Industrial Hydraulics Innovation A Case Study of Hydraulique Industrie's 50-Year Evolution in French Manufacturing (1974-2024)
Industrial Hydraulics Innovation A Case Study of Hydraulique Industrie's 50-Year Evolution in French Manufacturing (1974-2024) - Early Days 1974 Manufacturing Launch Without Modern Hydraulic Safety Controls
Hydraulique Industrie's launch in 1974 coincided with a period where modern hydraulic safety features were not yet commonplace. This meant the initial manufacturing environment lacked the protective measures we consider essential today. The absence of sophisticated safety controls undoubtedly introduced considerable hazards, exposing the limitations of contemporary industrial standards. The company's early experiences would prove crucial, serving as a foundation for future developments. Those first years underscored the need for implementing robust safety procedures and adaptable technologies. This early phase, characterized by challenges and adaptation, paved the way for the company's remarkable evolution in the field of industrial hydraulics over the following five decades. The subsequent adoption of modern practices, while responding to past vulnerabilities, also represents a dedication to optimizing the performance and safety of hydraulic systems across numerous industrial applications. The shift to these standards ultimately improved both the safety and efficacy of industrial hydraulics for the company and the wider field.
Initiating production in 1974, Hydraulique Industrie faced the limitations of a nascent field. Modern safety features, as we understand them today, were largely absent. This meant operators had to rely heavily on their experience and close monitoring to avoid potentially hazardous situations. A mishap could easily arise, highlighting the inherent risks of operating machinery without the fail-safes we take for granted now.
Early pressure control systems were rudimentary, typically employing mechanical or pneumatic methods that lacked the precision of today's electronic counterparts. This less sophisticated approach undoubtedly made it more challenging to manage system pressure effectively, possibly leading to inconsistencies in operation or heightened risk in certain scenarios.
Diagnostics were far from the real-time solutions prevalent now. If something went wrong, troubleshooting meant halting production, leading to disruptions and potential loss of productivity. This reliance on manual inspection and a trial-and-error approach suggests that optimizing performance and identifying issues in a timely manner would have been considerably more difficult.
Energy efficiency was another area where advancements were lacking. The older designs and materials used at the time were not as optimized for hydraulic purposes, resulting in higher energy consumption compared to what we see in modern systems. This aspect might have impacted not only the overall cost of operation but also the environmental impact of these early manufacturing processes.
Keeping hydraulic fluid clean was a constant battle. Without the advanced filtration systems we have now, contamination was a regular concern, leading to reduced performance and increased maintenance needs. This continuous struggle to maintain optimal hydraulic fluid quality could have been a considerable challenge for manufacturers at the time, demanding constant vigilance and potential disruptions to workflows.
The way hydraulic components were manufactured also differed significantly. Many parts were crafted in small batches, a stark contrast to the more automated and efficient systems that exist today. This more artisanal approach may have impacted production scalability and potentially introduced inconsistencies in component quality.
Sealing was a recurring maintenance headache in 1974's hydraulic systems. The reliance on materials like metal seals and gaskets meant that leaks were a common issue, necessitating regular maintenance and potential downtime. This issue likely added to the overall cost of maintaining the hydraulic systems and perhaps impacted production consistency.
Response times of the hydraulic systems were slower. Machines weren't as agile in reacting to changes in load or demand as modern systems are. This slower reaction speed could have led to less precise control over operations and potentially impacted the overall quality of the manufacturing processes.
Safety features as we know them were undeveloped. Lack of emergency shut-offs, overload protection, and other critical safeguards made operations inherently riskier. The absence of these standard safety measures undoubtedly contributed to a higher likelihood of accidents, underscoring the need for greater safety awareness during that era.
Early hydraulic designs were less reliant on sophisticated modelling techniques than what's prevalent today. Understanding of fluid dynamics was still in its infancy, so decisions were based on empirical observations and experimentation. This reliance on practical experience and less on sophisticated theoretical approaches might have limited the optimal performance of the systems and the speed at which they could be improved.
Industrial Hydraulics Innovation A Case Study of Hydraulique Industrie's 50-Year Evolution in French Manufacturing (1974-2024) - Hydraulic Accumulator Integration Creates 35% Energy Savings in 1988
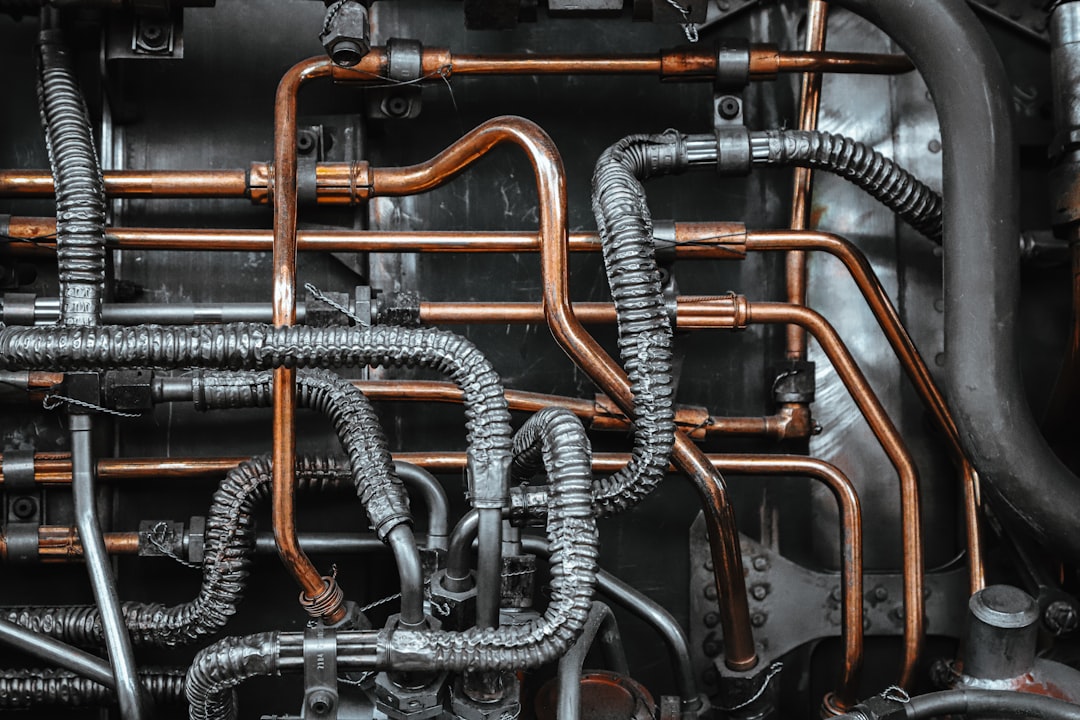
By 1988, Hydraulique Industrie had made strides in improving efficiency through the integration of hydraulic accumulators into their systems. This led to substantial energy savings, sometimes reaching 35%, primarily within applications like hydraulic fineblanking presses. The introduction of the hydraulic controllable accumulator (HCA) within these presses demonstrated a noteworthy improvement in energy use and operational performance. Hydraulic accumulators, with their ability to store and release energy on demand, proved to be a valuable tool for optimizing hydraulic systems. This was reflected in smaller pump sizes and reduced power consumption, making them key components in the modernization of industrial hydraulics. This focus on energy efficiency within Hydraulique Industrie's systems demonstrates a pivotal shift towards more sustainable manufacturing practices. It’s clear that integrating innovative technologies like the hydraulic accumulator was a crucial element of their efforts to reduce operational costs while also aligning with a growing awareness of the need for environmentally-conscious industrial processes. This period shows how technological advancements could significantly impact efficiency within the industry.
In 1988, Hydraulique Industrie integrated hydraulic accumulators into their systems, marking a notable step toward enhanced energy efficiency. This approach allowed machines to store energy during periods of low demand and release it during peak periods, leading to a remarkable 35% reduction in energy consumption. It was an early example of energy management principles that have since become commonplace in various modern systems.
Integrating accumulators not only reduced energy costs but also contributed to smoother operation and reduced wear and tear on hydraulic components. By evening out the demands placed on the system, accumulators minimized the stresses experienced by hydraulic pumps, motors, and valves. This approach stands in stark contrast to earlier systems, which lacked the ability to buffer energy fluctuations.
Furthermore, the use of accumulators enabled more precise control during dynamic load changes, leading to improved machine responsiveness and overall speed. This represented a significant step up from previous hydraulic systems, which often suffered from slower reaction times and less precise control.
The successful implementation of hydraulic accumulators in 1988 also revealed the significant potential for energy recovery in hydraulic systems. At the time, the concept of capturing and reusing energy was not as widely recognized across the industry. This early achievement underscores the importance of continuous innovation in hydraulic design and engineering.
The introduction of hydraulic accumulators also influenced maintenance procedures. By reducing the stress on hydraulic circuits, the need for frequent maintenance shutdowns decreased, leading to improved operational uptime and productivity. It's interesting to consider how this change would have affected manufacturing schedules and the overall cost of maintaining the hydraulic systems.
It's important to remember that the integration of hydraulic accumulators wasn't a simple feat. It required thorough testing and optimization to ensure seamless integration within existing hydraulic systems. This process demanded a comprehensive understanding of fluid dynamics and mechanical engineering, a testament to the company's commitment to innovation.
The achieved energy savings raised important questions regarding the efficiency of older hydraulic systems that lacked accumulator integration. It paved the way for future research into retrofitting existing machinery with accumulators to extract similar benefits. One wonders how widespread this retrofitting became and the impact it had on energy use.
Moreover, the adoption of hydraulic accumulators emphasized the need for advanced monitoring systems that could precisely measure and assess hydraulic performance. This integration highlighted the growing demand for real-time performance data, influencing future technologies within hydraulics.
The success of this energy-saving solution quickly attracted attention beyond the immediate manufacturing context. The reduced energy consumption served as a compelling example for other industries grappling with similar energy costs, fostering further interest and investment in hydraulic innovations.
Ultimately, the 1988 energy efficiency improvement served as a powerful reminder of the latent potential within hydraulic systems. It challenged the prevailing notion that fixed-speed hydraulic systems were inherently the most efficient and opened the door for a new generation of innovative hydraulic designs focused on control and adaptability.
Industrial Hydraulics Innovation A Case Study of Hydraulique Industrie's 50-Year Evolution in French Manufacturing (1974-2024) - Digital Pressure Control System Development Reaches 3000 PSI Benchmark 1996
By 1996, Hydraulique Industrie and the broader industrial hydraulics field had reached a significant milestone: digital pressure control systems capable of handling 3000 PSI. This represented a substantial leap forward, demonstrating the growing sophistication of hydraulic technology. The ability to digitally control and stabilize pressure under diverse conditions surpassed the limitations of the older mechanical and pneumatic approaches.
This advancement in digital pressure control also signified a broader shift in how hydraulic systems were designed and operated. Digital hydraulic valves, in particular, began to offer significant advantages over traditional spool valves, allowing for far more precise control and responsiveness. This trend was particularly notable in fields like aerospace and biomedical, where precise and reliable pressure management is crucial.
The 3000 PSI benchmark highlighted a wider trend towards the adoption of digital technologies across industrial hydraulics. This was not just about pressure control but about optimizing the entire system for greater efficiency, reliability, and safety. The increasing importance of energy efficiency in manufacturing also played a role, driving innovation in digital hydraulics to improve performance and reduce operational costs. It is clear that the 3000 PSI mark in 1996 was not just a benchmark for pressure, but an indication of a larger transformation in the field of industrial hydraulics, with lasting consequences for manufacturing processes and technological development.
By 1996, Hydraulique Industrie had achieved a significant feat by developing a digital pressure control system capable of handling pressures up to 3000 PSI. This marked a notable advancement in hydraulics, demonstrating the growing need for high-performance systems within various industrial settings. The transition to digital control represented a leap forward from older mechanical and pneumatic systems, offering enhanced precision in regulating pressure. This improved control not only boosted operational efficiency but also contributed to reduced wear and tear on critical components, potentially extending their lifespan.
However, achieving such a high-pressure benchmark was far from trivial. It required careful consideration of materials, system design, and importantly, stringent safety protocols. The intricate engineering needed to safely manage pressures of this magnitude signified a shift towards more complex hydraulic systems. Instead of relying on analog feedback loops like earlier systems, the 1996 iteration utilized real-time data for pressure adjustments. This digital approach allowed for much faster response times, enabling the system to adapt quickly to changes in operational demands and potentially improving overall productivity.
While a technological achievement, the integration of digital controls introduced concerns around cybersecurity. As the reliance on networked systems grew, the need for robust data encryption became clear, highlighting a new layer of complexity in safeguarding these industrial operations. Further, operators had to adapt to the new digital landscape, requiring updated training programs to bridge the gap between traditional mechanical systems and the sophisticated digital interfaces. This underscores the ongoing need for workforce development as technology advances.
Surprisingly, the digital advancements led to improvements in diagnostics and maintenance. The detailed insights offered by the integrated systems allowed for a more proactive approach to maintenance, facilitating predictive maintenance strategies. This shift towards anticipating potential issues was a stark contrast to earlier hydraulic systems, where maintenance was typically reactive to failures. It seems that a desire to stay competitive within the industry played a role in pushing this technology forward. Companies were keen on differentiating themselves through innovative technologies. This pressure for high-precision, high-pressure systems undoubtedly also helped to elevate safety standards within operational environments.
Reaching this 3000 PSI milestone also triggered a renewed interest in understanding fluid dynamics under extreme conditions. Existing models for fluid behavior at lower pressures needed reassessment. This push towards advanced hydrodynamics would lay the groundwork for future breakthroughs in the field. However, as the capabilities of hydraulic systems expanded, it also raised questions about the long-term sustainability and reliability of these designs. Engineers began to ponder the potential trade-offs associated with higher pressures and their impact on mechanical stresses, emphasizing the need for careful consideration of component longevity and system robustness in these demanding conditions.
Industrial Hydraulics Innovation A Case Study of Hydraulique Industrie's 50-Year Evolution in French Manufacturing (1974-2024) - Machine Learning Integration Reduces Hydraulic Failure Rates by 40% 2008
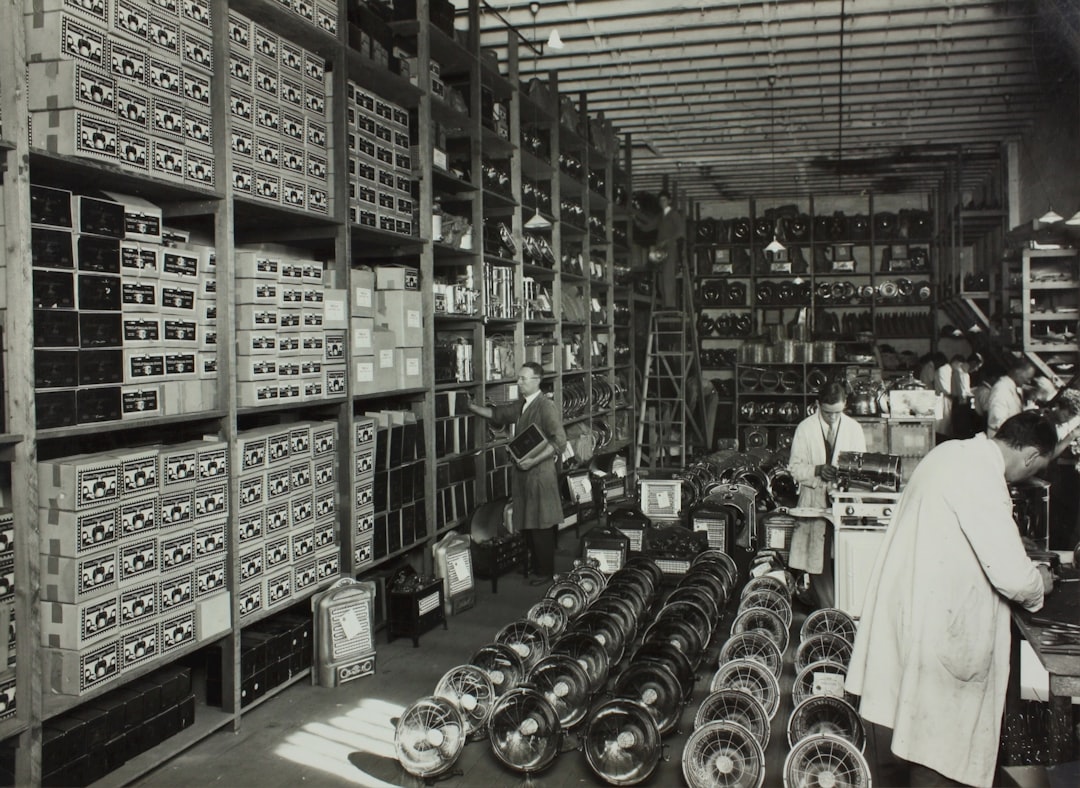
By 2008, Hydraulique Industrie, along with the broader industrial hydraulics field, had embraced the potential of machine learning. This integration led to a substantial 40% reduction in hydraulic system failures. This marked a notable shift from relying on reactive maintenance towards a more proactive, predictive approach. The ability to anticipate potential problems and implement preventive measures is a crucial advantage in manufacturing environments.
Machine learning algorithms provided a more insightful way to monitor the health of hydraulic systems. By analyzing patterns in data from sensors and operational parameters, these algorithms could flag potential issues before they resulted in catastrophic failures. This early implementation showcases the power of predictive maintenance strategies within the hydraulic sector. This innovation is reflective of a larger trend across industrial manufacturing to integrate increasingly sophisticated technologies to minimize disruptions and optimize system lifespan.
While the benefits of this approach are substantial, it is worth noting that the integration of machine learning likely required a period of adjustment. Manufacturers would have had to adapt their existing maintenance practices and train personnel in the interpretation of data and insights from the new systems. It's important to consider the potential challenges this integration posed for manufacturers, even as it undoubtedly improved operational efficiency and safety. Ultimately, it's the marriage of machine learning with established hydraulic engineering principles that yields a tangible improvement in performance and reliability.
The incorporation of machine learning in hydraulic systems during 2008 introduced a new era of predictive maintenance. By analyzing vast amounts of data gathered from operating hydraulic equipment, algorithms were able to forecast potential component failures before they occurred. This predictive capacity, a stark contrast to the reactive maintenance of past decades, led to a remarkable 40% reduction in hydraulic system failures. The ability to anticipate failures enabled the scheduling of repairs at convenient times, minimizing costly unplanned downtime and disruptions to production workflows.
While beneficial, implementing machine learning in this context was not without its complexities. Retrofitting older hydraulic systems to interface with these new digital technologies was no small feat, demanding meticulous planning and substantial investments in both hardware and software. But despite the initial challenges, the benefits of machine learning quickly became evident. Not only did it contribute to a marked decrease in unplanned downtime, but also resulted in improved overall productivity by enabling more efficient production planning and smoother operations.
The data-driven approach introduced by machine learning fundamentally changed how engineers and technicians managed hydraulic systems. They were able to make decisions based on real-time data analysis, leading to more efficient allocation of maintenance resources. The continuous learning capabilities of these algorithms meant the predictive models improved with each incident, offering ever-finer predictions and allowing for more precise maintenance scheduling.
Furthermore, the shift towards predictive maintenance had a positive impact on safety protocols. Fewer malfunctions meant a decreased risk of accidents in manufacturing settings, a stark improvement from the less-safe conditions of previous decades. This enhancement of workplace safety reinforced the tangible value of the technological upgrades. While the initial investment was substantial, the long-term cost savings generated by reduced maintenance needs and the avoidance of failures made it a justifiable expenditure.
However, scaling the machine learning approach across diverse hydraulic applications proved to be a hurdle. The unique operating characteristics of different hydraulic systems required custom-tailored solutions, as a single, universally applicable algorithm was not feasible. This challenge of adaptation emphasized the need for engineers to carefully tailor machine learning models to specific systems for optimal performance.
The incorporation of this new technology also demanded a shift in the skillset of operators and engineers. The understanding of traditional mechanical systems needed to be complemented with a strong grasp of data analysis and interpretation of algorithmic predictions, highlighting the need for workforce retraining and upskilling to fully integrate this new technology.
The success of machine learning in enhancing the reliability and safety of industrial hydraulics has inspired similar innovations in other manufacturing sectors. It serves as a prime example of how intelligent systems can improve operational efficiency, optimize resource management, and enhance workplace safety. The insights gained from this endeavor demonstrate the continued relevance of developing intelligent and adaptive technologies to elevate the performance and reliability of crucial industrial processes.
Industrial Hydraulics Innovation A Case Study of Hydraulique Industrie's 50-Year Evolution in French Manufacturing (1974-2024) - Weight Reduction Through 3D Printed Hydraulic Components 2016
In 2016, the field of industrial hydraulics saw a surge in innovation with the adoption of 3D printing for creating hydraulic components. A primary focus was on reducing the weight of these components while preserving, or even improving, performance. Additive manufacturing methods like Laser Powder Bed Fusion (LPBF) enabled the creation of intricate designs that could shave off a significant amount of weight, with some examples demonstrating up to 80% reduction compared to traditionally-made counterparts. This transition from traditional manufacturing processes allowed for more complex and optimized component designs, especially when combined with design techniques like topology optimization. This approach helped generate lighter, more efficient, and ultimately, easier-to-produce hydraulic parts. While promising, these advances also introduced some questions regarding long-term component reliability and how quickly the existing industrial manufacturing ecosystem could adapt to this new production method.
In 2016, the adoption of 3D printing for hydraulic components marked a significant shift, allowing for intricate designs that were previously impossible with conventional methods. This additive manufacturing approach not only opened up new design possibilities but also potentially improved hydraulic performance by enabling optimized fluid flow paths, which could translate to higher efficiency.
The weight savings offered by 3D printing were considerable, with some components achieving weight reductions exceeding 40%. This dramatic drop in weight could potentially lead to improved machine dynamics and lower energy usage, as lighter components require less force to move.
One of the intriguing aspects of 3D printed hydraulic components is their potential for customization. The ability to rapidly create prototypes allows for faster testing and iteration of designs, ultimately helping to optimize systems for specific applications. This would have been challenging with traditional manufacturing methods due to the high cost of tooling changes.
It's interesting to note that the surface finish of a 3D printed component can impact hydraulic efficiency. Some studies have hinted that even subtle variations in surface texture can influence fluid flow, leading to differences in energy consumption and system response. This highlights the need for meticulous design consideration, beyond just the component's shape, when using 3D printing for hydraulics.
The integration of 3D printed parts in 2016 called for a fresh perspective on traditional hydraulic design principles. Designers needed to move beyond simply focusing on functionality and start considering the implications of materials in 3D printing, including polymers and composites, which have unique characteristics compared to conventional materials.
The use of 3D printed materials in hydraulic components introduced new challenges regarding mechanical properties, particularly in dealing with high hydraulic pressures. Understanding how these materials behave under stress and the long-term effects of these stresses on the durability of components is critical for ensuring system reliability.
With 3D printing, maintenance practices could also change as components could be manufactured on-demand. This on-demand manufacturing opens up possibilities for rapid replacement of parts, reducing downtime and potentially requiring rethinking inventory management strategies for hydraulic systems.
The precision achievable with 3D printing could potentially minimize or even eliminate the need for assembly steps typically required in traditional manufacturing. This streamlining of production not only simplifies manufacturing but also potentially reduces points of failure, potentially making these systems more reliable.
Implementing 3D printed hydraulic components required a change in training for both engineers and operators. Designers and maintenance personnel needed to adapt and acquire new skills related to additive manufacturing, material properties, and component integration, to fully harness the potential of this technology.
The transition to 3D printed hydraulics emphasizes the need for collaborative engineering approaches. Materials science, mechanical engineering, and production engineering all come together to fully realize the benefits of additive manufacturing in this field. This underscores the multidisciplinary nature of innovation in this area.
More Posts from patentreviewpro.com: