Recent Advancements in Pulsed CMT Welding for Aerospace Materials
Recent Advancements in Pulsed CMT Welding for Aerospace Materials - Pulsed CMT Welding Enhances Aluminum Alloy Joining in Aerospace
Pulsed Cold Metal Transfer (CMT) welding has shown promise in joining aluminum alloys, particularly within aerospace manufacturing. This welding approach effectively reduces the heat input compared to traditional methods, thereby mitigating the common formation of cracks and porosity, particularly problematic with Gas Metal Arc Welding. When properly applied to high-strength alloys such as AA2014T6, pulsed CMT can deliver defect-free welds, highlighting its potential for demanding applications in the aerospace industry. Additionally, research indicates that pulsed CMT may improve the mechanical characteristics and corrosion resistance of welded joints, contributing to greater durability and integrity for aircraft components. The positive outcomes across a variety of aluminum alloy series suggest that pulsed CMT welding is a strong candidate for modern aircraft construction and repair, offering a potentially superior alternative to traditional welding techniques.
Pulsed CMT welding has shown promise in addressing the challenges associated with joining aluminum alloys, particularly in aerospace applications. The reduced heat input inherent to the process, compared to conventional GMAW, helps mitigate issues like cracking and porosity, which are common in aluminum alloys due to their susceptibility to thermal stresses. The ability to fine-tune parameters like current, voltage, and wire feed rate allows for tailored welding of various aluminum alloys, such as the high strength AA2014T6, without compromising joint quality. For example, studies suggest specific parameter windows for achieving high-quality welds in AA2014 and AA6061, highlighting the importance of optimization for specific alloys.
However, even with pulsed CMT, welding high-strength aluminum alloys like AA7475 remains challenging due to a propensity for cracking, though pulsed CMT can help mitigate this compared to standard GMAW. This signifies the ongoing need for refinement and development of techniques within the pulsed CMT spectrum for a broader range of aluminum alloys.
Interestingly, pulsed CMT is not limited to joining similar aluminum alloys. Researchers have demonstrated its versatility in joining different aluminum series like 2xxx, 5xxx, 6xxx, and 7xxx, as well as its potential for dissimilar material joining, such as aluminum to titanium and magnesium. This versatility potentially broadens the applicability of the technology for aerospace structures where mixed materials are increasingly utilized.
The improved mechanical properties, like tensile strength and fatigue resistance, observed in pulsed CMT welds are likely a consequence of finer microstructures formed due to the controlled heat input. The reduction in the heat affected zone minimizes microstructural changes and thus, the degradation of material properties. In addition, the inherently lower spatter levels with pulsed CMT offers potential for enhanced efficiency and reduced need for post-weld clean up. The potential for real-time weld monitoring using integrated technologies is another advantage that may allow for better quality control and improved overall consistency of the welding process, especially for complex aerospace components. The data suggests a significant leap in performance from conventional welding methods but much still remains to be discovered to further refine and optimize the technology.
Recent Advancements in Pulsed CMT Welding for Aerospace Materials - Cracking Resistance Improves with Pulsed CMT Technique
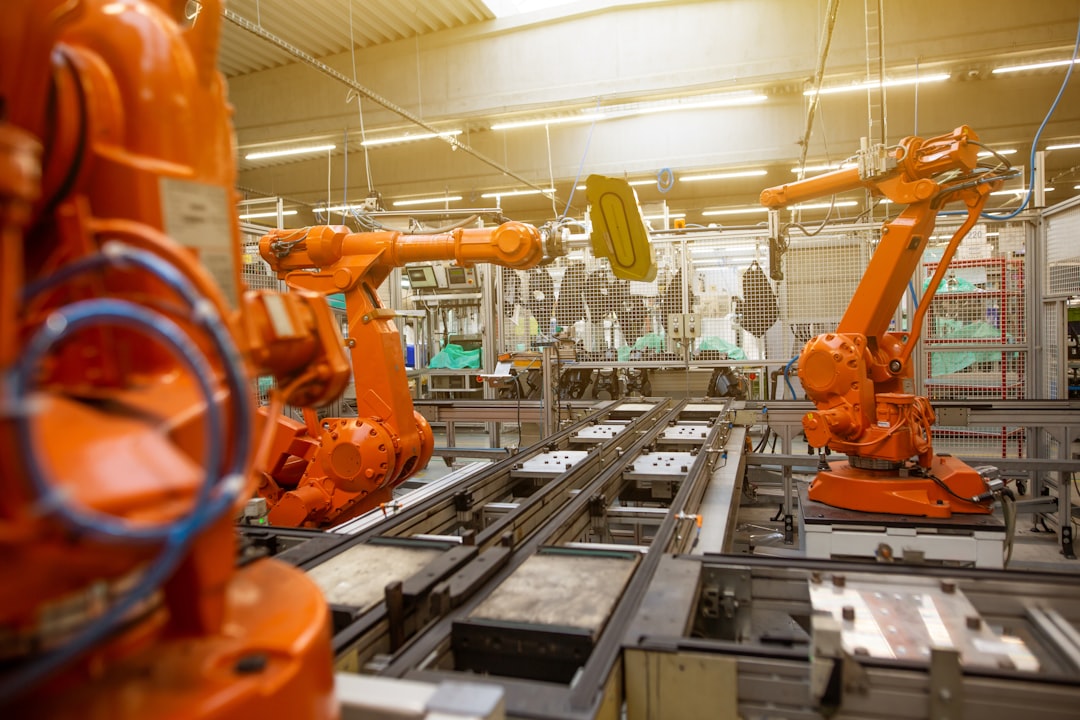
The pulsed Cold Metal Transfer (CMT) welding technique has emerged as a promising solution for improving the crack resistance in welding high-strength aluminum alloys, crucial for aerospace applications. By minimizing the heat input during the welding process, the pulsed CMT approach effectively reduces the risk of thermal stresses that can lead to cracking, a common issue particularly in alloys like AA7475. Studies have demonstrated that utilizing specific welding currents and speeds within the pulsed CMT process can produce high-quality welds without spatter, ultimately contributing to improved mechanical properties of the resulting joints. This enhanced crack resistance, coupled with the overall quality improvements, positions pulsed CMT as a potentially valuable advancement for aerospace welding, where reliable and efficient joining techniques are paramount. While the advantages of pulsed CMT are evident, ongoing research and development are needed to fully realize its potential and optimize its application across a wider range of aluminum alloys and complex aerospace component designs.
Cold Metal Transfer (CMT) welding, with its inherently lower heat input and stable operation, has already shown promise in reducing cracking during welding, especially when compared to traditional techniques. Further refinements, like pulsed CMT (PCMT), have been developed to enhance this capability even further. This pulsed variation allows for a more controlled and focused heat input, potentially lessening the stress concentration at the weld joint and therefore, lowering the risk of cracking. This becomes especially crucial in aerospace applications, where structural integrity under various stress conditions is paramount.
The ability to adjust the pulse frequency in PCMT offers an interesting avenue for optimization. By manipulating this frequency, we can manipulate the heat delivery to the weld pool. Studies have shown that tailoring this pulse behavior leads to improvements in weld pool dynamics, resulting in a reduction in susceptibility to cracking, particularly within high-strength aluminum alloys. Essentially, the fine-tuned pulses help guide and manage the molten metal more precisely, limiting the heat diffusion into surrounding areas. This, in turn, leads to a smaller heat-affected zone (HAZ), a region often prone to cracking due to thermal stresses and metallurgical changes.
The possibility of integrating advanced monitoring tools with the welding process, including high-speed imaging, also has the potential to enhance our understanding of the welding process in real-time. Being able to observe the weld pool and detect any developing defects, such as the initial stages of cracking, during the weld could be transformative. It could lead to faster feedback and the development of even more effective, in-process control measures.
Further, the reduced thermal cycle achieved with PCMT leads to less distortion in the welded piece. Minimizing distortions is also linked to reduced cracking, and this could be a significant advantage, especially in applications where precise tolerances are a necessity, like aircraft construction.
The advantage of PCMT extends to tailoring not just to various aluminum grades, but also to complex weld geometries. Conventional welding methods might struggle with such irregularities, while the more fine-grained control afforded by PCMT can provide better outcomes. Interestingly, researchers are investigating both fixed and variable pulse modes for different alloys. These modes lead to different thermal profiles that can be fine-tuned to address the unique hot cracking risks in different aluminum alloy chemistries.
Further, the controlled cooling rates associated with the pulsed CMT approach seem to have a positive impact on the microstructure of the weld. This may lead to improved precipitation of strengthening phases within the aluminum alloys, which is critical in contributing to the overall crack resistance. This type of improvement could be game-changing, expanding the range of applications where aluminum alloys can be utilized effectively and safely.
Evidence suggests that defects like undercuts and incomplete fusion are less likely with PCMT, effectively reducing potential crack nucleation points. Moreover, there is still significant research on this topic, exploring how pulsed CMT can be further optimized to improve the mechanical properties of the resulting weldments, specifically focusing on improving fracture toughness. It's exciting to think that this technology may open new doors for using aluminum alloys in applications where they were previously considered unsuitable, fostering innovation and creativity within the aerospace field.
While PCMT has shown substantial promise, more research is needed. A better understanding of the relationship between the welding parameters, arc behavior, and mechanical properties of the weld will lead to further improvements. Continued exploration and refined optimization of PCMT will hopefully unlock even more impressive results for the field of aerospace materials.
Recent Advancements in Pulsed CMT Welding for Aerospace Materials - Optimal Welding Parameters for AA7475T761 Alloy Identified
The AA7475T761 alloy, widely used in aerospace due to its excellent performance, presents welding challenges due to its high strength and tendency to crack with traditional methods. Pulsed Cold Metal Transfer (CMT) welding offers a potential solution by significantly reducing heat input compared to conventional Gas Metal Arc Welding (GMAW). This lowered heat input helps manage the thermal stresses that often cause cracking in this alloy, a crucial factor for aerospace applications. Researchers are now exploring how specific adjustments to welding parameters within the pulsed CMT process, like current and voltage, can create welds with superior mechanical properties. These findings could be critical in ensuring the long-term structural integrity of aerospace components built with this alloy. However, further research and optimization are necessary to fully exploit the potential of pulsed CMT in achieving consistently high-quality welds with AA7475T761, especially in complex aerospace applications.
AA7475T761, a prominent aluminum alloy enhanced with zinc and lithium, is widely favored in aerospace due to its exceptional strength-to-weight ratio. This makes it attractive for applications demanding both high performance and fuel efficiency. However, welding this alloy presents challenges, specifically concerning the potential for cracking, especially when using conventional welding techniques. This sensitivity to welding parameters makes finding the optimal settings crucial for achieving high-quality weld joints.
Pulsed Cold Metal Transfer (CMT) welding has demonstrated potential in mitigating the risk of cracking in AA7475 alloys. By lowering the peak temperature and creating a more consistent heat input compared to traditional methods, CMT can significantly reduce thermal stresses that lead to cracking. This approach holds significant promise for reducing weld defects.
Research suggests a specific heat input window, typically between 0.5 and 1.2 kJ/cm, is ideal for pulsed CMT welding of AA7475T761. Maintaining this delicate balance of heat input is essential to creating crack-free joints. The pulse frequency in CMT welding can be further optimized to tailor the heat delivery to the weld pool. Adjusting the pulse pattern and duration allows engineers to fine-tune the weld pool dynamics, further minimizing thermal stress and related issues like cracking.
Interestingly, the finer microstructures produced by pulsed CMT within AA7475T761 lead to improved fatigue resistance in the welded joints. This is a crucial characteristic for aerospace components that endure cyclical loading throughout their service life. Further, the ability to utilize high-speed imaging during the welding process offers exciting possibilities. This real-time monitoring can reveal potential defects early, allowing for rapid adjustments during welding, and ultimately potentially improving the quality of the weld.
The reduced heat-affected zone (HAZ) observed in pulsed CMT welds is another benefit. A smaller HAZ means less alteration of the surrounding base material, preserving the integrity and properties of the AA7475T761 alloy near the weld. The exploration of various pulse modes in pulsed CMT has led to observations that tailored pulse frequencies and amplitudes can further enhance mechanical properties. This suggests the possibility of refining pulsed CMT to achieve even better weld quality and open up new applications requiring high-performance welds.
Despite the promising outcomes, the relationship between specific welding parameters and the resultant microstructures in AA7475T761 remains complex. Further research is necessary to fully understand these intricate connections, especially within such a high-strength alloy. Continued investigation and refinement of the technique are expected to lead to further optimization and ultimately enhance the applicability of pulsed CMT welding for complex aerospace applications.
Recent Advancements in Pulsed CMT Welding for Aerospace Materials - Versatility in Welding Similar and Dissimilar Aluminum Components
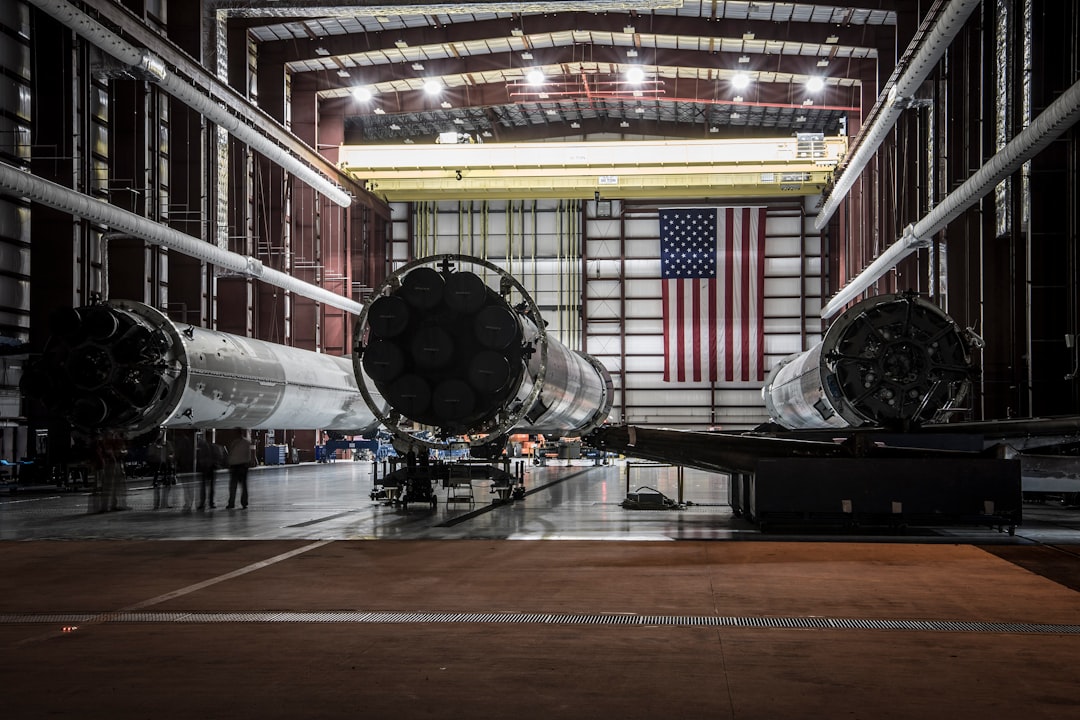
Pulsed Cold Metal Transfer (CMT) welding demonstrates a notable versatility when it comes to joining both similar and dissimilar aluminum alloys, a critical feature in the aerospace industry. This welding method's ability to control heat input effectively reduces the risk of distortion and cracking, crucial for preserving the integrity of aluminum structures, especially high-strength ones. It shows particular promise for handling the complex shapes often encountered in aerospace designs. Pulsed CMT's adaptability to a wide range of aluminum alloys, such as the common 2xxx, 5xxx, 6xxx, and 7xxx series, is noteworthy. Furthermore, it shows potential for joining dissimilar materials, a capability that could be useful in aerospace designs where multi-material assemblies are becoming more prevalent. Its potential integration with robotic systems has the ability to streamline the fabrication process, making it a potentially compelling option for the aerospace sector. While the promise is significant, continued investigation and a deeper understanding of how different welding parameters affect the final outcome will be important for refining this technique and achieving even better results across a wider range of aerospace materials and applications.
Pulsed CMT welding has shown remarkable versatility in joining a variety of aluminum alloys, ranging from the commonly used 2xxx series to the higher-strength 7xxx series, demonstrating its potential for a wide array of aerospace applications. This adaptability extends beyond similar alloys, with promising results in joining dissimilar materials like aluminum to titanium and aluminum to magnesium, a capability increasingly important as aerospace designs incorporate multiple materials to achieve lightweight structures.
The control offered by pulsed CMT is noteworthy. The ability to manipulate the pulse parameters provides a precise way to manage the heat input during welding, allowing for more controlled thermal cycles. This is critical for minimizing distortion in the welded parts, especially important when dealing with alloys that have differing thermal expansion characteristics. Engineers can fine-tune the settings based on the specific alloy and desired weld outcome.
The microstructural effects of pulsed CMT seem to translate to improved mechanical properties. Specifically, enhanced fatigue resistance – a critical factor for components subjected to repetitive stress cycles – has been observed. This suggests that pulsed CMT might play a role in creating more durable and reliable structures, crucial for aerospace applications.
A reduction in spatter is also an important advantage, as it improves welding efficiency and reduces the time and effort needed for post-weld cleanup. This translates to enhanced productivity in manufacturing environments.
Researchers have found that tailoring the pulse frequency can impact weld pool dynamics. This careful manipulation can control heat diffusion and minimize the heat-affected zone (HAZ). The smaller HAZ is a positive development because it reduces the degree of change in the base material’s properties surrounding the weld, maintaining the original strengths of the alloys.
The potential of real-time monitoring techniques like high-speed imaging coupled with pulsed CMT is intriguing. These technologies could usher in a new era of quality control in welding. By giving engineers instant feedback on weld quality and detecting defects during the process, it could lead to better, more consistent welds.
Minimizing changes in the microstructure of the heat-affected zone (HAZ) is a key benefit, leading to welds that maintain more of the parent metal's properties. This is especially vital for critical components built with high-strength aluminum alloys.
Interestingly, the specific cooling rates generated by pulsed CMT might facilitate the formation of strengthening phases within the aluminum alloys. These phases can further enhance the performance of the welded materials.
While the benefits of pulsed CMT are compelling, it’s important to acknowledge the challenges. Certain high-strength alloys, such as AA7475, still present difficulties in achieving consistently high-quality welds. Further optimization of welding parameters is needed for these alloys, including exploration of specific pulse modes and the development of methods to mitigate inherent cracking tendencies.
Continued research into pulsed CMT's behavior with different alloys and weld configurations will be necessary for further refining this technique and realizing its full potential within the aerospace industry.
Recent Advancements in Pulsed CMT Welding for Aerospace Materials - Spatter-Free Operations Lead to Cleaner Weld Joints
The ability to achieve spatter-free welding operations with pulsed Cold Metal Transfer (CMT) is a significant benefit, especially within the aerospace industry where clean and robust welds are crucial. By meticulously controlling heat input and the transfer of molten metal, the CMT process greatly minimizes the formation of spatter. This reduction in spatter not only leads to visually appealing weld beads but also greatly simplifies post-weld cleaning. Minimizing cleanup is particularly advantageous when dealing with the sensitive materials used in aerospace construction where maintaining structural integrity is paramount. Furthermore, the reduced heat input characteristic of CMT preserves the properties of the base material being welded. This helps ensures that the weld joint meets the high performance standards expected in aerospace applications. These advancements in pulsed CMT welding are leading to more effective and streamlined welding methods within the aerospace industry, contributing to a greater focus on high-quality joints for demanding aircraft and spacecraft components.
CMT welding, a refined version of MIG welding, uses a notably lower heat input—around 10% compared to traditional MIG—due to its two-state operation: an arc-generating "hot" state and an electrode-retracting "cold" state that lowers heat. This low heat input, along with its inherently lower voltage, makes it well-suited for thin-gauge metals, reducing distortion and minimizing the potential for heat damage. Recent innovations in pulsed CMT have especially proven valuable in aerospace materials, particularly with the strong AA7475T761 alloy.
The reduced heat input associated with CMT contributes to visually appealing weld beads because of the more regulated way the metal is deposited. This leads to cleaner welds with less spatter. It is worth noting that the use of filler metals, particularly copper-based ones, can sometimes lead to issues like cracking in the heat-affected zone (HAZ) when welding dissimilar metals. However, nickel-based fillers seem to alleviate this.
An interesting consequence of the CMT welding process is the refinement of the grain structure as the weld solidifies, leading to improved mechanical and microstructural characteristics. It's also gaining attention for its possible use in cladding and coating, improving the appearance and function of welds.
One of the major selling points of CMT is the ability to achieve spatter-free or near-spatter-free operations. This leads to a cleaner weld joint, reducing the need for post-weld cleanup, which in turn helps speed up the manufacturing process. Dissimilar metal welding, becoming increasingly important for constructing strong yet lightweight vehicles, relies on materials with different properties to optimize thermal conductivity, corrosion resistance, and recyclability. This also underscores the growing need for advanced welding technologies that can address these demanding requirements in various industries, particularly aerospace.
While the benefits of CMT and its pulsed variant appear significant, it's important to recognize that ongoing research is needed to better understand and optimize its parameters across a wider range of alloys and complex geometries. Nevertheless, given its potential, it's an exciting area of research and engineering.
Recent Advancements in Pulsed CMT Welding for Aerospace Materials - Energy Efficiency Gains in Pulsed CMT Welding Process
Pulsed Cold Metal Transfer (CMT) welding offers a compelling approach to welding, especially within aerospace, due to its significantly improved energy efficiency. This method drastically reduces heat input compared to conventional MIG welding, achieving a remarkable 90% reduction. This minimized heat input translates to less thermal distortion and a greater ability to maintain weld quality, especially when dealing with demanding materials like high-strength aluminum alloys. Pulsed CMT's ability to precisely control the welding process has shown potential for creating high-quality welds, even when depositing thicker layers of material or repairing damaged welds.
While research shows promising results in areas like improved weld strength, microhardness, and corrosion resistance, there is still room for refinement. Optimizing the various parameters in the pulsed CMT process holds promise for further increasing performance across a greater variety of aerospace materials. Further study is needed to fully realize the benefits of this technique across the range of aerospace applications. While promising, the current stage of development still requires more research to unlock the full potential of this welding approach in aerospace.
Cold Metal Transfer (CMT) welding, initially developed in 2004, stands out as an advancement within the Gas Metal Arc Welding (GMAW) family. Its key innovation is a significant reduction in heat input, achieving roughly 90% less compared to conventional MIG welding. This unique characteristic makes it particularly attractive for applications where controlling heat is crucial, like joining aluminum alloys in aerospace. The lower heat input is instrumental in minimizing the formation of cracks and porosity, which are common challenges in welding aluminum, particularly when dealing with high-strength alloys such as AA2014T6.
A further refinement, pulsed CMT, has enhanced this inherent heat control. The ability to tailor the pulse frequency allows for incredibly precise management of the weld pool. This, in turn, allows for finer grain structures within the weld, translating into improved tensile strength and fatigue resistance, essential characteristics for aerospace applications. Additionally, the ability to fine-tune these parameters seems to contribute to a smaller heat-affected zone (HAZ), decreasing the risk of microstructural changes that can promote crack formation. It's fascinating that researchers are actively exploring the integration of high-speed imaging and other real-time monitoring techniques with the pulsed CMT process. This kind of real-time feedback offers a tantalizing opportunity to better understand weld pool dynamics and to identify and correct defects in real-time, leading to a potential increase in weld quality.
CMT's capabilities are not limited to similar materials. It shows potential in joining aluminum to other materials, such as titanium or magnesium, which opens up possibilities for multi-material aerospace designs. The near spatter-free nature of the process offers another appealing advantage—cleaner welds with minimal post-weld cleanup, boosting manufacturing efficiency.
While the advantages of pulsed CMT in reducing cracking and achieving superior mechanical properties are evident, especially when dealing with challenging materials like AA7475, more research is needed to further optimize the process. Finding optimal parameters for different aluminum alloys and complex geometries is an ongoing area of exploration. There's an exciting potential for further advancement and for discovering even more novel applications within the field of aerospace materials engineering, which is why ongoing research in this domain is so crucial. The ability to tailor pulsed frequencies and explore different pulse modes for different alloys is another aspect of ongoing research that holds the promise of refining this technique even further. The future of pulsed CMT holds promising opportunities, both in improving the reliability of current aerospace materials and potentially unlocking novel applications.
More Posts from patentreviewpro.com: