Pneumatic Pistons Versatile Workhorses in Modern Industrial Automation
Pneumatic Pistons Versatile Workhorses in Modern Industrial Automation - Types of Pneumatic Pistons in Industrial Applications
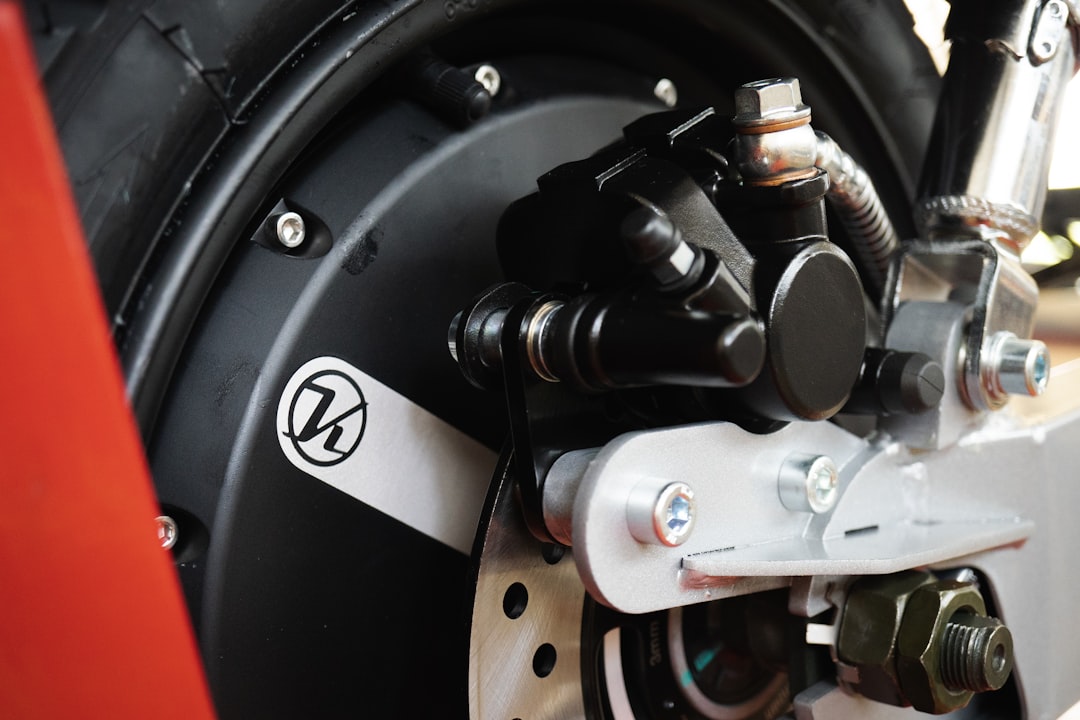
Pneumatic pistons are versatile tools in industrial settings, converting compressed air into linear or rotary motion. Their adaptability makes them suitable for a wide range of tasks, from delicate handling to heavy-duty operations.
One of the key aspects of pneumatic piston design is the distinction between single-acting and double-acting cylinders. Single-acting cylinders utilize compressed air for motion in one direction, relying on a spring to return the piston. Double-acting cylinders, on the other hand, utilize compressed air for both forward and reverse movements. This flexibility allows for diverse applications, encompassing everything from automotive components to aerospace control systems.
However, utilizing these pistons requires careful consideration of safety protocols. The high-pressure nature of compressed air and the potential for unexpected motion necessitates appropriate safety measures to prevent accidents.
Pneumatic pistons are the workhorses of many industrial processes, but delving deeper reveals a diverse world of specialized designs. Double-acting pistons, which use compressed air for both extension and retraction, offer versatility for continuous motion applications. In contrast, single-acting pistons rely on springs for return movement, limiting their functionality. Rotary pneumatic actuators, a unique design, convert air pressure into rotational motion, making them indispensable in applications requiring precise angular positioning, such as robotic arms.
The materials used in piston construction significantly impact their performance and longevity. While lightweight aluminum is favored for its corrosion resistance, stainless steel offers superior durability in harsh environments. Cushioned pistons help reduce the impact force at the end of a stroke, extending equipment lifespan and enhancing safety. Non-cushioned pistons, on the other hand, risk accelerated wear and tear due to abrupt stops.
While operating within the typical pressure range of 80 to 120 psi is optimal, exceeding this range can lead to piston failure due to either insufficient force production or overheating. The size variability of pneumatic pistons allows engineers to design compact systems without sacrificing performance, making them ideal for space-constrained applications. They operate at speeds of 0.5 to 1 meter per second, which can be vital in applications where timing is critical, such as assembly lines.
While specialized designs cater to specific industries, such as the food and beverage sector, where hygiene and corrosion resistance are crucial, there are considerations regarding energy efficiency. While pneumatic pistons offer rapid cycle times, they can be less energy-efficient compared to electric actuators, especially in applications that don't require high speeds. Integrating sensors into modern pneumatic piston systems enables real-time feedback on position and performance, leading to enhanced automation and control. This technology paves the way for predictive maintenance, potentially reducing downtime in industrial settings.
Pneumatic Pistons Versatile Workhorses in Modern Industrial Automation - Key Components of Pneumatic Control Systems
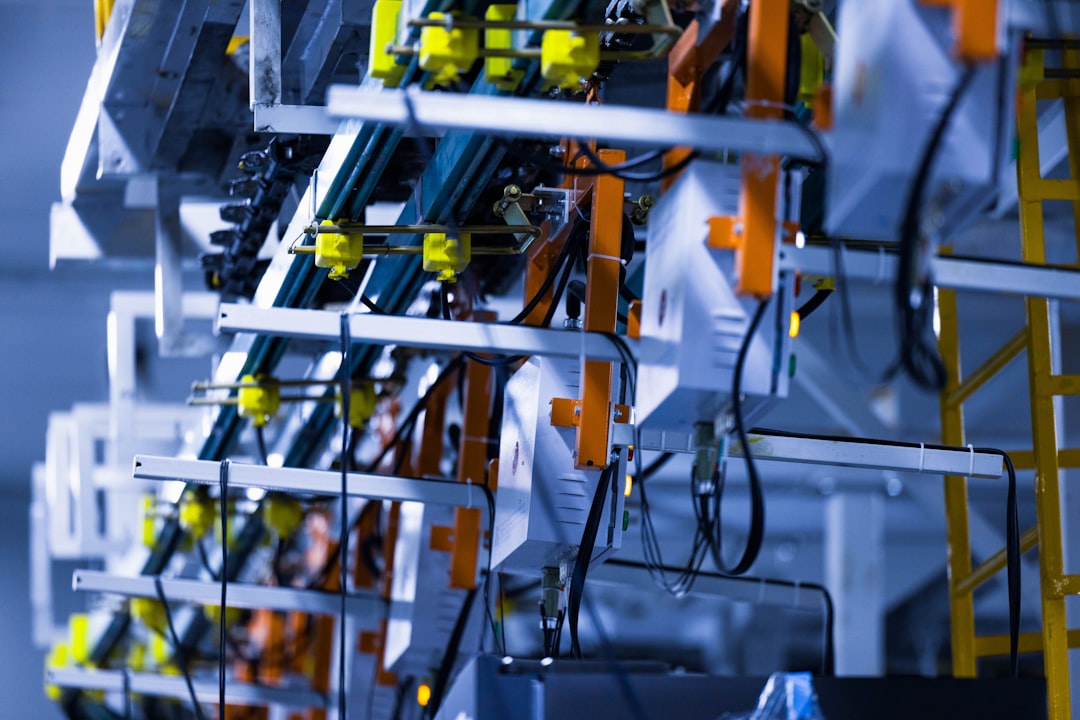
Pneumatic control systems are a cornerstone of industrial automation. They rely on a handful of essential components to convert compressed air into mechanical movement. The core of these systems is the pneumatic piston, which transforms the energy of pressurized air into linear motion. These pistons reside within cylinders, which provide a sealed environment for their movement. Airflow is regulated by ports, ensuring the proper direction and pressure of the air powering the piston. Seals are critical for maintaining system integrity, preventing leaks and ensuring sustained pressure. The configuration of the actuator can vary, from traditional NFPA tierod designs to more compact versions, each suited for specific needs. While pneumatic control systems are highly durable and integrate well with digital controllers and sensors, their design and implementation require careful attention to avoid potential operational challenges. Understanding these components is vital for achieving optimal performance and reliability in various industrial applications.
Pneumatic control systems are a fascinating blend of mechanical and electrical components, and their intricate workings are always worth exploring. While we often focus on the power of pneumatic pistons, it's equally important to understand the key players behind their performance.
Think of a pressure regulator as the gatekeeper of a pneumatic system. It ensures a steady output pressure even if the input pressure fluctuates wildly, which is essential for maintaining predictable piston movement and preventing equipment damage from sudden pressure spikes.
Directional control valves, like four-way valves, are the traffic cops of pneumatic systems, directing the compressed air to specific components. Imagine a double-acting cylinder: the four-way valve carefully manages the air flow, allowing for both extension and retraction with precision. This intricate dance is what enables the cylinder to perform complex movements with finesse.
And just as we take care of our engines, pneumatic systems need air preparation units to stay healthy. These units, including filters, lubricators, and regulators, work like a miniature mechanic shop for compressed air. They remove pesky moisture and particles, extending the life of the system and keeping it running smoothly.
Speed control valves, on the other hand, act like the accelerator pedal of a pneumatic actuator. They enable engineers to fine-tune the movement speed of pistons, which is critical in applications requiring precise timing. Think of an automated assembly line: these valves ensure each movement happens at just the right moment, creating a symphony of coordinated action.
However, pneumatic systems, despite their power, aren't immune to inefficiency. Leaks can be a real energy drain, and maintaining a leak-free system is crucial for optimal performance. Imagine a pinhole leak: it might seem insignificant, but over time, it can drain a considerable amount of energy, impacting the system's efficiency.
And then we have check valves, the safety guards of pneumatic systems. They prevent backflow, ensuring air travels only in the intended direction. This prevents unwanted pressure buildups and safeguards the system from potential failures.
The language of pneumatic systems is often expressed in visual diagrams, showcasing the relationship between components and the flow path of air. These diagrams, a combination of art and engineering, provide a roadmap for understanding how each element interacts.
Silence is golden, even in pneumatic systems. Silencers, often placed at exhaust ports, act like sound dampeners, reducing the noise generated by escaping air. This not only improves the working environment but also enhances safety by minimizing potential distractions.
Back pressure, another critical factor, can hinder a system's efficiency and even lead to actuator failure. Monitoring and controlling back pressure is crucial, akin to ensuring a healthy blood pressure for the system.
Finally, pneumatic systems are increasingly merging with digital technologies. Sensors and programmable logic controllers (PLCs) are weaving their way into these systems, opening doors for enhanced automation, advanced monitoring, and diagnostics. This integration creates a new level of intelligence, minimizing downtime and improving overall efficiency.
Pneumatic control systems are a fascinating world of interconnected components, each playing a crucial role in a well-orchestrated system. Understanding these elements, from the meticulous control of pressure to the subtle dance of air flow, is key to unlocking their full potential.
Pneumatic Pistons Versatile Workhorses in Modern Industrial Automation - Energy Efficiency Advancements in Pneumatic Technology
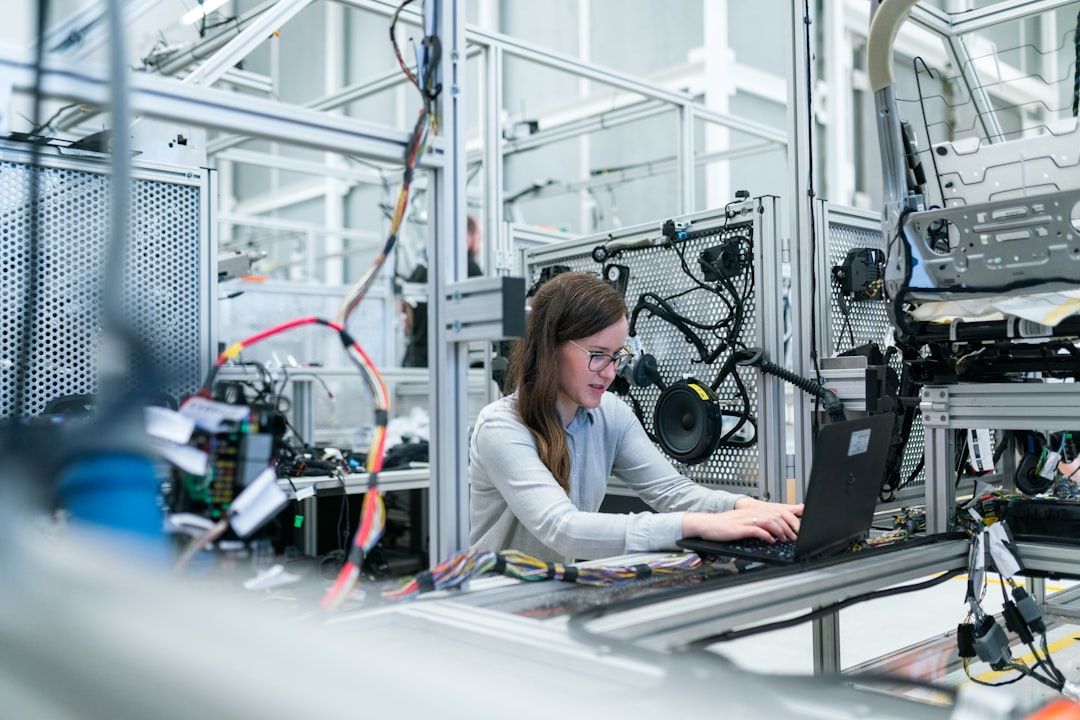
Pneumatic systems are undergoing a transformation, fueled by a push for greater energy efficiency. While pneumatic pistons are known for their power and versatility, they haven't always been the most energy-conscious. However, recent advancements are changing the game. Even small improvements in compressed air systems can translate into significant cost savings over time. The introduction of "smart pneumatics" has given rise to a new generation of systems where components like valves can now collect and share performance data, paving the way for more optimized operation.
The field is also witnessing the emergence of energy storage devices specifically designed for pneumatic systems. These innovations utilize the unique properties of materials to store energy efficiently, effectively extending the reach of compressed air technology. As industries become increasingly integrated with the Internet of Things, the potential for further breakthroughs in pneumatic system efficiency is enormous. With data collection and analysis at the forefront, these systems are poised to become even more intelligent and responsive, ultimately leading to greater productivity and sustainability within manufacturing environments.
The efficiency of pneumatic systems, while often overlooked, is a critical area of research and development. Traditional pneumatic systems, with their reliance on compressed air, have been known for their robustness and versatility but not necessarily for their energy efficiency. However, recent advancements are shifting this paradigm.
Energy recovery systems, for example, have emerged as a promising area. Technologies like regenerative braking, already common in electric vehicles, are now being adapted to capture and reuse energy that is typically lost during the operation of pneumatic actuators. This approach could lead to energy savings of up to 30%.
Optimizing operating pressure is another avenue for improving efficiency. Studies suggest that lowering standard operating pressures from 100 psi to 80 psi can yield energy savings of 20-30% without impacting performance. This adjustment is particularly relevant for systems where high pressures are not strictly required.
Smart pneumatic controls are another intriguing development. These systems leverage AI algorithms to predict and adjust air flow rates in real-time, ensuring just-in-time delivery of compressed air to pistons. This eliminates wasteful air delivery during non-peak periods, significantly enhancing energy efficiency.
The pursuit of lightweight materials is a crucial aspect of the ongoing quest for improved efficiency. Exploring materials like carbon fiber composites, known for their strength-to-weight ratio, could result in lighter and more responsive pneumatic actuators, further reducing energy consumption.
Advanced cushioning technologies within pneumatic systems also play a vital role. By minimizing energy losses due to shock at the end of strokes, these technologies contribute to quieter operation and improved energy efficiency by up to 15%.
Minimizing air losses, particularly those resulting from leaks, is an ongoing challenge. Modern high-performance seals are being developed to reduce leak rates from an industry average of 20% down to under 5%, significantly improving energy use.
Computational fluid dynamics (CFD) simulations are becoming increasingly prominent in the design phase of pneumatic systems. These simulations allow engineers to model airflow accurately and identify potential energy inefficiencies before physical implementation, leading to more efficient designs.
Integrating variable frequency drives (VFDs) with pneumatic systems is proving to be highly effective. VFDs modulate air compressor speeds based on demand, resulting in energy savings of up to 50% compared to traditional constant-speed compressors.
The adoption of wireless sensor networks for monitoring system performance enables predictive analytics. This capability allows for timely maintenance interventions that optimize energy consumption and extend equipment lifespan.
Finally, advanced control algorithms, such as model predictive control (MPC), optimize the command inputs for pneumatic actuators. By analyzing and adjusting pressure and flow dynamically, MPC significantly enhances operation efficiency.
The future of pneumatic technology is undeniably moving toward greater energy efficiency. These advancements, coupled with ongoing research and development, are shaping a more sustainable and efficient future for pneumatic systems in various industrial applications.
Pneumatic Pistons Versatile Workhorses in Modern Industrial Automation - Integration of Pneumatic Pistons with Digital Control Systems
The integration of pneumatic pistons with digital control systems is a major development in industrial automation. This merging of technologies opens up new possibilities for enhancing functionality and efficiency. The use of digital pneumatic valves and industrial Ethernet protocols like IO-Link creates a seamless connection, allowing for real-time monitoring and dynamic adjustments to pressure and motion control. This digitalization brings about streamlining of operational processes and makes them more cost-effective, eliminating the need for extensive wiring and simplifying traditional pneumatic systems.
The advancements in smart pneumatic technologies, including sensors and wireless communication, are expanding the range of applications, particularly in handling delicate materials. As industries demand more responsiveness and efficiency, the combination of pneumatic technology with digital control holds significant promise for future innovation.
The integration of pneumatic pistons with digital control systems is fascinating. It's like giving these powerful mechanical workhorses a brain. Digital control systems offer fine-grained control, allowing us to precisely adjust the movement and force of pistons in real-time. This is crucial in environments where tasks need to be completed quickly and with accuracy.
It's not just about precise control, but also about smart control. Digital control systems can be programmed with algorithms that optimize air usage, reducing energy consumption. It's like making the system "think" about how much air is needed for each movement, minimizing waste.
These systems also connect pneumatic pistons to the Internet of Things (IoT), opening a new world of data collection and monitoring. We can keep a constant eye on these pistons, gathering data to anticipate potential problems before they occur. This predictive maintenance capability minimizes downtime, a huge benefit in industrial settings.
What’s more, these digital systems can make pistons react much faster. We can get them to respond in milliseconds, essential for precision tasks like robotic assembly. It’s like adding lightning-fast reflexes to our mechanical systems.
There are also safety benefits. Digital control systems can incorporate automatic shut-off features, preventing accidents during unforeseen events. It's an added layer of protection, ensuring the system won't run out of control.
And it’s not just about individual pistons; these digital brains can also coordinate the movements of multiple pistons working together. This allows for complex, coordinated movements beyond the capabilities of manual control. Imagine a whole choreography of pistons, precisely synchronized for complex tasks.
Programmable Logic Controllers (PLCs) are essential parts of this integration. They allow us to automate complex sequences, from simple push-and-pull movements to intricate material handling processes, streamlining the workflow.
One of the biggest advantages is remote control. We can monitor and operate pneumatic cylinders from a distance, a real game changer for hazardous environments or situations where minimizing on-site personnel is essential.
Digital systems also bring sophisticated energy management tools to the table. They analyze air consumption trends, helping industries optimize energy use and reduce operational costs significantly.
Finally, sensors built into these systems create real-time feedback loops. They continuously inform the digital control system about the piston's position and pressure, enabling immediate adjustments for optimal performance and accuracy.
Overall, the integration of digital control with pneumatic pistons is a game changer for industrial automation, bringing precision, efficiency, safety, and a new level of intelligence to these powerful tools.
Pneumatic Pistons Versatile Workhorses in Modern Industrial Automation - Pneumatic Piston Applications in Robotics and Material Handling
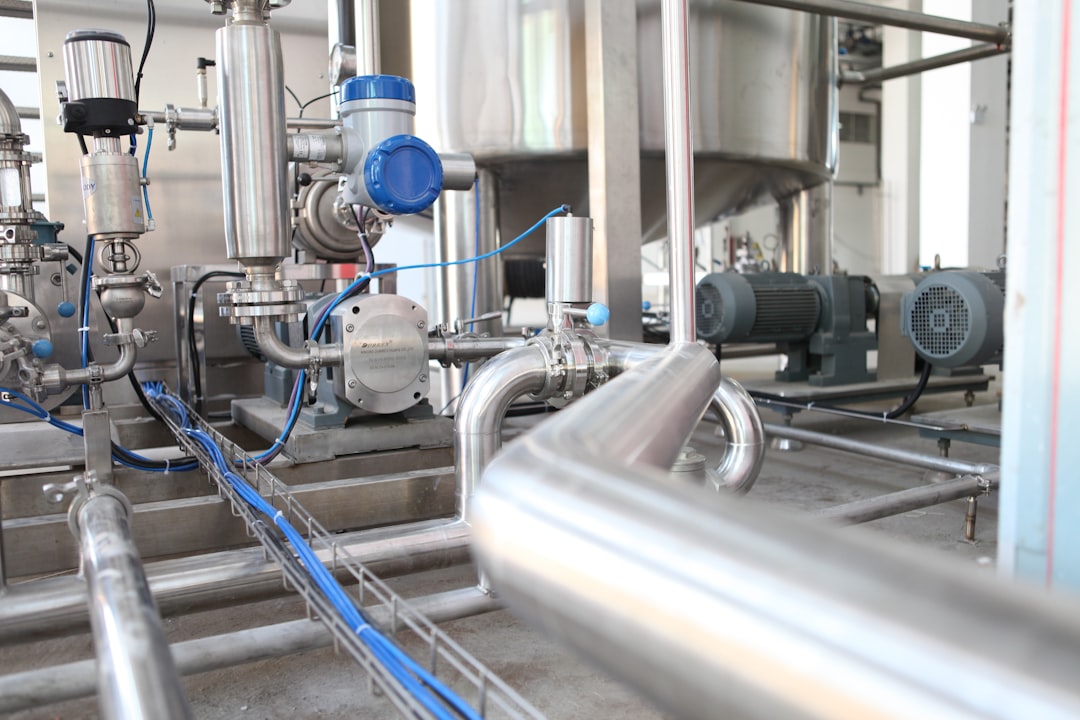
Pneumatic pistons are becoming increasingly commonplace in robotics and material handling applications, demonstrating their adaptability within modern industrial automation. These pneumatic actuators, especially double-acting cylinders, are widely used for tasks like sorting and assembling products because they offer quick response times and linear motion capabilities. New designs, such as pneumatic robot arms, improve operational space and efficiency, while the development of soft robotics innovations like self-folding actuators showcase the potential for adaptable solutions in a range of applications. The use of pneumatic systems in automation not only improves production efficiency but also offers significant cost reductions by streamlining labor requirements. However, challenges remain in ensuring energy efficiency and system reliability, highlighting the need for ongoing advancements and careful integration with digital control technologies.
Pneumatic pistons are fascinating tools in robotics and material handling. They're like the muscle behind the robotic arm, providing the strength and precision needed for complex tasks. Here are a few things that make me think they are worth researching:
Firstly, the control they offer is impressive. I'm fascinated by how they achieve fine, consistent movements, essential for things like delicate assembly. This is all thanks to their ability to provide a controlled linear motion and force, which is incredibly important for these kinds of applications.
Secondly, the speed is something to consider. Pneumatic pistons can move incredibly fast, up to 600 mm/s, making them perfect for high-speed processes, like on automated assembly lines, where time is critical. It's amazing to think of the speed and accuracy they achieve.
Thirdly, it's interesting how they can adjust grip dynamically. This is particularly helpful for handling fragile items. Imagine a robot gently picking up a delicate component without causing damage. That's something that relies on smart pneumatic systems, a fascinating application of this technology.
Also, their compact size is a major plus, especially in situations where space is tight. They allow for creative robotic arm designs without compromising efficiency or maneuverability. It's like a compact muscle that can fit into small places.
Another factor that excites me is their built-in cushioning. This helps to absorb impacts, protecting the piston and the entire robotic system, which, in turn, leads to a longer lifespan. It's like giving the system a bit of extra resilience.
I'm intrigued by how they can provide real-time positional feedback through integration with sensors. This means that robotic systems can adjust their movements quickly and accurately, something that's crucial for material sorting, reducing errors and enhancing accuracy.
Finally, their versatility is noteworthy. They have a wide range of applications, from automotive assembly to pharmaceutical manufacturing, which is testament to their ability to adapt to various conditions and handling requirements.
All these features make me believe that pneumatic pistons are a key component of modern industrial automation. They bring a unique blend of strength, precision, and flexibility to robotics and material handling, paving the way for smarter and more efficient systems.
Pneumatic Pistons Versatile Workhorses in Modern Industrial Automation - Challenges and Future Developments for Pneumatic Actuators
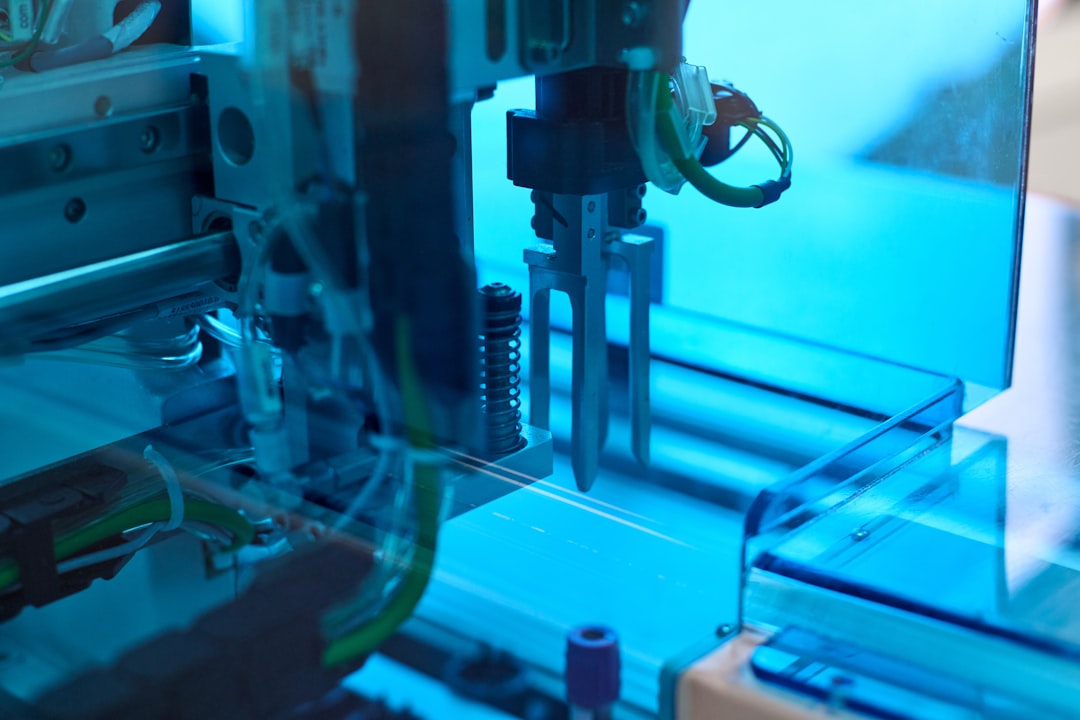
Pneumatic actuators, despite their established role in industrial automation, are facing evolving challenges and opportunities. While their inherent power and versatility are undeniable, they often fall short in energy efficiency compared to electric counterparts. This has led to a focus on improving energy management, with innovations like energy recovery systems and the use of lightweight materials gaining traction. The integration of smart technologies, including sensors and data collection, is also paving the way for more sophisticated automation and predictive maintenance. These advancements are set to reshape the future landscape of pneumatic actuators in industrial settings, bringing about new possibilities and challenges for their adoption.
Pneumatic actuators, despite their widespread use in industrial automation, face several challenges that need to be addressed to further improve their performance. Temperature fluctuations can significantly impact their efficiency, as air density varies with temperature. This means we need smart systems that can compensate for temperature changes to maintain consistent operation. Another hurdle is the internal friction and turbulence within the system, which can impede speed and efficiency. Using sophisticated tools like computational fluid dynamics (CFD) simulations could help us design actuators with optimal shapes and sizes to minimize these issues.
One unique challenge specific to pneumatic systems is the compressibility of air. This means that the force generated by a pneumatic actuator can vary depending on the pressure, unlike a more predictable electric actuator. This can lead to more dynamic handling of loads but also necessitates careful control to regulate pressure for consistent performance.
Air leaks continue to be a significant concern, with estimations suggesting that as much as 20-30% of the air used in traditional systems can be lost through leaks. This translates into reduced efficiency and wasted energy. Therefore, research and development efforts are focused on developing better seals and leak detection systems to minimize these losses.
It's fascinating how the field is using control algorithms to enhance pneumatic system efficiency. Model predictive control (MPC) is a promising approach that uses real-time operational data to dynamically adjust pressure and flow rates, leading to optimized air consumption.
Materials science is also playing a crucial role in improving the robustness of pneumatic actuators. The development of advanced polymers and composites is paving the way for more durable designs that can withstand harsher conditions and offer better performance over time.
One surprising aspect of pneumatic actuators is their surprisingly fast cycle time. They can operate at speeds of up to a fraction of a second, making them suitable for high-speed automation processes, particularly those found in assembly lines that require rapid, sequential movements.
Soft robotics is another exciting field where pneumatic actuators are changing the game. These actuators are typically made of inflatable materials, challenging the traditional rigid designs. This allows for flexible, adaptable shapes and gentler interactions, opening up a new world of applications, such as in biomedical and food handling.
Digital twin technology, where virtual models replicate the performance of real-world systems, is also being integrated into pneumatic systems. This allows for real-time simulations without interrupting actual production, providing valuable insights for maintenance and optimization.
Despite their impressive power, pneumatic actuators require complex control systems to ensure precise and repeatable performance. This is particularly important in robotic applications, where multi-axis synchronization is crucial for achieving complex movements.
Overall, despite facing challenges, pneumatic actuators are undergoing a transformative phase fueled by technological advancements. Their integration with digital control, improved materials, and novel applications in fields like soft robotics are shaping a more efficient and intelligent future for these versatile workhorses of modern industrial automation.
More Posts from patentreviewpro.com: