Cascade Refrigeration Systems Achieving Ultra-Low Temperatures for Industrial Applications
Cascade Refrigeration Systems Achieving Ultra-Low Temperatures for Industrial Applications - Multi-Stage Compression Enabling -80°C and Below
Achieving temperatures as low as -80°C and below hinges on the use of multi-stage compression. By breaking down the compression process into multiple steps, with cooling intervals interspersed, the system effectively manages the heat generated during compression. This approach, compared to a single-stage system, improves efficiency, reducing energy waste. In a cascade setup, this multi-stage concept is amplified through the interaction of separate refrigeration cycles, each with its own refrigerant. This cascade, facilitated by a specialized heat exchanger, allows for efficient heat transfer between cycles, maximizing the effectiveness of each stage. The freedom to choose the most suitable refrigerant for each stage further enhances the versatility of cascade systems. They are therefore well-suited for applications where significant cooling capacity and precise temperature control are paramount, such as specialized industrial processes and the storage of sensitive materials. It's worth noting that the effectiveness of these systems is highly dependent on design and operational optimization, which is crucial for achieving the desired temperature ranges and maximizing energy efficiency in a variety of industrial scenarios.
Reaching temperatures of -80°C and below necessitates a departure from conventional refrigeration methods. Multi-stage compression offers a path forward, allowing for extraordinarily large pressure ratios, often surpassing 20:1. This ability to compress in stages, with cooling intervals between each stage, is crucial for achieving such extreme temperature drops.
The selection of refrigerant becomes paramount at these low temperatures. We need to consider not only thermodynamic properties but also environmental impact. Refrigerants like helium and ammonia, due to their favourable characteristics, are frequently favoured because of their ability to efficiently absorb and release heat at ultra-low temperatures. However, there are always tradeoffs to consider in selecting refrigerants.
Inter-stage cooling plays a key role in optimizing energy usage. By cooling the refrigerant gas between compression stages, we can reduce energy consumption and improve overall system efficiency. It's a delicate balancing act, as any inefficiency in the cooling process will impact the overall system performance.
The demanding environment created by such low temperatures requires thoughtful mechanical design. Materials like stainless steel and high-strength alloys are used due to the stresses and thermal fluctuations they can withstand, combating issues like fatigue at these cryogenic temperatures. The design considerations are far from trivial when one considers the unique constraints.
One of the biggest challenges in these systems is sealing. Standard sealing technologies don't always perform adequately at such low temperatures. Thus, the need for advanced techniques like magnetic or hydraulic seals to maintain system integrity and prevent refrigerant leakage is crucial. The leakage rate could be critical in the long term. Is there a new class of seal that could be developed?
A key aspect of system design is managing the cooling load effectively. It's not just about the target temperature, it's about the changing demand imposed by the industrial process. Designers have to create systems that maintain consistent performance across a spectrum of loads. Is a new dynamic load management strategy required to optimize performance in such systems?
Control systems for these complex systems play a critical role in efficiency and reliability. Implementing advanced systems with real-time monitoring and automation allows for dynamic adjustment of compressor speeds and refrigerant flow rates. It is fascinating how control systems can respond to fluctuating operational conditions in these extreme environments.
Heat exchangers are a critical part of the design, particularly shell-and-tube varieties. Their ability to efficiently dissipate heat at such extremely low temperatures without sacrificing thermal efficiency is important. Are there any breakthroughs in heat exchange technology that might further enhance this aspect of the system?
While achieving these ultra-low temperatures is energy-intensive, advancements in compressor technologies and system optimization have brought us a long way in improving energy efficiency. This has allowed for these systems to be implemented in a more feasible manner for long-term industrial use. We continue to research how to further reduce energy consumption.
The potential for these multi-stage systems extends beyond refrigeration. They are essential in areas like cryogenics, where extremely low temperatures are needed for liquefying gases like helium and hydrogen. These gases are used for many industrial and research purposes. The broader uses of this technology continue to be explored.
Cascade Refrigeration Systems Achieving Ultra-Low Temperatures for Industrial Applications - Energy Optimization Techniques in Cascade Systems
Within the realm of cascade refrigeration systems, achieving optimal energy efficiency is paramount, particularly when targeting ultra-low temperatures for industrial applications. The pursuit of these extremely low temperatures necessitates a focus on techniques that minimize energy consumption while ensuring reliable performance. Improving the isentropic efficiency of compressors, a key component in these systems, is one avenue for optimization. Furthermore, the strategic use of inter-stage cooling can significantly impact energy usage. By cooling the refrigerant gas between compression stages, we can reduce energy losses and improve overall system efficiency.
The implementation of advanced control systems further enhances energy efficiency in these complex systems. These systems enable dynamic adjustments to compressor speeds and refrigerant flow rates, allowing them to respond to fluctuations in operating conditions and cooling demands. While traditional cascade systems have proven useful, newer approaches like integrating ejectors into two-stage systems show potential for greater energy savings.
The environmental impact of traditional refrigerants is a growing concern. Researchers are actively exploring more sustainable refrigerant options and conducting thermoeconomic studies to understand the trade-offs between energy efficiency and environmental footprint. These studies aim to guide the development of future cascade systems that are both energy efficient and environmentally friendly.
Ultimately, optimizing energy consumption in cascade systems is not just a matter of improving operational efficiency; it is a vital aspect of realizing a sustainable future for ultralow temperature refrigeration technologies. As the demand for reliable and energy-efficient cooling solutions in various industrial settings continues to rise, implementing these optimization strategies will be increasingly crucial. There's a delicate balance to be struck between operational efficiency and environmental impacts that will require ongoing research and development.
Ultra-low temperature refrigeration, vital in industries like pharmaceuticals and research, often necessitates cascade systems. These systems leverage multiple refrigeration cycles, each potentially using a different refrigerant, to achieve temperatures as low as -140°C. While offering significant cooling capacity, their energy efficiency is paramount for practical application.
Improving energy efficiency in cascade systems often revolves around optimizing the interaction of multiple stages. For instance, adaptive control strategies, like model predictive control, can dynamically adjust setpoints and operational parameters based on real-time conditions. This adaptive approach allows the system to respond effectively to load fluctuations, minimizing wasted energy. Interestingly, some cascade systems can be configured as heat pumps, recovering waste heat from the refrigeration process for other uses. This dual functionality can substantially increase the overall energy utilization in an industrial setting.
The selection of refrigerants is another area of considerable influence. While vapor pressure is a primary consideration, the refrigerant's thermal conductivity also impacts heat transfer efficiency. This underscores the need to carefully consider the refrigerant's overall properties within the context of the system. Moreover, operating at the very high pressure ratios often seen in these systems (exceeding 40:1 in some specialized applications) presents significant engineering challenges. Compressors and heat exchangers, for example, must be robust enough to handle such extreme operating conditions.
The physics of fluids at ultra-low temperatures can also complicate the design process. Fluids can exhibit non-Newtonian flow behavior, requiring a deep understanding of cryogenic fluid dynamics for optimal performance. Traditional sealing methods are frequently inadequate at extremely low temperatures. Therefore, researchers are looking at innovative solutions, such as cryogenic seals made from polymers or advanced metals, to maintain system integrity and prevent refrigerant leaks, which can be particularly problematic over time.
Insulation technologies also play a vital role. As temperature decreases, the effectiveness of traditional insulation diminishes, necessitating advanced materials such as high-performance foams or vacuum insulation techniques tailored for cryogenic environments. Furthermore, careful optimization of the inter-stage pressure variation can significantly reduce energy consumption. This highlights the sophisticated control required in these complex systems to achieve maximum energy efficiency.
The use of zeotropic refrigerant blends offers another avenue for improvement. These blends can optimize heat transfer by exploiting temperature glide, leading to increased energy efficiency during operation. While still a developing area, this approach shows promise for future innovations in refrigerant development and system design.
In summary, while cascade systems are powerful tools for reaching ultra-low temperatures, optimizing energy efficiency is a key aspect of their development. The pursuit of more efficient designs and operational strategies requires a multifaceted approach that spans everything from control mechanisms and material selection to the intricate behavior of fluids at these extreme conditions. Understanding these complex interactions is essential for making cascade systems more practical and sustainable solutions for industrial applications.
Cascade Refrigeration Systems Achieving Ultra-Low Temperatures for Industrial Applications - Natural Refrigerants Revolutionizing ULT Applications
Ultra-low temperature (ULT) refrigeration in industrial applications is experiencing a shift towards natural refrigerants. These refrigerants, like propane and ethane, offer a substantially lower environmental impact compared to traditional synthetic refrigerants because of their significantly reduced Global Warming Potential (GWP). This makes them an attractive option in a world increasingly focused on sustainability. The ability of cascade refrigeration systems to utilize natural refrigerants effectively, achieving exceptionally low temperatures, opens new possibilities for various sectors like medicine and industry, which heavily rely on precise temperature control. However, the journey to widespread adoption of natural refrigerants in ULT applications isn't without obstacles. Careful consideration of thermodynamic properties alongside environmental concerns when selecting refrigerants remains crucial. Further challenges related to energy efficiency and system design, including the ability to manage the high pressures often encountered, still need addressing to maximize the efficacy of these technologies. As the demand for reliable ULT refrigeration continues to grow, further innovations in refrigerant development and system optimization techniques will be vital to ensure the long-term viability and effectiveness of natural refrigerant-based systems.
Natural refrigerants like propane and ammonia are becoming increasingly popular in ultra-low temperature (ULT) applications because of their impressive energy efficiency and often lower operational costs compared to conventional synthetic refrigerants. While they can achieve similar performance, it is interesting how they sometimes offer lower costs.
Helium, with its extremely low boiling point of around -269°C, remains indispensable for achieving the coldest temperatures in cryogenics. Its unique properties make it ideal for applications that need to reach temperatures below what most other refrigerants can manage.
Ammonia's heat transfer capabilities become even more pronounced at very low temperatures, enabling more compact system designs without sacrificing efficiency. This is particularly beneficial in industrial settings where space is at a premium.
Employing zeotropic refrigerant blends in ULT applications is intriguing due to their potential to enhance heat transfer through a process called temperature glide. However, using these blends necessitates careful optimization to prevent issues like the build-up of non-condensable gases. It's a delicate balancing act in a complex environment.
Magnetic seals are emerging as a promising technology for combating leaks in low-temperature environments. This is a much-needed development in ULT systems, with the potential to decrease maintenance needs and prolong the lifespan of equipment operating at these harsh temperatures.
Advanced control systems like model predictive control (MPC) are being explored to optimize energy efficiency, particularly under fluctuating operational conditions. MPC can dynamically adapt system parameters to minimize energy waste while maintaining the desired cooling outputs, a testament to the growing sophistication in ULT systems.
Some refrigerants can be multi-purpose, enabling secondary uses like waste heat recovery systems in cascade processes. This can offer a significant boost to the overall efficiency of the system, adding another interesting aspect to their performance.
Balancing the need for extremely low temperatures with the high pressures often required in these systems presents a significant design challenge, particularly for compressor and heat exchanger technologies. Engineers need to devise innovative solutions to ensure reliable performance within these conflicting demands.
New high-performance insulation materials like aerogels are changing how we design ULT systems. By drastically reducing heat loss, they are crucial for maintaining low temperatures, as any slight temperature rise can significantly affect performance. It's amazing how a small heat gain can be so detrimental at these temperatures.
Studying cryogenic fluid dynamics reveals that the behavior of fluids at extremely low temperatures can be quite unusual. Properties like viscosity and thermal conductivity change, requiring tailored approaches to fluid management in ULT systems. This unexpected behaviour highlights the unique challenges and opportunities associated with these systems.
Cascade Refrigeration Systems Achieving Ultra-Low Temperatures for Industrial Applications - Autocascade Technology for Small-Scale Industrial Cooling
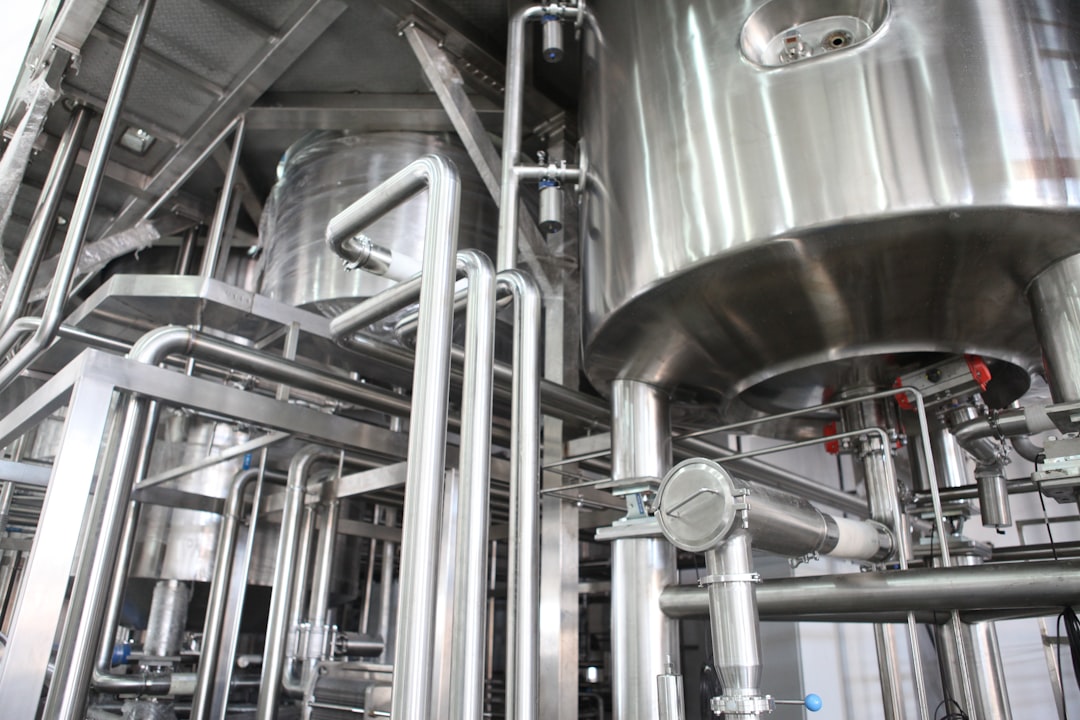
Autocascade technology introduces a new approach to small-scale industrial cooling, especially for applications demanding extremely low temperatures, reaching as low as -80°C. This technology cleverly employs a combination of refrigerants, such as R23 and R508B, resulting in enhanced cooling capacity and efficiency when compared to traditional cascade setups. While this increased performance comes with the cost of higher energy use due to the two-compressor arrangement, the ability to utilize less potent energy sources helps mitigate some of that impact. This makes the technology attractive for a diverse range of applications, including preserving biological samples and semiconductor manufacturing. Research and experimentation show potential for even greater energy efficiency by incorporating pre-cooling steps, which can help optimize the system's performance as operational demands evolve. However, the intricate nature of these systems introduces design complexities, refrigerant selection challenges, and difficulties in sealing at these very low temperatures. Carefully managing these aspects is crucial for both enhancing performance and ensuring sustainability in these applications.
Autocascade systems, with their ability to achieve very low temperatures, are increasingly relevant for small-scale industrial cooling applications. They can manage exceptionally large pressure ratios, sometimes surpassing 30:1, which translates to a noticeable increase in cooling capacity. While this enhanced performance comes with potential energy penalties, clever system designs often balance this with energy efficiency.
The use of zeotropic refrigerant mixtures in autocascade systems is interesting. These blends offer a temperature glide effect, resulting in a smoother transition during phase changes compared to pure refrigerants. This can improve heat transfer efficiency and optimize the cooling process, but researchers still need to navigate the complexities introduced by this approach.
The compact nature of these systems, often a result of the thermodynamic cycle employed, is particularly beneficial for applications where space is limited. This makes them a suitable solution for many small industrial settings that still require significant cooling power. Furthermore, the advanced control systems often integrated into autocascade setups allow for rapid adjustments to operating conditions. This means that these systems can respond quickly to changes in cooling demand, leading to more stable temperatures, even under fluctuating operational conditions.
However, designing for ultra-low temperatures does present challenges, including material selection. Components of the systems may require specialized alloys that can withstand the thermal cycling without experiencing fatigue or other mechanical issues caused by the drastic temperature changes. Furthermore, the development of magnetic seals for these systems is promising. This technology reduces refrigerant leakage and plays a key role in maintaining system integrity within the harsh environment.
Optimizing performance requires precise control of the refrigerant's liquid phase. A deep understanding of the refrigerant's behavior at such low temperatures is vital for efficiency. Some system designs can also incorporate waste heat recovery, leading to a potential increase in overall system efficiency and economic benefits through lower operating costs.
It's worth noting that understanding the autocascade thermodynamic cycle is more demanding than conventional systems. Predicting refrigerant behavior at extremely low temperatures becomes more challenging as these conditions push the limits of typical thermodynamic models. Beyond typical refrigeration uses, the unique capabilities of autocascade technology open doors to other specialized industrial applications, such as semiconductor manufacturing and advanced cryogenic processes.
Overall, autocascade systems are proving themselves as a capable technology for demanding cooling applications, though the challenges of implementing them require careful design and consideration. As a researcher, I'm intrigued by the prospect of further development, including exploring the frontiers of refrigerant blends, material science for ultra-low temperatures, and novel seal technologies that can help ensure the long-term reliability of these systems.
Cascade Refrigeration Systems Achieving Ultra-Low Temperatures for Industrial Applications - Performance Enhancements through Isentropic Efficiency
Within cascade refrigeration systems, especially those targeting ultra-low temperatures for industrial purposes, achieving enhanced performance is closely tied to improving energy efficiency. One key area for optimization is the isentropic efficiency of the compressors. This metric essentially measures how well the compressor achieves ideal performance during the compression process, directly affecting energy consumption and overall cooling capacity at extremely low temperatures. Improvements in this efficiency can be realised through clever design choices, integrating adaptive control systems that respond to varying cooling demands, and implementing efficient inter-stage cooling methods to reduce energy losses. However, it's important to consider the potential downsides of these improvements. For instance, optimizing for higher isentropic efficiency can sometimes increase complexity, impact the selection of appropriate refrigerants, and even raise concerns about environmental impact. As industrial sectors strive for more sustainable solutions, the careful balance between performance gains, system stability, and environmental responsibility becomes increasingly critical. Striking this balance is a major challenge that continues to shape research in this field.
Within cascade refrigeration systems, especially those targeting ultra-low temperatures, the isentropic efficiency of compressors plays a crucial role in determining both system performance and energy use. These compressors, often operating within a range of 60% to over 90% efficiency, become even more critical as the system attempts to achieve lower temperatures through multi-stage compression.
Isentropic processes, while ideal thermodynamic scenarios where entropy remains constant, don't perfectly reflect real-world conditions. The deviations from this ideal introduce efficiency variations and highlight the importance of design precision to minimize entropy generation within these complex cascade arrangements.
One challenge related to isentropic efficiency in these systems is managing the high pressure ratios – sometimes exceeding 40:1. These high ratios can lead to increased heat generation during compression, impacting the overall efficiency. Developing more effective compressors that can efficiently handle these demanding conditions is essential.
Inter-stage cooling techniques can also be a significant factor. By cooling the refrigerant gas between compression stages, we can reduce superheating and minimize energy losses. This results in a boost to the system's ability to achieve ultra-low temperatures.
Designing compressors for high isentropic efficiency in these harsh environments poses specific challenges. Material selection and compressor geometry must be carefully considered to ensure they can withstand extreme thermal stresses while maintaining long-term reliability.
Advanced control systems offer a pathway to dynamically adjust isentropic efficiency. By modifying compressor speeds and refrigerant flow rates based on real-time conditions and load changes, they can adapt to fluctuations in operating conditions. Maintaining high efficiency across varying conditions is crucial.
The refrigerant selection process has a considerable influence on isentropic efficiency. Choosing refrigerants with desirable critical temperatures and heat capacities, such as helium for reaching very low temperatures, can boost system performance. However, the decision-making process should consider the trade-offs involved in selecting specific refrigerants.
It's noteworthy that isentropic efficiency is intricately tied to the phase change characteristics of the refrigerants used within the cascade system. Optimizing the behavior of these fluids at very low temperatures is key to maximizing heat transfer and overall system performance.
Quantifying isentropic efficiency involves comparing the actual work input with the theoretical work required for an idealized, isentropic path. This comparison provides valuable insights into system performance, enabling targeted improvements and adjustments.
The field of cascade refrigeration technology is constantly evolving. Combining techniques focused on maximizing isentropic efficiency with emerging technologies like ejectors or absorption processes might lead to a new generation of hybrid systems offering enhanced cooling performance. It's exciting to consider the possibilities and advancements in this domain.
Cascade Refrigeration Systems Achieving Ultra-Low Temperatures for Industrial Applications - Balancing Energy Consumption and Temperature Stability
Within cascade refrigeration systems designed for industrial applications that require ultra-low temperatures, maintaining a delicate balance between energy efficiency and consistent temperature control is paramount. Optimizing the performance of compressors, specifically focusing on improving their isentropic efficiency, can lead to significant reductions in energy consumption. Coupled with strategic inter-stage cooling techniques, this optimization helps maintain desired temperatures with minimal energy waste.
The growing demand for these systems in fields like vaccine storage and semiconductor fabrication underscores the need for advanced control systems. These systems allow for real-time adjustments to compressor speeds and refrigerant flow, enabling the systems to adapt to fluctuating cooling demands and maintain temperature stability. However, pursuing these improvements comes with design complexities. Optimizing these systems requires intricate engineering considerations, especially when dealing with the demanding operational environments that involve extreme pressure ratios and a wide range of refrigerants. It's a complex environment with challenging operating conditions.
As the drive towards sustainability intensifies, researchers and engineers are challenged to refine ULT cascade systems to minimize environmental impacts, while continuing to deliver reliable cooling at extremely low temperatures. Finding this balance between optimized performance and reduced environmental footprint remains a critical aspect of future research and development within this field.
In the realm of cascade refrigeration systems designed for achieving ultra-low temperatures, the interplay between energy consumption and maintaining stable temperatures is a fascinating and complex challenge. One way to optimize energy usage is through inter-stage cooling. By harnessing the heat removed from one refrigeration stage to pre-cool the next, we can create a synergy that significantly reduces the overall energy demand.
The specific refrigerants we choose play a pivotal role in this energy dance. The way they behave under different pressure and temperature conditions directly impacts the system's performance, highlighting a close link between refrigerant selection and energy efficiency. It's all about choosing the right refrigerant for the job.
Sophisticated control systems can really make a difference in energy efficiency. They allow the system to adapt to varying cooling demands in real time, minimizing wasted energy during periods of lower demand and maintaining consistent temperature stability, which is crucial for the applications these systems are designed for.
The materials used to construct cascade systems are another crucial factor. For instance, certain alloys can withstand the extreme thermal cycling and stress inherent in these systems, which can lead to more reliability and help reduce energy loss caused by less-than-ideal heat transfer.
The high pressure ratios, sometimes exceeding 40:1, can result in substantial energy losses as more heat is generated during the compression cycle. So, choosing compressors built to handle these demanding conditions is paramount for retaining efficiency.
The use of zeotropic refrigerant blends is proving to be a smart approach for achieving better thermal efficiency. The unique property of 'temperature glide' during the refrigerants' phase changes enhances heat transfer, becoming a powerful strategy to maintain energy balance at these extreme temperatures.
Traditional seals often lose their effectiveness at the incredibly low temperatures these systems operate at. This makes the development of innovative sealing techniques, including magnetic and cryogenic seals, absolutely vital. These newer seal technologies not only address leakage issues but also help preserve the energy integrity of the entire refrigeration process.
Achieving high isentropic efficiency – a measure of compressor performance – requires meticulous designs that minimize the generation of entropy. A deep understanding of the mechanics of compressors and the way refrigerants act in these complex systems is key to ensuring the energy we input translates to the desired cooling.
Researchers are exploring the use of infrared spectroscopy to observe refrigerant thermal performance in real time. This could be a game-changer in terms of detecting inefficiencies and refining designs, offering another route toward optimizing the balance between energy consumption and temperature control.
The study of cryogenic fluid dynamics is unveiling unique challenges. For instance, we're learning how viscosity and flow patterns change at cryogenic temperatures. Understanding these shifts is critical for maximizing performance and energy efficiency in ultra-low temperature cascade refrigeration.
In essence, balancing energy consumption and stable temperatures in cascade systems for ultra-low applications demands a multi-faceted approach that incorporates careful material selection, astute refrigerant choice, innovative sealing techniques, and intelligent control strategies. Ongoing research and a deeper understanding of the underlying science, such as cryogenic fluid dynamics, are needed to further refine these systems to be more energy efficient.
More Posts from patentreviewpro.com: