Baldwin Technology's PREPAC Zero How Water-Free Cleaning Innovation Transforms Industrial Maintenance
Baldwin Technology's PREPAC Zero How Water-Free Cleaning Innovation Transforms Industrial Maintenance - Water Free Cleaning Method Cuts Industrial Maintenance Time By 50 Hours Per Year
Baldwin Technology's PREPAC Zero system utilizes a waterless cleaning approach that's altering the landscape of industrial maintenance. Claims suggest it can reduce annual maintenance efforts by a substantial 50 hours. Traditional industrial cleaning frequently encounters difficulties like inconsistency and inefficiency, often requiring significant manual intervention to rectify subpar results. The PREPAC Zero system, through automation and a water-free process, not only addresses this by offering more reliable cleaning but also contributes to a reduction in water consumption and wastewater output within factories. This, in turn, has positive implications for the environment. Furthermore, the heightened cleaning efficacy translates to notable cost reductions, showcasing the system's potential to improve operational efficiency while fostering a more environmentally friendly approach to industrial upkeep. This innovative cleaning method might well set new standards in the industry for ensuring cleanliness and compliance with regulations.
Baldwin Technology's PREPAC Zero system presents an intriguing alternative to conventional industrial cleaning methods. By substituting compressed air and specialized cleaning agents for water, it aims to drastically reduce the time spent on cleaning operations. Anecdotal evidence suggests that facilities employing PREPAC Zero have seen a 50-hour annual reduction in maintenance, hinting at a potentially significant impact on operational efficiency.
While immersion tanks and manual cleaning can often be inadequate, leaving residue and requiring further effort, PREPAC Zero's proponents argue that it minimizes the risk of incomplete cleaning. However, evaluating the effectiveness of such a system would require a thorough assessment across various industrial settings and types of machinery. Moreover, the assertion that it minimizes wear and tear by preventing water-related corrosion needs rigorous validation in a wider range of contexts.
The claim that PREPAC Zero cleaning agents are specifically designed to avoid damage to sensitive components raises questions about their long-term impact and potential side effects. The system's versatility, as claimed by Baldwin, is commendable, but further evidence on its compatibility with various material types and surface finishes is essential for wider adoption.
It is noteworthy that, in addition to saving maintenance time, PREPAC Zero's water-free approach reduces water treatment costs, thereby offering environmental benefits. However, one should also be cautious in assessing the environmental impact of the specialized cleaning agents used in the system. The claim of reduced evaporation rates leading to enhanced cleaning efficiency needs further substantiation.
Furthermore, the seamless integration of PREPAC Zero into existing maintenance workflows is a valuable feature, although the extent of any required workflow adjustments for specific industries remains unclear. The technology's ability to positively influence production uptime via cleaner and more reliable equipment operation is plausible, but it necessitates detailed investigation in various operational environments.
While the technology's foundation lies in extensive chemical research, it's important to approach such innovations with healthy skepticism. It remains to be seen whether PREPAC Zero's impact on industrial cleaning truly lives up to its claims of innovation and advancement. The absence of water and reliance on novel compounds calls for careful consideration of both its benefits and potential downsides across the broader industrial landscape.
Baldwin Technology's PREPAC Zero How Water-Free Cleaning Innovation Transforms Industrial Maintenance - Pre Impregnated Cloth Technology Makes Traditional Water Sprays Obsolete
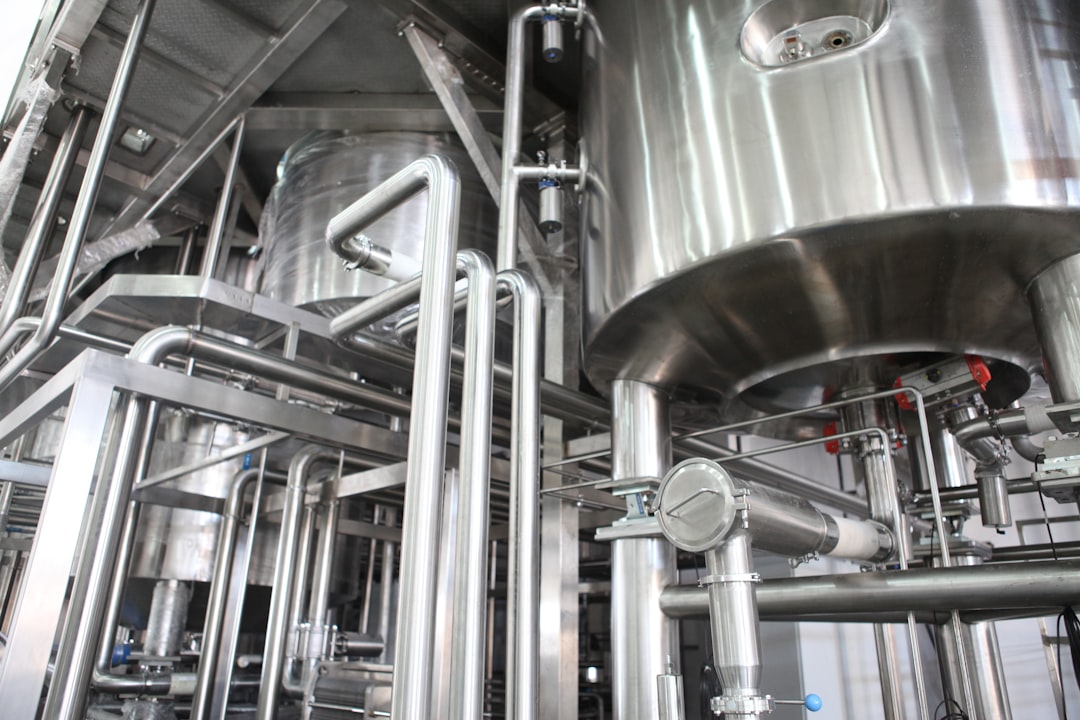
Pre-impregnated cloth technology is changing how industrial cleaning is done, potentially making traditional water spray methods a thing of the past. The core of this change is systems like Baldwin Technology's PREPAC Zero, which employ specially designed cloths saturated with cleaning agents. These cloths are engineered to effectively absorb ink and debris, providing a consistent, thorough cleaning process without the use of water. This not only simplifies the cleaning process and improves efficiency but also reduces the amount of waste produced and the costs associated with water use and treatment. While this technology seems promising, we need to critically evaluate the environmental effects of the specialized cleaning agents involved and confirm its compatibility with different types of materials and surfaces. The long-term effects and sustainability of the technology require ongoing assessment. Despite these considerations, the introduction of pre-impregnated cloths marks a significant step toward more efficient and eco-conscious practices in industrial maintenance. It is a change that could impact the industry's future approach to cleanliness and compliance.
Pre-impregnated cloth technology presents an intriguing alternative to conventional cleaning methods, particularly in industrial settings where water-based sprays are the norm. By removing the need for water as a primary cleaning agent, it potentially minimizes the risk of microbial growth and the presence of waterborne contaminants that can hinder equipment cleanliness. However, this approach introduces reliance on specific chemical formulations that need to be meticulously tailored to different materials and contaminants. The efficacy of this customization in minimizing residue and ensuring surface compatibility across various materials like metals, plastics, and composites warrants further investigation, particularly concerning long-term effects.
This shift in cleaning methodology could potentially reduce labor costs, as the cleaning process becomes faster and more efficient. The ability to reduce manual effort in cleaning tasks is promising in optimizing resource allocation. Interestingly, some formulations also incorporate static control capabilities, making them well-suited for environments where static discharge can pose problems, like electronics manufacturing.
Many manufacturers are promoting the biodegradability of the cleaning agents within the pre-impregnated cloths as an environmentally-friendly aspect of the technology. However, the scope and long-term implications of the breakdown process and its influence on the environment require further clarification. The incorporation of advanced microfiber technology can elevate cleaning performance through more effective dirt and particle capture, although it's important to note that the use of specialized cloths might increase the frequency of cloth replacement, or necessitate unique disposal procedures.
While the claims of this technology are enticing, the need for rigorous, independent testing across diverse industrial settings is crucial. It's important to evaluate the technology's efficacy, material compatibility, and overall safety before widespread adoption. It's also crucial to consider any potential trade-offs related to the reliance on specific chemical formulations. We must examine whether the absence of water necessitates a greater reliance on chemicals or frequent cloth replacement, and if so, what implications this has for user safety and handling protocols.
Ultimately, while pre-impregnated cloth technology offers an appealing departure from traditional water-based cleaning, careful consideration of both its benefits and potential drawbacks within a range of industrial contexts is essential before declaring it superior or universally applicable. Claims of enhanced cleaning and efficiency require validation, and the transition necessitates a comprehensive understanding of the associated risks and potential shifts in operational procedures.
Baldwin Technology's PREPAC Zero How Water-Free Cleaning Innovation Transforms Industrial Maintenance - WestRock Plant North Carolina Documents 100k USD Savings After PREPAC Implementation
A WestRock facility in North Carolina reported over $100,000 in cost savings during its first year after adopting Baldwin Technology's PREPAC cleaning system. This plant shifted from traditional dry cleaning cloths to PREPAC's pre-packaged cleaning cloths, a change that seems to have boosted productivity while supporting sustainability initiatives. One specific benefit cited was a reduction in solvent costs by roughly $13,000, highlighting how this change reduced expenses. The transition to PREPAC appears to have made cleaning both more effective and efficient, which contributes to their broader environmental goals. It's an example of how small changes in a manufacturing process can deliver large financial and operational improvements. This investment in PREPAC has clearly paid off in the first year. This success aligns with WestRock's broader efforts to operate more sustainably and fits within a growing industry trend towards greener production practices and technologies. It suggests that the way plants approach cleaning is evolving, with innovation like the PREPAC system potentially becoming more common.
A WestRock facility in North Carolina saw a significant cost reduction of over $100,000 in its first year after adopting Baldwin Technology's PREPAC cleaning solution. This suggests that innovative maintenance practices can have a substantial impact on the financial health of large-scale manufacturing operations.
Beyond just saving time, PREPAC's water-free approach also saves energy typically used for heating and moving water, hinting at a multi-faceted strategy for decreasing operational expenditures beyond just maintenance time.
The specially designed cloths within the PREPAC system seem to minimize the risk of contamination from cleaning residue, which is especially important in industries with strict cleanliness standards for product quality and regulatory compliance.
The cleaning agents in PREPAC Zero appear to be formulated to target common industrial contaminants, suggesting a more focused and efficient cleaning process that potentially reduces the need for repeated cleaning cycles.
Baldwin's emphasis on the high volatility of the cleaning agents used in PREPAC suggests these chemicals are designed to evaporate quickly, potentially leading to reduced drying times and less downtime for maintenance. This quicker process is valuable for operations aiming to keep production running smoothly.
The water-free nature of PREPAC potentially leads to less machine wear and tear in two ways: first, the absence of water reduces corrosion, and second, the cleaning process may involve less mechanical agitation compared to traditional methods. While intriguing, the overall impact on wear and tear in various industrial applications needs further exploration.
Baldwin promotes the use of phosphate-free and other environmentally-friendly formulations in PREPAC, which could potentially lead to longer equipment lifespan and operational stability, a claim that needs to be scrutinized through long-term studies.
The swift adoption of PREPAC in industrial settings might disrupt traditional cleaning schedules, giving facilities the potential for more flexible maintenance planning and greater production uptime. However, it's unclear how universally applicable this advantage is, given the inherent differences between diverse manufacturing settings.
The reliance on pre-impregnated cloths might mean maintenance staff needs to be retrained, which highlights a human factor often overlooked in discussions of technological change. Understanding and mitigating potential obstacles to training is essential for ensuring a successful transition.
The $100,000 in savings is a good indication of immediate cost benefits. But, more importantly, the optimized maintenance strategy through reduced downtime could provide the WestRock facility with long-term financial resilience in today's intensely competitive manufacturing landscape. However, we must remember that this is one specific case study and generalizing it without further evidence would be premature.
Baldwin Technology's PREPAC Zero How Water-Free Cleaning Innovation Transforms Industrial Maintenance - 50 Percent Reduction In Cleaning Waste Through Updated Material Design
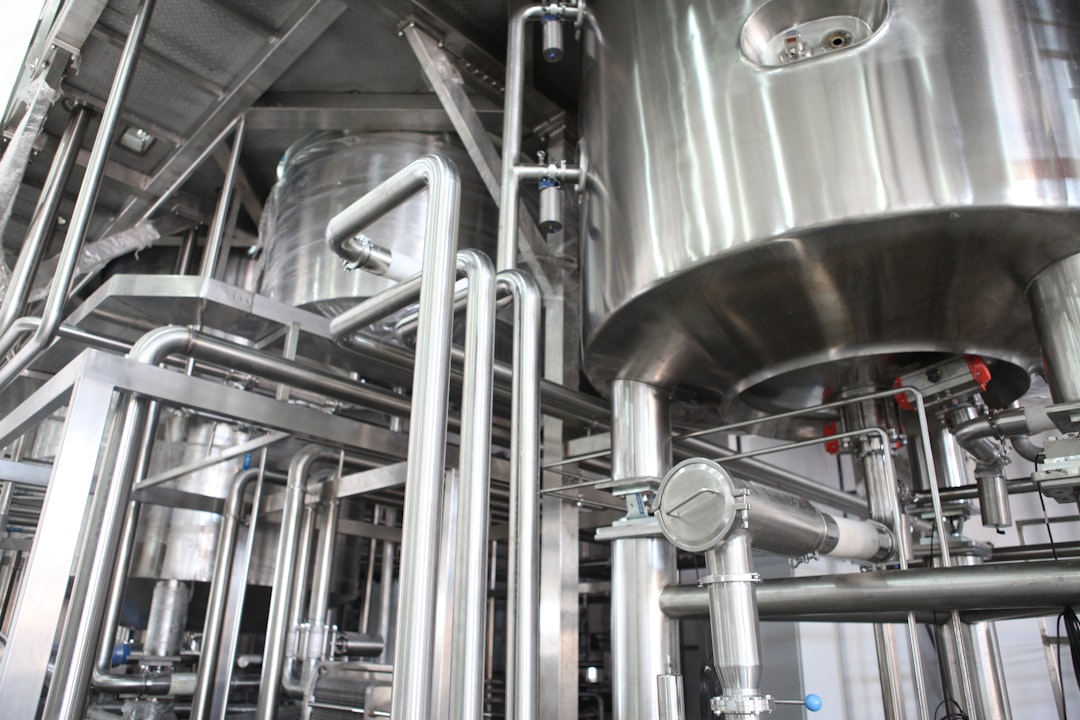
Baldwin Technology's PREPAC system incorporates a redesigned cleaning cloth and specialized cleaning agents that contribute to a substantial reduction in cleaning waste, potentially up to 50%. This advancement in material design plays a key role in enhancing the system's overall cleaning efficacy. By improving the effectiveness of the cleaning process, PREPAC aims to not only streamline industrial maintenance but also contribute to more sustainable practices. The specialized cloth, designed to efficiently capture contaminants and debris, and the tailored solvent formulas are intended to minimize waste generation. This focus on reducing waste is significant, especially as industries increasingly seek to implement more environmentally-conscious procedures.
While this material design update is presented as a key feature in optimizing industrial cleaning, it's crucial to rigorously evaluate its performance and compatibility across a broader range of applications. The long-term effectiveness of these updated materials, particularly when used in conjunction with diverse equipment and operating environments, needs to be thoroughly investigated before widely assuming a universal benefit. The environmental impact of the specialized solvents also remains a point that needs careful examination and ongoing assessment, given the shift away from traditional water-based cleaning. Despite these potential areas requiring further research, the changes introduced through the new material design do hold promise for significantly improving industrial cleaning protocols in a way that is more aligned with broader sustainability goals.
Recent advancements in industrial cleaning, exemplified by Baldwin Technology's PREPAC Zero, center around a shift from traditional water-based methods to a system relying on pre-impregnated cloths. These cloths, constructed from high-performance microfiber materials, are saturated with specifically formulated cleaning agents designed to target common contaminants found in various industrial environments.
The use of these specialized cleaning agents, while seemingly beneficial for targeted contaminant removal, also presents questions concerning their compatibility with different materials and surfaces. A thorough evaluation of long-term interactions is needed to ensure that this approach doesn't lead to unforeseen material degradation or chemical interactions. The unique formulation of these cleaning agents plays a crucial role in the efficiency of the PREPAC system, leading to a noticeable decrease in the number of cleaning cycles required. This is potentially a significant cost and labor reduction factor for various industries.
One appealing aspect of the waterless cleaning approach is the reduction of potential hazards associated with wet environments. By eliminating water from the process, the risk of accidents associated with moisture, such as slips, falls, and electrical hazards, is minimized.
Moreover, the cleaning agents' design emphasizes rapid evaporation. This characteristic is advantageous, as it helps reduce downtime related to drying. Consequently, equipment can be cleaned and returned to operation promptly, improving overall productivity. Notably, water's absence also decreases the possibility of microbial growth, which is critical in applications where hygiene is paramount, such as pharmaceutical or food production environments.
The system's compatibility with automated processes is also intriguing. This flexibility allows for potential integration with existing or planned automated cleaning systems. The prospect of smoothly transitioning from manual cleaning to automated workflows enhances the system's practicality.
Ultimately, PREPAC Zero's efficacy in reducing downtime is plausible. The accelerated cleaning process facilitates extended periods of operational uptime for machinery. However, it's important to note that the actual impact on downtime and production can vary depending on the specific industrial setting and operational environment.
The waterless nature of PREPAC also potentially addresses concerns about surface texture preservation. Unlike traditional methods that can sometimes degrade surface finishes, the PREPAC system aims to minimize such impacts, which is important for processes requiring high-precision machinery and consistent surface properties.
While preliminary results from a few facilities have demonstrated notable time and cost savings, implementing PREPAC Zero more widely is likely to encounter hurdles. Proper training, adaptable implementation strategies, and consistent execution are crucial for guaranteeing the success and maximizing the advantages of this system across a variety of industrial applications. It remains to be seen whether the initial successes can translate to consistent benefits across a wide range of manufacturing sectors. The technology's broad adoption will depend on its ability to effectively bridge the gap between promising preliminary results and reliable, widespread applicability.
Baldwin Technology's PREPAC Zero How Water-Free Cleaning Innovation Transforms Industrial Maintenance - 25 Year Track Record Shows Consistent Innovation In Industrial Cleaning
For 25 years, Baldwin Technology has been refining its approach to industrial cleaning, a journey marked by consistent innovation. This commitment to advancement is evident in products like PREPAC Zero, which offer a water-free cleaning method. The shift towards waterless cleaning simplifies the process by removing the need for water pump stations, making it more streamlined. Additionally, the system utilizes specially formulated cleaning agents and cloths that excel at removing common contaminants, like paper lint and ink, resulting in a more efficient clean.
Beyond streamlining the process, Baldwin's innovative technologies have the potential to significantly reduce waste—by as much as 50% in some cases—and shorten cleaning times, ultimately contributing to improved productivity. The ongoing development and integration of environmentally-conscious solutions, reflected in their technologies, show Baldwin is actively responding to the industry's growing focus on sustainable maintenance practices. However, it's crucial to remember that newly developed technologies require careful scrutiny in a variety of real-world applications to fully understand their effectiveness and long-term impact. Only through thorough evaluations across different industrial contexts can we truly assess the full scope of these innovations and their implications.
Baldwin Technology's 25-year history in industrial cleaning, particularly through their PREPAC line, suggests a sustained focus on refining cleaning techniques. The PREPAC Zero system stands out with its waterless approach, relying instead on pre-impregnated cloths to remove dirt and debris. These cloths, crafted from advanced microfiber materials, are designed to significantly improve contaminant capture compared to older methods. This improvement in dirt and particle retention translates to cleaner machinery, potentially increasing equipment longevity and reducing downtime linked to buildup.
The specialized cleaning agents in PREPAC Zero are formulated for fast evaporation, cutting drying times and the risk of residue. This rapid drying capability is important in environments demanding high cleanliness, like pharmaceutical or food processing. It's worth noting that the lack of water in the process also reduces the possibility of corrosion, a major concern for metal-intensive machinery. Reduced corrosion could lead to extended equipment lifespan and potentially lower maintenance expenditures.
Furthermore, PREPAC's compatibility with automation seems promising. It can integrate into existing cleaning routines with minimal disruption, potentially simplifying the transition to automated systems. The specialized nature of the cleaning agents is also an intriguing feature. Baldwin's chemists seem to have created blends aimed at specific contaminants in different sectors. This targeted approach potentially leads to more efficient cleaning cycles, reducing the need for excessive or repetitive cleaning, and saving both time and resources.
The water-free element of PREPAC has brought about a notable change in how cleaning is done in industrial settings. It’s an alternative for facilities seeking to minimize their water footprint without sacrificing cleanliness. Notably, the cleaning agents also feature static control capabilities, potentially addressing issues in sectors like electronics manufacturing where static can be troublesome. Reports from industrial users point towards substantial savings in solvent expenses, further reinforcing the economic benefit of reducing water and chemical use.
While the results seen with PREPAC Zero are encouraging, there's still a need for longer-term study into the interactions between the cleaning agents and the wide array of materials used in industry. We need more data to be certain the technology's effectiveness holds up across diverse industrial settings. The specific chemistry of the cleaning agents and their potential long-term impacts on various surfaces remain an open area of investigation. This is crucial, as it relates to the responsible and sustainable adoption of the technology across a broader range of applications. This critical evaluation phase is important to ensure that the initial promise of PREPAC Zero translates into enduring improvements in cleaning efficiency and effectiveness across diverse industrial settings.
Baldwin Technology's PREPAC Zero How Water-Free Cleaning Innovation Transforms Industrial Maintenance - Ink Management System Eliminates Drippage Issues In Printing Operations
Baldwin Technology's advancements in ink management systems have proven effective in addressing a long-standing challenge in printing: ink drippage. These systems, through the use of software and self-correcting features, ensure the right amount of ink is mixed and distributed. This precision minimizes waste and helps maintain consistent ink quality across large print jobs. Automation also plays a key role in simplifying ink preparation, increasing overall efficiency in the printing process. Moreover, these changes can lead to more environmentally responsible printing practices due to reduced ink waste. While these advancements show promise, it is important to understand how well they perform in various printing settings before concluding they're universally beneficial. As the printing industry continues to embrace automation and accuracy, well-designed ink management systems are likely to become a crucial part of operations.
In the realm of printing operations, ink management is crucial for maintaining both print quality and operational efficiency. One common challenge has been ink drippage, where excess ink or cleaning fluids tend to accumulate or leak from machinery, resulting in messy situations, contamination, and wasted materials. Baldwin Technology's PREPAC system tackles this problem with a unique ink management approach centered around specialized cleaning cloths.
The PREPAC system uses cloths designed with specific capillary flow properties, which enhance ink absorption and prevent dripping. This feature makes for cleaner operations since the cloths effectively capture ink and prevent it from dripping onto surfaces or causing other issues. Fewer drips translate to less frequent cleaning, ultimately improving operational efficiency. The impact of ambient humidity on ink behavior is a significant concern in conventional systems, as it can exacerbate drippage. The PREPAC system, by operating water-free, is less susceptible to these humidity-related problems. The waterless feature mitigates the complex interaction of water and environmental conditions, which are often a source of drippage issues.
PREPAC's cleaning agents are engineered with a specific focus on manipulating surface tension. By altering the surface tension of the ink and cleaning agent interface, the cleaning process becomes more efficient at absorbing ink and preventing the possibility of drippage during ink application. This approach improves the overall effectiveness of the cleaning process.
It's claimed that this enhanced ink absorption and management through PREPAC can reduce ink residue on equipment surfaces by a considerable margin – up to 80%, based on some findings. This decreased ink residue directly relates to the mitigation of drippage, but it also plays a role in improving the quality of the prints and minimizing the need for rework, as cleaner machinery equates to more consistent output.
The technology underpinning PREPAC includes methods for regulating ink dispersion from print heads with remarkable precision. This level of control over ink flow is vital for preventing drippage during the fast-paced operations of high-speed printing. The PREPAC system is also designed to accommodate a wide range of inks, including those that are UV- or water-based, meaning it can efficiently manage drippage across different printing applications and materials.
Interestingly, the water-free nature of the PREPAC system inherently reduces volatile organic compounds (VOC) released during cleaning and normal operation, a benefit related to the decreased drippage. Reduced VOC emissions contribute to a safer working environment and potentially improve a plant's adherence to relevant environmental standards.
Operators can fine-tune ink levels and flow rates thanks to the real-time feedback mechanisms built into the PREPAC system. These mechanisms act as a preventative measure, allowing operators to detect and correct any potential for drippage issues proactively. This feature promotes more stable and efficient operations.
However, while the early results from PREPAC are encouraging, it's important to adopt a research perspective. The long-term reliability and effectiveness of the PREPAC system in a diverse range of operating conditions need further scrutiny. Ongoing studies under different operating parameters and across various industrial contexts are essential to verify and refine the initial findings, to ensure the technology's robustness and its ability to perform consistently over time. It's through this kind of continuous evaluation and assessment that we can ensure that the promise of PREPAC translates into sustained improvements in the efficiency and effectiveness of printing operations.
More Posts from patentreviewpro.com: