Decoding the Permanent Press Cycle A Deep Dive into Wrinkle-Reducing Laundry Technology
Decoding the Permanent Press Cycle A Deep Dive into Wrinkle-Reducing Laundry Technology - Origins of Permanent Press in 1950s Laundry Technology
The rise of synthetic fabrics in the 1950s created a need for new laundry methods. Traditional washing techniques weren't well-suited for these materials, often leading to excessive wrinkling. Permanent press technology emerged as a solution, specifically tailored to the care requirements of these newer fabrics. This approach centered around a unique wash cycle that cleverly combined warm water for washing and cold water for rinsing, aiming to suppress wrinkle formation. Further, by tweaking the traditional agitation and spin processes – reducing their intensity and slowing spin speeds – the cycle aimed to decrease fabric compression during the wash cycle. This helped minimize the development of wrinkles. While initially designed for synthetic fabrics, it soon became apparent that permanent press benefits extended to many everyday materials that are prone to wrinkling. In effect, it presented a valuable alternative to ironing while also helping to maintain the vibrancy of colors and protect the integrity of the fibers in fabrics.
The genesis of permanent press in the mid-20th century was driven by the expanding availability of synthetic fabrics. These fabrics, while offering advantages like durability and colorfastness, were often prone to excessive wrinkling, requiring considerable effort to maintain a presentable appearance. This spurred the development of washing and drying cycles specifically designed to address this issue.
The permanent press cycle, as it became known, primarily targeted fabrics with a propensity for wrinkles, encompassing blends of natural fibers like cotton and linen with synthetics. The core principles of the cycle focused on mitigating wrinkle formation through carefully controlled temperature profiles. The wash phase often utilizes warmer water to help loosen dirt and detergent, but the rinse phase shifts to cooler temperatures, preventing the setting of wrinkles during the cooling process.
This cycle distinguishes itself by utilizing gentler agitation and slower spin speeds, minimizing the physical compression of wet garments that can lead to crease formation. The incorporation of a cool-down period before the final spin allows the fibers to gradually relax, further minimizing wrinkling. Similar concepts are reflected in dryer settings which utilize medium heat coupled with a prolonged cooldown period for optimal wrinkle release.
Interestingly, permanent press techniques are not strictly limited to synthetics. Many natural fiber garments that readily wrinkle also benefit from these cycles. Beyond simply reducing wrinkles, the temperature profile of the permanent press cycle also contributes to fabric and color preservation. The combination of warmer wash and cooler rinse contributes to colorfastness and fiber integrity.
While the convenience of reduced ironing is highly appealing, it's important to acknowledge that the chemical treatments often used in permanent press fabrics can have drawbacks. These treatments, aimed at making garments wrinkle-resistant, can lead to a degradation of the fabric over time. This can translate into a shorter lifespan for clothes treated with permanent press finishes. The balance between convenience and garment longevity remains an interesting tradeoff for both textile manufacturers and consumers.
Decoding the Permanent Press Cycle A Deep Dive into Wrinkle-Reducing Laundry Technology - Cool Temperatures and Slow Spins The Wrinkle-Reducing Mechanism
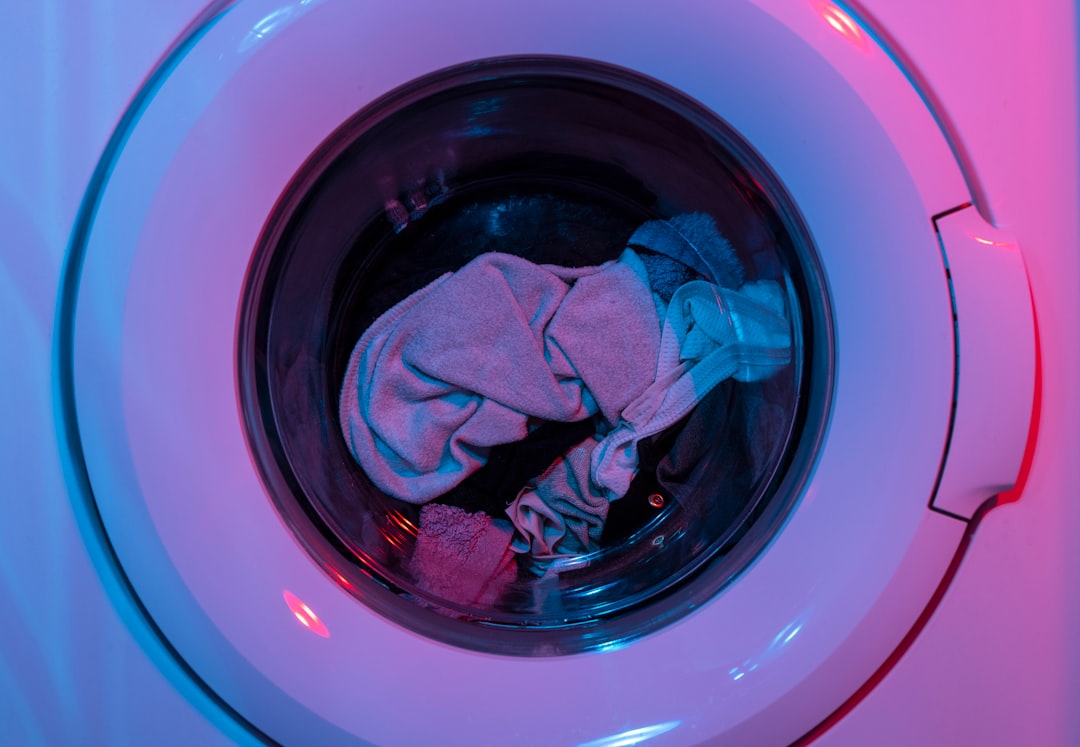
The heart of the Permanent Press cycle's wrinkle-reducing prowess lies in its use of "Cool Temperatures and Slow Spins." By employing cooler water during the wash and employing gentler, slower spin cycles, the process reduces the compression and stress on fabrics. This minimizes the formation of deep wrinkles and creases during the washing process itself. Importantly, the cycle includes cool-down phases which allow the fibers to relax, further reducing the chances of wrinkles becoming permanent. This strategy not only helps maintain the desired appearance of materials like synthetics and wrinkle-resistant fabrics but also aids in preserving fabric integrity by minimizing damage that can cause fading and wear.
It's worth noting that while this technological approach undeniably makes laundry easier by decreasing the need for ironing, there can be drawbacks associated with it. The chemical treatments used to create wrinkle-resistant fabrics, while helpful, can sometimes compromise the long-term durability of garments. This is a trade-off consumers may need to consider when choosing clothing. The convenience provided by wrinkle-resistant fabrics and the Permanent Press cycle should be balanced against the potential for a reduced lifespan of some garments due to those chemical treatments.
The cool-down rinse within the permanent press cycle isn't just about reducing wrinkles; it also subtly influences the fabric's final state, minimizing any temporary distortions that arise during washing as the fabric's temperature gradually settles. This careful management of temperature transitions is crucial for achieving a smooth, wrinkle-free finish.
The slower spin speeds employed in the permanent press cycle are a key aspect of wrinkle reduction. By minimizing the centrifugal force on wet fabrics, it avoids the extreme creasing that can occur during high-speed spins. This gentle approach helps maintain fabric integrity and prevents deep wrinkles from setting in.
Interestingly, the incorporation of a cooldown period, both during washing and drying, plays a vital role in how synthetic fibers behave. This pause allows these fibers to slowly relax, thereby minimizing the internal stress that often leads to wrinkles. This gentle relaxation process is a critical aspect of reducing wrinkles and preventing long-term damage.
The permanent press cycle's success is also tied to its ability to regulate the moisture content of fabrics. By managing moisture levels, it significantly decreases the probability of wrinkles forming from excess dampness as the garment dries. This careful balance of moisture is important for achieving a wrinkle-free finish.
The gradual temperature changes built into the permanent press cycle contribute to the overall stability of synthetic fabrics. Abrupt temperature shifts, in contrast, can lead to fiber distortion or swelling, causing potential long-term harm. Thus, this smooth temperature transition plays a significant role in maintaining the fabric's structure over time.
It's noteworthy that many synthetic fabrics undergo chemical treatments to achieve wrinkle-resistance. However, the effectiveness of these treatments often declines over time, particularly when exposed to high heat. The permanent press cycle provides a valuable tool for maintaining fabric performance by carefully limiting heat exposure.
Beyond just reducing wrinkles, the combination of warm water washing and a cool rinse in the permanent press cycle optimizes cleaning. These distinct temperatures can enhance detergent performance, potentially leading to more effective stain removal. This integrated approach is a benefit in addition to wrinkle-reduction capabilities.
Since the permanent press cycle incorporates cooler rinse temperatures and lower agitation levels, it often results in reduced energy consumption when compared to conventional hot wash cycles. This can lead to a significant decrease in both energy use and related expenses over time, promoting a more energy-efficient laundry process.
Research suggests that consistently employing the permanent press cycle can extend the lifespan of garments compared to traditional washing methods. The reduced mechanical stress and thermal shock during these cycles help minimize fabric degradation, resulting in fewer instances of wear and tear.
As textile and washing machine technologies progress, we'll likely see new wrinkle-reducing methods emerge. These advancements, possibly including novel fabric treatments or innovative washer designs, could enhance the effectiveness of permanent press technology in the future. This continuous pursuit of improvement highlights the ongoing relevance of wrinkle reduction and fabric care.
Decoding the Permanent Press Cycle A Deep Dive into Wrinkle-Reducing Laundry Technology - Fabric Compatibility Optimizing Permanent Press for Synthetics
Within the realm of laundry care, tailoring the permanent press cycle for synthetic fabrics presents a targeted method for wrinkle management. This cycle, particularly suitable for materials like polyester and rayon, leverages a measured approach involving controlled water temperatures and minimized agitation to effectively reduce wrinkling. The strategic combination of a warmer wash followed by a cooler rinse not only promotes wrinkle resistance but also helps maintain the structural integrity and color vibrancy of these fabrics. While the convenience of wrinkle-resistant fabrics is undeniable, it's crucial to understand that the chemical treatments often used to achieve this can potentially shorten the overall lifespan of a garment. Consumers must, therefore, consider the balance between the ease of reduced ironing and the possibility of a shorter garment lifespan when selecting fabrics that utilize permanent press treatments.
1. **Synthetic Fabrics and Moisture**: Synthetics, unlike cotton or linen, have a lower water absorption capacity. This characteristic means they dry more quickly, potentially reducing the window of opportunity for wrinkles to set in during the drying process. It seems that the quicker drying time is linked to reducing wrinkle development.
2. **Temperature Management and Fiber Stability**: The combination of warm water washing and a cold water rinse in the permanent press cycle is not only beneficial for wrinkle reduction, but also appears to help maintain the shape of synthetic fibers. Rapid shifts in water temperature can cause the fibers to swell, potentially leading to distortions. A gradual shift in temperature seems to prevent this, contributing to long-term fabric integrity.
3. **Gentle Agitation**: The gentler agitation found in permanent press cycles compared to other washing cycles minimizes the physical stress on the fabric structure. This seems particularly important for delicate fabrics that might be susceptible to stretching or damage during harsh washing. It's likely this reduced mechanical stress is essential for maintaining the size and shape of some fabrics.
4. **Detergent Optimization**: The warm water wash in the permanent press cycle can activate certain detergent enzymes. This might lead to better stain removal and a more efficient cleaning process. This means it is possible to achieve better cleaning with less harsh chemicals, which could lead to less wear and tear on the fabric.
5. **Extended Fabric Lifespan**: Research indicates that using the permanent press cycle can prolong the usable life of clothes. This might be due to the gentler nature of the cycle, which reduces the mechanical stress on fibers and prevents damage that can shorten garment lifespan. It's intriguing that a slower, gentler approach can be better for fabric durability.
6. **Cooling Down for Fiber Relaxation**: The gradual cool-down phase at the end of the permanent press wash cycle allows synthetic fibers to relax. This slow transition helps to minimize the risk of "thermal shock," which can cause fibers to wrinkle or become distorted, potentially leading to permanent creases. It's logical that if the fiber has time to adjust to changing temperatures, it may behave differently and not get damaged.
7. **Moisture Balance and Dye Stability**: The permanent press cycle helps regulate the moisture content within the fabrics, which can be crucial for both wrinkle reduction and maintaining the vibrant colors of the garment. It's interesting that maintaining a consistent level of moisture might not only improve wrinkle-free appearance but also affect the long-term color retention.
8. **The Importance of Controlled Spin**: The speed at which the wash cycle spins the clothes during the rinse process is not just random. Slight variations in spin speed can cause noticeable differences in how fabric wrinkles and how much stress the fibers experience. It's clear that reducing the spin rate is key to minimizing the formation of wrinkles.
9. **Chemical Finish Durability**: Many permanent press garments undergo chemical treatment to achieve their wrinkle-resistant qualities. But these treatments can be damaged by repeated heat exposure. By utilizing lower temperatures during washing, the permanent press cycle helps to preserve these finishes, extending the wrinkle-resistant effect. It makes sense that maintaining the fabric finish is important and it appears a well designed cycle can assist.
10. **Future of Permanent Press**: As advancements in materials continue, it's likely we'll see new types of synthetic fibers emerge that may be even more wrinkle-resistant than those currently available. This evolution could lead to future washing machines and permanent press cycles that are designed for these new materials and further reduce wrinkles. This area seems promising as researchers continually work to improve fabrics and cleaning processes.
Decoding the Permanent Press Cycle A Deep Dive into Wrinkle-Reducing Laundry Technology - Cycle Duration Analysis Comparing Permanent Press to Normal Wash
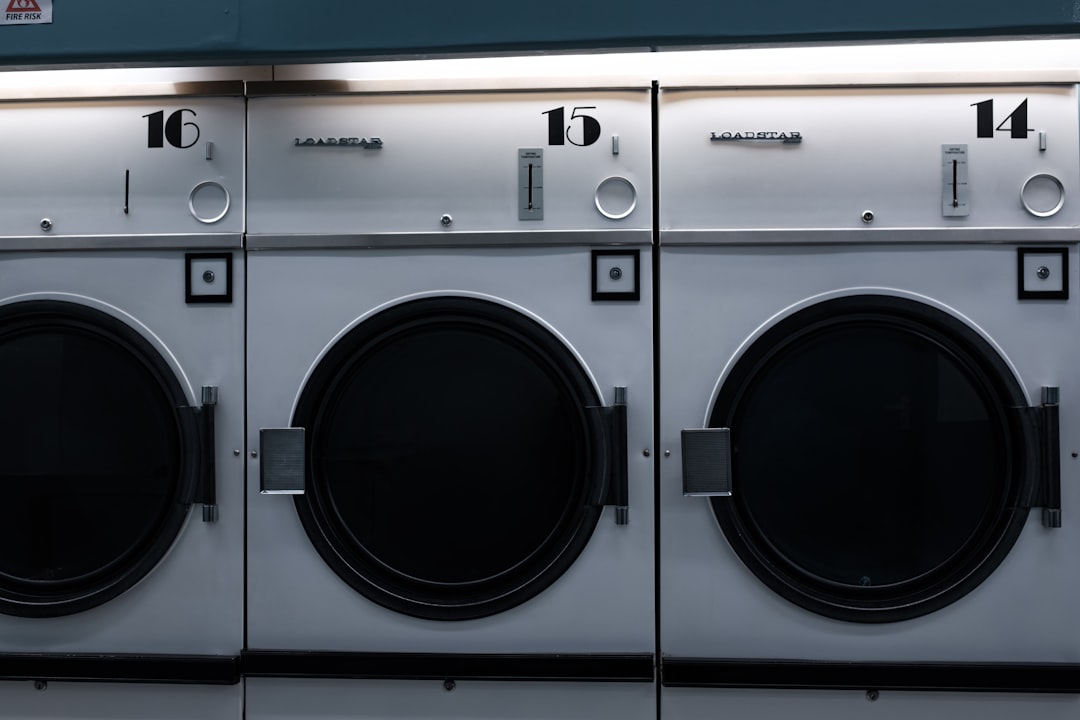
Examining the duration of wash cycles reveals distinct approaches between permanent press and normal wash cycles. The permanent press cycle prioritizes gentler handling of fabrics, using lower water temperatures and slower spin speeds. This is particularly beneficial for synthetics and blends prone to wrinkling, as it minimizes the development of creases and helps maintain the fabric's structure. Conversely, the normal cycle, with its hotter water and more vigorous agitation, is generally more suited for sturdy fabrics that can withstand harsher treatment. However, this can increase the risk of damage like fading or shrinking in more delicate fabrics. By appreciating these differences in approach, we can select the appropriate wash cycle to optimize garment care and maximize their lifespan.
When comparing the permanent press cycle to a normal wash, several key distinctions emerge, particularly regarding the duration, temperature management, and agitation intensity. The permanent press cycle typically takes longer, often extending 15 to 30 minutes beyond a normal wash. This extended time is dedicated to implementing cool-down stages, a critical aspect of preventing wrinkles from becoming ingrained in the fabric, particularly for synthetics.
Spin speeds within the permanent press cycle are considerably slower, sometimes as much as half the speed of a normal wash. This reduction in centrifugal force is designed to minimize intense creasing and ensure a gentler approach to handling more delicate fibers. Synthetics, like polyester, are particularly prone to deformation under excessive heat. The permanent press cycle mitigates this risk by limiting heat exposure, thus preventing distortion and maintaining the overall structural integrity of the garment.
Interestingly, the use of warm water in the permanent press cycle enhances the effectiveness of certain enzyme-based detergents. This optimized cleaning allows for better stain removal without requiring harsher chemical solutions that could potentially weaken the fabric. Further, maintaining a more balanced moisture level throughout the wash process is a central tenet of the permanent press cycle. This precise control minimizes the possibility of wrinkles developing due to excessive dampness during the drying phase.
Many permanent press fabrics are treated with chemical finishes to impart wrinkle resistance. It's notable that the gentler temperature profiles used in the permanent press cycle help maintain the effectiveness of these treatments over time, unlike traditional wash methods, which can lead to their degradation. The impact of fabric composition on the outcome of a permanent press cycle is also an area of interest. Different synthetic blends can respond differently; for instance, polyester blends often exhibit fewer wrinkles compared to pure synthetics, highlighting the importance of understanding fabric composition when selecting wash cycles.
The inclusion of cooling phases during the permanent press cycle is aimed at mitigating the potential for thermal shock, which can damage delicate fibers. This gradual adjustment in temperature helps to preserve the garment's appearance and lifespan. Research suggests that the gentler spinning and agitation characteristic of the permanent press cycle also leads to reduced machine vibration. This, in turn, minimizes fabric tangling and overlap, further reducing wrinkles, a particularly beneficial aspect for delicate materials.
Future developments in fabric technology hold promise for even more wrinkle-resistant synthetics. As these advances emerge, we can expect laundry technologies and cycle designs, including the permanent press cycle, to evolve to optimize performance and maximize wrinkle reduction for newer materials. The intersection of textile and washing machine innovation continues to refine fabric care practices and demonstrate the persistent relevance of wrinkle reduction.
Decoding the Permanent Press Cycle A Deep Dive into Wrinkle-Reducing Laundry Technology - Energy Efficiency Room Temperature Air in Dryer Finish
The final stage of the permanent press dryer cycle often introduces room temperature air, a detail that contributes to wrinkle reduction. This cool-down period helps to gradually lower the temperature of the clothes, promoting relaxation in synthetic fibers and reducing the likelihood of persistent wrinkles. By controlling the temperature at this point, the dryer aims to minimize creasing and potentially preserve the effectiveness of any chemical treatments designed to resist wrinkles. While this cool-down approach provides a convenient way to manage wrinkles as they form, there's a question of how frequent use of these cooling cycles might influence the longevity of these chemical treatments and the overall lifespan of the garments. Ultimately, the trade-off between the ease of reduced wrinkles and potential effects on fabric durability remains a point of consideration when evaluating this technology.
The use of room temperature air in the final stages of a dryer's cycle for permanent press settings is a fascinating aspect of energy efficiency. While it might seem counterintuitive, allowing garments to cool gradually using ambient air can surprisingly reduce energy use compared to traditional dryer heat. This method offers a potential path towards lessening energy demands and lowering operating costs in laundry settings.
However, the effectiveness of this method is intricately linked to the humidity present in the surrounding air. Higher humidity can interfere with the drying process, potentially increasing the likelihood of wrinkles lingering in the fabrics. Finding the right balance between temperature and moisture becomes crucial for a wrinkle-free finish, adding another layer of complexity to the process.
Furthermore, the gradual temperature changes during this cooling period seem to influence the fibers themselves. Fabrics, especially synthetic ones, experience less thermal shock, helping them relax and return to their original form. This gentler approach to cooling has the potential to improve garment comfort and overall aesthetics, particularly for delicate synthetic materials.
It's also intriguing that the effectiveness of this room-temperature drying varies depending on the type of fabric. Polyester, for instance, seems to respond differently than cotton blends, indicating that tailored drying approaches could optimize results for different material compositions. This suggests that future research and development may lead to more sophisticated drying programs that automatically adjust to fabric type.
Furthermore, air circulation plays a substantial role in how effective this technique is. The flow and distribution of air within the dryer can impact drying times and wrinkle reduction, while simultaneously influencing energy consumption. Optimal airflow could contribute to both enhanced performance and decreased energy expenditure.
The density of the fabric also factors into the drying process. Heavier materials tend to retain heat for longer, even at room temperature, which can slow down the entire process. This means understanding the properties of fabrics becomes essential for predicting drying times and properly adjusting dryer settings.
Synthetic fabrics' inherent "memory" helps explain why this technique can work. They seem to possess a remarkable ability to return to their original shape when exposed to certain environments. Leveraging this characteristic via cooler air at the end of the drying process allows fabrics to naturally smooth out without the risk of setting unwanted wrinkles.
Interestingly, the amount of laundry placed in the dryer can influence both drying effectiveness and wrinkle formation. Overpacking, or including incompatible fabric types in the same load, could lead to inconsistent drying, increasing the chances of undesired wrinkles. This highlights the importance of proper load management for optimal results.
Tools like dryer balls or other aids can improve the efficiency of this room temperature air drying approach. They likely help create a better distribution of air within the drum, thus increasing the efficiency of the cool-down phase and potentially reducing wrinkle formation.
Emerging technologies promise even more advanced air-drying methods for the future. Smart sensors that can control humidity and airflow within the dryer are being investigated to precisely control the environment and ensure optimal drying while maintaining energy efficiency. These innovations could significantly refine the permanent press cycle, ensuring garments remain wrinkle-free while minimizing energy consumption.
This entire field of laundry technology continues to evolve. The application of room temperature air in the dryer finish suggests that achieving both wrinkle-free results and energy efficiency in laundry is a worthy objective. As the research and development of new textile and laundry technologies progress, we can expect to see continued advancements and optimizations that refine the wrinkle reduction and energy efficiency aspects of permanent press settings.
Decoding the Permanent Press Cycle A Deep Dive into Wrinkle-Reducing Laundry Technology - Chemical Treatments vs Mechanical Process Durable Press Distinction
The methods used to create durable press fabrics, meaning fabrics that resist wrinkles, can be divided into chemical treatments and mechanical processes. Chemical treatments, often called Durable Press or Permanent Press, involve altering the fabric's fiber structure on a molecular level to create a lasting resistance to wrinkling. In essence, they change the fabric's fundamental makeup to make it less prone to creases. On the other hand, mechanical processes, most notably the permanent press laundry cycle, achieve wrinkle reduction through carefully controlled washing and drying methods. This involves gentler agitation, precise temperature changes, and slower spin speeds to physically limit the formation of wrinkles.
While chemical treatments offer immediate benefits by readily making garments wrinkle-resistant, they can potentially degrade the fabric over time, which can lead to a shorter lifespan for the garment. In contrast, the mechanical processes found in the permanent press cycle rely on physics and gentle handling of the fabric, which generally have less negative impact on a garment's durability.
As advancements in textile and laundry technology continue, the combination and understanding of both chemical and mechanical approaches will be crucial for developing effective and durable wrinkle-reducing strategies. Striking the right balance between the convenience of easy-care fabrics and the long-term health of a garment is a challenge that both fabric manufacturers and consumers must grapple with.
The interplay between chemical treatments and mechanical processes like the Permanent Press cycle is crucial for understanding how wrinkle resistance is achieved in fabrics. While chemical treatments aim to create a surface-level resistance to wrinkles by modifying fiber structures, mechanical processes rely on careful temperature management and handling during washing and drying to physically minimize wrinkle formation.
Durable press finishes, achieved through chemical treatments, typically involve using cross-linking agents to modify the fibers' molecular structure. While effective, this modification can impact the fabric's long-term strength and increase the likelihood of fiber damage and breakage over time. This raises questions about the sustainability of this approach.
Interestingly, the efficacy of wrinkle-resistant chemical treatments is not static. They can gradually decline with repeated washes, especially those involving high heat. This highlights a potential trade-off: while the treatments provide immediate benefits, their effectiveness might not be fully maintained in common laundry practices.
The sensitivity of chemical treatments to temperature fluctuations is another aspect to consider. The Permanent Press cycle's cooler rinse step plays a dual role—it prevents wrinkles from setting while also helping to preserve the integrity of these chemical treatments. This synergistic effect showcases a potential benefit that purely mechanical methods wouldn't achieve.
Many synthetic fabrics exhibit a unique characteristic called “fiber memory”. They have a natural tendency to return to their original shape after being strained or distorted. The Permanent Press cycle leverages this quality by employing controlled temperature and moisture levels to encourage fibers to relax and revert to their original form. This contrasts with chemical treatments which aim to create a more static, inflexible state.
Mechanical processes intrinsically minimize the risk of distortion, unlike chemically-treated fabrics. Over time, chemically treated garments, if not carefully maintained, might experience a decline in structural integrity. In contrast, fabrics primarily relying on mechanical methods may exhibit greater resilience.
The textile industry increasingly explores a hybrid approach combining the durability of mechanical processes with the convenience of chemical treatments. This approach aims to create fabrics that are both long-lasting and easy to care for, showcasing a notable shift in the innovation landscape of textile technology.
Residual chemical agents from the treatments can react poorly with high heat during drying or ironing. This factor is often overlooked in common laundry practices and highlights a potential weakness of reliance on certain chemical finishes.
The specific composition of a fabric, particularly the combination of different fiber types, can impact both the performance of chemical treatments and mechanical processes. Blends may respond unpredictably, complicating the wrinkle reduction process. This underlines the importance of tailoring wash cycles to the specific fabric characteristics to achieve optimal results.
As material science continues to progress, we're likely to see new fabrics engineered to inherently resist wrinkles while maintaining a durable structure. This advance could change the role of current chemical treatments and create laundry cycles that cater to the specific demands of these improved materials.
Overall, the interplay of chemical treatments and mechanical methods in fabric wrinkle resistance reveals a complex relationship. Each approach presents its advantages and drawbacks, necessitating careful consideration by consumers and textile manufacturers to make informed choices for optimal garment care and lifespan.
More Posts from patentreviewpro.com: