Recent Advancements in Hydraulic Shutoff Valve Technology for Precision Flow Control
Recent Advancements in Hydraulic Shutoff Valve Technology for Precision Flow Control - Digital Hydraulic Valves Revolutionize Precision Control
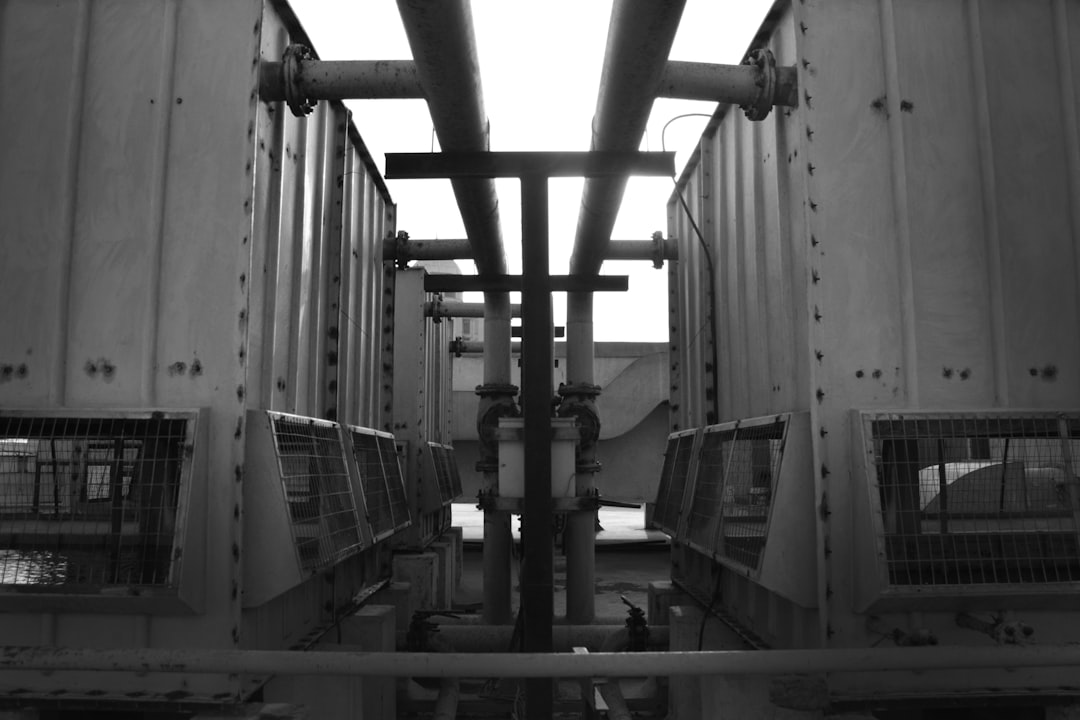
Digital hydraulic valves are transforming the landscape of precision control by offering a new level of responsiveness and efficiency in managing fluid flow. The architecture of these systems, often using parallel valve configurations like the Digital Flow Control Unit, leverages the individual strengths of each valve – rapid switching times, high reliability, and predictable performance – to achieve a greater level of control. Traditional hydraulic systems can suffer from significant energy loss due to the nature of pressurized fluid flow within complex circuits. Digital hydraulic approaches, however, address this inefficiency with a more direct and efficient approach to regulating flow.
A key benefit lies in the inherent digital nature of the control mechanisms. The use of digital signals eliminates the need for analog-to-digital conversion, resulting in a simplified control system. This simplification, in turn, enhances system response and improves the handling of both operational data and external disturbances. The adoption of digital hydraulics is gaining traction in engineering fields requiring precision control, showcasing the growing recognition of its advantages. By offering better control, higher efficiency, and reduced system complexity, digital hydraulic valves have the potential to elevate the performance and robustness of many hydraulic systems.
1. Digital hydraulic valves leverage microprocessors that offer instantaneous feedback on flow rates, leading to quicker adjustments and notably improved system response compared to traditional mechanical valves. This responsiveness is crucial in situations where fast reaction times are required.
2. These valves can be coupled with sophisticated control algorithms that refine performance. They use sensor data to anticipate flow demands and proactively adjust operation, effectively mitigating fluctuations in pressure. However, the effectiveness of these algorithms likely depends heavily on the accuracy and reliability of the sensors used.
3. It's noteworthy that integrating digital control within hydraulic systems has the potential to reduce energy consumption by up to 30%. This stems from more precise flow management, where the pump only operates when needed, thus curtailing unnecessary energy expenditure. This aspect, while promising, requires rigorous validation in diverse real-world applications.
4. The remote monitoring and control capabilities of digital hydraulic valves pave the way for predictive maintenance. By allowing engineers to forecast potential malfunctions, downtime and maintenance expenditures can potentially be minimized. But this capability relies on the continuous accessibility and integrity of the communication network.
5. The high degree of precision achievable with digital valves has made them ideal for intricate applications such as those in autonomous vehicles. In these demanding contexts, accurate flow regulation is paramount for both safety and optimal performance. However, the robustness of digital valves under extreme conditions still needs to be more thoroughly examined.
6. Unlike conventional valves that succumb to wear and tear, leading to mechanical failures, digital valves predominantly rely on electronic components, which tend to be more resilient and less susceptible to such failures over their lifespan. Yet, the long-term reliability of these electronic components in harsh industrial environments remains to be observed.
7. In situations where space is constrained, digital valves present an advantage with their smaller form factor and lighter weight. This enables the design of more compact hydraulic systems without sacrificing performance. However, the miniaturization of components might introduce new challenges concerning heat dissipation and component fragility.
8. As digital control systems progress, they are progressively incorporating machine learning methods. These algorithms adapt to changing load conditions, enhancing overall system efficiency and responsiveness across various operating situations. Nonetheless, the efficacy of machine learning in handling unforeseen or complex situations warrants further exploration.
9. The integration with the Internet of Things (IoT) broadens the capabilities of these valves. They become integral components within larger networked systems, unlocking comprehensive data analytics. This wealth of data can inform more refined system designs and operation strategies. However, privacy and security aspects associated with sharing and processing large datasets must be thoroughly addressed.
10. While the benefits of digital hydraulic systems are evident, the transition to them necessitates careful consideration of the associated software and cybersecurity risks. Since the control systems are based on software, potential vulnerabilities could have far-reaching consequences in safety-critical applications. Thus, thorough risk assessment and rigorous security protocols are indispensable for implementing digital hydraulic systems in such scenarios.
Recent Advancements in Hydraulic Shutoff Valve Technology for Precision Flow Control - Global Flow Control Industry Reaches $225 Billion Milestone
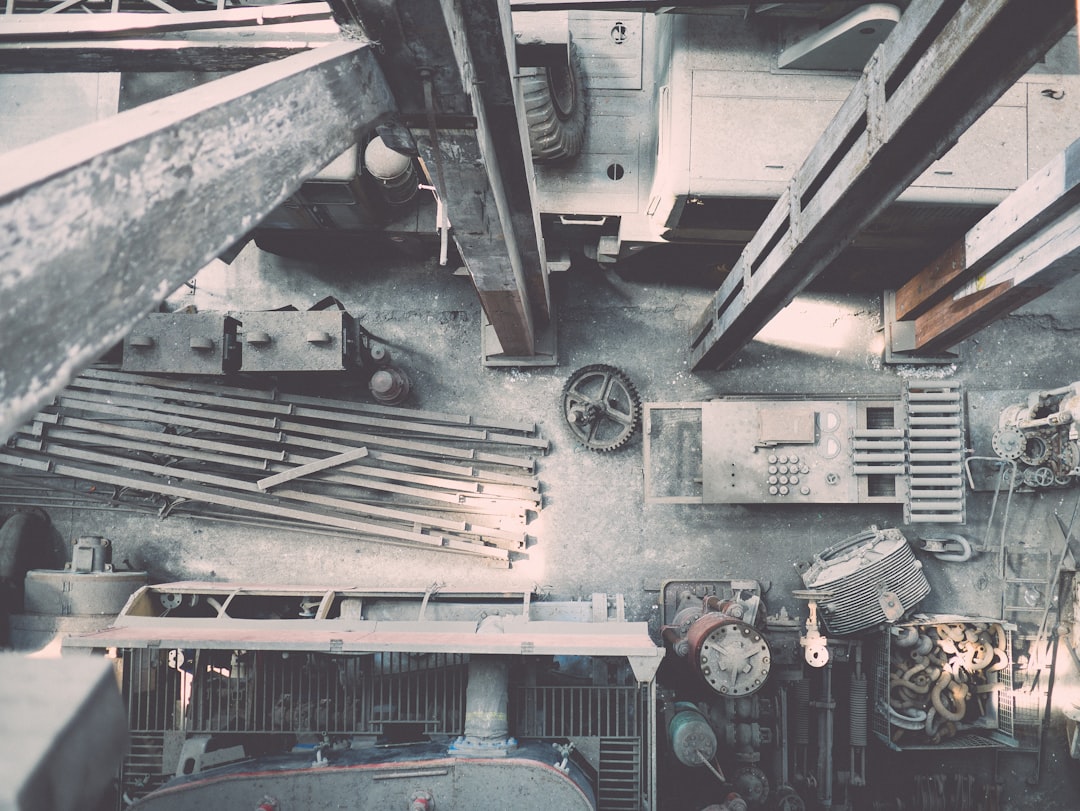
The global flow control industry has reached a noteworthy milestone, exceeding $225 billion in value. This substantial figure highlights its significance across diverse sectors, such as energy production, infrastructure, and manufacturing. Recent advancements in hydraulic valve technologies, specifically those focusing on precision flow control, are impressive, achieving remarkable accuracy and speed. These new valves can adjust flow within incredibly small increments, as small as 0.01 millimeters, and react extremely quickly, with response times as low as a tenth of a second. Despite these advancements, hurdles remain. Specifically, some hydraulic systems struggle with energy efficiency, showing operational effectiveness below 30%, a significant concern as industries focus on sustainability. The industry's future will likely depend on tackling these energy efficiency problems and fostering further innovation to accommodate the growing global need for refined flow management and control.
The flow control industry's recent achievement of a $225 billion valuation highlights the expanding need for managing the movement of fluids and gases across diverse industries. This significant market size, driven by a healthy growth rate, suggests that industries are increasingly reliant on sophisticated flow control solutions.
The hydraulics sector, a key component of flow control, is predicted to grow, partly due to the increasingly intricate demands of modern manufacturing. More complex processes often require a level of precision that traditional hydraulics struggle to achieve, pushing the need for advanced flow control solutions.
Hydraulic shutoff valves, specifically, have gained prominence in industries like aerospace and automotive. The stringent requirements for precision flow control within these sectors showcase how specialized applications can catalyze technological developments.
The rising adoption of automation within manufacturing is fueling the transition to digital hydraulic systems. These systems can be fine-tuned to optimize performance, which might eventually make traditional hydraulic systems less relevant in highly automated environments.
It's fascinating how digital hydraulics has led to a reduction in system noise. Studies have shown that precise flow control measures can significantly decrease acoustic emissions compared to older, mechanical systems. This opens up possibilities for quieter and more environmentally friendly industrial environments.
Digital hydraulic valves are designed not simply for high performance but also for self-monitoring. Many systems now include built-in diagnostic capabilities, enabling continuous performance tracking and predictive maintenance approaches. This change emphasizes a shift from reactive maintenance to proactively anticipating issues within the system.
The introduction of machine learning in hydraulic systems marks a profound shift in how we approach flow control. Algorithms, rather than solely relying on human operators, can now make real-time adjustments to optimize the system's performance. This suggests a future where human oversight might be significantly lessened.
The growing connectivity of flow control systems highlights the rising importance of cyber-physical systems, where digital and physical elements are tightly interconnected. This underscores a crucial need for strong cybersecurity measures to protect critical industrial infrastructure.
Surprisingly, the advancement of digital valve technology has not only enhanced performance but has also led to a decrease in the overall size of hydraulic systems. This enables easier integration into compact industrial settings, where space is at a premium.
While the benefits of digital flow control are substantial, the shift towards these systems necessitates a reevaluation of traditional maintenance practices. Maintaining electronic components requires a different skillset than traditional hydraulic repairs. The shift necessitates a workforce adapted to troubleshooting and maintaining this new generation of hydraulic equipment.
Recent Advancements in Hydraulic Shutoff Valve Technology for Precision Flow Control - High-Precision Valve-Controlled Systems Achieve 01 mm Accuracy
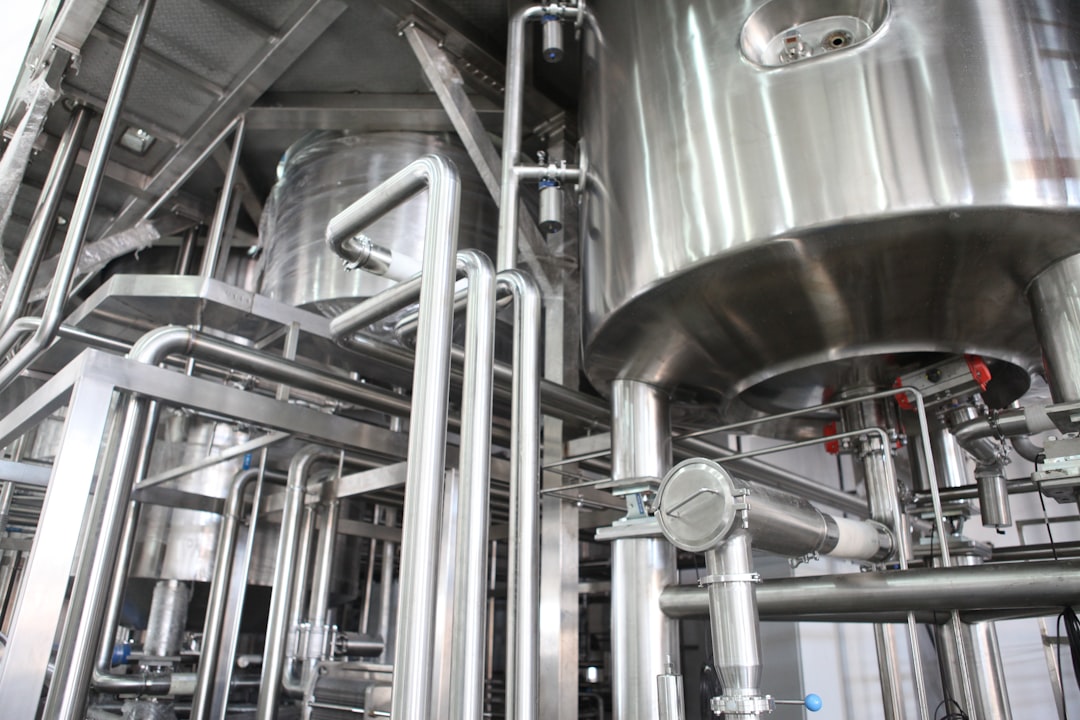
Recent advancements in hydraulic systems have enabled valve-controlled systems to achieve a remarkable level of precision, reaching accuracies of 0.01 mm. This high level of accuracy is paired with swift response times as low as 0.1 seconds, making these systems particularly suitable for applications requiring quick and precise adjustments of fluid flow. However, despite these significant steps forward, energy efficiency continues to be a major hurdle. Many systems using valves for precision control fall short, often exhibiting energy efficiency below 30%. This inefficiency can be attributed to losses due to flow throttling within the valves themselves.
Researchers have explored various solutions to overcome this issue, including the use of advanced control strategies. Adaptive fuzzy PID control has shown potential in significantly improving control accuracy, particularly when it comes to positioning. Systems employing this type of control can see position control precision enhanced by as much as 59% compared to traditional PID controllers.
While these solutions show promise, the need to balance high precision with increased energy efficiency remains a central focus for future research. This is especially true in growing areas of application like robotics and high-tech manufacturing, where the demands for precise and responsive fluid control are particularly high. Continued research and innovation in hydraulic shutoff valve technology are needed to overcome these limitations and ensure that advancements in precision flow control also address the crucial concerns of sustainability and resource management.
1. Achieving 0.01 mm accuracy in valve-controlled hydraulic systems relies on a sophisticated interplay between hydraulic and electronic components. This usually involves a feedback loop that allows for rapid adjustments to changing operating conditions, showcasing remarkable responsiveness. It's quite intriguing how precise these systems can be.
2. The accuracy of these systems doesn't just stem from the valve design itself but heavily depends on the integration of extremely sensitive sensors. These sensors can detect even the smallest changes in pressure and flow rate, ensuring the system maintains accuracy even during dynamic conditions. It's remarkable how they can keep track of everything so precisely.
3. Interestingly, the fluid used in these high-precision systems isn't always standard hydraulic oil. Synthetic fluids have been specifically engineered to improve things like lubrication, thermal stability, and response time. This leads to better overall valve performance. It's a testament to the ongoing advancements in fluid technologies.
4. When we talk about accuracy, it's worth mentioning that the manufacturing tolerances of high-precision valves are very strict. Often, these tolerances are measured in micrometers, ensuring there's very little "slop" or backlash that can affect the precision of the system. This level of manufacturing precision is crucial.
5. The digital control systems found in these valves often use redundancy for increased reliability. This means they have multiple paths or algorithms working together to ensure consistent performance. This is critical in applications like aerospace or medical devices where system reliability is paramount. It's interesting how they can build in backup systems to increase reliability.
6. The advancements in these systems have changed how prototypes are created. Engineers can now use simulations to test the fluid dynamics in real time, significantly reducing the development time for new products requiring precision control. This faster prototyping process is a major benefit.
7. A surprising outcome of this evolution is that the compact design of these new valves can sometimes reduce the overall number of components needed in a hydraulic system. This simplification leads to increased reliability and makes maintenance easier. It's impressive how a smaller design can make things simpler.
8. Despite the great accuracy that can be achieved, engineers must deal with the challenge of keeping the system stable. High-precision can lead to sensitivity to disturbances, meaning advanced control strategies are needed to maintain optimal performance. This highlights a potential trade-off between precision and stability.
9. While hydraulic systems are often perceived as less precise than other systems due to fluid compressibility, improvements in valve-controlled designs are mitigating those limitations. This opens the door for them to be used in applications that have traditionally relied on pneumatic technologies. It's interesting to see them compete with established technologies.
10. These high-precision valve systems come at a significant price. The cost-effectiveness of these systems in industries with tight margins needs careful consideration. Engineers have to determine if the enhanced capability justifies the upfront investment, especially when the application is less demanding. It's crucial to weigh the added capabilities against the increased cost.
Recent Advancements in Hydraulic Shutoff Valve Technology for Precision Flow Control - Energy Efficiency Challenges in Conventional Hydraulic Valves
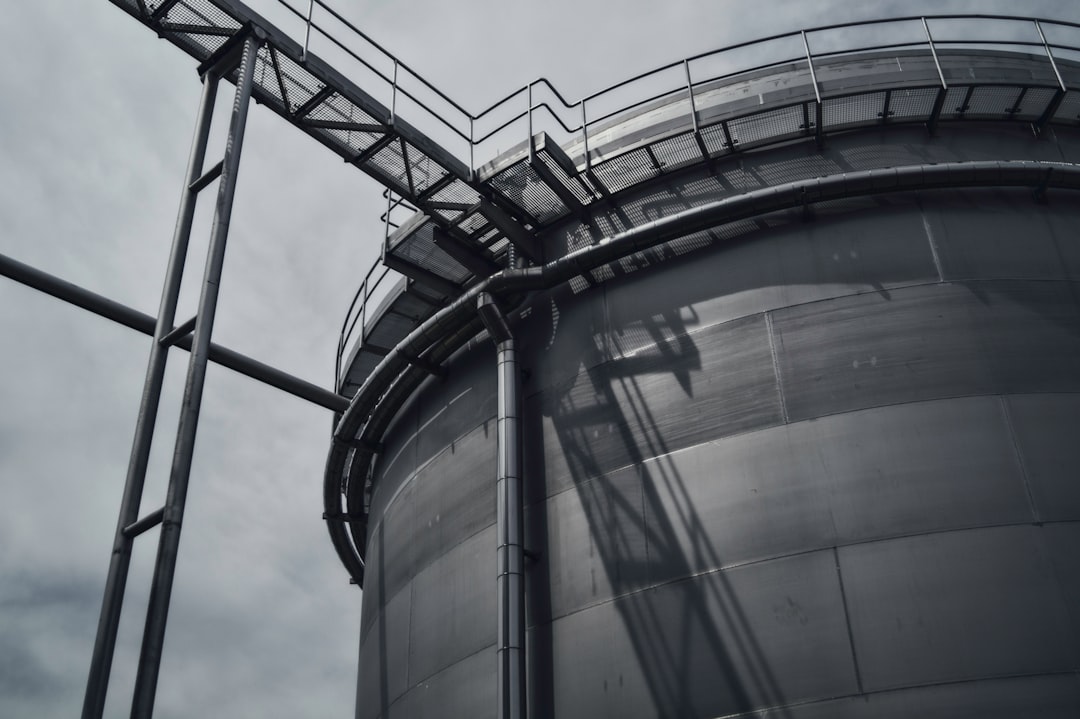
Conventional hydraulic valves present a persistent challenge when it comes to energy efficiency. A major source of this inefficiency is the energy lost through throttling, often resulting in systems with overall efficiency rates below 30%. This low efficiency is becoming a growing concern as industry emphasizes sustainability and resource conservation. In contrast, pump-controlled hydraulic systems offer an alternative approach with much higher efficiency rates, typically between 60-80%, as they eliminate the need for conventional flow control valves. Although innovations like digital and programmable valves have advanced the precision and energy-saving capabilities of newer hydraulic systems, the inherent energy inefficiency of traditional valve designs remains a crucial hurdle. To address this, research into smarter control methods and valve components is crucial. This ongoing research aims to enhance energy efficiency without sacrificing the precision that modern applications require for efficient fluid flow management.
Traditional hydraulic valves present several hurdles when it comes to energy efficiency. One significant issue is internal leakage, which can lead to energy losses of 20-40% of the system's power input. This not only reduces overall efficiency but also makes controlling the system more complex, demanding more robust design approaches.
Accuracy in traditional systems can be hampered by factors like hysteresis and friction, which can distort performance by up to 10% in crucial applications. These mechanical constraints necessitate more rigorous maintenance schedules and more frequent adjustments to keep the system operating within specifications.
Operating pressures in conventional hydraulic valves generally range from 1500 to 5000 psi. However, pushing towards the upper limits of this range can negatively impact efficiency and hasten wear, ultimately contributing to increased maintenance costs and downtime.
The sensitivity of hydraulic fluids to temperature variations is another challenge. A mere 10% change in viscosity can result in a 50% jump in energy use due to suboptimal flow conditions, emphasizing the narrow operating window that conventional systems must adhere to.
The intricate nature of hydraulic circuits often leads to cavitation, a phenomenon that can cause harm to components. Research suggests that cavitation can reduce flow efficiency by up to 30%, potentially compromising the dependability of the entire system.
Interestingly, even small misalignments during the installation of a conventional valve can cause a significant drop in system efficiency – as much as 25%. This highlights the critical need for accuracy during assembly and regular maintenance to avoid detrimental effects.
Contrary to the intuitive notion that bigger valves always equate to better flow, inefficient valve designs can lead to higher pressure drops, adversely affecting energy efficiency. Achieving a good balance between valve size and flow is crucial.
The extensive piping and fittings typically found in conventional hydraulic systems can create friction losses and hinder maintenance efforts. Each additional fitting can potentially introduce a 5-10% reduction in efficiency due to flow disruptions.
Flow control in these systems is largely achieved through mechanical throttling, which can lead to substantial energy dissipation as heat. This approach can lead to thermal runaway issues if not properly managed, creating potential risks for the system's operation.
Based on observations from real-world systems, many conventional hydraulic systems operate at an efficiency rate below 30% under typical operating conditions. This observation raises questions about the ability of older hydraulic technology to meet the increasing demand for precision in modern applications, particularly in sectors where energy conservation is a key factor.
Recent Advancements in Hydraulic Shutoff Valve Technology for Precision Flow Control - Advanced Solenoid Actuation Improves Response Time and Accuracy
Modern hydraulic shutoff valves are leveraging advancements in solenoid actuation to achieve faster response times and greater accuracy in fluid control. The use of high-performance solenoids allows for quicker opening and closing of valves, with some designs achieving closure times around half a millisecond and opening times just a bit slower. This improved speed is vital for applications requiring swift and precise flow adjustments, like those found in aerospace or automotive systems. It's important to note that increasing the mass of the solenoid's moving parts can negatively impact these fast response times, making optimal design a continuing challenge. As the field continues to move towards digital and automated control strategies, the interplay between solenoid technology and control algorithms will become increasingly important in driving progress in the area of precise flow regulation. There are still potential drawbacks to explore, but for now, the advancements in solenoids are bringing tangible benefits to the field.
Solenoid actuation has emerged as a promising method for improving the responsiveness and precision of hydraulic shutoff valves. Recent advancements in this technology have yielded impressive results, with some solenoid valves demonstrating response times as low as 50 milliseconds—a significant improvement over traditional hydraulic systems which often take several seconds to respond to changes. This swift reaction is made possible through more refined solenoid design, leading to quicker and more precise control of fluid flow.
This enhanced speed translates to a marked increase in system accuracy. Solenoid-operated valves often achieve flow rate variations as low as 1% of the desired setpoint. This level of precision is crucial in applications where even slight changes in flow can have severe consequences, such as in medical devices or aircraft systems. It's remarkable that such fine-grained control is now readily achievable.
The speed of solenoid valves also extends to the frequency of operation. They can switch fluid paths at rates up to 5 Hz, allowing them to be integrated into applications that demand high-frequency control, such as those found in automated manufacturing. However, maintaining this speed under extreme operating conditions presents a research challenge.
High-power solenoids are another key area of advancement, with some capable of handling pressures up to 700 bar while still retaining a smaller footprint than traditional valves. The ability to increase pressure handling in a smaller package could lead to significant design simplifications. It would be interesting to see the practical application of this innovation in the field.
In safety-critical applications, the fail-safe mechanisms incorporated into advanced solenoid designs are a major benefit. These mechanisms ensure that valves remain in a desired position (open or closed) even if electrical power is lost. This added reliability makes these valves particularly well-suited for situations where system failure could have catastrophic consequences. Yet, if this reliability relies solely on electronic components, one has to be wary of the implications on long-term system durability and the potential for increased maintenance over time.
Compared to conventional valve systems, solenoid-operated valves show less susceptibility to mechanical wear and tear. This potentially lowers maintenance costs and increases the system's overall lifespan. However, a critical examination reveals that this advantage is balanced by potential issues concerning the durability and reliability of the electric components. Harsh industrial environments can subject electrical components to stress, and their long-term performance under such conditions may necessitate more intensive maintenance practices than anticipated.
The incorporation of digital feedback and adaptive control algorithms in some advanced solenoid designs represents another area of innovation. These algorithms can adapt valve operation in response to changing process demands, allowing systems to self-tune for optimal performance. These self-adjusting systems offer a potential reduction in manual operator adjustments, though further research is needed to ensure they perform reliably under a wider range of conditions.
While advantageous, solenoid valves are not immune to environmental influences. Shifts in temperature can affect their performance, potentially causing changes in coil resistance that could affect response times and energy consumption. Understanding the extent of these effects and developing design techniques to mitigate them is important.
One of the most noticeable benefits of recent advancements is the ability to miniaturize solenoid components. This allows designers more flexibility to integrate valves into compact spaces without sacrificing performance. However, miniaturization may raise questions about the ability to dissipate heat effectively, especially within confined areas.
Despite these numerous advantages, it's crucial to acknowledge that solenoid actuation also carries potential drawbacks. For example, electromagnetic interference (EMI) can impact operation in sensitive environments, necessitating careful design consideration to minimize these effects. Shielding and grounding are often used in mitigating EMI, but further innovations in the technology itself are needed to minimize or eliminate such concerns.
Recent Advancements in Hydraulic Shutoff Valve Technology for Precision Flow Control - Digital Flow Control Units Enable Precise Multi-Valve Operations
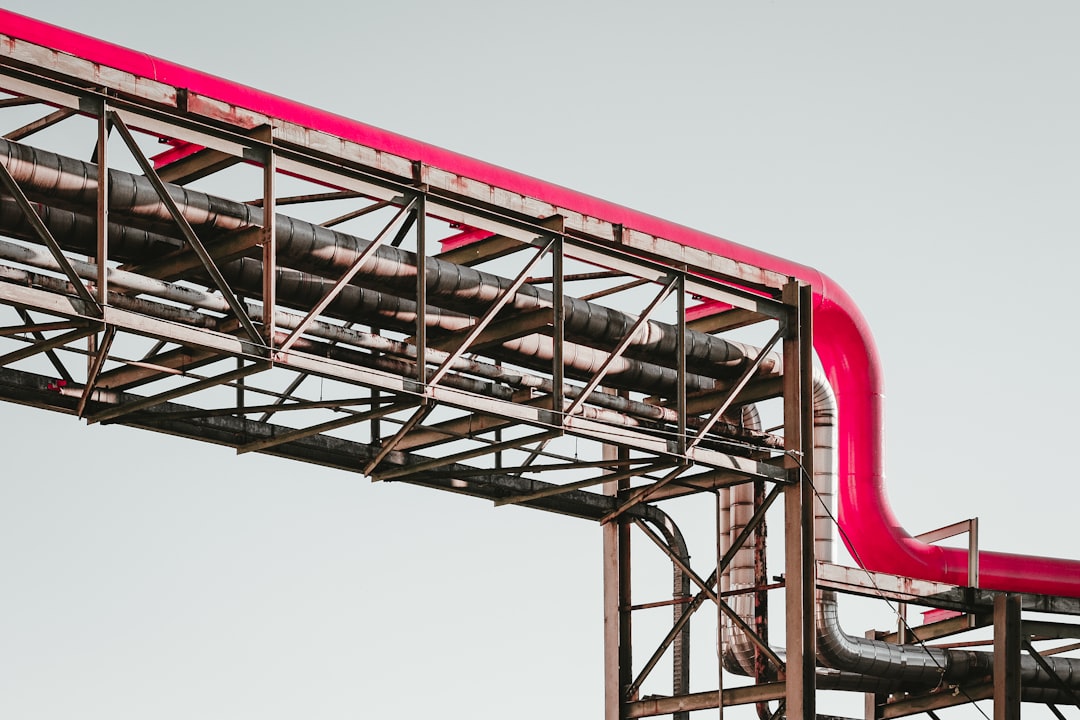
Digital flow control units represent a significant step forward in managing multiple valves within hydraulic systems, offering a new level of accuracy and control. By integrating digital control, these units enable real-time monitoring and manipulation of fluid flow, allowing for extremely precise adjustments. This level of control is vital for intricate applications found in fields such as aerospace, automotive, and manufacturing, where fine-tuned fluid management is critical. While traditional hydraulic systems often suffer from inefficiency due to pressure loss and slow response times, the digital approach minimizes these issues. However, the reliance on electronic components raises concerns about long-term durability and maintenance challenges in harsh environments. Though the potential benefits are considerable, issues like environmental sensitivity and maintenance requirements still need careful consideration when adopting these units. Overall, digital flow control is changing the landscape of hydraulics, but it also highlights a persistent tension between innovative capabilities and reliable, durable design in demanding industrial settings.
Digital flow control units (DFCUs) offer a new way to manage multiple valves in a coordinated fashion. This capability allows for intricate fluid control tasks that were previously difficult to achieve with traditional systems. By synchronizing multiple valves, these systems can optimize fluid flow across various channels, resulting in improved overall system efficiency. It's interesting how the synchronized valve operation can improve overall system efficiency.
The use of sophisticated solenoid technology has enabled significant advancements in the miniaturization of digital valves. Consequently, DFCUs can be designed in more compact forms, making them adaptable to tighter spaces in a variety of applications. This is noteworthy because we can now have complex functionality in limited spaces.
DFCUs use sophisticated modeling algorithms that can predict flow disruptions in real time. The algorithms can then adjust valve positions preemptively, effectively ensuring the system stays within its optimal operating parameters. While this preemptive approach sounds promising, it is important to recognize that the effectiveness of this relies on the ability of the algorithms to accurately predict disturbances.
The high-speed capabilities of the solenoid actuators in these systems are remarkable. They can switch valves significantly faster than their mechanical counterparts. The improved speed is crucial for applications that require extremely quick adjustments to accommodate fluctuating demand, which will impact many industries in the near future. However, it is likely that maintaining this speed across a wide range of operating conditions may still be challenging.
While hydraulic systems are commonly associated with standard hydraulic oils, the capabilities of DFCUs are not limited to conventional fluids. DFCU systems can now leverage custom-formulated hydraulic fluids that are specifically designed to enhance performance across a variety of factors. This opens possibilities for more efficient hydraulic operations, but it also necessitates a careful consideration of the properties of the chosen fluid. This idea of bespoke hydraulic fluids is certainly a change in thinking from what we've seen in the past.
Interestingly, DFCUs can adapt to operational patterns using machine learning techniques. This adaptive capability allows systems to learn from historical data and optimize future valve performance. It will be exciting to see how this develops, but it is important to keep in mind that this capability is a relatively new development, and the full extent of its benefits and limitations are still under investigation.
DFCUs offer a new level of precision in flow control. The accuracy of flow control has improved, often enabling the precise regulation of flow rates down to 0.01 millimeters. This level of accuracy has implications for a variety of applications that require a very tight control of fluid flow, and it will be important to see where these types of systems are most useful.
The implementation of digital components in these units might lead to higher upfront costs. However, the reduction in long-term maintenance requirements and energy consumption could ultimately result in significant overall cost savings. Although the economics of this approach might be appealing, it is important to carefully consider the specific application and operating conditions to ensure that the higher upfront costs are justified.
The diagnostic capabilities built into these systems provide real-time insight into the health of the system. This functionality allows for potential failure points to be identified before they become major problems. Consequently, maintenance can be transitioned from a reactive approach to a more proactive one, potentially leading to a longer lifespan for hydraulic systems. This is certainly a useful capability, and it will be interesting to see how it is utilized in various applications.
As the field of hydraulics transitions towards DFCUs, maintenance personnel must adopt new skills. Traditional mechanical maintenance expertise will be less important as the reliance on digital and software-based controls increases. This transition will require a shift in training and education for the workforce. The changes in maintenance needs of these systems present a substantial challenge for the workforce, but it is also an opportunity to update and refresh the knowledge base of those who work with hydraulic systems.
More Posts from patentreviewpro.com: