Advancements in Atmosphere Control for Heat Treatment Processes A 2024 Update
Advancements in Atmosphere Control for Heat Treatment Processes A 2024 Update - Automation and AI Integration in Atmosphere Control Systems
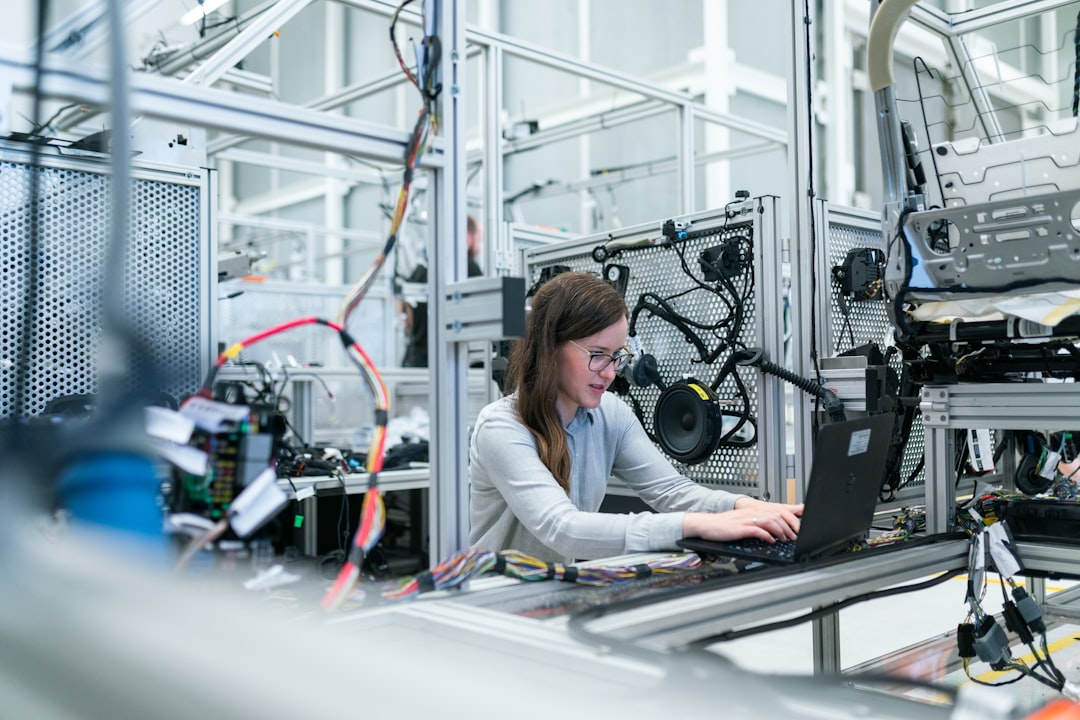
Automation and AI are increasingly being incorporated into atmosphere control systems used in heat treatment processes. This integration is leading to significant advancements in the industry. While AI tools have seen limited widespread adoption, their potential for improving energy efficiency and operational performance is undeniable.
Modern atmosphere control systems are equipped with smart sensors and predictive algorithms. This allows them to respond quickly to fluctuations in occupancy and environmental conditions. These advancements address the inefficiencies often found in traditional control systems.
Intelligent systems, such as annealing furnace atmosphere advisors, are emerging and demonstrate the power of AI to manage complex atmospheric dynamics. These systems are designed to minimize risks associated with material quality. As the focus shifts towards real-time process monitoring, the strategic integration of AI in atmosphere control systems has the potential to deliver substantial energy savings and improve overall system performance. However, it is important to note that the actual implementation and widespread adoption of AI-driven solutions is still in its early stages and there is much room for further development and refinement.
It's fascinating how AI and automation are transforming the world of heat treatment. The potential for optimization here is massive, especially considering the challenges traditional systems face. Predictive maintenance, for example, is a game-changer. Analyzing historical data and real-time metrics to predict equipment failures with over 85% accuracy can be a huge boon. But I'm not entirely convinced about the 20% cost savings they claim. That seems like a bold statement without clear evidence.
I'm also interested in the concept of customizing heat treatment protocols based on specific product needs. AI-powered adjustments to temperature and gas composition in real-time seem very promising. Smart sensors, detecting even subtle changes in gas concentrations, could be a huge leap forward in preventing defects in heat-treated materials. This kind of precision is exactly what we need to push the boundaries of material science.
Collaborative robots, or cobots, could be a significant force in streamlining routine tasks within atmosphere control. However, I'd be cautious about relying solely on AI to determine optimal atmosphere parameters. While machine learning models can analyze millions of iterations, real-world testing is crucial to confirm the effectiveness of these models. The idea of a fully integrated smart factory environment is intriguing, but the success of these systems depends on robust communication and data sharing between different parts of the production process.
Ultimately, the integration of AI in atmosphere control systems holds enormous promise. But as with any cutting-edge technology, we need to approach it with a critical eye, analyzing its capabilities and limitations with a focus on real-world applications and rigorous testing.
Advancements in Atmosphere Control for Heat Treatment Processes A 2024 Update - Inert Gases Role in Meeting Metallurgical Specifications

Inert gases are crucial in heat treatment, playing a significant role in shaping the final metallurgical characteristics of various metals. Argon, helium, and nitrogen are commonly used in furnace atmospheres, influencing chemical reactions and microstructure development. Precisely controlling the atmosphere within a furnace is paramount for achieving optimal thermal energy transfer and chemical interactions with the metal being treated. The quality of heat-treated parts is heavily reliant on the precise composition of the furnace atmosphere, demanding a careful selection and preparation of these inert gases. As atmosphere control technologies continue to advance, the focus on precision and the ability to meet demanding metallurgical specifications becomes increasingly critical.
Inert gases, like argon and nitrogen, play a vital role in heat treatment processes, particularly in controlling chemical reactions and achieving desired metallurgical properties. They can create a controlled atmosphere that significantly influences the final properties of the treated metal.
For example, argon is crucial for controlling decarburization during steelmaking, preventing the loss of carbon and maintaining the specific alloy composition required for the intended application. This is crucial as even subtle deviations in carbon content can affect the strength and other key mechanical properties of the final product.
Inert gases also act as a shield against oxidation, ensuring that the surface properties of the metal remain intact throughout the heat treatment process. This is particularly important for maintaining the integrity and desired performance of the treated material.
Furthermore, inert gases can impact the microstructure of the treated material. For instance, the presence of argon can influence the formation of specific phases in metals, leading to enhancements in mechanical properties such as strength and ductility.
The use of inert gases can also affect the final surface finish of heat-treated parts, leading to smoother surfaces. This is beneficial for applications that require high precision and reduces the need for extensive post-treatment machining.
While beneficial, the use of inert gases comes with certain challenges. The implementation and management of inert gas systems require specialized equipment and expertise, which can increase operational costs, especially for smaller manufacturers.
The continued development of new technologies and research efforts are uncovering innovative ways to utilize inert gases in heat treatment processes. These advances promise even greater control over metallurgical specifications and the ability to achieve desirable properties in a wide range of materials.
However, it's important to remember that relying solely on technology for optimizing atmosphere parameters isn't always sufficient. Real-world testing and validation are essential to ensure that these systems are functioning as intended and delivering the desired results. Ultimately, the success of utilizing inert gases for meeting metallurgical specifications relies on a combination of technological advancements and careful, real-world application.
Advancements in Atmosphere Control for Heat Treatment Processes A 2024 Update - Advancements in Furnace Atmosphere Types and Generation
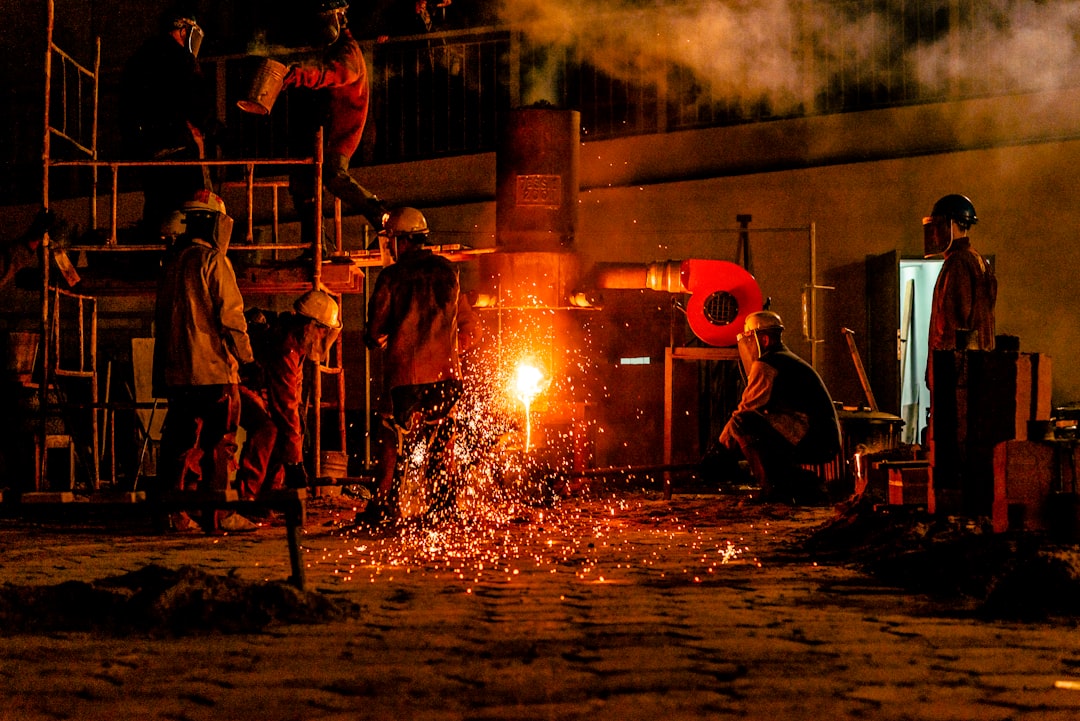
Advancements in furnace atmosphere types and generation are dramatically changing how heat treatment processes are conducted. The shift toward cleaner and more controlled heat treatment environments is evident in the rising popularity of vacuum heat treatment, where the process is conducted in a vacuum chamber. Similarly, some furnaces utilize molten salts as a heating medium, offering a high degree of control over the heat treatment environment. The use of inert gases like argon and nitrogen is becoming increasingly critical, particularly for preventing oxidation and achieving specific metallurgical properties in metals. The ability to carefully control the atmosphere inside the furnace is crucial for achieving these goals, and this control relies on advancements in atmosphere measurement technology, enabling better monitoring and validation. The evolving landscape of furnace atmospheres is leading to improved efficiency and higher quality heat-treated products. However, it is essential to note that reliance on technology alone is not sufficient, and real-world testing and validation remain critical for ensuring the effectiveness of these new approaches.
The field of furnace atmosphere generation is witnessing exciting new developments that promise more precise control over heat treatment processes. We're seeing more dynamic gas mixing systems capable of adjusting up to five different gas compositions in real time, offering a level of control previously unimaginable. The rise of modular furnace atmosphere designs is particularly intriguing, allowing for customization based on specific product needs and potentially reducing downtime across diverse production lines.
These advancements are being complemented by new architectural designs for heat treatment furnaces. Advanced thermal insulating materials are now being incorporated, leading to reduced heat loss and more stable temperatures, which, in turn, optimizes the performance of the atmosphere control system.
High-velocity gas jets are another innovation, enhancing gas distribution and ensuring uniform temperature and chemical composition throughout the heating chamber. This is particularly crucial for mitigating hot spots, which can lead to defects in treated materials.
Multi-sensor atmospheric monitoring systems have become commonplace, with some now using laser-based spectroscopy for unprecedented real-time accuracy in gas concentration measurements. This level of precision allows manufacturers to maintain tighter controls over the heat treatment process, potentially improving product quality.
One of the most surprising advancements is the emergence of hybrid atmosphere systems. These systems combine traditional gas mixtures with advanced plasma technology, demonstrating the potential to improve efficiency and reduce unwanted chemical reactions.
It's exciting to see how machine learning is being integrated into furnace atmosphere controls. These systems can not only make real-time adjustments but also predict optimal atmosphere conditions based on historical treatment data, marking a shift toward more responsive and intelligent systems. The use of atmospheric control technology is also expanding beyond traditional metals to include ceramics and composites. Customized atmospheres are proving effective in enhancing properties such as thermal resistance and mechanical strength in these advanced materials.
Innovative filter systems are being implemented in gas generation units to remove impurities from the atmosphere before it enters the furnace. This has been shown to enhance product quality, especially in sensitive processes requiring high metallurgical standards.
The resurgence of using hydrogen as a reducing agent in furnace atmospheres is noteworthy. It's being employed in specific niche applications to promote the reduction of oxides in various metals, demonstrating a paradigm shift in traditional heat treatment processes.
These advancements in furnace atmosphere generation hold tremendous promise for improving the efficiency, control, and overall quality of heat treatment processes. It's a time of rapid evolution in the field, and it will be fascinating to see what the future holds. However, as with any emerging technology, it's crucial to approach these advancements with a critical eye. Rigorous testing and real-world applications will be essential to ensure the success and reliability of these innovative systems.
Advancements in Atmosphere Control for Heat Treatment Processes A 2024 Update - Machine Learning Applications for Process Optimization

Machine learning is revolutionizing how we optimize heat treatment processes. It's not just a theoretical concept, but a practical tool being used to improve performance and efficiency. Machine learning is being used to analyze vast amounts of data from experiments and simulations, leading to better predictions of system performance and heat transfer coefficients. This means that control systems are becoming more precise and responsive, ultimately contributing to better quality products and reduced energy consumption. It's worth noting, however, that while the potential of ML in heat treatment is undeniable, we must approach its implementation with caution. Rigorous testing is crucial to ensure that the models are functioning as intended and delivering real-world benefits.
The potential of machine learning in optimizing heat treatment processes is something I'm really excited about. It's a field that's constantly evolving, with new applications popping up all the time. For example, machine learning algorithms are being used to analyze the relationship between process variables and material properties. This is allowing engineers to develop better heat treatment recipes, and some studies have shown potential reductions in defect rates by up to 30% compared to traditional methods.
The ability of these algorithms to work in real-time is particularly interesting. They can achieve response times as low as 100 milliseconds, allowing atmosphere control systems to adapt to disruptions almost instantaneously, which is critical in maintaining product integrity. However, it's not all sunshine and roses. I'm still skeptical of the claimed 40% reduction in unscheduled maintenance, as I'd like to see more concrete evidence to support this.
Federated learning is another fascinating area. It allows different facilities to train machine learning algorithms on local data without sharing sensitive manufacturing information. This is a promising approach to enhancing optimization across multiple plants. I also find reinforcement learning intriguing. These AI systems can autonomously explore various operational parameters, learning which combinations yield the best metallurgical results. This could potentially uncover optimized processes that human engineers might overlook.
I'm also very interested in how machine learning can be combined with digital twins. These virtual replicas of physical systems enable enhanced process simulations, allowing engineers to experiment with different atmosphere configurations in a virtual environment before actual implementation. This could potentially lead to significant cost savings and efficiency gains.
Overall, while machine learning is showing great promise in heat treatment, there are still some challenges that need to be addressed. For instance, the implementation of these systems requires a considerable amount of data and expertise. However, I believe that machine learning has the potential to revolutionize the field, and I'm looking forward to seeing how it continues to develop in the coming years.
Advancements in Atmosphere Control for Heat Treatment Processes A 2024 Update - Real-time Monitoring Tools for Atmosphere Measurement

Real-time monitoring tools for atmosphere measurement are undergoing a significant transformation, driven by the need for greater precision and control in heat treatment processes. Smart monitoring systems, powered by IoT technology, are now capable of tracking crucial parameters like temperature, humidity, and gas composition in real-time, providing a detailed snapshot of the furnace environment. This capability is essential for fine-tuning furnace atmospheres, ultimately leading to improved material properties and a reduction in defects. Techniques such as infrared and gas analyzers, along with dew point analysis, are becoming increasingly prevalent, offering a more in-depth understanding of the complex dynamics involved in heat treatment. However, the challenge going forward isn't just about the technology itself; it's about ensuring its seamless integration and validation within real-world heat treatment environments. The practical implementation of these advanced monitoring tools will be crucial for realizing their full potential.
Real-time monitoring tools for atmosphere measurement are getting increasingly sophisticated. They can now detect changes in gas concentrations with an accuracy of up to 0.01%, which is essential for maintaining the quality of high-value materials during heat treatment processes. Some modern sensors, employing laser-based techniques, can even measure gas concentrations up to 1,000 times faster than traditional methods, allowing for instantaneous adjustments to the atmosphere within furnaces to prevent defects.
This level of precision is remarkable, but I'm cautious about the potential for calibration errors. It seems like regular maintenance will be crucial to ensure these systems are working as intended. It's also important to note that integrating these advanced tools into existing infrastructure can be expensive and challenging.
On the positive side, smart real-time monitoring systems have been shown to improve efficiency by enabling predictive analytics. This means that we can use historical data to predict future behavior, which could potentially reduce energy consumption by 15-25%. It's exciting to see how these systems are being integrated with cloud-based analytics, allowing for remote monitoring and management of heat treatment processes.
Overall, these new tools are pushing the boundaries of what's possible in atmosphere control. However, I think we still have a long way to go before they become truly commonplace. A lot depends on finding a way to make them accessible to smaller manufacturers and ensuring their long-term reliability. It's a fascinating area of development, and I'm looking forward to seeing what innovations the future holds.
Advancements in Atmosphere Control for Heat Treatment Processes A 2024 Update - Tailored Solutions for Diverse Heat Treatment Requirements
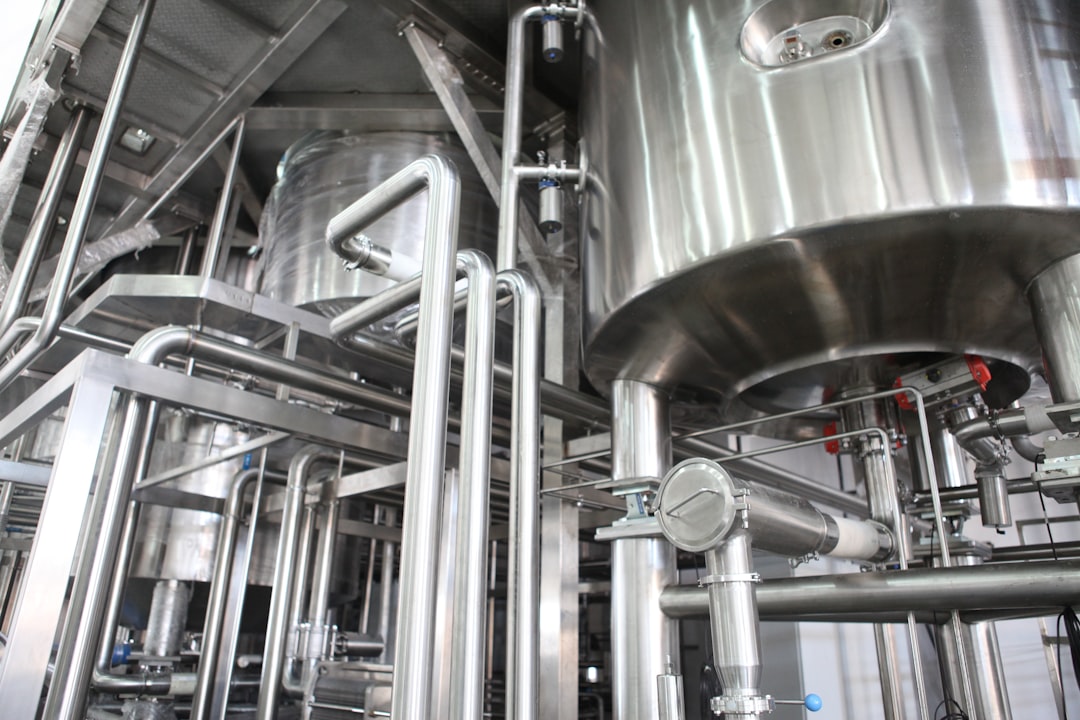
Tailored Solutions for Diverse Heat Treatment Requirements
The field of heat treatment is undergoing a major transformation, driven by a growing demand for customized solutions that meet a wide range of specific requirements. Achieving precise metallurgical outcomes has become paramount, and tailored furnace atmospheres are now crucial for optimizing thermal processes and achieving specific material properties. This means creating a controlled environment that caters to the specific needs of each material and treatment objective.
Advances in real-time monitoring and machine learning are revolutionizing this process. Now, we can dynamically adjust gas compositions within furnaces based on real-time data. This allows for a level of precision never before possible and directly influences the efficacy of treatments and the quality of finished products. For example, we can fine-tune the atmosphere to achieve specific surface finishes, minimize oxidation, or control the rate of chemical reactions.
However, these exciting advancements shouldn’t overshadow the need for rigorous testing and validation. Just because a technology is sophisticated doesn't mean it actually delivers on its promises in a real-world setting. The challenge lies in ensuring that these new integrated systems are reliable and effective across diverse sectors and applications. Ultimately, the key to success is finding a balance between sophistication and tangible, reliable results.
The realm of tailored solutions for diverse heat treatment requirements is a fascinating one, particularly when you consider the meticulous level of control that's becoming possible. We're seeing some truly remarkable advancements that push the boundaries of what we can achieve in heat treatment.
For example, achieving temperature gradients across large workpieces with less than a degree Celsius difference is something that was unimaginable just a few years ago. This kind of precision is critical to preventing stress concentrations, which can ultimately lead to material failure. But it's not just about precise temperature control; it's about real-time adaptability as well. Systems are now emerging that allow for dynamic adjustment of gas compositions during the heat treatment cycle. This ability to make immediate corrections to atmospheric imbalances is essential for maintaining the desired metallurgical properties in high-value materials.
Another aspect that's particularly intriguing is the use of RFID technology to monitor individual parts throughout the heat treatment process. This provides a detailed history of the specific conditions that each part experienced, allowing for a high level of quality control and minimizing defects. Imagine being able to analyze historical data to predict and address potential issues in real-time. That's exactly what's happening with the use of advanced analytics and machine learning in heat treatment. Some systems are even capable of learning from previous performance data to automatically adjust parameters, resulting in defect rate reductions of up to 30%.
The power of dynamic modeling techniques shouldn't be underestimated. We're now seeing software that can simulate various heat treatment scenarios, allowing engineers to test and refine their approaches without costly and time-consuming physical trials. The use of feedback loops for process control adds another layer of sophistication to these systems. These loops can automatically make adjustments based on ongoing measurements, providing an exceptional level of consistency and quality in the final product.
It's exciting to see how collaborative efforts between heat treatment specialists and materials scientists are leading to the development of highly specialized protocols that are tailored to specific alloy compositions. This deep level of understanding about the interplay of materials and heat treatment processes can lead to dramatic improvements in mechanical properties.
Layered process strategies are also gaining traction in advanced applications. This involves utilizing distinct heat treatment processes in sequential order to optimize specific phases of a material's microstructure. The outcome is a material with enhanced performance characteristics.
Custom-designed insulating materials are another area where we're seeing significant advancements. These materials are allowing for greater energy efficiency while maintaining the desired thermal profile. This reduction in heat loss contributes to the overall stability of the heat treatment process.
But perhaps the most exciting development is the alignment of tailored heat treatment solutions with Industry 4.0 principles. This integration fosters an environment of continuous improvement and optimization across manufacturing systems.
There's no question that the future of heat treatment is bright. We are witnessing a surge of innovation, driven by the desire for precision, adaptability, and data-driven decision-making. These advancements will inevitably change the landscape of how we design and manufacture products, particularly in industries that rely heavily on advanced materials.
More Posts from patentreviewpro.com: