World's Largest Ethanol-to-Jet Fuel Plant Inside Summit Next Gen's 250M Gallon SAF Facility Patent Implementation
World's Largest Ethanol-to-Jet Fuel Plant Inside Summit Next Gen's 250M Gallon SAF Facility Patent Implementation - ETJ Plant Construction Progress at Houston Ship Channel 60 Acre Site
The massive 60-acre site at the Houston Ship Channel is now the construction ground for what's being billed as the world's largest ethanol-to-jet fuel plant. Summit Next Gen, the driving force behind this venture, intends to produce around 250 million gallons of sustainable aviation fuel (SAF) per year, relying on Honeywell's Ethanol to Jet (ETJ) technology to convert ethanol into this alternative fuel. The chosen location provides an advantage by facilitating efficient transportation and supply chain access via existing marine, pipeline, and rail infrastructure, a key factor in ensuring the economic viability of the project. The hope is that this facility will create a new market for producers of low-carbon ethanol, offering them a path forward, while helping to address the aviation industry's struggle to meet environmental targets. A major step forward for this venture occurred on September 13th of this year, when the land acquisition was officially closed, solidifying Summit Next Gen's commitment to bring this ambitious project to life in the face of environmental concerns about aviation's carbon footprint. Whether this facility will truly deliver a significant environmental benefit remains to be seen. While the intent is admirable, the scale and complexities of implementing such a large-scale project might pose a challenge.
Summit Next Gen's ambitious project to build the world's largest ethanol-to-jet fuel (ETJ) plant at the 60-acre Houston Ship Channel site is progressing. The design aims to efficiently convert a substantial quantity of feedstock – roughly 250 million gallons annually – into SAF using novel chemical processes. It seems they're aiming for a flexible operation, capable of handling diverse feedstock options, including crop residues and energy crops, which could have implications for the local agricultural economy.
The plant's design incorporates a sophisticated distillation system to ensure the SAF produced meets industry standards. This is a crucial aspect of achieving a successful product and suggests they are striving for high-quality SAF. The integration of carbon capture technology, although not a new concept, is being positioned as a key aspect of the project, hinting at an effort to optimize the entire conversion process to reduce waste and enhance output.
The site itself was cleverly chosen with logistics in mind. Its proximity to existing transportation infrastructure – marine, pipelines, rail, and other connections – suggests they have considered the need for streamlined movement of materials to and from the plant, potentially minimizing potential logistical bottlenecks. The construction method appears to rely on modular components, an approach that often leads to faster build times and greater flexibility. The use of modular construction indicates a focus on getting the plant operational quickly.
Further, the site is well-equipped with extensive storage infrastructure, crucial for managing the large volumes of feedstock needed for a plant of this scale. This, in theory, ensures a continuous flow of raw material through the production process. And, unsurprisingly, they've incorporated modern safety protocols and monitoring systems into the construction and planned operation, acknowledging the risks associated with handling potentially hazardous materials.
The location in the Houston Ship Channel area is strategically selected not only for the logistics and infrastructure but also because the region has a significant chemical and energy industry presence. This raises a question of what existing relationships or shared knowledge might be involved in this project. Moreover, the project highlights the important role of collaboration between engineering teams and researchers. This collaborative effort suggests a commitment to refining the production process and implementing the most advanced available technology. It will be interesting to see the outcome of the project. The sustainability goals of the aviation industry are, however, quite challenging to achieve.
World's Largest Ethanol-to-Jet Fuel Plant Inside Summit Next Gen's 250M Gallon SAF Facility Patent Implementation - Honeywell Processing Technology Implementation for 250M Gallon Output

Honeywell's Ethanol to Jet (ETJ) technology is at the heart of Summit Next Gen's effort to build the world's largest ethanol-to-jet fuel plant, aiming for a 250 million gallon annual output. Located strategically near the Houston Ship Channel, the 60-acre facility leverages existing transportation infrastructure to streamline operations. This project hinges on Honeywell's ability to convert a variety of ethanol feedstocks, including corn-based and potentially even some bio-based sources, into a usable jet fuel. While the idea of reducing the environmental footprint of air travel through SAF is appealing, it's crucial to question whether this ambitious project can deliver on its promise. The scale of the operation introduces challenges, and whether this approach will truly contribute to the aviation industry's sustainability goals remains uncertain. The technical hurdles and logistical complexity of achieving such a large-scale output while meeting stringent quality standards need careful consideration. Ultimately, the industry and the public will be looking to see if this initiative provides a meaningful advancement in decarbonization efforts for the aviation sector.
Honeywell's Ethanol to Jet (ETJ) technology is at the core of Summit Next Gen's ambitious project to create the world's largest ethanol-to-jet fuel plant. The technology relies on catalytic hydrodeoxygenation, a complex series of chemical reactions that aims to efficiently convert ethanol into a sustainable aviation fuel (SAF) product. The use of modular construction is intriguing, as it could lead to a faster construction schedule and provide the flexibility to potentially expand the facility in the future, adapting to changing market demands. However, the sheer volume of ethanol required – potentially up to 1.5 billion gallons annually to produce 250 million gallons of SAF – is a staggering figure, highlighting the extensive agricultural and industrial investment needed to keep the plant running.
This plant emphasizes the importance of producing high-quality fuel. They've incorporated advanced distillation and purification processes designed to meet aviation fuel standards, which is critical for aircraft performance and safety. Notably, this facility has the potential to transform how we use agricultural byproducts. Its design allows for different ethanol sources, from crop residues to more conventional grains, hinting at a potential shift in resource utilization within the agricultural sector. Carbon capture technology is part of the design, and it will be interesting to see how it plays out in the grand scheme of the facility's CO2 output.
The location in the Houston Ship Channel area was likely chosen for a combination of factors, including its proximity to pipelines, marine terminals, and a well-established chemical and energy industry. This raises questions about how the project might tap into existing expertise and infrastructure within the region. Furthermore, the collaborative nature of this project – involving engineering teams and research institutions – is noteworthy. It emphasizes that developing and implementing large-scale ethanol-to-jet conversion technologies necessitates a multi-faceted approach, incorporating cutting-edge technology and ongoing research. Given the scale of this undertaking, thorough safety protocols and monitoring systems are clearly crucial, and the project design reflects a focus on these elements.
Finally, the sheer size of the project offers a chance for positive economic effects within the community. The construction and ongoing operation of such a plant would likely generate significant job opportunities, impacting local economies in areas like agriculture, energy, and transportation. The long-term viability and environmental impacts of this massive project remain to be seen, especially concerning the environmental impact of the necessary agricultural resources and the feasibility of the embedded carbon capture technologies. While the initiative addresses an urgent need in the aviation sector for more sustainable fuels, its success will rely on overcoming numerous technical, logistical, and economic challenges, and it will be fascinating to watch the project unfold in the coming years.
World's Largest Ethanol-to-Jet Fuel Plant Inside Summit Next Gen's 250M Gallon SAF Facility Patent Implementation - Marine Pipeline Rail Systems Integration for Ethanol Transport
The success of Summit Next Gen's large-scale ethanol-to-jet fuel plant hinges on a well-functioning transportation network. Their plan to utilize existing marine, pipeline, and rail systems for ethanol transport is central to the project's viability. This integrated approach is designed to keep costs down and ensure the consistent supply of ethanol needed to produce the ambitious target of 250 million gallons of sustainable aviation fuel annually. But seamlessly integrating these diverse transport modes will present its own set of operational challenges. Coordinating the flow of ethanol between ships, pipelines, and trains will require careful management to avoid bottlenecks and disruptions.
Beyond the logistical aspects, the project's reliance on various ethanol feedstock sources raises questions about the environmental consequences of increased agricultural production and resource use. While the facility aims to provide a new market for low-carbon ethanol producers, its full environmental impact remains to be seen.
Despite these challenges, the integration of marine, pipeline, and rail infrastructure is a crucial element in making large-scale sustainable aviation fuel production a reality. The future of this endeavor depends on overcoming the inherent complexity of coordinating these systems while also mitigating the broader environmental impacts of ethanol sourcing.
Summit Next Gen's plan for the world's largest ethanol-to-jet fuel facility in Houston highlights the importance of seamlessly integrating marine, pipeline, and rail systems for ethanol transport. This is a complex undertaking, as each transport method has its own operational quirks and maintenance needs. Successfully bringing them together will require meticulous planning and coordination.
One interesting aspect is the versatility of ethanol as a feedstock. The plant can potentially use a range of sources, from agricultural byproducts to energy crops. This flexibility is essential for ensuring a steady flow of ethanol, which is vital for achieving the plant's ambitious production goals of 250 million gallons of sustainable aviation fuel per year. However, meeting this goal would require a massive amount of ethanol – possibly as much as 1.5 billion gallons annually – which raises questions about feedstock availability and its impact on agricultural practices.
Of course, safety is paramount, especially when dealing with a flammable substance like ethanol. Pipelines and rail transport introduce specific safety considerations and regulations that must be diligently followed to minimize risks.
The establishment of this extensive ethanol transport network has the potential to create jobs in related industries, including agriculture and logistics. However, the project's long-term economic viability is dependent on a lot of factors, including market demand and the availability of ethanol. It's not clear how these things might change over time.
Each transportation mode offers unique benefits. Pipelines, for instance, are efficient for moving large volumes of liquid, while rail can navigate congested areas. Optimizing the use of these methods is crucial for minimizing transportation costs and maximizing overall efficiency.
To ensure the entire system runs smoothly, the different modes of transport must be able to interact seamlessly. That’s where innovative technologies and careful planning come into play. This interoperability will heavily impact how effective the overall supply chain will be.
However, the regulatory landscape can introduce complications. Marine, pipeline, and rail transportation are all heavily regulated, especially when dealing with hazardous materials like ethanol. This adds another layer of complexity to the project, as compliance with numerous regulations will require ongoing communication with regulatory agencies.
Emerging technologies can help improve safety and efficiency. Smart sensors and real-time data analysis in pipelines could provide immediate information about potential issues, which can help prevent leaks and disruptions. This shows how technological innovation can positively impact operations.
And we also need to consider the environmental aspects of the transportation processes themselves. While the plant is designed to produce sustainable jet fuel, the environmental impact of transporting the ethanol should be factored into the broader assessment of the project’s sustainability. Examining the carbon footprint of the entire transportation logistics is key.
In conclusion, while the Summit Next Gen project is focused on producing a more sustainable aviation fuel, it faces considerable challenges in the intricate integration of existing and planned infrastructure. The project's success relies on numerous elements, ranging from managing a massive feedstock supply to navigating complex regulations. Given these complexities, it's important to stay curious and to continue assessing all aspects of the project to fully understand the environmental and economic implications of such a large-scale endeavor.
World's Largest Ethanol-to-Jet Fuel Plant Inside Summit Next Gen's 250M Gallon SAF Facility Patent Implementation - Texas Deepwater Partners Land Acquisition Deal Structure
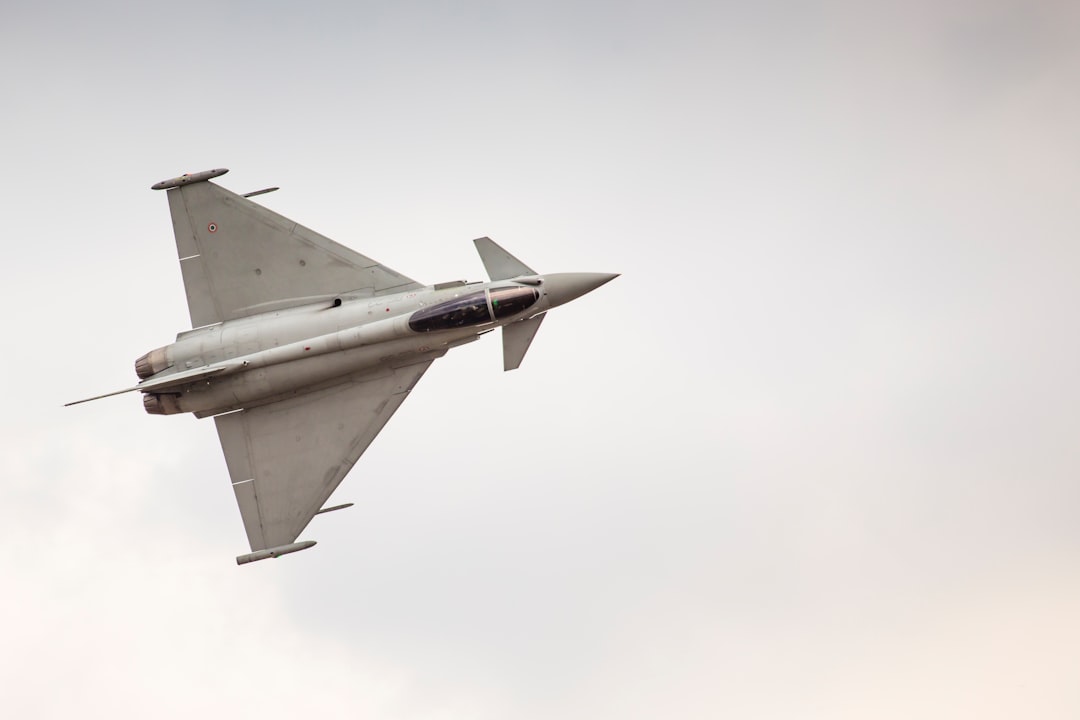
Summit Next Gen's pursuit of building the world's largest ethanol-to-jet fuel (ETJ) plant took a significant step forward with the acquisition of a 60-acre site from Texas Deepwater Partners. This deal, finalized in September 2024, places the future facility strategically along the Houston Ship Channel. The plan is to produce a substantial 250 million gallons of sustainable aviation fuel (SAF) each year, capitalizing on Honeywell's ETJ technology to convert ethanol into jet fuel. The exact financial terms of the land deal are not public knowledge. However, the location clearly prioritizes access to existing marine, pipeline, and rail infrastructure, potentially streamlining both the inflow of raw materials and the distribution of the finished product.
There's a clear ambition to lessen aviation's environmental burden through this project. However, its potential to meaningfully improve sustainability remains to be seen. The challenges of constructing and operating a plant of this scale, alongside questions about the overall ecological impact and the industry's ability to consistently provide enough low-carbon ethanol, are significant factors to consider. Success hinges on a combination of technological innovation, intricate logistical planning, and addressing regulatory concerns related to fuel production and environmental protection. While this is a noteworthy endeavor, it will be crucial to monitor how it addresses the hurdles inherent in both the technical and environmental aspects of decarbonizing the aviation industry.
Based on the publicly available information, the Texas Deepwater Partners land sale to Summit Next Gen appears to be more than just a simple property transaction. It likely involves a complex set of considerations, including navigating zoning regulations and federal oversight, typical of large industrial ventures in developed areas. The Houston Ship Channel site was undoubtedly chosen after meticulous examination of its logistics, including access to waterways for shipping, pipeline connections, and the availability of a skilled workforce, highlighting how critical strategic location is for industrial efficiency.
There are hints that Texas Deepwater Partners may be involved in improving the surrounding transportation infrastructure, potentially going beyond what's directly needed for the ethanol-to-jet facility. This raises questions about whether they see broader economic benefits for the region and could be a way to incentivize other businesses to set up shop nearby.
It's plausible that Summit Next Gen opted for a modular construction approach, where pre-fabricated components are assembled onsite. This can speed up construction timelines and possibly reduce overall project costs compared to conventional building methods. It's interesting to consider how this construction strategy was factored into the land deal itself.
The agreement could involve innovative legal frameworks that help foster collaboration between private entities like Summit Next Gen and local government agencies. This approach can be useful in navigating complex land acquisition processes, which are often riddled with bureaucratic hurdles. It's conceivable that financing for the project utilizes a blend of conventional and unconventional models, like public-private partnerships. Sharing the financial risk among different stakeholders could be critical to offsetting the large capital outlay needed for such a venture.
The nature of the plant also suggests a nuanced strategy for securing ethanol feedstock. They're likely aiming for flexibility to use various sources, from specially cultivated crops to agricultural byproducts. This adaptability in their supply chain is probably crucial for maintaining a steady supply of ethanol.
Further adding a layer of complexity, the land deal may be tied to future carbon capture projects. This could potentially lead to new income opportunities or access to regulatory incentives for the facility. How the operational landscape is influenced by carbon capture is an intriguing aspect of this project.
Community engagement initiatives are another possibility. Given the project's size and potential impact on the local community, it's reasonable to assume that Summit Next Gen has considered establishing proactive communication and engagement programs to address concerns and maintain public trust.
Finally, the land acquisition agreement probably anticipates future expansions and technological improvements. This longer-term vision goes beyond the immediate needs of the facility and reflects the expectation that the aviation fuel market and related technologies will evolve over time. This foresight is notable in a project of this scale.
While the specific details of the land transaction are not public, examining the broader context reveals many facets that shape this significant project. The intertwining of complex logistics, infrastructure, financing, and social responsibility adds several layers to the simple act of buying land. It will be fascinating to observe how these considerations affect the development and ultimate success of the world's largest ethanol-to-jet facility.
World's Largest Ethanol-to-Jet Fuel Plant Inside Summit Next Gen's 250M Gallon SAF Facility Patent Implementation - US Gulf Coast Aviation Fuel Production Infrastructure Plans
The US Gulf Coast is experiencing a surge in initiatives aimed at bolstering aviation fuel production infrastructure, with Summit Next Gen's planned ethanol-to-jet fuel facility being a prime example. Situated near the Houston Ship Channel, this large-scale project aims to produce 250 million gallons of sustainable aviation fuel (SAF) yearly. The core technology focuses on converting low-carbon ethanol into a usable jet fuel alternative. The project's success, however, is closely tied to how well it integrates existing transportation infrastructure, including marine, pipelines, and rail systems, to ensure the consistent supply of ethanol needed for operations.
While the project's intentions are focused on addressing environmental concerns within the aviation industry, it also brings to the forefront important questions about the feasibility of such a massive endeavor. Can large-scale agricultural production be maintained in a truly sustainable manner to feed this facility? Will the complexities of coordinating transportation and managing regulatory hurdles prove too challenging? Despite being a promising development, there is still uncertainty as to whether it will usher in a significant shift towards a more sustainable future for the aviation fuel sector.
The US Gulf Coast's existing infrastructure is playing a crucial role in the plans for Summit Next Gen's SAF facility. A key advantage is the region's extensive pipeline network, which connects to a large portion of US ethanol production. This close proximity greatly simplifies the task of reliably supplying ethanol to the plant, representing a strong foundation for its operations.
The chosen location along the Houston Ship Channel is also ideal for maritime transport. Ethanol can arrive via ship, offering the benefit of high-volume deliveries. This strategy potentially reduces transportation costs compared to trucking or rail, which can become a significant expense for such a large-scale project.
The Gulf Coast states, specifically Texas, boast significant ethanol production capacity, with numerous existing facilities. This local ecosystem of ethanol producers offers a diverse and potentially robust supply of feedstock for the Summit Next Gen facility. However, the potential for this kind of localized ethanol production to ramp up to the massive scale needed for the project is a big question.
While the integration of marine, pipeline, and rail transportation offers a robust logistical approach, it also introduces complexities. Each mode of transport comes with its own safety regulations and operational protocols, necessitating meticulous coordination to avoid potential disruptions in the supply chain.
With the flammable nature of the raw materials involved, the plant will likely integrate advanced safety measures. This could involve automated safety systems and real-time monitoring to quickly react to any leaks or transportation mishaps. Implementing these kind of response systems in the various transport modalities will be a challenge in its own right.
This massive project is expected to generate a considerable number of jobs in the region during construction and ongoing operations. This represents a major economic boon for the area. However, it's important to consider the potential strain on local infrastructure and labor markets. Effective planning will be essential to manage this anticipated influx of activity.
The facility's design utilizes modular construction, making it possible to expand in stages. This flexible approach makes it easier to adapt to changing market conditions and allows the facility to respond to future fluctuations in SAF demand. This future-proofing is especially important with a brand-new industry.
Producing 250 million gallons of SAF annually requires a vast amount of ethanol, roughly 1.5 billion gallons. Meeting this demand presents a significant challenge, requiring the facility to develop extensive relationships with ethanol producers and possibly agricultural producers to secure reliable supplies. Whether those supply lines can be created and maintained is a big unanswered question.
Modern information technology plays a crucial role in optimizing this entire operation. Smart logistics and real-time data analytics are essential for tracking and managing inventory, transportation metrics, and ensuring efficiency throughout the supply chain.
The project is likely to foster collaborations with universities and research centers in the area. This collaboration could lead to groundbreaking advances in SAF production processes and help create a well-trained workforce in the field of biofuel technology. The need to continue innovation is important since many parts of the process are relatively untested at the scale that Summit Next Gen envisions.
It will be interesting to observe how the facility integrates these complex transportation systems and whether the challenges posed by scale and complexity are overcome. The success of the project depends heavily on these interrelationships.
More Posts from patentreviewpro.com: