Vulcan Spring's Innovative Constant Force Springs Applications and Advancements in 2024
Vulcan Spring's Innovative Constant Force Springs Applications and Advancements in 2024 - Vulcan Spring's Custom Constant Force Solutions Meet Complex Application Demands
Vulcan Spring's expertise lies in crafting custom constant force springs that are specifically designed to tackle the intricate demands of diverse applications. Their "Conforce" springs are notable for their consistent force output across their entire extension range, which makes them a strong choice for a variety of uses, including medical devices and retail displays. Their design process incorporates advanced tooling and machinery to quickly review custom designs and transition them to high-volume production runs. Vulcan Spring's approach is to align spring designs precisely with the specifications of each application, seeking efficiency in material utilization while ensuring performance standards are met. This focus on customized solutions speaks to their dedication to addressing the unique challenges across various industries, making their spring designs efficient and effective. As 2024 progresses, Vulcan Spring remains at the forefront of spring technology, expertly navigating the complexities of contemporary engineering requirements.
Vulcan Spring's expertise lies in crafting bespoke constant force springs, often called "Conforce," to meet the diverse demands of various applications. They've built a global reputation for both designing and producing these springs at scale, utilizing specialized machinery and tooling. Their strength lies in rapidly reviewing customer designs and translating them into high-volume production runs of precisely functioning springs.
It's interesting how these springs maintain a consistent force across their entire extension range. Unlike standard springs whose force varies with extension, this constant force is particularly valuable for uses like displays in retail settings or within manufacturing processes. Their focus extends beyond general applications, as they've also delved into medical device manufacturing, producing springs for everything from surgical instruments to MRI equipment.
One of the intriguing aspects is their claim of higher force output per unit weight of material, making them energy-efficient in applications requiring linear or rotational movements. A noteworthy example of their specialization is the creation of motor brush springs, critical components in power tools, power generators, rail transit, and even wind turbines. This demonstrates their ability to target specific applications, taking into account factors such as fatigue life and overall size optimization to avoid unnecessary cost and premature failures.
Having been in the game since 1967, Vulcan Spring has become a go-to partner for industries needing custom spring solutions. The fact that they continue to meet the demands of various market sectors implies they're adaptable, able to tackle challenges through creative approaches. This sustained success seems to suggest they're continually evolving and pushing the boundaries of constant force spring technologies. Whether it's meeting strict material requirements or figuring out a solution for a challenging design constraint, it appears they're meeting those demands.
Vulcan Spring's Innovative Constant Force Springs Applications and Advancements in 2024 - Conforce Springs Deliver Consistent Force in Compact Designs
Vulcan Spring's Conforce springs are designed to provide consistent force within a compact package, a feat achieved through innovative design and manufacturing processes. This ability to deliver steady force throughout their extension range is particularly useful for applications where consistent performance is crucial, like in industrial automation or intricate aerospace components.
The compact size of these springs is made possible through their construction, which allows for a high number of coils within a smaller space. Furthermore, Vulcan Spring offers a choice between two mounting configurations: tandem and laminar. Each configuration is designed to optimize force and footprint for a specific application.
The ability of these springs to hold energy indefinitely when extended makes them incredibly versatile. This characteristic allows them to be employed in a diverse range of applications, from point-of-sale displays that require constant tension to medical devices that need controlled and consistent force delivery.
Whether it's maintaining constant torque or delivering variable torque gradients, Conforce springs demonstrate the advancement in constant force spring technologies. However, it remains to be seen if this design maintains its efficiency across all applications and whether their current options truly maximize force/size ratios in all conditions. Nonetheless, Vulcan Spring seems to be investing in making these springs suitable for an expanding range of demanding requirements across various industries.
Conforce springs are designed to produce a consistently high force output within incredibly compact packages. This is particularly useful for scenarios where available space is extremely limited, such as in some medical devices. While traditional springs often have a nonlinear force response as they extend or compress, the Conforce design attempts to achieve a truly constant force delivery over their entire range of motion. This aspect of consistent force makes them a good choice for situations requiring precise and predictable force, though it remains to be seen how well they perform in real-world applications when compared to their specifications.
One intriguing point is the claim of higher force output relative to the weight of the material. If true, this means potentially lighter and more compact designs without sacrificing performance. It will be interesting to see how this characteristic performs during actual use, particularly in applications where fatigue resistance is a concern. The longevity of these springs seems to be tied to their construction and material choices, though more data is needed on this point. While currently finding niche markets like medical devices and automotive engineering – where controlling precise torque is essential, such as in certain hatchback designs – one wonders how broadly these springs can be adapted.
The springs appear customizable, allowing engineers to control many operational factors, including the specific force profile and extension range, a potentially beneficial design feature. The option for specialized coatings is also notable, potentially enhancing the lifespan in extreme environments where corrosion or friction resistance is important. One might wonder how widely available these options are and if it increases the cost or complexity of the production process. The use of automation and robotics in manufacturing suggests a potential for higher quality control and manufacturing consistency while potentially reducing manufacturing time. However, the effectiveness of this automation will need to be assessed, as it's crucial to ensure the production process continues to meet high standards of quality control and does not create unforeseen issues. It is also noteworthy that these springs show promise for stability across varying temperatures, making them potentially useful in harsh environmental conditions. Whether this stability translates to other potential stressors, like pressure or humidity, remains a question. Lastly, the fact that Vulcan's Conforce springs have found traction in various markets around the world – from Europe's medical sector to Asian industries – indicates their possible versatility and ability to adapt to diverse environments. One wonders whether any challenges have arisen from the adaptation to different manufacturing standards and environmental variations in each geographic region.
Vulcan Spring's Innovative Constant Force Springs Applications and Advancements in 2024 - Material Selection and Force Requirements Key to Optimizing Spring Performance
The performance of constant force springs hinges on meticulous material selection and precise force requirements, particularly in applications demanding high precision and reliability. Achieving optimal spring performance necessitates careful consideration of material properties, especially their ability to withstand various environmental factors, including extreme temperatures, to maximize their lifespan. It's not just the spring's shape that matters; the design process must incorporate accurate force output calculations and appropriate prestressing techniques to ensure the spring delivers consistent performance across its entire extension range. As we move deeper into 2024, comprehending how these factors impact spring behavior becomes increasingly crucial for meeting the diverse demands across different industries. However, challenges remain. The actual performance of these springs under real-world operating conditions – particularly when it comes to material fatigue and their ability to adapt to different environments – requires more investigation to fully understand their limitations and capabilities. Until these questions are thoroughly answered, their widespread adoption in complex applications will continue to be scrutinized.
The performance of constant force springs hinges heavily on the materials used in their construction. Higher-performance materials like specific steel alloys or high-carbon steel can dramatically improve fatigue life, potentially extending their service life by a significant margin compared to standard spring materials. It's intriguing to consider the differences in lifespan under similar conditions and if these materials can truly deliver on this promise.
The consistent force these springs deliver across their entire extension is a result of the meticulous design of their coil geometry. Each coil interacts in a specific way, resulting in a steady force output, a stark contrast to the variable force characteristics of traditional springs. However, a question remains as to how this design consistency is maintained in variable operational conditions.
Design and material choices are optimized through sophisticated manufacturing processes like computer simulation and 3D modeling. These advancements make prototyping faster and allow for better performance predictions before actual production, potentially avoiding costly design revisions. However, the accuracy of the predictive models compared to real-world performance is a factor that bears scrutiny.
The compact designs not only save space but also lead to a significant reduction in the amount of material needed, leading to reduced weight. While a 30% weight reduction compared to traditional springs is claimed, verifying this reduction in real-world applications would be beneficial. While the potential for lighter and smaller designs is evident, it's important to understand the limits of these benefits and the trade-offs associated with them.
A core concept in the application of these springs is "mechanical advantage." They're engineered to maximize output force while minimizing input load, particularly valuable in applications with size and weight constraints. This aspect seems quite promising for specific use cases but remains to be seen if it holds true across a wider range of applications with diverse demands.
Interestingly, engineers can tailor the force delivery rate through precise adjustments to the design parameters. Factors like the ribbon material's thickness or the number of coils can be modified, creating virtually endless customization possibilities. This high degree of flexibility allows them to meet very specific engineering challenges, though the complexity of design and manufacturing can potentially become a concern.
Constant force springs are frequently used in dynamic applications, demonstrating their ability to withstand repeated extension and contraction without significant performance degradation. Reports of over a million cycles under continuous use suggest excellent reliability. This would seem to be a strong feature for many applications but raises questions about durability in harsh or highly specialized applications.
Temperature variations can affect the performance of springs. However, Vulcan's constant force springs are designed to perform across a range of temperatures, with some materials suitable for environments ranging from -40°C to +70°C. While this range is impressive for many applications, it's important to assess if they hold up under extreme temperatures and fluctuations in ways not tested thus far.
The use of advanced coatings like PTFE or zinc nickel can significantly enhance performance in challenging environments, especially when considering wear and corrosion resistance. This adaptability seems key for extending the lifespan of springs, but the choice of coating and its impact on other performance characteristics would need to be considered.
Various industries are recognizing the benefits of utilizing constant force springs in applications ranging from aerospace to healthcare. Their implementation in these industries highlights the drive to incorporate compact and lightweight solutions without compromising performance or reliability. The extent to which these springs are readily adaptable to the unique demands of diverse industries is a topic that requires further exploration.
Vulcan Spring's Innovative Constant Force Springs Applications and Advancements in 2024 - Constant Force Spring Market Projects Growth Through 2031
The market for constant force springs is projected to expand significantly in the US through 2031. This growth is being fueled by ongoing technological improvements and the rising need for these springs in a wide range of industries. Vulcan Spring's advancements, especially their Conforce line of constant force springs, are contributing to this trend. Conforce springs deliver reliable, consistent force output in a compact form, making them a desirable choice for sectors like medical device production and aerospace engineering. They are designed to provide a substantial force within a small space, which can be advantageous in scenarios where space and weight are at a premium. However, moving forward, the emphasis will be on optimizing the materials and manufacturing processes to ensure that these springs operate reliably across a variety of demanding conditions. There is still some uncertainty surrounding the limitations of these springs, and it remains to be seen how well they hold up in specific challenging applications. If manufacturers can continue to refine spring design and improve manufacturing efficiency, the constant force spring sector seems poised to grow even further and potentially reshape how engineers approach specific design problems in various sectors.
The market for constant force springs is projected to experience substantial growth through 2031, driven by a rising demand across diverse sectors like medical devices and automated systems. This signals a shift beyond their traditional applications.
Constant force springs work differently than conventional springs. They are designed to provide a consistent force output throughout their entire extension range, unlike conventional springs whose force varies. This constant force characteristic is crucial in applications that demand precise responses.
Research suggests that constant force springs can outperform traditional spring designs by achieving up to a 30% weight reduction while maintaining, or even improving, their force output. This potential for more compact and efficient designs has opened up exciting possibilities across various technologies.
Vulcan Spring's "Conforce" technology is interesting due to its ability to withstand dynamic environments. Some variations of their springs are designed to endure over a million cycles of extension and contraction. This kind of resilience indicates a potential for reliability in high-demand applications.
The design of the coil geometry in constant force springs enables the creation of customized force profiles, allowing for a wide range of optimization opportunities. However, this customization capability also raises concerns about design complexity and potential for errors during the customization process.
The choice of materials is a critical factor, as higher-performance options like specialized steel alloys can significantly improve the fatigue life of these springs. In fact, depending on the conditions, they could potentially extend the spring's lifespan by a considerable amount compared to those made with standard materials.
The use of advanced coatings, like PTFE or zinc nickel, offers the possibility of improved performance in demanding environments. These coatings enhance wear resistance. However, it's essential to carefully consider the potential trade-offs in terms of manufacturing processes and cost.
Unlike conventional springs that can experience fatigue under continuous load, constant force springs seem to maintain a consistent performance under repeated stress. This design characteristic makes them attractive for industries like aerospace and automotive.
The growth trajectory of this market emphasizes a greater focus on optimizing force-to-size ratios. Engineers are exploring the balance between compact designs and the necessary mechanical advantage for diverse applications. This drive has led to innovations in spring design and the materials used to create them.
Vulcan Spring utilizes advanced manufacturing technologies, including computer simulations and 3D modeling, to boost production efficiency. These tools help accelerate the prototyping process and create more accurate performance predictions. However, it's crucial to ensure that these simulated results accurately represent real-world performance for quality control.
Vulcan Spring's Innovative Constant Force Springs Applications and Advancements in 2024 - Improved Firearm Magazine Performance with Constant Force Technology
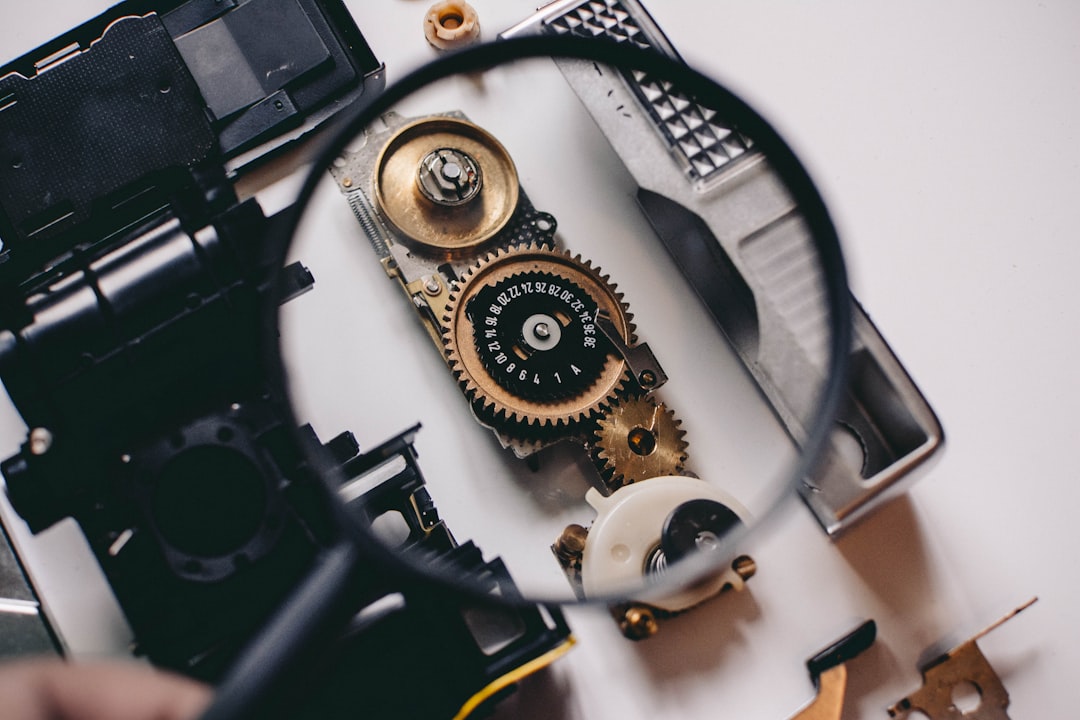
Vulcan Spring's constant force technology, particularly their "Conforce" springs, is making waves in firearm magazine design. By using constant force springs instead of traditional compression springs, firearm magazines can offer a more consistent loading experience. Unlike traditional springs whose resistance increases as the magazine fills, constant force springs provide a steady force throughout their extension. This translates to easier loading and potentially smoother operation of the magazine.
Additionally, these springs boast an extended lifespan compared to their traditional counterparts. The consistent force and reduced stress on the material can lead to higher cycle life, making them more dependable for use in demanding situations. This improved dependability is a significant potential benefit for firearm owners and manufacturers. The adoption of this technology indicates a notable shift in firearm design practices, particularly towards solutions that enhance usability and address the limitations of older spring designs.
However, it's important to consider that the performance claims of constant force springs need to be fully verified in the field. Their performance across varying environmental factors, use conditions, and ammunition types requires further evaluation to determine the full extent of the benefits they offer to the various types of firearm applications. While this technology shows promise, further testing and real-world data are necessary before a definitive assessment of its impact on firearm performance can be made.
Constant force springs offer a distinct advantage over traditional compression springs in firearm magazine design, primarily due to their ability to deliver a consistent force throughout the entire loading process. Unlike traditional springs, whose resistance increases as more rounds are loaded, constant force springs maintain a uniform force, which contributes to a more reliable and predictable feeding mechanism. This consistent force output is particularly beneficial for ensuring smooth feeding of ammunition under diverse conditions.
One of the intriguing aspects of this technology is the potential for weight reduction. Manufacturers report achieving up to a 30% decrease in magazine weight by incorporating constant force springs, which can make firearms more comfortable to handle and carry, particularly for users who may be physically challenged or for designs where a lighter package is preferred. It will be important to carefully consider if this weight savings actually leads to improvements in handling and how it impacts the overall balance and stability of the firearm.
Durability is a crucial factor in firearm design, and constant force springs show promise in this area. Reports indicate they can endure over a million cycles of extension and compression without a noticeable reduction in performance. This high cycle life makes them particularly suitable for firearms that are subjected to repeated firing and high stress environments. However, it's important to note that the true impact of the operating environment and any potential for premature failure due to repeated loading and unloading should be better understood in future research.
Another point of interest is the ability of constant force springs to operate within a broader range of temperatures compared to traditional springs. Some of these springs are designed to function effectively from -40°C to +70°C, making them less susceptible to performance degradation caused by changes in environmental conditions. Though, we should consider the impact of fluctuating temperatures on the performance of the springs over time and across a range of uses. While the stated range suggests greater adaptability to diverse environments, more rigorous testing may be needed to confidently validate the reliability of these springs under extremely fluctuating temperatures.
The materials used in these springs also contribute to their performance. Engineers are now able to employ higher-performance alloys like certain steel varieties that enhance fatigue resistance. This translates into a potential for longer service life of firearm magazines, potentially reducing the need for maintenance or replacement. While it's promising to see an emphasis on longer life, the long-term effects of these alloys on the lifespan of the spring should be further studied to determine if they actually meet the extended lifespan that's hoped for.
Furthermore, the inherent design of constant force springs offers the opportunity to fine-tune the force profile. Engineers can now adjust factors such as the material thickness or the number of coils to precisely match the needs of a particular firearm and ammunition type. This customization flexibility allows for optimization of the feeding process based on specific operational needs. The challenge becomes managing the design and manufacturing complexity that comes with customizing these spring types.
Due to their design, constant force springs can be packed into a smaller space. This compact design capability allows firearm designers to incorporate more coils within a confined space, which is particularly useful in firearms where space is limited, such as in concealed carry handguns. However, we must determine if there are design constraints that lead to a trade-off between size and performance and how those design changes impact the function of the magazine.
One of the claims related to this technology is that it increases the efficiency of semi-automatic firearm systems. The consistent force output leads to less energy loss in the feeding cycle, resulting in faster rates of fire. This enhanced efficiency may translate to a performance advantage under certain circumstances. However, it remains to be seen how much of a real-world impact this efficiency improvement truly has on the performance of the firearm.
It's also noteworthy that these springs are often treated with advanced coatings such as PTFE to enhance wear and corrosion resistance. This is particularly beneficial in harsh operating environments where the weapon may be subjected to dirt, moisture, or other factors that can degrade spring performance over time. It will be important to explore how these coatings affect the performance of the springs, if it introduces any other limitations, and to determine if the application of those coatings impacts the efficiency or the lifespan of the spring.
Lastly, the concept of mechanical advantage is often discussed in relation to constant force spring design. These springs are engineered to maximize output force while minimizing input load. This aspect is particularly helpful for high-capacity magazines that need to rapidly deliver rounds during firing. However, further exploration into how this design element impacts a range of magazine configurations and ammunition types is needed for engineers to fully understand the implications of that feature.
In summary, constant force spring technology shows significant promise for enhancing firearm magazine performance across a range of characteristics. The consistency of force, weight reduction, longevity, temperature resilience, material innovations, customized force profiles, compact design, enhanced efficiency, coating options, and mechanical advantage all point to potential improvements in firearms. However, more in-depth research is needed to fully assess the performance of these springs in a variety of environments and under diverse operating conditions.
Vulcan Spring's Innovative Constant Force Springs Applications and Advancements in 2024 - Contorque Springs Enhance Smooth Operation in Window Shade Applications
Contorque springs are proving to be increasingly important in window shade systems, offering a path towards smoother operation. Their unique design enables consistent torque delivery in a compact form factor, particularly beneficial in space-constrained applications. This characteristic makes them well-suited for modern window shade systems, including cordless options, where smooth and reliable winding/retracting is crucial. Notably, Contorque springs can maintain a constant force even with multiple turns, potentially improving efficiency and offering a less complex alternative to motor-driven solutions. The future holds promise for exploring further applications of these springs, with the potential for advancements in various design and engineering areas beyond window shades. However, it is unclear how these springs would perform in more demanding conditions like extreme weather and if they truly provide a cost-effective solution. There is still much to learn about the versatility and longevity of Contorque springs before they become widely adopted.
Contorque springs, with their ability to produce a constant, rotational force throughout their entire operational range, offer a compelling solution for creating smooth and consistent movement in window shade applications. This consistent force eliminates the jerky movements often seen in systems using traditional springs, resulting in a more refined and aesthetically pleasing operation.
The design of contorque springs allows for a remarkably compact size, packing a high number of coils into a smaller space while still generating a significant torque. This compact nature is particularly advantageous for window shades where space is at a premium and a consistent force is essential for proper functionality. One wonders how this compact design affects the overall structural integrity and if it introduces any limitations in terms of durability or overall force output when compared to larger spring configurations.
These springs also exhibit a notable reduction in energy loss during operation, a welcome trait in automated window systems where minimizing energy usage is critical for optimal actuator lifespan and energy efficiency. The question of whether this energy efficiency extends to a wider range of conditions and shade configurations remains, as does the long-term impact on the spring's lifespan.
Moreover, contorque springs are built for extended durability. The consistent force output across their operational range reduces the stress accumulation that typically leads to fatigue in conventional springs. This enhanced durability can result in reduced maintenance needs and better reliability for the window shade systems, potentially increasing their overall lifespan. It will be interesting to see data over the long-term on the wear and tear in actual field use to understand the full impact of this durability in real-world operating conditions.
Additionally, their smooth operation minimizes friction. This is beneficial for reducing noise and wear within the window shade system. Keeping noise levels low is often a priority for those installing interior window coverings, and minimized wear on other components within the shade can lead to longer component lifespans. While the minimization of friction seems like a positive attribute, it's important to consider whether this minimization of friction affects the overall safety or stability of the shade mechanisms.
The ability to withstand a broad range of temperatures, from -40°C to +70°C, is a significant advantage, especially when considering both indoor and outdoor applications. This range of operation demonstrates their versatility in varying environments, potentially increasing the adoption of contorque springs for a greater range of window coverings. However, the performance characteristics of the springs at the very limits of these temperature ranges should be carefully documented for a full understanding of their capabilities and limitations.
Another crucial aspect is the ability to customize torque profiles. Engineers can adjust parameters like the number of coils or material thickness to achieve precise control over torque delivery. This flexibility enables tailored solutions for window shades of various sizes and materials. The feasibility of designing springs with such specific requirements for custom designs is intriguing, and the question arises as to how adaptable the design and manufacturing process is to different torque needs.
Contorque springs can be treated with specialized coatings that enhance their ability to withstand moisture, dust, and corrosion. This added layer of protection is especially useful for outdoor installations where exposure to the elements is unavoidable. The long-term effectiveness and any potential trade-offs of these coatings (like impacts on overall flexibility or spring performance) need to be carefully examined.
Furthermore, the inherent design of these springs potentially simplifies the installation process for automated window shade systems. This could lead to reductions in labor costs and installation time, ultimately impacting the economics of implementing such automated systems. The question of whether this easier installation leads to any compromise in functionality or potential long-term stability and reliability needs further scrutiny.
Finally, these springs can maintain reliable force delivery even in highly demanding environments where traditional springs might fail or fatigue. This high degree of reliability is critical in applications where window shades are frequently adjusted, such as in spaces that experience changing light conditions throughout the day. It's still unclear how these springs would behave in extremely high-stress scenarios where cycles per hour or force output are maximized, and this needs further investigation.
In conclusion, contorque springs represent a promising development for window shade applications. Their ability to generate constant torque, operate in compact designs, minimize energy loss, extend durability, and offer customization capabilities suggests they have a place in improving the performance of window shade systems. However, a closer examination of their performance in diverse real-world applications and across a wider range of operating conditions is necessary for a more comprehensive understanding of their full capabilities and limitations.
More Posts from patentreviewpro.com: