Silicon in Construction Technical Limitations and Material Science Challenges of Bulk Applications
Silicon in Construction Technical Limitations and Material Science Challenges of Bulk Applications - Structural Limitations of Silicon Crystals in Load Bearing Applications
Silicon's suitability for load-bearing applications in construction is severely restricted by fundamental structural limitations. While silicon excels in microelectronics due to its electronic properties, its inherent material properties, especially the relatively weak Si-Si bonds, pose significant challenges. Compared to materials like polycrystalline diamond, silicon exhibits a considerably lower capacity to withstand stress before fracturing. This brittleness, coupled with its high stiffness and limited plasticity, makes it unsuitable for structures subjected to substantial loads. Furthermore, imperfections during crystal growth, such as the formation of growth ridges, can compromise the overall structural integrity and uniformity of the material. This inherent fragility and vulnerability to flaws make silicon an impractical choice for applications demanding high mechanical resilience. Consequently, researchers are exploring alternative materials like tough hydrogels and bio-inspired designs to address the limitations of silicon and develop more robust and durable solutions for structural applications in engineering and construction.
Silicon crystals display a pronounced directional dependence in their mechanical behavior, meaning their strength varies greatly depending on the direction of the applied force. This anisotropy can lead to unforeseen failures in load-bearing applications, especially where a uniform stress distribution is a key design assumption.
Silicon's inherently brittle nature, particularly at ambient temperatures, hinders its ability to withstand stress through plastic deformation. As a result, it's prone to sudden and catastrophic failures rather than gradually yielding under load, a concerning factor for any structural application where resilience is vital.
Silicon's relatively low toughness is a key limitation when considering its role in load-bearing structures. Its toughness falls short of traditional construction materials such as steel or concrete, making it less suitable for supporting significant loads in most engineering applications.
Exposure to alkaline environments can lead to alkali corrosion and subsequent degradation of silicon's performance. This susceptibility requires careful consideration of material protection methods to mitigate potential stress-related failures over time.
The formation of microscopic cracks during crystal growth can significantly impact the mechanical integrity of silicon. These flaws act as stress concentrators when under load, often leading to premature failure in structural applications, highlighting the importance of material quality control.
While silicon possesses high thermal conductivity, this property also presents a challenge. Rapid fluctuations in temperature can cause damaging thermal stresses within the crystal structure, posing a risk in environments with large temperature swings.
The temperature at which silicon transitions from brittle to ductile behavior is relatively high. In scenarios involving heat generation, such as frictional forces, silicon's strength unexpectedly weakens, complicating its use in load-bearing roles where elevated temperatures are possible.
The presence of even trace impurities within the silicon crystal lattice can considerably affect its mechanical properties. These impurities lead to variability in load-bearing capacity, making it challenging to consistently select and utilize silicon in structural applications.
The size of silicon crystals is directly linked to their mechanical properties. Larger crystals can amplify existing flaws, leading to reduced structural integrity in construction compared to smaller, more precisely controlled crystal sizes.
While composite materials incorporating polymers have been proposed to enhance silicon's load-bearing potential, the interfaces within these hybrid materials remain a complex issue. There are questions surrounding the long-term durability and ability of these composites to sustain loading forces.
Silicon in Construction Technical Limitations and Material Science Challenges of Bulk Applications - Temperature Constraints of Silicon Materials in Construction Projects
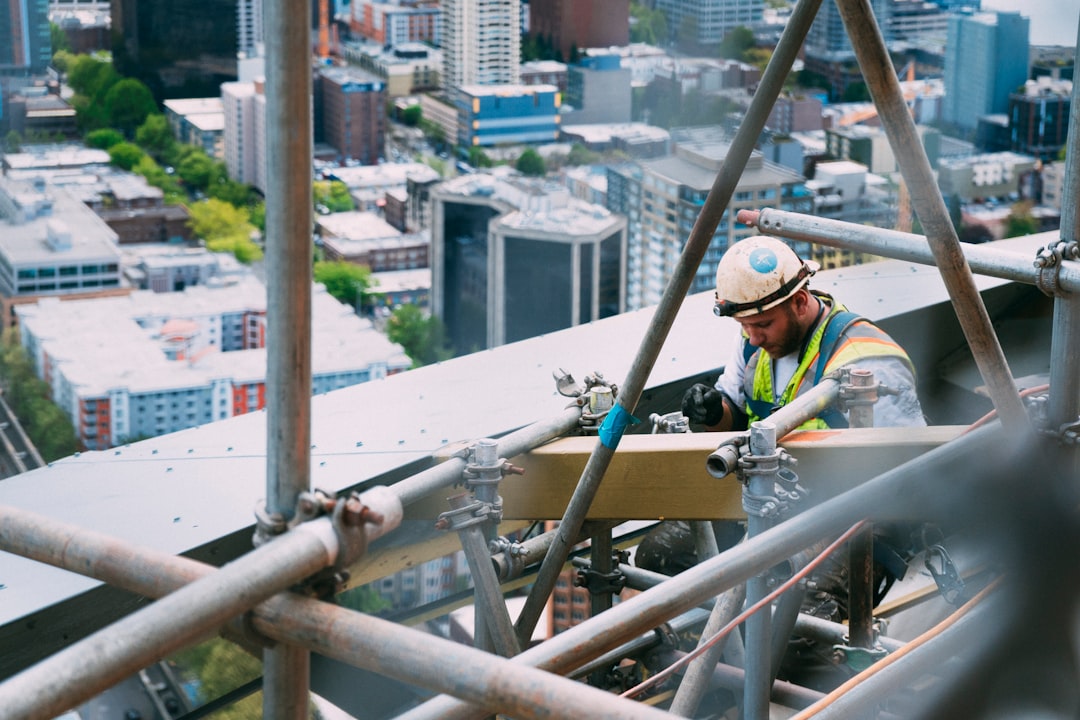
Silicon's use in construction is significantly affected by temperature, particularly regarding its mechanical stability and performance across varying thermal conditions. The inherent brittleness of silicon at lower temperatures, along with its transition to a more ductile state only at higher temperatures, poses challenges in environments with fluctuating temperatures or substantial heat exposure. Furthermore, the mechanical properties of silicon, influenced by factors like crystal orientation and impurity levels, can change with temperature, making it difficult to rely on consistent performance at elevated temperatures. Given the growing demand for construction materials that can withstand diverse climates and rigorous performance standards, understanding how temperature impacts silicon is essential for its wider adoption in bulk applications. This also underscores the necessity for further research into developing alternative materials or composite structures that could improve the resilience and adaptability of silicon-based solutions for construction projects.
Silicon's use in construction projects is influenced by its behavior under varying temperatures, presenting both opportunities and challenges. While some silicon-based materials, like silicones, have a long history in the industry, their application in bulk structural elements is still limited.
One concern is the increased fragility of silicon at lower temperatures, making it susceptible to brittle failure during impacts in colder climates or environments with significant temperature fluctuations. Further, at higher temperatures, silicon's thermal expansion rate differs from many common construction materials like steel or concrete. This mismatch can create internal stresses at material interfaces, potentially leading to failure when subjected to temperature shifts.
Beyond simple expansion issues, silicon's magnetic properties are also influenced by temperature. Near its Curie temperature, the material's magnetic behavior changes considerably, which could interfere with applications using electromagnetic technologies. Achieving the ductility improvements silicon offers at ~900°C in most construction scenarios is unlikely without damaging the material's overall structure beforehand, limiting the practicality of this property.
Similarly, silicon's brittle nature makes it susceptible to thermal shock, as rapid temperature changes can induce cracking and compromise its integrity. Even its crystalline structure can undergo phase transformations at high temperatures, changing the material's properties in potentially unpredictable ways.
Large silicon crystals, while potentially attractive, can exacerbate problems related to heat dissipation. This can create localized hotspots, increasing thermal stress and the risk of structural failure. Even small impurities present in the crystal lattice can have a major effect on silicon's thermal limits, potentially leading to weaknesses at elevated temperatures.
While bulk silicon has impressive thermal conductivity, this advantage is lost at smaller scales, which becomes a challenge for micro-fabricated silicon components subjected to thermal loads. Finally, composite materials incorporating silicon often experience interface challenges under thermal stress. Poor adhesion between components can lead to delamination or failure under load, impacting their reliability in construction.
Overall, a deeper understanding of the interplay between silicon's crystal structure, impurities, and temperature-dependent properties is necessary for designing and building reliable and robust construction projects. These thermal constraints continue to be a significant area of investigation as researchers seek to unlock silicon's full potential within the realm of construction materials.
Silicon in Construction Technical Limitations and Material Science Challenges of Bulk Applications - Cost Barriers for Large Scale Silicon Implementation in Building Components
The widespread adoption of silicon in large-scale building components is currently hampered by substantial cost barriers. The production of high-quality crystalline silicon, a crucial step for many envisioned applications, involves complex and expensive processes. Methods like the Czochralski technique, while capable of producing the necessary silicon wafers, contribute significantly to the overall manufacturing cost. Furthermore, the challenges of adapting silicon, a material primarily used in microelectronics, to the demands of construction projects introduce further cost complications. Integrating silicon into building structures on a large scale requires overcoming compatibility and scalability hurdles, often adding to the existing cost burden. Although silicon presents enticing possibilities for enhanced performance in construction, the economic hurdles can overshadow these potential gains, making traditional building materials more financially attractive in many scenarios. Overcoming these cost limitations will be essential if silicon is to transition from a material with niche applications to a viable and widely adopted component in the building sector.
The widespread adoption of silicon in building components faces a significant hurdle in the form of high production costs. Creating high-quality, defect-free silicon crystals demands stringent control over growth conditions, requiring substantial investment in specialized equipment and monitoring systems. This translates into higher initial costs compared to traditional building materials.
Historically, the energy required for silicon wafer production has been substantial, further impacting the economic feasibility of silicon in construction. The processes for growing and refining silicon crystals are energy-intensive, pushing prices above those of materials like steel or concrete.
Logistical challenges related to silicon's fragility and weight add to the cost burden. Bulk transport of silicon presents a risk of damage during transit, necessitating overproduction to account for potential losses. This added cost is eventually passed on to consumers.
Maintaining quality during silicon fabrication necessitates rigorous testing to detect crystal imperfections. These quality control procedures can be expensive, creating a barrier to widespread use in construction projects demanding material consistency.
The lack of established building codes and regulations for silicon in large-scale structural applications also slows its adoption. Adapting to existing safety standards requires costly research and compliance, adding delays and expenses to project timelines.
Silicon's thermal expansion properties differ considerably from other commonly used building materials. This mismatch can lead to costly repairs and replacements if not carefully addressed in building designs, creating a significant economic consideration for builders.
The current market demand for silicon-based construction components doesn't justify large-scale production facilities, resulting in a challenging feedback loop. The lack of demand discourages investment in production infrastructure, which in turn limits the opportunity for economies of scale that could lower costs.
Silicon's inherent brittleness at typical temperatures not only poses a risk during construction but also creates complications for insurance and risk management. These extra costs can discourage the use of silicon, as project stakeholders evaluate these increased risks.
Research into silicon composites is underway, but the cost and reliability of obtaining high-quality polymer interfaces introduce further expenses. The economic viability of employing silicon composites in cost-sensitive construction projects remains uncertain, impacting their practical adoption.
Despite promising theoretical advantages, silicon's limited lifespan and predictable performance in structural roles necessitate more comprehensive lifecycle analyses for builders. These assessments are costly, and the potential for premature material failure could push builders toward more established materials. This ultimately impacts market acceptance of silicon in construction.
Silicon in Construction Technical Limitations and Material Science Challenges of Bulk Applications - Silicon Carbide Manufacturing Challenges for Construction Grade Materials
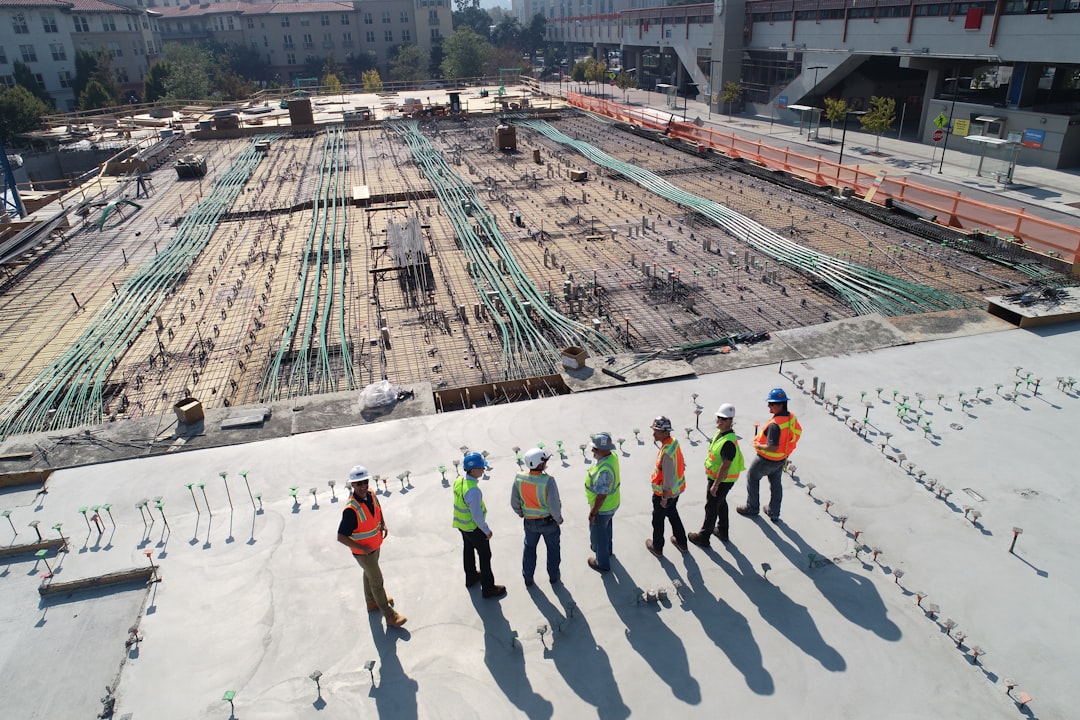
Silicon carbide (SiC) holds potential as a construction material due to its ability to withstand high temperatures and its inherent strength. However, its widespread use is hindered by various manufacturing challenges. Creating high-quality SiC ceramics with the necessary precision for construction applications is still difficult. Furthermore, SiC's inherent brittleness raises concerns about its capacity to withstand the stresses encountered in real-world construction environments, especially in demanding situations. The shift from its primary application in microelectronics to construction presents unique challenges in terms of material science and engineering. If SiC is to become a viable, reliable construction material, researchers and manufacturers must overcome these hurdles related to both its production and suitability for bulk applications. Addressing these limitations is key to fully exploring SiC's potential in the construction industry.
Silicon carbide (SiC) holds promise as a high-performance material due to its impressive strength at elevated temperatures and resistance to harsh environments. However, its journey from specialized applications to widespread use in construction faces numerous obstacles, primarily rooted in material science and manufacturing complexities. One key challenge lies in consistently producing large, high-quality SiC crystals that meet the structural demands of construction. While SiC excels at withstanding extreme heat, current manufacturing methods can struggle to achieve the level of uniformity needed for bulk applications without introducing defects that could compromise its performance.
Furthermore, the process of doping SiC to enhance specific properties is far more intricate than with crystalline silicon. This precise manipulation of the material is crucial for construction applications, but it also adds another layer of complexity to the already challenging manufacturing process. The compatibility of SiC with traditional construction materials is another area of concern. The interface between SiC and common substrates can present challenges in adhesion, potentially leading to material failure. Developing robust and effective interface solutions remains a significant hurdle in achieving widespread adoption.
The cost of producing bulk SiC is another major barrier to its widespread use. Processes like chemical vapor deposition and sintering are currently expensive, often making SiC a less economically feasible option than more conventional materials like concrete or steel for large-scale building projects. Moreover, the relatively limited research base on SiC's applications in construction hinders the pace of innovation compared to more established materials. This slower progress in understanding its behavior in construction settings can make design and implementation challenging.
Even slight variations in the manufacturing process of SiC can lead to considerable differences in its mechanical properties, which creates challenges when attempting to predict its behavior reliably in large-scale structural applications. Furthermore, SiC tends to exhibit higher brittleness compared to some other construction materials at normal temperatures, raising concerns about potential catastrophic failures due to unexpected impact or stress. Growing large, flawless SiC crystals is itself a significant technological hurdle; the demanding growth conditions can introduce stress points that can severely weaken the material.
Finally, while SiC is exceptionally stable at high temperatures, it's not entirely immune to degradation in the presence of certain environmental factors over time. This potential for long-term chemical deterioration necessitates protective measures or design choices to ensure the material's sustained functionality in construction settings. Overcoming these manufacturing and material science challenges will be essential for unlocking SiC's true potential as a viable material for diverse construction applications.
Silicon in Construction Technical Limitations and Material Science Challenges of Bulk Applications - Environmental Impact Assessment of Silicon Based Building Materials
The environmental performance of silicon-based building materials is becoming a central focus, particularly with the growing use of Life Cycle Assessment (LCA). LCA provides a framework for evaluating the entire lifespan of a material, from its raw material extraction to its eventual disposal. This is especially important within the construction industry, a sector with a substantial environmental footprint, consuming a large amount of energy and contributing to a sizable portion of global carbon emissions. Understanding the specific environmental impacts of silicon-based materials, encompassing the sourcing of raw materials, manufacturing processes, application in construction, and finally, disposal and recycling, is key to developing more environmentally conscious construction practices.
While there is potential for positive environmental impacts with some silicon materials, finding effective ways to minimize negative impacts requires careful consideration. Attempts to mitigate environmental issues might be counterproductive if not carefully thought out. Furthermore, the technical characteristics of silicon, such as its inherent brittleness and susceptibility to variations in temperature, introduce constraints on its broader implementation. Continued research and innovation are needed to address these challenges and fully explore silicon's potential in a way that aligns with environmental sustainability. Ultimately, a thorough understanding of the environmental implications of using silicon in construction will help guide choices that can positively contribute to both climate change mitigation and resource management within the construction industry.
1. The energy required for producing high-quality silicon is quite high, reportedly exceeding 100 times that of conventional materials like concrete. This raises questions about both its economic viability and its potential for wide-scale use in building projects.
2. Tiny cracks that form during the growth of silicon crystals are often unavoidable and can significantly reduce the strength of the material. These flaws can concentrate stress, potentially leading to failure under load, highlighting the crucial need for quality control during production.
3. Silicon only becomes workable (ductile) at very high temperatures, around 900°C. This limited range restricts its use in most typical construction environments that experience more moderate temperature fluctuations and impacts.
4. Silicon's rate of expansion or contraction with temperature is quite different from common construction materials like steel and concrete. This difference can cause stress at the joints between materials, which can affect the structural integrity of the whole structure as temperatures change.
5. Even minuscule amounts of impurities within silicon crystals can greatly change its mechanical behavior. These impurities can lower the load a silicon element can hold and make performance less predictable, which poses a significant obstacle in ensuring consistent material performance.
6. The size of silicon crystals directly influences their strength – larger crystals often contain more flaws and are therefore weaker. This connection between size and strength adds a degree of complexity to the production process since maintaining a specific crystal size is essential for many structural uses.
7. Silicon's brittle nature makes it more challenging to handle and install compared to more robust materials. Because there's a higher risk of catastrophic failure during construction, it necessitates careful planning and execution which isn't typically needed for stronger materials.
8. Initial research suggests that silicon-based materials might experience performance degradation in specific environmental conditions over time. For instance, prolonged exposure to moisture can lead to the formation of oxides on its surface, possibly affecting both its physical properties and its strength.
9. Combining silicon with polymers to create composites can potentially boost its strength, however, creating a robust and enduring interface between the two types of material is a significant engineering obstacle. This introduces uncertainty regarding the reliability of this approach to constructing buildings.
10. Silicon's use in construction lacks a strong historical precedent, making it difficult to establish building codes and regulatory approvals for it. The absence of clear guidelines hinders its integration into the wider construction industry, delaying progress in its adoption.
Silicon in Construction Technical Limitations and Material Science Challenges of Bulk Applications - Integration Issues Between Silicon Components and Traditional Construction Materials
The integration of silicon-based components within conventional construction materials is fraught with challenges due to fundamental differences in material characteristics and structural behavior. Silicon's inherent mechanical properties, particularly its anisotropic nature, can lead to unexpected behavior when subjected to load-bearing forces in construction applications. Its tendency towards brittleness at typical temperatures further complicates its suitability for structural elements, especially in dynamic environments where resilience is a priority. Bridging the gap between silicon and traditional construction materials requires overcoming several hurdles related to material compatibility. This includes developing robust interfaces to ensure long-term structural integrity, optimizing processing techniques to minimize defects and enhance reliability, and mitigating the inherent fragility of silicon. Further research into refining manufacturing processes and improving understanding of silicon's interaction with conventional construction materials is vital for overcoming these integration barriers and ultimately fostering broader adoption in the construction sector.
1. Silicon's behavior in construction environments can be impacted by water, as it can absorb moisture, leading to the creation of silica gel and subsequent surface swelling. This potential for moisture absorption raises concerns about the long-term integrity of silicon-based structures, especially in applications where exposure to water is likely.
2. The manufacturing processes used to create silicon-based materials often introduce stress concentrations due to imperfections within the material. These stress points can become significantly more pronounced when the material is subjected to dynamic loads. This makes conventional stress analysis techniques less effective for predicting the performance of silicon components in real-world applications.
3. Silicon's high thermal conductivity, while beneficial for electronic applications where rapid heat dissipation is desired, can create issues when dealing with composite materials in construction. Uneven heat distribution within the material can result in differences in expansion rates, which in turn, may lead to structural failure.
4. The crystal orientation of silicon significantly impacts its mechanical characteristics. For instance, if the crystals aren't aligned correctly during the fabrication process, the resulting material might have substantially lower strength than predicted. This can create significant challenges for structural engineers when designing with silicon, as the material properties can be less predictable than in other materials.
5. Rapid temperature fluctuations can lead to thermal fatigue in silicon components, an issue often overlooked in design considerations. This can greatly reduce the useful life of silicon-based constructions that are repeatedly exposed to temperature variations.
6. While some surface treatments can enhance silicon's mechanical performance, their implementation can introduce other issues. The treatment methods might cause chemical incompatibilities with other construction materials, leading to unforeseen failure mechanisms.
7. The presence of dislocations within the crystal structure of silicon affects its strength. A greater number of dislocations generally leads to a reduction in the material's mechanical performance. This means that for large-scale construction applications of silicon, extremely precise manufacturing processes will be required to control the number of dislocations.
8. Silicon's inherent resistance to wear and abrasion is a positive characteristic. However, its poor impact resistance across various conditions is a significant drawback when considering high-traffic areas or applications where impact loads are a possibility. Traditional construction materials often perform better under these types of conditions.
9. Silicon's inherent electronic properties can cause unwanted interactions with other materials nearby, leading to unintended electromagnetic interference. This becomes a design challenge in situations where electronic functionality is integrated into the construction of load-bearing structures.
10. Preliminary research suggests that silicon's brittleness can be made worse by the presence of low-frequency vibrations. This is a factor that is often overlooked in construction environments where machinery and equipment are in close proximity. This implies that designers may need to implement extra measures to ensure the safety and performance of silicon components under these conditions.
More Posts from patentreviewpro.com: