Analyzing Adhesive Joint Stress Distribution Key Factors for Optimal Performance in 2024
Analyzing Adhesive Joint Stress Distribution Key Factors for Optimal Performance in 2024 - Non-uniform stress distribution challenges in adhesive joints
The uneven distribution of stress within an adhesive joint is a major obstacle to its long-term performance. This unevenness creates concentrated areas of stress, potentially exceeding the adhesive's capacity and leading to early failure. Achieving a perfectly uniform distribution of stress is virtually impossible given the unpredictable nature of applied forces and environmental influences.
This challenge is further amplified by the geometry of the joint itself. Different shapes and sizes lead to distinct stress patterns, demanding careful consideration during design. Recent developments in bi-adhesive systems, however, offer potential solutions to mitigate these complexities. By combining different types of adhesives, these systems strive to achieve a more balanced stress distribution and enhance the overall structural integrity of the joint.
Adhesive joints are tricky because stress doesn't distribute evenly. This unevenness is a big deal because it can cause the joint to fail, even if the overall design seems strong.
Think of it like this: a small bump on a surface can cause stress to concentrate in one spot, making it more likely to break. This unevenness can be caused by a bunch of factors: the shape of the joint, how thick the adhesive is, or even how the materials are put together. It's also influenced by how the joint is used - like if it's constantly being flexed or exposed to heat.
The way the adhesive was made and cured can also play a big role. If the adhesive doesn't cure properly, it might not be as strong as expected, causing stress to distribute unevenly.
Even the way the surface is prepared can affect how stress is spread across the joint. A well-prepared surface might have a more predictable and even distribution of stress compared to a poorly prepared surface.
There's a lot we can do to understand how stress behaves in these joints, like using computer models to simulate how the force is distributed. But these models can only be as good as our knowledge of the material's properties and how it behaves under different conditions. It's not as simple as it seems!
So, while we can create great designs, the real challenge is ensuring that the stress is distributed evenly across the entire adhesive joint to maximize its performance and longevity.
Analyzing Adhesive Joint Stress Distribution Key Factors for Optimal Performance in 2024 - Impact of metal inserts on joint stress patterns
Metal inserts in adhesive joints can significantly change how stress is spread out, creating both opportunities and problems. While these inserts can boost a joint's ability to handle heavy loads and improve stability between the materials being joined, they can also cause stress to bunch up in specific areas where they connect with the adhesive. This localized stress build-up is something engineers need to keep a close eye on because it could cause the joint to fail unexpectedly.
Since every adhesive material behaves differently, and how the joint is shaped makes a big difference, it's crucial to study how these metal inserts work alongside the specific adhesive and joint design. Only then can we truly understand how they impact performance and ensure these joints hold up well in the real world.
Metal inserts are fascinating additions to adhesive joints because they can dramatically alter how stress is distributed. They act like tiny reinforcement points, potentially easing stress concentrations and strengthening the overall joint. However, they can also shift the way a joint fails. Instead of the adhesive itself giving way, the failure might occur within the adhesive itself or even within the materials it's bonding (the substrate).
The way the metal insert is shaped, its size and orientation, all have a huge impact on how stress responds. Think of a cylindrical insert versus a square one – they can completely change the way stress is dispersed. The metal's properties, like how it handles heat and pressure, also need to be considered as they can interact in surprising ways with the adhesive.
Even how the metal's surface is treated matters. Is it rough or smooth? Does it have a special coating? These details directly influence how well the adhesive sticks to it, which impacts the overall stress pattern and, in turn, the lifespan of the joint.
Computer models are incredibly useful in studying the effects of metal inserts, giving us a chance to see how we can strategically place them to minimize stress concentrations. It's all about precision in design. Different types of adhesives also respond in different ways to metal inserts. Some, like flexible adhesives, handle repetitive stress (dynamic loads) better than rigid ones, leading to a more localized stress-based failure.
While metal inserts can boost fatigue resistance, it's crucial to consider high-cycle fatigue conditions because the benefits might not always hold up under extreme stress repetition.
The challenge of truly understanding the interplay between adhesives and metal inserts is complex and requires a team effort. It demands knowledge from various fields like material science, structural engineering, and mechanical design to ensure that the joint will perform well under a wide range of conditions.
Analyzing Adhesive Joint Stress Distribution Key Factors for Optimal Performance in 2024 - Comparative analysis of single-lap vs double-lap joint performance
The way single-lap joints (SLJs) and double-lap joints (DLJs) handle stress and load is a crucial topic for engineers. While SLJs can sometimes perform as well as stepped-lap designs, especially when the overlap length is kept long, DLJs tend to distribute load more evenly. This is important because it helps reduce stress buildup in the adhesive layer. The type of adhesive you use, whether it's brittle or flexible, also plays a role. How the joint is designed also matters. These factors, plus how temperature and moisture affect the joint over time, make it essential to understand how both SLJs and DLJs fail and how strong they really are. In the end, choosing the right joint type directly affects how stress is spread out, so it's a key decision when designing for optimal performance in different applications.
Single-lap joints (SLJs) and double-lap joints (DLJs) are two common types of adhesive joints used in structural applications, and their performance differences are often a topic of debate. While both configurations rely on adhesives to bond materials, the way they distribute loads and manage stress varies considerably, leading to different failure mechanisms and suitability for specific applications.
One key distinction lies in load distribution. Double-lap joints tend to handle shear loads better due to their larger bonding surface area, effectively dispersing the stress more evenly. This can result in a lower stress concentration in the adhesive, potentially reducing the risk of premature failure.
However, SLJs often fail through adhesive failure, meaning the bond between the adhesive and the materials breaks, while DLJs tend to exhibit mixed-mode failure, where both adhesive and cohesive failures can occur depending on the material properties. This indicates that the way DLJs fail might be more complex, and we need to carefully analyze the entire joint system, not just the adhesive, to predict behavior.
The geometry of the joint also plays a role. SLJs have abrupt changes in geometry at the ends of the adhesive layer, which can lead to stress concentration points that could be detrimental to the joint's longevity. In contrast, DLJs offer a more continuous bonding surface, potentially reducing these stress concentrations.
Temperature can impact both types differently. The way the adhesive expands and contracts due to heat can vary between SLJs and DLJs, possibly affecting their performance under fluctuating temperatures.
The quality of the surface preparation is crucial in determining how well the adhesive bonds to the materials, and this factor can further exacerbate the performance differences between SLJs and DLJs. A well-prepared surface will promote a more even distribution of stress and ensure a strong bond.
Delamination, or the separation of the adhesive from the surface, is a concern for both, but it is more common in SLJs due to the exposed edges which are subjected to greater shear stresses. The greater coverage of adhesive in DLJs can mitigate this issue.
The choice of materials, particularly their compatibility, can be an important factor. DLJs often offer better compatibility with dissimilar materials, reducing the potential for issues caused by differential thermal expansion.
In addition, the thickness of the adhesive layer in a DLJ can be greater, which can help absorb more energy before failure occurs. This makes DLJs more resilient under high-impact loads.
Under dynamic loading conditions, where the force on the joint is constantly changing, DLJs have shown superior performance, suggesting that they may be better suited for applications where repeated impacts are expected.
Furthermore, in applications using composite materials, DLJs have consistently demonstrated superior performance in fatigue testing, indicating that they can better withstand long-term stress and wear, particularly critical in situations where durability is a primary concern.
Choosing the right type of adhesive joint requires a careful consideration of many factors, including the specific application, the materials being used, the load conditions, and the expected environmental factors. Each type offers unique advantages and disadvantages, and understanding these nuances can lead to more effective designs and longer-lasting structures.
Analyzing Adhesive Joint Stress Distribution Key Factors for Optimal Performance in 2024 - Shot peening effects on aluminum alloy adhesive joint load capacity
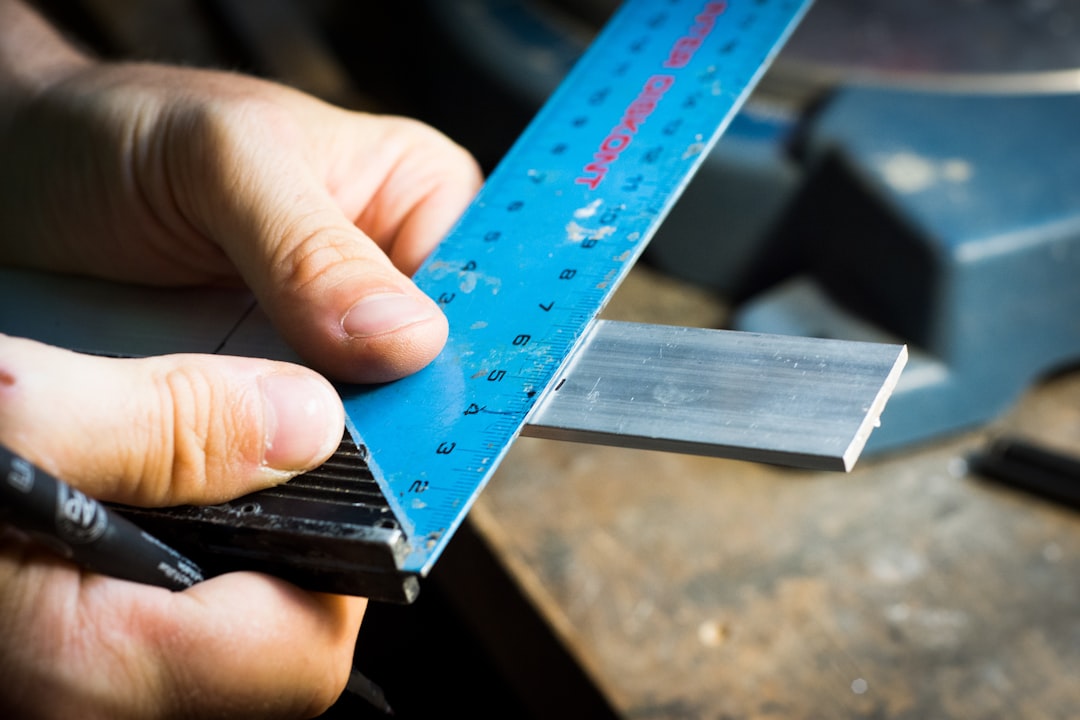
Shot peening, a process that involves bombarding a surface with small, hard particles, has become a potential tool to increase the strength of adhesive joints made from 2024T3 aluminum alloy. Studies have shown that manipulating the time spent shot peening and the size of the shot particles can dramatically change the load capacity of these joints. Interestingly, applying the shot peening process to the outer surfaces of the joint results in a marked improvement in strength. Research suggests that 120 seconds of shot peening using 1 mm diameter balls at a pressure of 0.5 MPa provides the best performance. The way shot peening affects surface roughness and load capacity has also been explored, indicating that meticulous surface preparation is crucial to get the most out of this technique. In essence, these discoveries help us better understand the mechanics of adhesive joints and point towards the importance of finding the perfect shot peening parameters for applications where load-bearing is paramount.
Shot peening, a process where tiny metal balls are blasted onto a surface to introduce compressive stresses, has proven to be a promising method for improving the performance of adhesive joints made with 2024 aluminum alloy. However, there's more to this technique than meets the eye.
The size of the shot used for peening significantly impacts its effectiveness. Smaller shots create a finer distribution of compressive stresses, leading to stronger adhesive joints, while larger shots can leave the surface rough, potentially hindering the adhesive's ability to bond properly. The depth and distribution of these compressive stresses can vary depending on the shot size and the amount of time spent peening, making it a crucial consideration.
Peening not only affects the metal itself but also alters the way the adhesive interacts with the surface. The resulting changes to the adhesive's microstructure can lead to increased shear strength or peeling resistance, but this isn't guaranteed. The specific adhesive used plays a vital role in determining how peening impacts performance.
Furthermore, the thickness of the adhesive layer also plays a role. Thin layers may not be able to effectively distribute the compressive stresses introduced by peening, limiting the overall improvement in joint strength. This makes optimizing the adhesive thickness alongside the peening process vital.
Shot peening can influence how joints fail. It can shift failure modes from cohesive failure, where the adhesive itself breaks, to adhesive failure, where the adhesive separates from the aluminum. This indicates that peening can help to strengthen the bond between the adhesive and the metal surface, but it's essential to understand how these shifts in failure modes impact the overall performance of the joint under various stress conditions.
The duration, intensity, and coverage of the peening process all affect the outcome, influencing not just the load capacity but also the longevity of the joint in diverse environments. A well-executed peening process can create micro-locking mechanisms at the adhesive interface, boosting load capacity. However, it's crucial to be cautious, as excessive peening can create a rough surface, leading to gaps and voids in the adhesive layer, potentially weakening the joint.
While shot peening can enhance the performance of aluminum alloy adhesive joints in many situations, it is not a one-size-fits-all solution. Carefully balancing the benefits of mechanical strengthening with optimal adhesive performance is critical for designing reliable adhesive joints. This calls for a thorough understanding of the specific alloy used, the chosen adhesive, and the environmental conditions the joint will face.
Combining shot peening with the use of bi-adhesive systems, where different adhesives are layered to distribute stress more evenly, may hold promise for improving the performance of high-stress applications, offering a potential pathway to overcome the limitations of traditional adhesive joints.
Overall, while shot peening is a powerful tool for enhancing the load capacity of aluminum adhesive joints, it demands a careful approach to optimization. A deeper understanding of the complexities of this technique, combined with rigorous testing, is necessary to fully unleash its potential in critical applications.
Analyzing Adhesive Joint Stress Distribution Key Factors for Optimal Performance in 2024 - Mathematical modeling advancements for predicting joint behavior
Mathematical modeling for predicting the behavior of adhesive joints is rapidly evolving. Cohesive zone modeling is emerging as a key technique, giving us a better grasp of how single-lap joints behave under tension and compression, and helping to predict their failure loads more reliably. Finite element analysis (FEA) is also playing a significant role, especially in dealing with complex shapes and helping us understand how stress is distributed in intricate joints. There's been a push to use semi-analytical models alongside FEA to improve our ability to predict joint strength, especially under cyclic loading, which remains a major challenge for long-term performance. These advancements hold immense promise for optimizing joint designs and mitigating common failure mechanisms in adhesive bonds across a wide range of applications.
Predicting the behavior of adhesive joints is a fascinating and ever-evolving challenge. While we've learned a lot about how stress distributes within these joints, the quest to accurately model their behavior continues. Recent advances in mathematical modeling offer new insights into these complex systems.
One area of progress is the refinement of Finite Element Analysis (FEA) tools. These powerful software programs allow us to simulate how adhesive joints behave under various conditions. These simulations provide a deeper understanding of stress distribution and help us predict how joints might fail, ultimately leading to better designs.
Another exciting development is the integration of machine learning algorithms into predictive models. By analyzing vast datasets of past performance, these algorithms can identify trends and patterns that might be missed by traditional methods. This allows us to refine predictions and make more informed decisions about joint design and material selection.
The way adhesive joints behave under dynamic loading is becoming more thoroughly understood. We're seeing significant progress in modeling how these joints respond to repeated stresses and strains, which is crucial for applications like vehicles and aircraft. These models are shedding light on the failure modes that are more likely to occur in real-world situations, providing valuable data for preventing premature failures.
One promising area of research explores the role of temperature fluctuations. These models are getting better at considering how variations in temperature can affect the properties of adhesives and ultimately the strength and stability of the joint. This is particularly important for applications where the joint might experience extreme temperatures, such as aerospace or automotive parts.
The viscosity of adhesive materials also plays a crucial role in stress distribution, and new models are now capable of analyzing how viscosity changes with temperature and time. This opens doors to more accurate predictions of how adhesive joints will behave in different environments.
And then there's the issue of nonlinearity. Adhesive materials often display non-linear behavior under stress, meaning they don't react in a straightforward way. Mathematical models are increasingly incorporating these complex non-linear responses, improving the accuracy of predictions and the reliability of designs.
Another crucial aspect is considering environmental factors, like humidity and exposure to chemicals. These factors can have a significant impact on the performance of adhesives and are now being incorporated into advanced modeling techniques. This helps ensure that predictions of joint behavior are more realistic and account for the real-world conditions.
With the rise of 3D printing, the way we design and manufacture adhesive joints is evolving. Mathematical models are being developed to understand how 3D-printed joints, with their unique geometries and potentially complex internal structures, affect stress distribution. This has the potential to lead to more efficient and reliable joint designs.
It's clear that the field of mathematical modeling for adhesive joints is continuously expanding, driven by the need to better understand these critical components. These new models are paving the way for more robust and durable adhesive joints that meet the challenges of complex and demanding applications.
More Posts from patentreviewpro.com: