute
Machine vision systems are rapidly changing how we ensure quality in glass bottle production. These systems can now identify minuscule surface flaws at a speed of 120 bottles per minute, which is a significant leap forward in inspection efficiency. They combine advanced optical components with deep learning algorithms to achieve this rapid inspection, leading to much more reliable and accurate quality checks.
The ability to capture and analyze images in real-time is a cornerstone of these modern inspection systems. It means flaws can be immediately spotted during the manufacturing process. This real-time feedback replaces older methods that relied on human inspection, which often led to inconsistencies. Increased productivity is just one of the benefits of this shift.
Though powerful, these technologies aren't without challenges. Creating effective machine vision systems requires large amounts of labeled training data and can be expensive to develop. Getting the data needed to accurately verify the detection of defects can be costly and time-consuming.
Nevertheless, in an industry where maintaining quality standards is crucial—especially for things like food and drug packaging—the development of machine vision systems marks a major step forward. It's clear that these systems are playing a pivotal role in reshaping the landscape of glass bottle production as manufacturers strive for higher quality and consistency.
Machine vision systems are now capable of identifying incredibly small surface defects on glass bottles, down to a mere 3 microns—about the size of a grain of salt. This remarkable level of detail reveals the increasing sophistication of these systems in quality control. The algorithms used in these systems allow for real-time detection and categorization of defects, enabling adjustments to the manufacturing process without interrupting production. This continuous feedback loop is crucial in refining the manufacturing process.
These systems can inspect bottles at a rapid pace of 120 per minute, processing over 7,200 bottles each hour. This speed dramatically outpaces traditional manual inspection methods, which are inherently slower and prone to inconsistencies. The use of AI within machine vision allows the system to learn from patterns observed in past defects, which progressively enhances the accuracy of future defect identification. This continuous learning aspect allows these systems to adapt and improve over time.
Recent advancements in lighting techniques have played a significant role in improving defect detection accuracy. Specialized lighting designs are now employed to reveal subtle imperfections that might otherwise go undetected under conventional lighting. This targeted illumination is a crucial aspect of these systems' ability to achieve precise results.
Beyond simple defect identification, these systems offer valuable data analytics capabilities. Engineers can gain insights into recurring defects, enabling them to identify and address the root causes of such issues, optimizing the production process. The physical setup often involves a combination of high-resolution cameras and laser-based triangulation technologies to create a detailed 3D image of the surface, allowing them to scrutinize even very fine surface irregularities.
One hurdle these systems face is adaptability to the varied shapes and surface coatings of glass bottles. However, there's ongoing development in algorithms that can dynamically adjust to these diverse features of each bottle batch. This flexibility is needed to ensure consistent performance across the spectrum of glass bottle designs currently seen in the market.
Implementing machine vision to identify defects has led to a reduction in the amount of wasted materials. Research suggests that early detection of defects can reduce the rejection rate of faulty bottles by as much as 30%. This cost-saving is a significant benefit from a business perspective. The integration of machine vision technology into the glass bottle manufacturing industry is part of a broader automation and smart manufacturing trend, driving improvements in efficiency and product quality across the board. While the promise of these systems is significant, the continued development of more adaptable and cost-effective systems is critical in its broad adoption by the glass industry.
Understanding Glass Bottle Refinement Advanced Manufacturing Techniques and Quality Control in 2024 - Temperature Regulated Annealing Chambers Transform Glass Strength Parameters
The use of temperature-controlled annealing chambers has become increasingly important in enhancing the mechanical properties of glass used in bottle production. These chambers allow manufacturers to precisely manage the annealing process, which is critical for reducing internal stresses within the glass structure. The specific annealing methods used can vary depending on the intended production volume and bottle design, encompassing techniques such as Lehr annealing for high-volume manufacturing and kiln annealing for more complex designs.
The annealing process itself involves carefully controlling the temperature and cooling rate of the glass, ensuring that stresses are relieved and the glass achieves optimal strength and durability. While this is a well-established process, the increasing need for high-performance glass necessitates greater precision in the annealing process. Variations in temperature during this cooling phase, even seemingly minor ones, can lead to unwanted stress within the finished glass, potentially impacting its integrity. Key factors like glass thickness and the size of the bottle must be carefully considered to create the optimal temperature profile for annealing.
Furthermore, research into advanced annealing methods like high-pressure sub-Tg annealing is pushing the boundaries of glass engineering. These newer approaches suggest that we may be able to achieve new levels of control over the material properties of glass, potentially leading to stronger, more resistant bottles. It remains to be seen how widespread these techniques will become, but they hint at a future of even greater refinement in the manufacturing of glass containers.
Temperature-controlled annealing chambers play a pivotal role in shaping the strength characteristics of glass, which is critically important for refining the production of glass bottles. The annealing process itself, which involves carefully controlled heating and cooling, is fundamental in relieving internal stresses that develop during glass forming. Different annealing methods, like the large-scale Lehr annealing, kiln annealing suited for complex designs, and rapid flame annealing, all serve their unique purposes in manufacturing, showcasing the adaptability of this crucial stage.
The effectiveness of annealing is deeply tied to achieving the right temperature and a precisely defined cooling curve. These parameters are heavily influenced by factors like the glass thickness and the size of the container being manufactured. Maintaining a uniform cooling environment is particularly important, and ideally, temperature variations within the glass shouldn't exceed 5°C (10°F) to avoid introducing undesirable stress points that could cause future failures. It's intriguing how a seemingly simple control, like a uniform temperature field, has such a profound impact on the integrity of a glass structure.
We can study the intricate behavior of glass through techniques like Differential Scanning Calorimetry (DSC), which is instrumental in examining glass formation, relaxation, and crystallization. During the annealing process, the glass transition temperature can shift based on structural changes occurring in the glass, and this aspect is scrutinized through a range of heating experiments. It would be fascinating to investigate how the interplay of chemical composition and thermal history alters glass properties during annealing.
The drive towards improved efficiency in manufacturing is spurring research into automated engineering calculations that can optimize the glass annealing process. The ability to precisely predict the cooling behavior of glass would be immensely valuable. Proper temperature monitoring inside the kiln is obviously vital to ensure that the cooling process unfolds as intended. This control is necessary for achieving the mechanical properties that determine the functionality and robustness of the finished glass products.
There's a growing interest in exploring high-pressure sub-Tg annealing, which appears to open access to unique glass states that were previously unattainable. This technique has the potential to significantly expand our capabilities in producing advanced glass materials with tailored characteristics. While the potential of this newer approach is exciting, it will take time and extensive experimentation to understand its full scope. It highlights how the interplay between pressure and temperature during annealing can be leveraged to influence the structure and properties of glass.
It appears that annealing is a stage in glass bottle production that remains reliant on precise physical parameters, as opposed to the virtual representations and predictive controls offered by digital twins. In that way, it remains more of a traditional manufacturing step in a world of evolving automation. However, it’s likely that integrating sensors and real-time data processing will become more important in the future, bridging the gap between classical annealing methods and advanced manufacturing principles.
Understanding Glass Bottle Refinement Advanced Manufacturing Techniques and Quality Control in 2024 - Automated Raw Material Mixing Systems Achieve 9% Batch Consistency
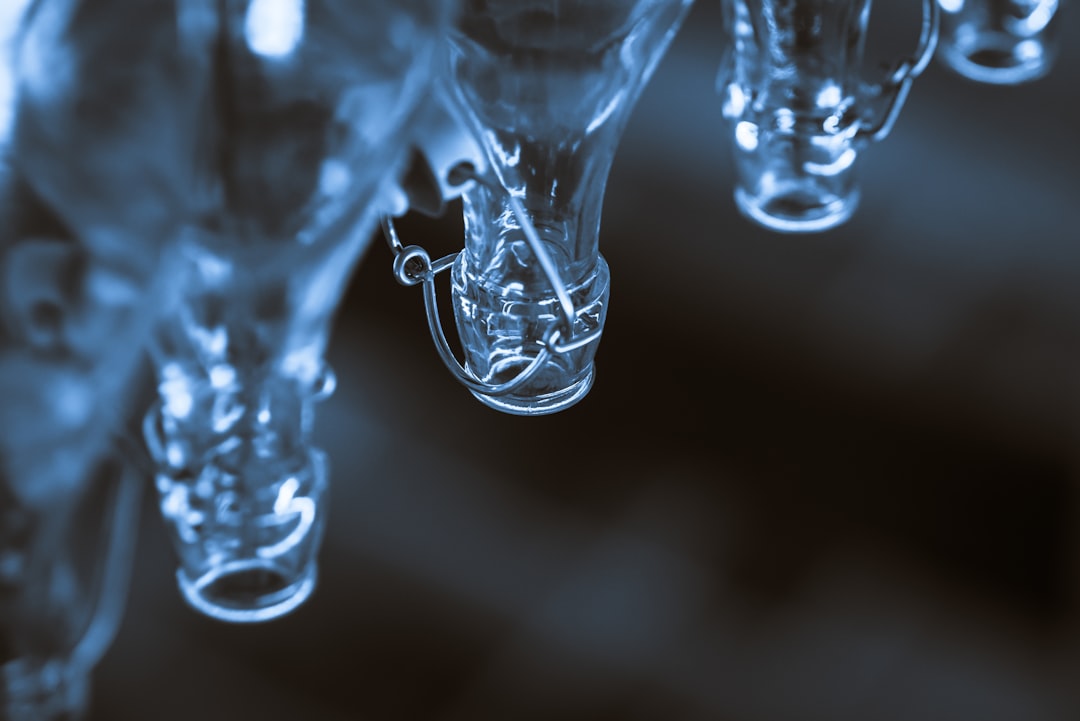
The introduction of automated raw material mixing systems in glass bottle production has led to a notable 9% improvement in batch consistency. These systems are designed to precisely measure and deliver the necessary quantities of raw materials, resulting in a more uniform final product. This precision is especially beneficial for ensuring consistency of minor and trace components that are critical for achieving desired glass properties. The automated mixing systems not only boost consistency but also reduce the time required for batch processing, leading to gains in efficiency. As glass manufacturing increasingly embraces automation and advanced manufacturing techniques, precise material mixing becomes a cornerstone of overall quality control, ensuring the production of consistently high-quality glass bottles. It remains to be seen how far this trend of automated material mixing will progress, but it represents a positive step toward greater manufacturing precision in a sector that often needs to manage highly variable raw materials.
In the realm of glass bottle refinement, achieving consistent raw material mixtures is fundamental for producing high-quality glass. It's fascinating how automated raw material mixing systems are now achieving a 9% improvement in batch consistency, a significant leap forward compared to traditional manual mixing processes. These systems use advanced weigh-in-motion sensors to precisely measure and control the quantities of raw materials, offering real-time adjustments that maintain uniformity between different batches. This level of precision is remarkable, and suggests that the days of inconsistent mixes may be coming to an end.
A key advantage of automation is the reduced potential for human error. Manual mixing is inherently prone to variation because of the differing skills and attention levels of individual operators. In contrast, automated systems execute the same mixing protocol each time, ensuring consistency in every batch. While automation may initially seem like a straightforward concept, there's a lot of complex technology behind it. Advanced data analytics play a significant role in maintaining control over the mixing process. These systems constantly monitor the mixture composition in real-time and can quickly adapt to any deviations from desired specifications, ensuring that the final mixture meets the required standards. The capability to continuously adjust the mixing process, using this data, helps minimize any potential for variations in the finished product.
Automated mixing systems also enhance productivity by increasing the speed and volume of materials that can be mixed compared to manual methods. This is a boon for production lines needing to fulfill a higher demand for glass bottles. Furthermore, these systems are incredibly versatile, allowing manufacturers to adapt to different production volumes or specific customer needs, a valuable feature for the ever-changing market. Some of these systems even integrate IoT technologies, facilitating remote monitoring and predictive maintenance. This connectivity allows engineers to analyze real-time data and quickly react to any potential issues, reducing downtime and operational costs.
It's interesting how the material composition and homogeneity of the mix directly impact the characteristics of the finished glass. Precise tracking of the raw materials throughout the process is paramount for ensuring the glass has the intended mechanical and aesthetic properties. Automated systems excel in this respect, helping ensure that each batch of glass is remarkably uniform. Many automated mixing systems employ closed-loop control, where the system continuously monitors the output against the defined parameters, actively making adjustments if deviations are detected. This continuous feedback loop maintains a desired level of precision and provides quality control throughout the mixing process.
One question that remains is how flexible these automated systems can be in adapting to different or customized glass formulations. The ability to easily tailor the mix based on specific product requirements is critical, especially as consumer preferences or market needs evolve. The capacity for customization without significant alterations to the process itself suggests that these systems have the potential to drive innovation in the glass industry. Ultimately, the benefits of these systems extend to the end-product, which benefits from improved consistency and homogeneity in the material properties. This leads to a more uniform glass product that has more consistent strength, clarity, and other characteristics. Automated mixing systems are clearly playing a significant role in refining the glass bottle manufacturing process by achieving improved consistency, precision, and homogeneity in raw material mixtures. It will be fascinating to see how these technologies continue to evolve and influence glass bottle production in the future.
Understanding Glass Bottle Refinement Advanced Manufacturing Techniques and Quality Control in 2024 - Laser Guided Mold Alignment Technology Reduces Production Defects by 47%
Laser-guided mold alignment technology has emerged as a valuable tool in glass bottle manufacturing, achieving a notable 47% reduction in production defects. This innovative approach uses lasers to precisely align the molds during the glass shaping process, significantly minimizing the errors that contribute to faulty bottles. The technology's ability to integrate seamlessly with existing production lines makes it particularly attractive for manufacturers seeking improvements in both efficiency and consistency. However, implementing laser-guided mold alignment involves initial capital expenditures and the need for thorough employee training to maximize the technology's benefits. Nonetheless, for glass bottle producers seeking to adhere to rigorous quality control standards, this technology offers a promising avenue for achieving more consistent and defect-free output, potentially leading to less production waste.
Laser Guided Mold Alignment Technology (LGMAT) has shown promise in improving glass bottle production by using laser sensors to achieve incredibly precise mold alignment, within a margin of error of ±0.1 millimeters. This level of accuracy is remarkable, as it significantly reduces the potential for gaps or misalignments that often cause defects during the molding process.
A key finding is that LGMAT has led to a 47% reduction in production defects. This decrease in defects not only improves the quality of the final product but also minimizes material waste, which is a substantial economic benefit. The relationship between precise alignment and overall manufacturing efficiency is highlighted by these results.
One of the noteworthy aspects of LGMAT is its ability to make adjustments in real-time. The system can detect and immediately correct misalignments, which is crucial for maintaining a consistent level of quality throughout production runs. This real-time feedback loop is a significant advancement over traditional methods, which often relied on less precise manual interventions.
Furthermore, LGMAT substantially reduces the time needed for mold changes. Traditional methods require considerable downtime for manual alignment, while LGMAT can complete the process in a fraction of the time, often within three minutes. This shortened cycle time translates into increased production throughput, which is beneficial in environments with high production demands.
Interestingly, LGMAT can be integrated with existing digital twin technologies, which could improve predictive maintenance strategies. By providing detailed data on mold alignment, the combination of these technologies could improve the accuracy of predicting future alignment needs. However, further research will be necessary to fully explore the interplay of LGMAT and digital twin systems.
While many technologies have limitations, LGMAT appears to be very flexible. This adaptability means that it can be readily calibrated for various glass mold shapes and sizes. This flexibility is especially valuable in a market where glass bottle designs are constantly changing to meet consumer preferences.
There are also some speed benefits that can be attributed to LGMAT. Mold alignment can be done in about three minutes, which is remarkably faster than the 25+ minutes needed with more traditional approaches. These time savings provide a strong incentive for manufacturers to explore adoption.
Additionally, studies suggest that using LGMAT can reduce energy consumption during the molding process. This is likely because the improved alignment reduces the number of molds that are improperly formed and fail. While these energy savings are potentially significant, additional research is needed to verify and quantify these improvements in a variety of production settings.
The adoption of LGMAT aligns with the goals of Industry 4.0 in that it promotes a more automated and data-driven approach to manufacturing. By using advanced technologies and real-time data, LGMAT helps to elevate production standards and improve process control.
While there are many advantages to LGMAT, it's important to note that implementing this technology requires a substantial initial investment and employee training. This cost-benefit trade-off is likely to be particularly relevant for smaller manufacturers considering adopting the technology as part of an update to their production techniques. It’s a fascinating example of how modern technologies can potentially reshape glass bottle manufacturing.
Understanding Glass Bottle Refinement Advanced Manufacturing Techniques and Quality Control in 2024 - Smart Pressure Testing Methods Using IoT Sensors Monitor Real Time Quality Metrics
The integration of smart pressure testing methods, leveraging IoT sensors, offers a new way to monitor real-time quality metrics during glass bottle production. These sensors embedded within the manufacturing process continuously track pressure levels, providing immediate insights into potential issues related to bottle integrity and safety. This continuous monitoring allows manufacturers to identify problems early on, potentially preventing defects before they lead to flawed products. It also fits into the broader Industry 4.0 vision by emphasizing data-driven decision-making in manufacturing. While smart pressure testing holds potential to improve production efficiency, the initial cost and complexity of these systems should not be overlooked. While the future looks promising, it's too early to fully grasp how effectively these IoT-enabled methods will perform across a variety of manufacturing situations.
The integration of the Internet of Things (IoT) into pressure testing for glass bottles is revolutionizing how we monitor the quality of these products. By embedding sensors within or around the bottles, we can gather continuous, real-time data about the pressure conditions inside them. This is a substantial improvement over traditional methods which often involved infrequent, manual checks. The ability to detect minute pressure changes, potentially as small as 0.05 psi, is especially important. It allows us to spot inconsistencies very early in the process, which could otherwise escalate into more significant problems or even catastrophic failures.
These smart pressure testing setups send the acquired data to cloud-based platforms where machine learning algorithms continuously assess the data for patterns. This offers a powerful opportunity for predictive maintenance. Instead of simply reacting to a problem, we can anticipate issues based on the data trends. The systems can essentially predict when a pressure-related issue is likely to develop and alert manufacturers beforehand. This proactiveness has the potential to prevent production disruptions and improve overall efficiency. There's also an added benefit of enhanced traceability through these digital systems. Each bottle's data is logged, providing a detailed history of its manufacturing process and pressure profile. This is incredibly valuable when defects occur because we can quickly identify the source and pinpoint when and where the problem happened.
The implications for cost reduction are also very intriguing. By catching faulty bottles early in the process, we reduce the amount of wasted raw materials and scrap. This is where we've seen reports of reduced material costs in the 15% range. While it's still early in the adoption of these systems, early observations are promising for manufacturers.
It's not just pressure these systems can monitor. Temperature and humidity levels, factors that can impact bottle integrity, can also be measured and analyzed, contributing to a more holistic quality control system. Moreover, we can better link these measures to the digital twin representations of the production lines that have already been discussed. By integrating this pressure data, we can improve the accuracy of the digital models and potentially get better predictive capabilities.
Furthermore, this new generation of smart pressure testing methods appears more flexible. The ability to rapidly adapt testing protocols based on real-time conditions allows us to tweak things based on specific glass formulas or production process changes. This adaptability is crucial for manufacturers because it reduces the time required to adjust to variations in the raw material characteristics. There's also an added layer of worker safety in these systems. Since the data can be collected remotely, fewer hands-on inspections are required, leading to potentially safer working environments. While it's early days for this technology, the potential benefits are substantial. It's a fascinating example of how technological advancement can be applied to a traditional field like glass bottle manufacturing, leading to improved quality and efficiency.
More Posts from patentreviewpro.com: