Analyzing Water Wheel Bucket Design Impact on Efficiency and Power Generation
Analyzing Water Wheel Bucket Design Impact on Efficiency and Power Generation - Impact of Smooth Water Flow on Blade Efficiency
The performance of water wheels hinges on the quality of the water flow encountering the blades. A smoother flow translates to reduced turbulence and minimizes the energy losses that occur when water initially hits the blades. This improved energy capture is central to maximizing the water wheel's overall efficiency. Furthermore, stable and predictable water flow allows for fine-tuning the spacing between the blades. This spacing is vital for maintaining optimal performance across a range of operating speeds. While various blade designs and configurations contribute to efficiency, especially in low-head applications, understanding the relationship between water flow smoothness and blade interaction is key. This comprehension can drive substantial improvements in the efficiency of hydropower generation from water wheels.
When water flows smoothly around the water wheel blades, turbulence is minimized, fostering more efficient energy transfer. This can boost efficiency by a notable margin, potentially as high as 30%, compared to situations where the water flow is turbulent.
The design of the water wheel blades significantly influences how smooth water flow impacts performance. Specific blade curvatures are engineered to encourage laminar flow, which further enhances the wheel's ability to capture energy from the water.
The way a blade intercepts the water's flow is vital for performance. Through careful optimization of the blade's angle of attack, designers can reduce drag and improve the overall conversion of the water's kinetic energy into usable mechanical energy.
The width of the water jet impinging on the blade is strongly tied to the efficiency of energy extraction. Smooth water flow allows for a narrower jet width while still maintaining effective energy capture.
Smooth water flow, surprisingly, also contributes to the longevity of a water wheel. Reducing the forceful, turbulent impacts that blades normally experience in less optimal designs translates to reduced wear and tear. This translates to lower maintenance and a longer operational lifespan for the water wheel.
Interestingly, in pursuit of smooth water flow, design approaches frequently prioritize the use of materials with reduced friction. This highlights the importance of materials science, alongside fluid dynamics, in the pursuit of improved blade efficiency.
The relationship between water speed and blade design is not always straightforward. Fluid dynamics modeling suggests that exceeding a certain flow rate can result in diminishing returns on efficiency gains. This implies that there's an optimal flow rate to maximize performance.
Computational fluid dynamics (CFD) simulations offer a powerful tool for examining the effect of diverse water flow scenarios on blade performance. CFD analysis can reveal how even small design changes can significantly influence efficiency and other performance metrics.
The occurrence of "flow separation" can negatively impact the efficiency of the water wheel blades. Well-designed blades that prioritize smooth flow can mitigate this phenomenon, leading to substantial performance improvements that may not be evident without careful analysis.
Real-world applications demand that engineers consider the inherent variability of water flow conditions when designing for smooth flow. A successful design often needs adaptability to ensure consistent efficiency across the spectrum of operational environments.
Analyzing Water Wheel Bucket Design Impact on Efficiency and Power Generation - Inflow and Outflow Losses in Traditional Overshot Wheels
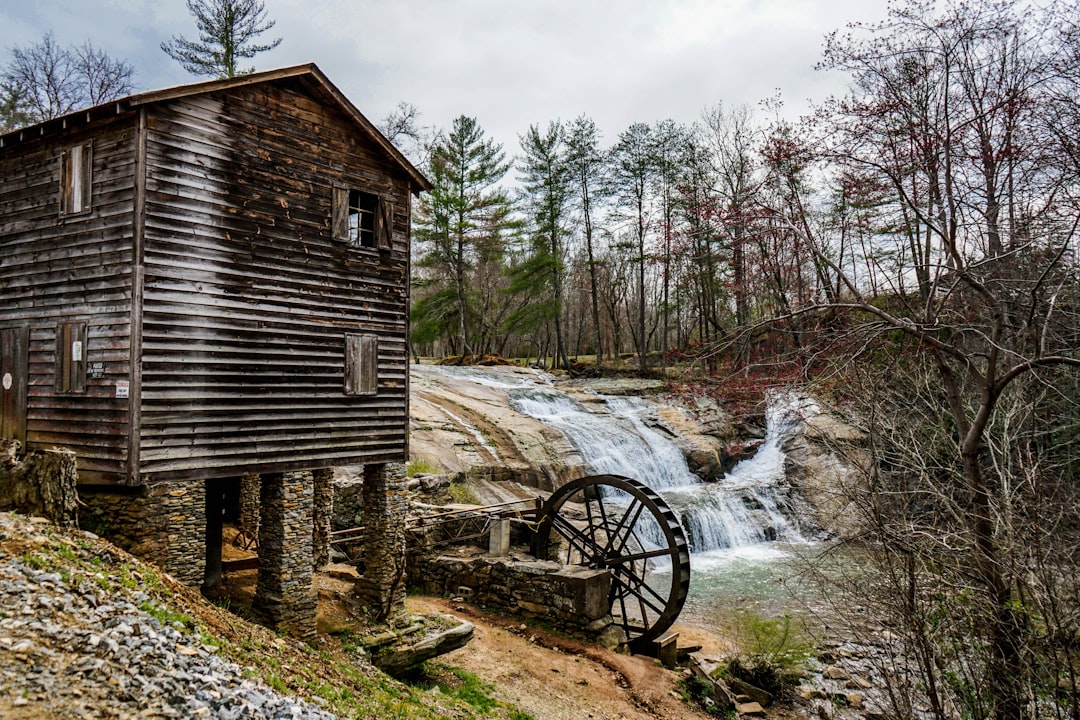
In traditional overshot water wheels, a significant portion of the available energy is lost during the water's entry and exit from the buckets. Inflow losses occur because the water doesn't always seamlessly transition into the buckets, often leading to less-than-ideal filling. This imperfect coupling can result in energy being wasted rather than converted to useful work. On the other hand, outflow losses occur when water spills out of the buckets as the wheel rotates. These losses, together with other losses like water impacts and incomplete bucket filling, emphasize the importance of thoughtful bucket design.
The challenge is to improve water wheel efficiency by minimizing these losses. This means designing buckets that facilitate smooth entry and exit of water to maximize the conversion of water's potential energy to mechanical energy that turns the wheel. This challenge drives efforts to create new water wheel bucket configurations that aim to reduce these power losses. While the path to optimization is still being investigated, ongoing tests and designs show promising directions for improving water wheel efficiency and enhancing hydropower production. The relationship between bucket design and hydropower efficiency remains a core focus of ongoing research, suggesting that further advancements in water wheel design are possible.
In traditional overshot wheel designs, inflow and outflow losses can be substantial, potentially representing up to 40% of the total energy losses. This makes understanding and mitigating these losses a critical aspect of improving the overall efficiency of the wheel. The manner in which water enters the buckets – the inflow angle – has a strong influence on outflow losses. Well-designed bucket entrances can minimize the spillage of water during rotation, ensuring a larger portion of the water's energy is effectively transferred to the wheel.
The depth and curvature of the buckets play a crucial role in how well water is retained as the wheel turns. Optimizing these features can lead to a longer retention time for water within the buckets, increasing energy extraction by as much as 25%. Intriguingly, even minor irregularities in the bucket's shape can introduce turbulence and exacerbate inflow losses. This emphasizes the importance of employing precise manufacturing methods when creating water wheels.
The timing of water release from the buckets also holds significant influence on efficiency. If water exits too early, there can be a considerable loss of kinetic energy. This underlines the need to carefully coordinate the wheel's speed with the water's flow rate and level. Depending on the application, buckets that are either too small or too large can hinder water flow, possibly resulting in the formation of bubbles. This bubble entrainment further reduces the efficiency of energy capture in overshot wheels.
Researchers and engineers have leveraged tools like computational fluid dynamics (CFD) and experimental fluid mechanics to show that managing the velocity profile of water at both the inflow and outflow stages can result in noticeable gains in power output, potentially up to 15%. Variations in inflow rates can alter the hydraulics within the buckets, impacting efficiency. Designs that account for these fluctuations can offer a significant performance advantage.
Furthermore, it's important to consider maintenance practices, as debris or biofouling within the buckets can disproportionately increase both inflow and outflow losses, even with relatively small obstructions. Interestingly, when reviewing historical overshot wheel designs, it becomes clear that the design of water exit pathways was often overlooked. Modern analysis suggests that optimizing these exit pathways can significantly minimize drag and further improve energy recovery from the system. This perspective highlights the ongoing research and refinement efforts in overshot wheel design, continually seeking ways to improve performance and energy efficiency.
Analyzing Water Wheel Bucket Design Impact on Efficiency and Power Generation - Volumetric Losses and Water Impact on Overshot Wheel Blades
Overshot water wheels can suffer from volumetric losses, which occur when the wheel's buckets don't fill completely with water. This incomplete filling reduces the amount of energy that can be extracted from the water, impacting the overall efficiency of the system. The shape and entry points of the wheel's blades are key factors in minimizing these losses. Well-designed blades facilitate smoother water flow into the buckets, leading to more effective energy capture.
However, as the rotational speed of the wheel increases, the potential for further volumetric losses also grows. This highlights the importance of understanding the relationship between rotational speed and blade design in optimizing performance. Sophisticated design strategies, focusing on water flow optimization, offer promising avenues for significant efficiency improvements, particularly when applied to lower-head hydropower systems. While efficiency gains are possible, the challenge remains to create designs that balance energy capture with minimizing these losses, particularly at higher rotational speeds.
Overshot water wheel efficiency can be significantly impacted by how well the buckets capture and retain water, a phenomenon influenced not just by bucket design but also by water's inherent properties like viscosity and surface tension. This interplay can affect how efficiently buckets fill during the initial inflow.
When water exits the buckets, the timing and angle of release are critical. A well-timed release can greatly reduce kinetic energy losses, potentially boosting overall efficiency by up to 20%. This highlights the need to precisely coordinate water flow and wheel speed for optimal performance.
A poorly designed bucket can cause flow separation, creating swirling eddies that disrupt the smooth flow of water and dramatically reduce efficiency. In some instances, this turbulence can cause a decrease in efficiency exceeding 30%. The importance of minimizing flow separation is evident in the need for careful bucket design.
CFD simulations have shown that minor tweaks in bucket curvature can have a significant influence on inflow losses. This reveals how small changes in design can lead to noticeable differences in engineering performance, highlighting the importance of meticulous design.
The size of the water jet entering the buckets varies with the water wheel's rotation speed, impacting the efficiency of water capture. Optimizing this relationship across different operating speeds can lead to a reduction in inflow losses by roughly 15%, suggesting a need for robust designs.
Intriguingly, research suggests that buckets designed to retain water for longer durations can result in significant energy recovery gains. Some designs show up to a 25% increase in energy extraction efficiency, emphasizing the importance of considering water retention time in bucket design.
Debris and biofouling, which are natural occurrences, can noticeably increase outflow losses by up to 10%, highlighting the importance of regular maintenance to ensure the wheel's continued optimal operation. This emphasizes the need to incorporate maintenance considerations in the design process.
The rotational inertia of the wheel and the water's flow rate are interconnected in a way that can influence water release timing. If the wheel has high inertia, it can lead to poorly timed release, ultimately affecting the wheel's efficiency. This interaction requires careful attention during design.
The relationship between inflow angles and bucket depth is essential. A carefully chosen inflow angle can not only reduce turbulence but also improve how efficiently water is captured, leading to marked performance gains. This underscores the need for integrated design considerations.
Interestingly, a review of historical designs shows that often aesthetic concerns were prioritized over functional hydrodynamics. This provides a compelling opportunity for contemporary engineers to leverage advanced fluid dynamics tools to enhance traditional overshot water wheel designs, potentially boosting efficiency significantly. This approach combines traditional wheel concepts with cutting-edge analysis.
Analyzing Water Wheel Bucket Design Impact on Efficiency and Power Generation - Bucket Shape and Material Influence on Power Generation
The shape and material of water wheel buckets play a pivotal role in determining their efficiency and power output. Traditional bucket designs, while functional, often exhibit shortcomings in terms of water flow management. For instance, straight or conventionally shaped buckets can lead to substantial energy losses during water entry and exit, as well as incomplete filling of the bucket itself. However, alternative shapes, like circular buckets, have demonstrated improved flow patterns, resulting in higher energy conversion. This suggests there is untapped potential in optimizing bucket geometry for more efficient energy capture.
Furthermore, the material choice significantly impacts the water wheel's performance and longevity. The material's inherent frictional properties influence the amount of energy lost due to drag, and its durability impacts the system's lifespan and overall maintenance needs. The interplay between bucket shape and the material used is crucial for reducing energy losses and improving efficiency. Careful consideration of these two aspects is critical for creating optimized water wheels that can provide a higher return on the energy investment, ultimately contributing to more effective hydropower generation. While the design of traditional buckets was largely driven by practical considerations, the analysis of the relationship between bucket design, material selection and energy generation provides pathways to improved efficiency. Ongoing efforts towards refinement of bucket design, coupled with a thorough understanding of materials properties, will hopefully advance water wheel efficiency in the future.
The selection of materials and the resulting bucket shape significantly impact the power generation capabilities of a water wheel. For example, the material's density influences the overall weight distribution, which, in turn, affects the rotational inertia of the wheel. Heavier materials can offer enhanced stability but may require more energy to initiate and maintain rotation, potentially decreasing overall efficiency. Conversely, lighter materials may improve responsiveness but could compromise structural integrity if not carefully designed.
Optimizing the bucket's shape itself can have a profound effect on the power coefficient – the ratio of power output to the power of the incoming water. For example, a curved bucket can often capture energy from the water more effectively, possibly resulting in a 15-20% efficiency improvement compared to a less optimized design. Researchers often use computational methods to find the balance between intricate bucket shapes that enhance energy capture and practical considerations during manufacture and operation.
Another crucial aspect is the material's coefficient of friction. A lower coefficient of friction between the bucket surface and the water reduces energy loss from drag during water entry and exit. This results in smoother wheel operation and can lead to a noticeable gain in efficiency, potentially up to 10%.
Temperature fluctuations can also play a significant role in material performance. Changes in temperature can alter the material's physical properties, such as its tensile strength and flexibility. This understanding is crucial, as variations in temperature can lead to unexpected drops in efficiency during periods of high water flow and operational demands.
Surprisingly, bucket shape also has implications for aerodynamics, especially in larger wheel designs. Poorly designed buckets can generate drag that hampers performance even when the wheel isn't fully submerged in water. This might lead to efficiency reductions as high as 20% compared to well-designed buckets, underscoring the importance of considering multiple aspects during the design process.
The inertia of the bucket's profile influences how quickly a water wheel responds to changes in flow rate. A design with lower inertia allows for rapid adjustments, enabling the wheel to better capture energy in conditions where the flow rate varies. This can be particularly advantageous in settings with variable water sources.
Some materials used in bucket construction can absorb moisture over time, potentially changing the weight distribution and compromising structural integrity. Continuous monitoring of material behavior is important in these cases to ensure that the bucket maintains its designed performance.
Finite element analysis (FEA) is a computational tool engineers use to test different bucket shapes against the stress exerted by the force of the water. FEA has been instrumental in the development of designs that can withstand greater impacts without sacrificing energy efficiency.
The specific geometry of the bucket edges influences water interaction during entry and exit. Minimizing interference at the bucket edge creates a smoother transition for the water, potentially improving energy capture by around 15%.
Interestingly, a review of historical water wheel designs reveals that aesthetics often took precedence over functional hydrodynamics. Modern engineers, equipped with advanced computational fluid dynamics tools, have the opportunity to apply aerodynamic principles to these designs, refining bucket shapes to potentially achieve substantial efficiency improvements. This shows how the past can inform the future and offers a powerful opportunity to enhance traditional hydropower methods.
Analyzing Water Wheel Bucket Design Impact on Efficiency and Power Generation - Pelton Wheel Design for High-Head Hydroelectric Applications
Pelton wheels are a prevalent choice for high-head hydroelectric power generation, excelling at converting the potential energy of water into rotational energy. The effectiveness of this conversion hinges on the intricate design of the wheel, including aspects like bucket geometry, exit angles, and overall structural configuration. Optimizing the bucket exit angle, ideally aiming for close to 180 degrees, is a key strategy to minimize energy losses and maximize efficiency. Furthermore, the performance of the Pelton wheel is significantly impacted by the height of the water source (hydraulic head) and the precision of manufacturing methods employed. This leads to a wide range of Pelton wheel applications, from small, low-power systems to large-scale installations designed for substantial power generation. While Pelton wheel technology is established, the ongoing search for enhancements in these design elements presents a path towards potentially substantial increases in power generation within the context of high-head hydropower. This area of design presents promising avenues for ongoing research and development to further refine and advance the technology.
Pelton wheels are a type of impulse turbine that are especially good for hydroelectric power plants with high water pressure differences and lower flow rates. These are often found in mountainous areas where the water can fall from a great height. The efficiency of a Pelton wheel relies on several factors including the shape of the buckets, the speed the wheel spins, and the characteristics of the water jet.
One of the most important aspects of Pelton wheel design is the angle at which the water exits the bucket. Ideally, the water should exit close to 180 degrees to minimize energy loss and improve efficiency. The amount of power a Pelton wheel can produce can be estimated using a fairly basic equation that takes into account the flow rate of water and the speed of the water jet. Pelton wheels are available in a wide range of sizes, from tiny turbines used for low power applications to massive units that can generate a lot of electricity in large hydroelectric dams.
The height from which the water falls – or head – has a major effect on how well a Pelton wheel performs. Higher heads result in better performance as the water falls faster and thus gains more kinetic energy. Pelton wheels are very good at transforming the stored energy of the water into useful mechanical energy and can achieve high efficiency levels especially when the water is flowing at very high speeds. Some critical design factors include keeping the clearances between the moving parts as small as possible to reduce energy losses due to friction and maximize the transfer of kinetic energy from the water jet to the turbine's rotation.
Pelton wheels are built to take advantage of the kinetic energy of high-speed jets of water. The water strikes the specially-shaped buckets, which in turn rotates the turbine. The pressure in the casing around the turbine can vary depending on the height of the water in the reservoir. This casing pressure does affect the Pelton turbine's efficiency in sometimes unpredictable ways.
It's important to remember that the relationship between water jet speed and Pelton wheel efficiency is complex. There's likely an optimum speed for a given design, and exceeding this speed can lead to reduced efficiency because of increased turbulence and other losses. This understanding is essential for maximizing the performance of Pelton turbines in various applications. Computational fluid dynamics (CFD) modeling is a powerful tool for investigating the impact of different factors on Pelton wheel performance. This type of modeling allows for a wide range of scenarios to be investigated without having to build physical models.
The issues around cavitation in Pelton designs is an important one. Cavitation can damage Pelton wheel components if the water pressure is too low in certain regions. Designers must understand the limitations and select operating points that minimize the possibility of cavitation damage to the turbine.
Analyzing Water Wheel Bucket Design Impact on Efficiency and Power Generation - Numerical Analysis Methods for Water Wheel Performance Prediction
Numerical methods, especially computational fluid dynamics (CFD), are becoming increasingly important for understanding how water wheel designs affect performance. CFD allows researchers to simulate the complex water flow around the wheel's buckets, providing insights that may be difficult to obtain through experiments alone. Recent research has shown success in using techniques like the Volume of Fluid (VOF) method, combined with turbulence models, to predict a water wheel's performance. These predictions have been shown to correlate well with experimental data. This approach enables designers to explore different design variations, such as changing the bucket shape or inflow angle, to improve energy conversion. The progress in numerical analysis methods not only helps us better understand how water wheels work, but also provides valuable information to guide future developments in water-based energy generation. While the field is still evolving, it's clear that these numerical tools are providing a powerful platform for innovation in hydropower technology. There are some challenges to CFD modeling that still need to be addressed, such as ensuring the models accurately represent real-world conditions. Despite these, CFD's ability to quickly evaluate different designs is an important benefit for engineers working on water wheels.
1. **Optimizing Stability:** The design of water wheel buckets plays a major role in overall stability. Minimizing losses during water entry and exit is key, as poor bucket designs can lead to energy losses exceeding 40% of the total. Addressing this through careful design could significantly improve overall wheel performance.
2. **Flow Rate Sweet Spot:** Interestingly, the relationship between water flow rate and efficiency isn't linear. It's possible that increasing flow beyond a certain point may actually decrease efficiency, suggesting an optimal flow rate for maximizing energy capture.
3. **Material Impacts Efficiency:** The material used to construct the water wheel buckets has a direct effect on energy loss due to friction. Choosing materials with lower coefficients of friction could reduce energy losses by as much as 10%, highlighting the importance of material selection in the overall design process.
4. **Bucket Geometry: Depth and Curvature:** The depth and curvature of the buckets have a substantial influence on how long water is retained within them. A properly designed bucket can increase the water retention time and improve energy extraction by up to 25%, demonstrating the significant impact of these geometrical parameters on efficiency.
5. **Cavitation Challenges in Pelton Wheels:** Cavitation is a potential problem in Pelton wheel applications, particularly in high-head systems. It can cause significant damage if water pressure in certain areas drops too low. Designers must consider these pressure conditions carefully to prevent cavitation damage to the turbine and ensure its longevity.
6. **Inertia and Responsiveness:** A wheel's rotational inertia impacts how quickly it can adapt to changes in water flow. Lower inertia designs may enable faster adaptation and energy capture, especially in variable water flow conditions like those encountered in natural river systems.
7. **Manufacturing's Role in Efficiency:** Even subtle imperfections in the manufacturing of water wheel buckets can disrupt water flow and increase energy losses. This highlights the need for meticulous design and manufacturing processes to maximize efficiency and minimize turbulence.
8. **Learning from History:** Historical water wheel designs often prioritized aesthetics over functional hydrodynamics. Modern engineers can learn from these past designs and apply advanced knowledge of fluid dynamics to develop more efficient water wheel designs that take full advantage of the available energy.
9. **CFD for Optimization:** The use of computational fluid dynamics (CFD) in the design process can provide crucial insights into how small changes in bucket shape can impact performance. This allows engineers to predict and optimize for greater efficiency before building a physical prototype.
10. **Aerodynamics: A Hidden Factor:** Surprisingly, the aerodynamics of water wheel buckets can be a significant factor in efficiency, even when the wheel is only partially submerged. Poorly designed buckets can lead to drag losses as high as 20%, emphasizing the need to consider aerodynamic aspects during design for overall performance improvements.
More Posts from patentreviewpro.com: