Fronius CMT Revolutionizing Precision Welding with Low Heat Input Technology
Fronius CMT Revolutionizing Precision Welding with Low Heat Input Technology - Dynamic Arc Control Enhances Gap-Bridging Performance
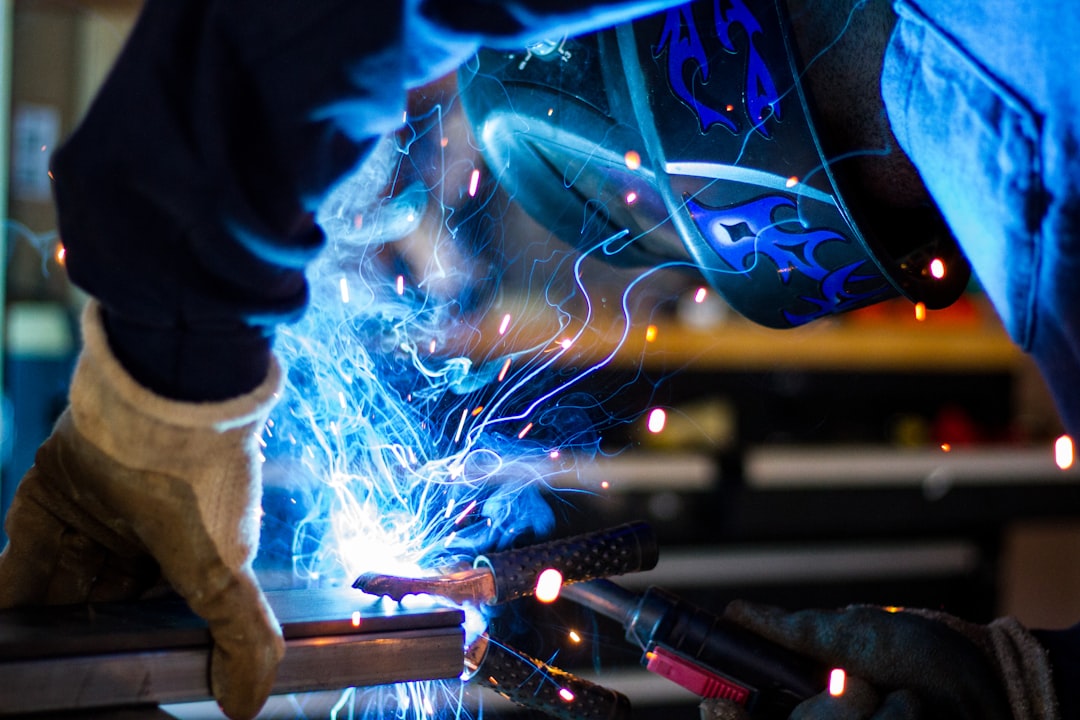
A core aspect of the Cold Metal Transfer (CMT) process is its Dynamic Arc Control, which plays a pivotal role in improving the ability to bridge gaps during welding. This control system manages the separation of weld droplets both electronically and mechanically, providing a significant enhancement to welding performance. It demonstrably improves gap bridging capabilities in aluminum, with the ability to cross gaps from 1 mm up to 2.5 mm—a notable leap forward. This capability stems from the use of high-frequency pulses, a core element of CMT. These pulses minimize the heat input during welding, mitigating the chances of the material burning through or becoming distorted. Furthermore, this approach facilitates faster welding times while preserving weld quality.
The specific torch design and the new Cycle Step process within CMT further contribute to the process's versatility. These advancements lead to improved weld bead aesthetics and more predictable results, expanding the applicability of CMT to a wider range of materials and applications. In essence, these advancements in CMT demonstrate a move towards more versatile and efficient precision welding methods, benefiting various industries and applications.
The dynamic arc control inherent in CMT welding plays a critical role in maximizing its gap-bridging capabilities. By exerting fine-grained control over the arc, the system is able to dynamically adjust droplet detachment and transfer. This electronically mediated manipulation of the arc's behavior allows for more precise control of the weld pool, something not readily achieved with more conventional pulsed arc methods.
It seems that a major consequence of this control is a significant boost in the ability to bridge gaps. Some studies have found it can increase this capability by a substantial margin, effectively increasing the maximum achievable gap width significantly, specifically for challenging materials like aluminium. It's interesting to consider the specific mechanisms at play; how the high-frequency pulse interacts with the feedback controls and the arc behavior to achieve this.
The versatility of DAC is notable, adapting to different materials and weld geometries while maintaining this enhanced gap-bridging performance. This characteristic has implications for a wide range of applications. Additionally, the automated nature of the compensation for variables, like component fit-up or surface contaminants, is intriguing. This ability to automatically compensate for process disturbances highlights the potential of DAC to enhance the reliability and robustness of the process, especially when dealing with parts with varying gap sizes and surface qualities.
However, questions remain regarding how precisely these algorithms function and the role real-time monitoring plays in achieving this adaptive behavior. The integration of robotics-inspired feedback techniques is promising, but I wonder if it can truly adapt to all types of disturbances encountered in real-world manufacturing. While the improvements in spatter reduction and weld appearance are clearly beneficial, the overall cost-effectiveness in terms of increased system complexity still requires deeper analysis. The overall trend is clearly towards increased automation and sophistication in welding techniques, particularly in areas like automotive and aerospace where the quality and consistency of weld joints are paramount.
Fronius CMT Revolutionizing Precision Welding with Low Heat Input Technology - Unique Droplet Transfer Mechanism Improves Arc Stability
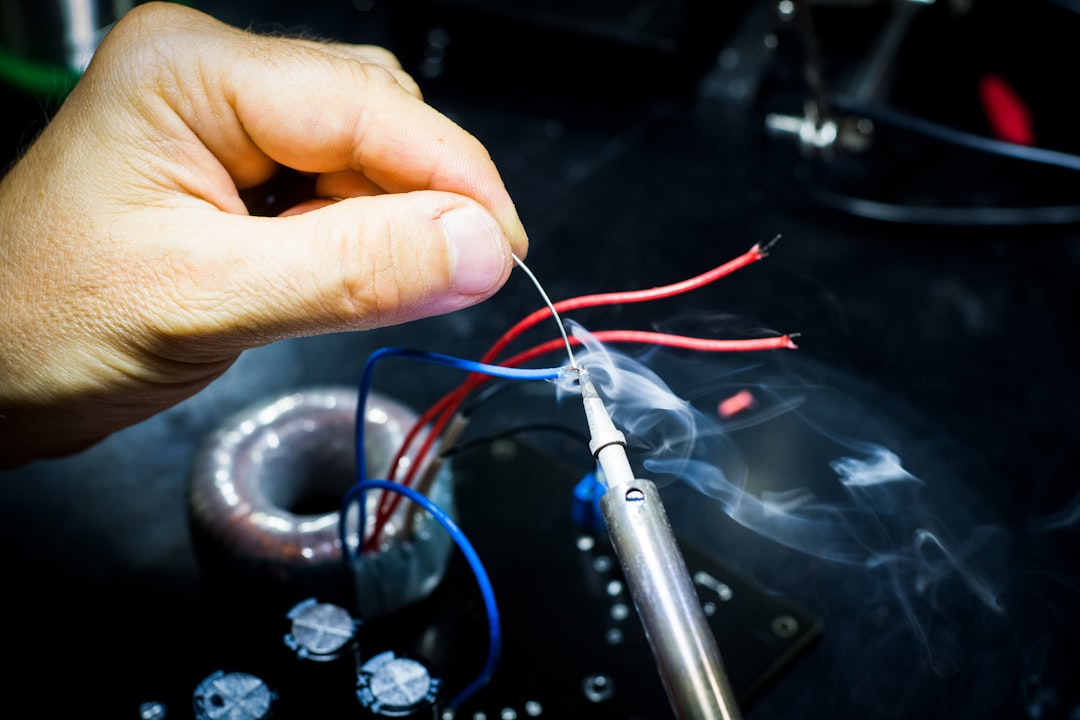
Fronius's Cold Metal Transfer (CMT) welding process utilizes a unique droplet transfer mechanism that contributes significantly to improved arc stability. This mechanism involves using a precisely controlled high-frequency pulse to transfer molten metal droplets. A key benefit is the reduced heat input to the workpiece, helping to minimize issues like burn-through and distortion. The CMT welding cycle is divided into three distinct phases—peak, base, and short-circuit—each with its specific impact on droplet formation and arc behavior. The use of reverse polarity further supports arc stability, even at lower current levels, which is beneficial for producing high-quality welds. Additionally, this method seems to work well when joining different materials. While this technology presents clear advancements in welding, it's important to remember that careful evaluation of its practical implications in various industrial settings, along with a close assessment of its cost-effectiveness, remain crucial as its adoption grows.
Fronius's CMT process employs a distinct droplet transfer mechanism, crucial for achieving the high arc stability that sets it apart. This method involves carefully timed droplet release, minimizing the erratic behavior often observed in conventional welding techniques. The ability to precisely control this release seems key to the method's success.
By exerting this control over droplet formation, CMT significantly reduces spatter. This isn't just about a tidy work environment, but also suggests improved weld quality as less spatter likely equates to stronger, more structurally sound welds.
One of the notable aspects is the reduced energy input during droplet transfer. This minimizes heat input to the workpiece, reducing the likelihood of warping or distortion, particularly critical when working with thinner materials. While reduced heat input seems advantageous, it's worth considering if it might come with trade-offs such as slower weld speeds or other limitations.
The high-frequency pulses used in the process lead to a more uniform weld bead profile, enhancing the visual appeal and potentially improving the strength of the joint. This raises the question of whether the consistency in bead shape truly translates to substantial improvements in joint performance. More research on that connection would be useful.
It's quite interesting how the CMT process can adapt to inconsistent surfaces. Its inherent self-adjustment to variations in material quality seems promising for practical applications, as it ensures consistent results even in environments where surface quality isn't strictly controlled. This adaptability, however, might rely on complex algorithms and feedback mechanisms, the nature of which needs to be better understood.
This stability also makes the process applicable to a wider range of materials, including challenging ones like high-strength steels and complex alloys. While the promise of broader applicability is tempting, further research is needed to demonstrate the consistent performance across various material combinations.
Real-time feedback loops help dynamically adjust the welding process. This adaptive feature allows the process to react to environmental fluctuations or variations in the workpiece, enhancing overall control. It's intriguing to see how such a system interacts with external factors; understanding these interactions would help in developing predictive models for process optimization.
The impressive ability to bridge gaps ranging from 1 mm to 2.5 mm indicates a solution for common problems in assembly. This bridging capability can simplify the assembly process by reducing the need for pre-weld adjustments, potentially saving time and money. But the long-term effects of using this method on wider gaps on weld quality and fatigue resistance should be examined further.
The emphasis on low heat input in the CMT process aligns with modern industry trends focused on reduced post-processing. This suggests CMT could become a prominent approach in future welding, as the demand for high-precision applications continues to rise. This potential impact should encourage further development and standardization efforts.
Finally, we must acknowledge the potential complexity of the CMT system. The intricate nature of this droplet transfer mechanism could lead to increased training needs and more elaborate maintenance requirements. The question of whether the benefits outweigh the increased technical demands is important, and its effect on the wider adoption of the technology warrants further investigation. Overall, the CMT process seems like a significant step forward in welding, but understanding its intricacies and potential limitations is crucial for optimal deployment in diverse applications.
Fronius CMT Revolutionizing Precision Welding with Low Heat Input Technology - Cycle Step Capability Ensures Precise Droplet Control
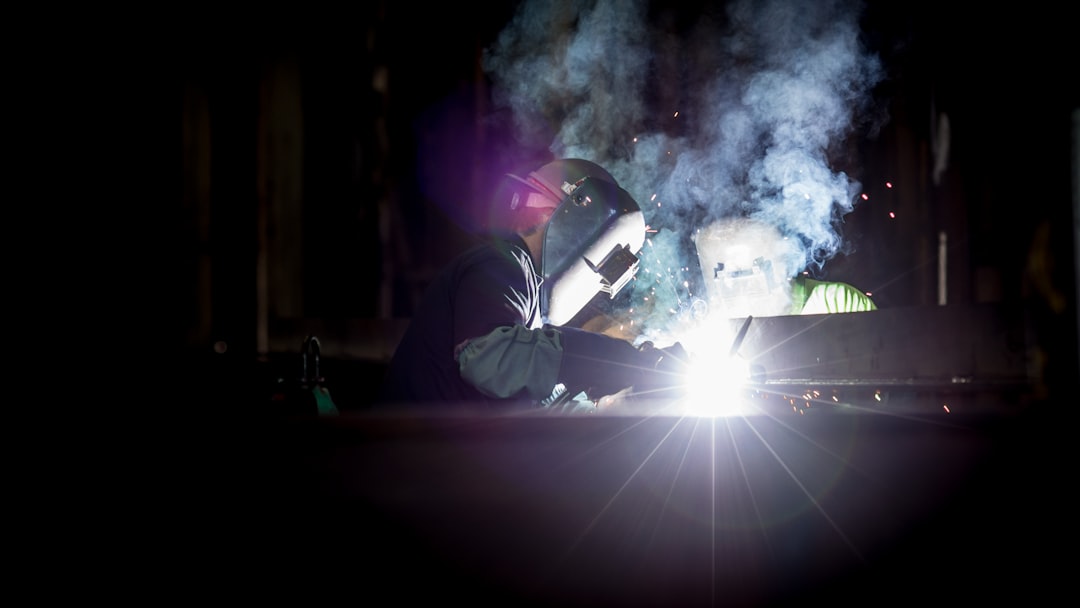
Fronius's Cold Metal Transfer (CMT) process incorporates a Cycle Step feature that significantly improves droplet control. This functionality gives users the ability to adjust both the number of individual droplets released and the duration of the pauses between each cycle. This fine-grained control allows for significant customization, adapting the welding process to specific material needs. One outcome of this feature is a reduction in heat input during welding. This minimizes distortion of heat-sensitive materials and results in a weld bead with distinct, uniform ripples. This consistency contributes to a high degree of reproducibility in the weld quality. Cycle Step's versatility extends its usefulness into a variety of industrial applications, from creating aesthetically pleasing welds to supporting additive manufacturing processes. While this level of control offers clear benefits, its use requires a comprehensive understanding of the technology and careful management of its settings. If not handled correctly, the complexities could lead to suboptimal outcomes.
The Cycle Step feature within Fronius's CMT process seems designed to exert a high degree of control over droplet formation during welding. By manipulating the transfer process through a series of controlled phases, it can potentially achieve a level of precision in droplet size and, by extension, weld pool characteristics that was previously unattainable with traditional methods. It's quite remarkable how this level of control can be achieved.
It appears that the precise timing of droplet detachment, a core aspect of Cycle Step, contributes to more stable arcs by reducing interruptions. This is scientifically interesting as it implies a minimization of arc wander and associated weld defects. While the claim is intriguing, it would be useful to understand how consistently this translates across a wider range of welding scenarios.
The connection between droplet size and arc dynamics is a key principle highlighted by Cycle Step. The idea is that smaller droplets are transferred more efficiently, producing a more stable arc. This aspect would seem particularly useful when welding thin materials, where preventing distortion is crucial. It would be useful to see controlled experiments demonstrating this relationship.
Cycle Step implementation apparently enables not only improved gap bridging but also enhanced weld penetration. This capability could be crucial for applications requiring high-performance welds, particularly in structural engineering. But how does this change across different alloys or thicknesses?
The real-time control over droplet transfer is a significant aspect of CMT. This makes it responsive to variations in the material and the shape of the joint being welded. This is especially useful in scenarios where traditional methods might struggle. But how effectively does it adapt to complex or rapidly changing conditions?
The refined control of droplet transfer seems to translate into reduced spatter generation. This is a positive outcome for both workshop cleanliness and potentially weld quality. But it's crucial to ensure this consistency holds across a variety of environmental and operational conditions.
Another notable claim is that Cycle Step can maintain effectiveness even in the presence of surface contamination. While this robustness is advantageous, it's worth asking if this ability to adapt could mask issues with material cleanliness that might impact weld integrity in the longer term. This is a point worth deeper exploration in future studies.
The ability to dynamically control the weld process requires complex algorithms that adjust in real-time. This algorithmic control is vital for ensuring the effectiveness of Cycle Step across different materials and environments. A deeper look into the nature of these algorithms would be beneficial to researchers interested in optimizing these processes.
The precision of Cycle Step could lead to a simplification of the assembly process, reducing the need for pre-welding adjustments. This efficiency could improve labor costs and throughput in manufacturing settings. However, we need more information on how this impact plays out in real-world production settings, especially on weld longevity and fatigue resistance.
While the improvements provided by Cycle Step in droplet control are promising, it's important to consider the added complexity to the welding system. Operator training and system maintenance could be more challenging, potentially offsetting some of the benefits. A careful assessment of this increased complexity and whether it is justified by the improvements is needed to ensure its widespread adoption in manufacturing.
Fronius CMT Revolutionizing Precision Welding with Low Heat Input Technology - Reverse Polarity Creates Stable Arc at Low Current
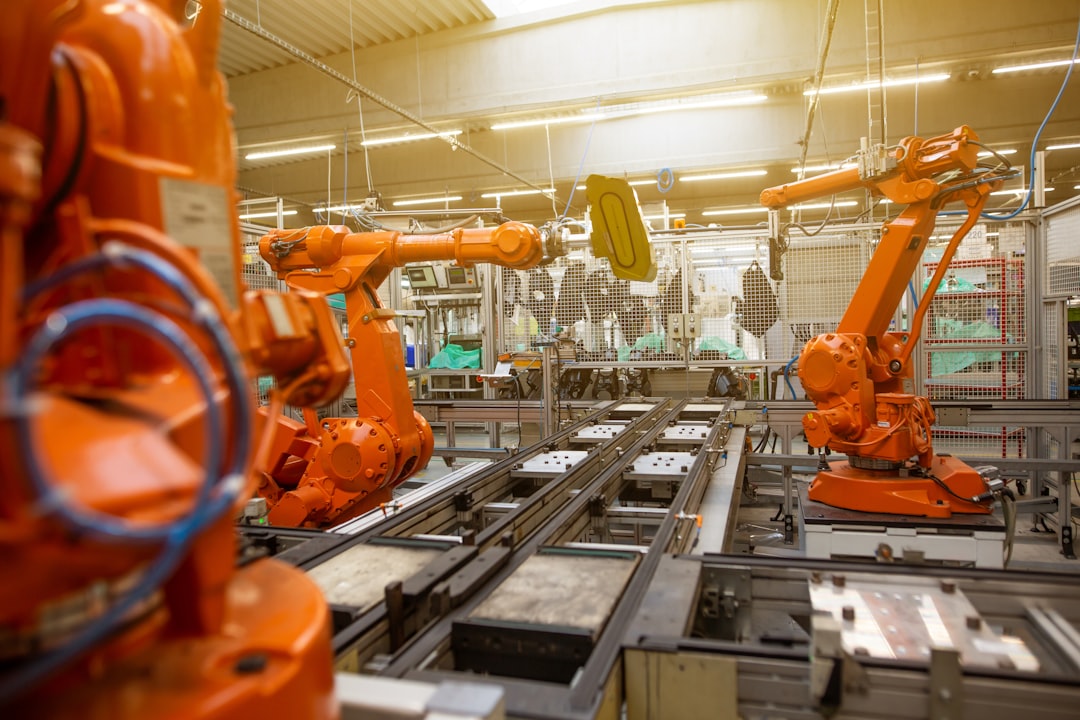
Fronius's Cold Metal Transfer (CMT) welding method uses reverse polarity to maintain a stable arc, even when operating at lower current levels. This contributes to superior weld quality while minimizing the amount of heat transferred to the workpiece. This reduced heat input lessens the likelihood of burning through or distorting the material. The core of CMT involves using high-frequency pulses to carefully control how molten metal droplets are transferred. This refined control leads to precise metal deposition and noticeably less spatter. The stable arc generated by CMT allows it to handle challenging materials effectively and promotes visually appealing and structurally sound welds. Though these improvements seem significant, it's crucial to fully understand how these innovations would translate to different industrial settings before they become widely adopted.
Fronius's CMT welding process utilizes reverse polarity to establish a stable arc, even when using low current levels. This is noteworthy because minimizing current reduces the heat input during welding, which is crucial when working with materials sensitive to heat distortion. The reduced heat input is a primary advantage of the CMT method.
This reverse polarity configuration seems to influence how the electrode interacts with the workpiece. There's a suggestion that this interaction improves metallurgical bonding during the welding process, likely contributing to weld quality. This is something to look into more closely as it suggests a potential pathway towards optimizing weld characteristics.
One interesting potential benefit of reverse polarity is that it might lead to less wear and tear on the electrode. By managing the thermal loads more effectively, the electrode could potentially last longer, potentially resulting in cost savings. However, this claim needs more evidence as it's unclear if it holds for all electrode types and material pairings.
The CMT process doesn't just rely on reverse polarity for arc stability—it also involves dynamic feedback mechanisms that are integrated into the process. In essence, the system continuously monitors the arc and adjusts the welding parameters like current and voltage in real-time. This adaptive behavior could lead to improved efficiency and consistency, but it’s important to be critical and explore whether this adaptive capability truly translates to advantages in a wider variety of industrial applications.
It is claimed that this approach leads to reduced energy consumption during welding. This is a potential benefit for both the environment and industrial settings looking to improve their energy footprints. However, a thorough comparison to traditional methods is needed to determine if this claim holds true across the board, as it could be highly dependent on specific factors.
Another area where reverse polarity seems to show its value is in the welding of dissimilar materials. The process's inherent stability facilitates welding materials that wouldn't bond easily with conventional methods. This broader material compatibility could open up new opportunities in manufacturing where diverse materials are combined in assemblies.
The stability of the arc produced through reverse polarity seems to have a knock-on effect of decreasing spatter formation. This reduction in spatter is desirable for reasons beyond cleaner workplaces. Less spatter could lead to higher-quality welds with fewer imperfections. It's worth examining the specific mechanisms by which arc stability leads to spatter reduction.
A reduction in heat input generally leads to a finer microstructure in the weld zone. This refined microstructure could potentially improve the mechanical properties of the weld joint, offering enhanced strength or ductility. But determining the exact nature of these improvements in specific applications would require further research.
The feedback mechanisms present in the CMT process provide adaptive control, responding to variations in the workpiece and environment. This adaptability is crucial for ensuring consistent weld quality in settings with variations in the workpieces being joined. Understanding the full capabilities and limitations of this adaptive nature would require more research.
While the advantages of reverse polarity are numerous, it's also crucial to be aware of potential drawbacks. Under certain conditions, such as specific gas mixtures or welding environments, reverse polarity can lead to problems with arc stability or weld quality issues like increased porosity. This suggests that the applicability of the process in different industrial contexts needs to be carefully studied and verified.
It’s clear that reverse polarity is a core technology in the Fronius CMT process, enabling several advantages in terms of weld quality, stability, and operational efficiency. However, further investigation into the limitations and optimization of reverse polarity within CMT is needed to truly assess its potential to revolutionize diverse applications and manufacturing sectors.
Fronius CMT Revolutionizing Precision Welding with Low Heat Input Technology - Zero Spatter Welding Ideal for Aluminum Alloys
The ability to weld aluminum alloys with minimal or zero spatter is a significant development, primarily achieved through techniques like Cold Metal Transfer (CMT). CMT utilizes a controlled droplet transfer method and reverse polarity to minimize spatter, benefiting both the workplace environment and weld quality. A key aspect is the reduced heat input during the welding process, which becomes especially valuable when dealing with aluminum alloys due to their sensitivity to heat distortion. This refined control over the weld also allows for better joining of diverse metals, making CMT a versatile solution. It's widely favored in applications like automotive manufacturing where high-quality welds are critical. However, the sophistication of this method necessitates careful consideration of the associated complexities, including the training requirements for operators and the potential impact on production workflows. While this technology holds great promise, a complete evaluation of its implications is necessary before it becomes more widely adopted.
Cold Metal Transfer (CMT) welding, with its focus on low heat input, appears particularly well-suited for aluminum alloys. A key aspect is the potential for minimal spatter, which in the context of CMT means most of the transferred molten metal directly contributes to the weld. This is especially valuable for aluminum, which tends to oxidize, and trapped spatter can degrade weld integrity.
CMT's ability to tightly control the heat affected zone is crucial when working with aluminum. This zone, where the material's properties change due to the heat, needs to be managed carefully to preserve the base material's qualities, particularly important in applications demanding high strength, like those in aerospace. The precise droplet transfer inherent in CMT facilitates accurate metal deposition, which seems to minimize the chance of weld defects. This improved accuracy can lead to more durable weld joints capable of withstanding demanding conditions.
One interesting feature is the adaptive nature of CMT welding, especially regarding surface contaminants or uneven geometries. The system seems to manage these variations effectively, delivering more uniform weld quality, which is vital for applications with highly variable assembly components. It's not just the structural strength that benefits but also the visual appeal. CMT's focus on minimal spatter can result in more aesthetically pleasing welds, relevant in applications emphasizing appearance, like architectural elements or certain consumer products.
The method's versatility across various aluminum alloys makes it an intriguing technology. Its effectiveness with different alloys is advantageous for sectors like automotive and aerospace, where specific alloy choices are crucial for performance. This technology utilizes real-time monitoring, continuously adjusting welding parameters to achieve the minimal spatter outcome. The immediate feedback loops seem essential for maintaining quality and allowing quick corrections if the weld deviates.
Another practical benefit is the reduced distortion seen in thinner aluminum materials. Warping and distortion are common problems in conventional welding techniques, especially with thinner materials. This characteristic could be game-changing in situations where precision dimensions are paramount. The decreased spatter in CMT translates to less cleaning and rework, which positively impacts manufacturing efficiency. This aspect can lead to lower labor costs and faster production cycles.
There's also a suggestion that fume production is reduced with this method, creating a potentially safer work environment. While a controlled welding environment with appropriate safety measures is always crucial, less fume is a potentially welcome side effect, particularly in situations with confined workspaces.
While the advantages look compelling, there's always a need for continued research and careful evaluation of these techniques in various contexts. Understanding the full range of operating conditions and material interactions is vital for optimal implementation in specific industrial applications. It's also important to consider factors like training needs and system maintenance, especially if the increased sophistication of the method introduces higher system complexity. The overall trend in welding technologies continues towards increasing levels of automation and control, and CMT appears to be part of that progression.
Fronius CMT Revolutionizing Precision Welding with Low Heat Input Technology - Second-Generation CMT Process Offers Faster Welding Speeds
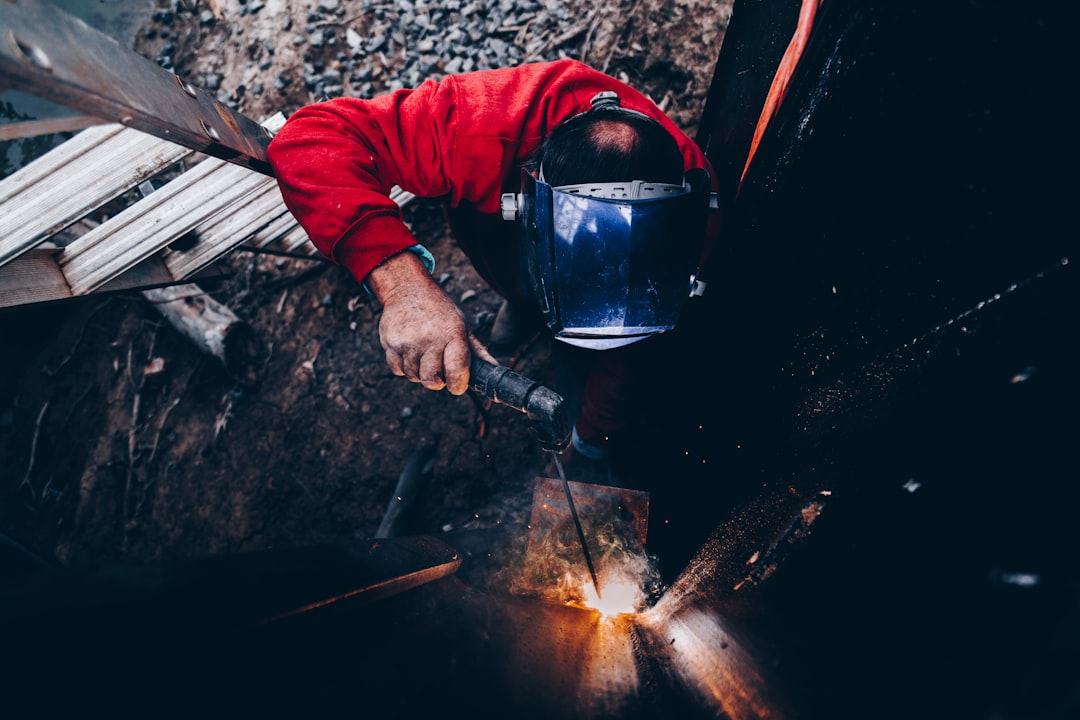
Fronius's Cold Metal Transfer (CMT) process, in its second generation, represents a substantial leap forward in welding, particularly in terms of speed. This newer version boasts significantly faster welding compared to conventional techniques. The method relies on a very stable, spatter-free arc, which inherently improves weld quality by reducing flaws. CMT's signature is its low heat input, a characteristic which helps minimize distortion and the risk of burning through the workpiece, making it a good choice for materials prone to these issues, like aluminium and high-strength alloys. The versatility of CMT is another strength, as it facilitates the joining of diverse materials, a capability highly sought after in fields such as automotive and aerospace. While CMT offers attractive benefits, including the potential to increase manufacturing speed, it's essential to acknowledge that it adds complexity to the welding process. This complexity might involve more demanding training needs and potentially more intricate maintenance routines. As CMT technology continues to develop, it will be interesting to see how it's integrated into a wider range of industrial settings and the trade-offs that come with its use.
Fronius's second-generation Cold Metal Transfer (CMT) process seems to have made significant strides in welding speed, which could be quite beneficial for industries with high production demands. It supposedly boasts a significant increase in speed compared to earlier versions and more traditional welding methods, potentially boosting productivity.
A core element appears to be a refined control over the welding cycle through high-frequency pulses. This refined control, it's claimed, allows for much faster cycle times without sacrificing weld quality. How they manage to accomplish this, however, is not immediately apparent.
Another key aspect of this newer CMT seems to be an improved ability to regulate droplet size and its transfer rate. While it's claimed this leads to more consistent weld beads, and in turn, more consistent mechanical properties, more experimental validation on the consistency of these properties in diverse applications would be necessary before drawing strong conclusions.
The scope of materials that can be welded with this process has also expanded. While earlier CMT versions have shown promise with aluminum, the second-generation is reported to be proficient at welding a wider range of materials, including high-strength steels and other alloys. The breadth of its effectiveness with such a range of materials needs to be assessed through broader testing across different combinations.
The incorporation of sophisticated, adaptive feedback mechanisms is another interesting feature. These supposedly allow the system to react and adjust to changing material characteristics and environmental conditions during the welding process. It remains to be seen how robust this adaptive capability is in a wide range of real-world settings and for various material combinations.
A reduction in the size of the heat-affected zone (HAZ) is also reported, which could have implications for improving joint strength and preventing damage to adjacent materials, especially important when working with sensitive materials. However, it is important to quantify the HAZ reduction in controlled experiments across a wider range of materials and thickness values.
The stability of the welding arc is another frequently mentioned improvement. Improved arc stability, achieved through changes in droplet transfer mechanisms, seemingly leads to less spatter and a reduction in common welding defects, which could have a noticeable impact on weld quality. But it is important to rigorously evaluate the spatter reduction in diverse settings to confirm claims of consistent improvement.
Interestingly, the design of the second-generation CMT makes it easier to integrate with robotic welding systems. This feature could streamline the transition to more automated welding operations in factory settings, potentially leading to greater efficiency. However, evaluating the actual cost-benefit of using robotics with this specific CMT process in different situations remains important.
Real-time monitoring and adjustment of welding parameters based on what the system is "seeing" is a key feature. This allows for greater control during the process, which is especially appealing in industries requiring high-precision welds like automotive and aerospace. But one needs to critically consider whether this real-time adjustment can lead to improvements beyond those achievable with more manual methods.
While the upfront complexity of this system might be a factor, proponents suggest the long-term savings from lower rework, reduced material waste, and higher throughput make it a compelling option for manufacturers seeking efficiency. It will be interesting to see how the long-term costs and efficiency claims stack up against more traditional methods in a diverse range of production environments. Overall, the second-generation CMT process appears to offer compelling benefits in speed, adaptability, and precision, but further rigorous research and testing are needed to verify these improvements and to fully understand its potential for broader adoption in diverse industrial applications.
More Posts from patentreviewpro.com: