Optimizing Steam Flow for Enhanced Heating Capacity A Thermodynamic Analysis
Optimizing Steam Flow for Enhanced Heating Capacity A Thermodynamic Analysis - Understanding Steam Flow Dynamics in Heating Systems
Grasping the behavior of steam flow is central to improving heating system performance. Steam's unique properties, notably its high latent heat capacity compared to water, make it a potent heat carrier. This means it can transport substantial amounts of energy using relatively small masses. The ability to distribute steam effectively hinges on creating pressure differentials within the system, making it a readily deployable heating agent.
However, reaching optimal efficiency is not without its challenges. The inherent limitations of thermodynamic cycles and unavoidable losses within steam systems can impact overall performance. This underscores the need for detailed energy and exergy analyses to pin-point areas for refinement. A thorough understanding of these flow dynamics and related energy aspects opens the door to operational improvements, ultimately leading to higher energy system performance.
1. Steam's heat transfer capabilities significantly exceed those of liquids, which is why we see quicker heating in applications where it's used. This property is quite useful, especially when needing to rapidly heat surfaces or spaces.
2. Water's latent heat of vaporization is substantial, around 2,260 kJ/kg at standard pressure. This means a large amount of energy can be transferred by steam without a corresponding temperature change, highlighting its effectiveness as a heat carrier.
3. Steam traps are essential for keeping heating systems operating efficiently. If not managed properly, condensate can accumulate and lead to notable energy losses, reducing the overall heating effectiveness.
4. The steam's quality, which is essentially the percentage of vapor in the mixture, is a critical factor in how effectively it heats. Steam with a lower quality will have more entrained water, negatively impacting its heat transfer capability.
5. Insulation is a crucial factor in reducing heat losses in steam pipes, with reductions of up to 90% achievable with proper implementation. This underscores the importance of considering thermal management for optimal steam flow.
6. Superheated steam can achieve temperatures exceeding 500°F without a change in pressure. This feature makes it suitable for applications where high energy content is beneficial, like turbine operations or specific chemical processes.
7. Steam flooding, where water builds up in steam systems, can disrupt flow patterns and significantly reduce the efficiency of heat transfer. Managing the condensate effectively is crucial for steam system design to avoid this problem.
8. While necessary for steam system operation, excessive pressure drops in steam pipelines can reduce efficiency and lead to higher energy costs. Even small increases in pressure drop can cause measurable increases in energy consumption over time.
9. The velocity of the steam plays a key role in how fast it transfers heat. Higher steam velocities can result in faster heat transfer, but care is needed in system design to avoid issues like water hammer, which can cause significant damage.
10. Achieving uniform heating in steam distribution systems can be challenging, especially in large or complex structures. Variations in the velocity profiles of steam can lead to inconsistent heating, necessitating careful planning and design to ensure even heat distribution.
Optimizing Steam Flow for Enhanced Heating Capacity A Thermodynamic Analysis - Thermodynamic Principles Applied to Steam Optimization
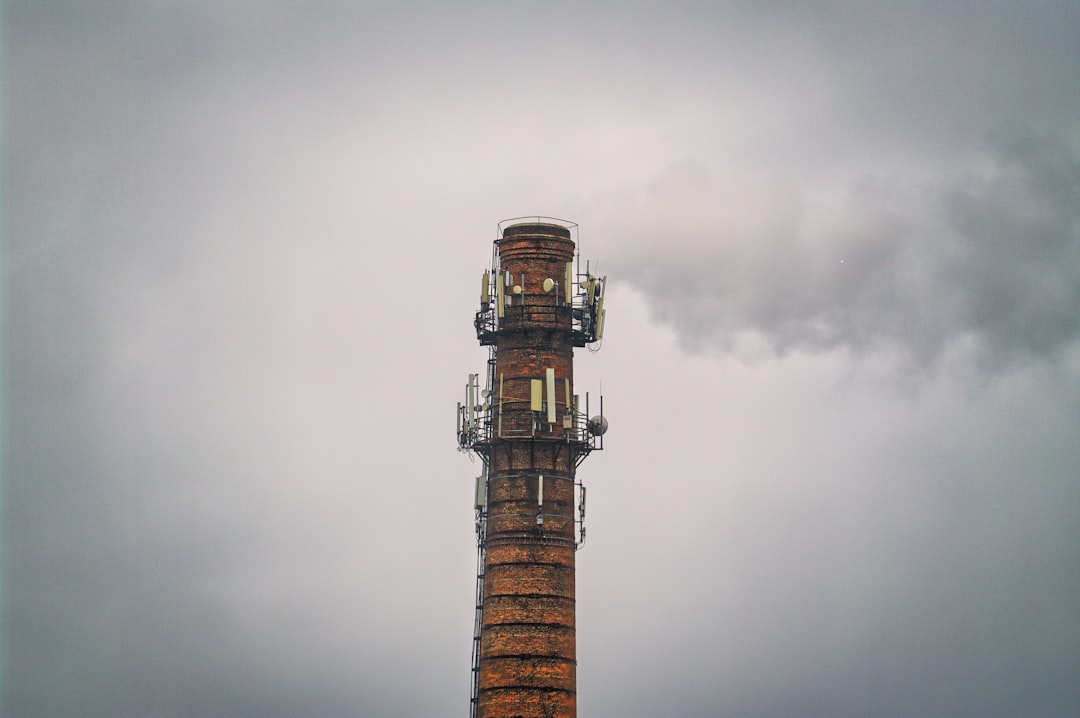
Applying thermodynamic principles to optimize steam systems offers a powerful way to enhance heating capacity. By carefully examining energy and exergy flows, along with operational variables like steam quality and pressure, we can find opportunities to significantly boost efficiency. Historically, methods like linear programming have been used to develop more effective steam cycle designs, while more recent work has incorporated complex simulations and even multi-generation systems that seek to maximize thermal efficiency across multiple applications. However, challenges still remain. For example, minimizing system losses and finding the optimal balance between steam quality and pressure are crucial for attaining the best performance. Understanding how these thermodynamic factors interact is vital, as it informs the design changes and operational adjustments needed to develop highly efficient steam systems. While promising, the ongoing quest for improvement necessitates ongoing research and refinement to fully leverage the inherent potential of steam-based heating systems.
Steam, due to its significantly lower density compared to water, experiences substantial volume changes even with small pressure fluctuations. This can affect the efficiency of transporting steam within a system, something that needs careful consideration when designing or modifying existing systems.
Operating a steam system at the saturation temperature of 100°C can yield steam at pressures as low as 0.1 bar. This makes it attractive for lower-temperature processes, but it's important to remember that the heat content per unit mass of steam decreases at lower pressures. This highlights the need for careful pressure management to maintain efficiency.
The enthalpy of steam, a measure of its total energy content, differs significantly depending on whether it's saturated or superheated. Superheated steam possesses more energy, offering the opportunity for its use in applications demanding higher temperatures and energy input.
Ideally, a steam cycle could achieve a thermal efficiency in the 40-50% range. However, real-world systems often fall short, rarely exceeding 30%. Friction, heat loss, and imperfections in the fluid flow are significant factors in this efficiency gap. This reality underscores the importance of careful system design and operational optimization.
Uninsulated steam systems can suffer from substantial energy losses—over 20% of the total energy can escape through radiation and convection. Regular inspections and improvements to insulation can greatly reduce these losses.
Water's critical pressure, around 22.1 MPa, marks the point where the distinctions between liquid and gas phases disappear. At this pressure, steam displays unique thermodynamic properties that offer potential for building very efficient energy systems.
Implementing advanced control strategies, like adapting steam flow based on demand, has shown the potential for energy savings exceeding 20%. These approaches can improve a system's responsiveness and optimize performance in variable conditions.
The practice of blowdown—removing impurities and excess water—can enhance heat transfer. But, poorly managed blowdown can lead to the waste of considerable amounts of energy and water, a consideration in its own right.
Flash steam recovery—a process that captures energy from condensate—can potentially recover up to 60% of the energy in high-pressure applications. This is beneficial both for improving efficiency and lowering operational expenses.
The Joule-Thomson effect describes how gases cool when they expand. In steam systems, this effect can be leveraged to recover energy during pressure drops. Understanding and incorporating this principle is key to making steam heating applications more efficient.
Optimizing Steam Flow for Enhanced Heating Capacity A Thermodynamic Analysis - Analyzing Heat Transfer Efficiency in Steam-based Heating
Examining how efficiently heat is transferred in steam-based heating systems offers a path to improved performance. Maintaining the cleanliness of boiler components like tubes is crucial, as the buildup of substances like soot and scale can significantly impede heat transfer, impacting both energy and exergy efficiency. Achieving optimal steam pressure and temperature is key for efficient heat exchanger operation, a central component of maximizing overall system performance. Additionally, understanding how steam flows within a system, particularly within steam generators, is important as it influences heat transfer capabilities, especially in the colder areas of these components. The complex interplay between these aspects highlights the ongoing need for careful steam system design and a continuous effort to improve efficiency.
Keeping a clean boiler, free of soot and mineral buildup, is crucial for maximizing both the energy and the thermodynamic potential of the steam. This is because it improves the transfer of heat, enhancing overall steam boiler performance.
Finding the right balance between steam pressure and temperature is key to getting the most out of steam-based heat exchangers. This optimization isn't trivial, and a nuanced understanding of the process conditions is needed to achieve the ideal operating point.
Troubleshooting steam heating issues can often be done with a brief assessment by a specialist. This approach can highlight underlying issues and pave the way for improving heating capacity without extensive overhauls.
While increasing the pressure and temperature of steam may seem like an easy way to improve performance, it can actually lead to significant energy losses. These losses can be particularly noticeable in high-efficiency power generation systems like ultra-supercritical plants, highlighting the complex interplay between performance gains and operational trade-offs.
Combining heat pumps and compressors is a potential route to making steam generation much more energy-efficient, particularly in heating applications. This type of hybrid system could potentially help reduce reliance on other heat sources, though the practicality needs careful consideration.
Increasing the height of a separator plate inside a steam generator has a positive effect on heat transfer within a certain range. This observation suggests that careful geometric design of internal components can have a considerable impact on the thermal performance of a generator.
The way steam flows within a steam generator can drastically affect the process of heat transfer, primarily impacting the cooler section of the device. Achieving a consistent flow profile is a significant challenge when designing such systems.
Heat Recovery Steam Generators (HRSG) are ingenious devices that capture waste heat from gas turbines and use it to generate steam. This captured heat can then be used for additional power generation or other applications, creating more efficient use of the thermal energy produced by the turbine.
The effectiveness of these HRSGs depends on things like how much gas flows through them, the density of the hot gas, and how much energy is required to raise the temperature of the gas. Understanding these parameters is essential for optimizing their effectiveness.
Heat transfer enhancement methods are often far more efficient than conventional approaches. This often leads to a decrease in superheated steam temperatures, potentially changing the design criteria for downstream systems. While this seems to be a beneficial outcome, the trade-offs for specific applications are not always clear.
Optimizing Steam Flow for Enhanced Heating Capacity A Thermodynamic Analysis - Impact of Pressure and Temperature on Steam Flow
The interplay of pressure and temperature significantly influences steam flow, a critical factor in optimizing heating systems for increased capacity. Higher pressure and temperature can boost thermodynamic efficiency by minimizing the temperature difference between the hot gases and the steam, thereby improving the overall energy conversion process. However, indiscriminately increasing these parameters can lead to inefficiencies. For instance, elevated pressure and temperature can result in a higher degree of irreversibility in the system, potentially hindering the full potential of thermodynamic cycles, particularly in very high-pressure steam power plants. This underscores the need for careful management of pressure and temperature to prevent energy loss. Achieving the best system performance necessitates ongoing monitoring and adjustments, making continuous analysis an essential part of the optimization process. Therefore, a deep comprehension of how pressure and temperature affect steam behavior is crucial for maximizing the effectiveness and dependability of steam-based heating.
Steam's behavior can be surprising. At high temperatures and pressures, its density can actually decrease, resulting in larger flow volumes. This makes designing efficient piping systems more challenging, as engineers must carefully manage these volume changes to avoid performance losses.
Water reaches a critical point around 374°C and 22.1 MPa, where the distinction between liquid and vapor phases disappears. This unique state offers possibilities for highly efficient energy systems that leverage steam's thermodynamic characteristics under extreme conditions.
Increasing steam temperature not only boosts its energy content (enthalpy) but also impacts its volume. This can lead to increased demands for steam traps and condensate management, potentially adding complexity and operational costs if not properly considered during the design phase.
In saturated steam systems, even small pressure increases cause large temperature jumps. For instance, a 1 bar pressure rise can increase saturation temperature by roughly 45°C. This relationship necessitates precise control to prevent overheating and ensure efficient heat transfer.
The phenomenon of "flash" steam occurs when high-pressure steam is suddenly released to a lower pressure, causing instant water vaporization and rapid expansion. While this can be utilized for energy recovery, it must be carefully controlled to prevent damage to system components.
Power plants using superheated steam can achieve thermal efficiencies close to 45%, but this depends on maintaining a precise balance of pressure and temperature. Deviation from these optimal conditions can lead to significant drops in thermal performance, highlighting the delicate balance between efficiency and potential problems.
Steam mass flow rate is heavily influenced by both temperature and pressure, and the relationship isn't linear. Small variations in either parameter can cause major shifts in flow characteristics and heating capacity.
In practical scenarios, a 10°C increase in steam temperature can improve heat transfer by 5-10%. However, increasing steam temperature requires added precautions to prevent thermal stress and material failure within the system.
When rapid pressure changes or emergencies occur, steam bubbles can form, leading to cavitation. This can damage equipment and disrupt flow, so smooth transitions in pressure and temperature are vital.
Superheaters and reheat cycles can enhance steam system efficiency, but they increase complexity and initial investment costs. Striking a balance between return on investment and the technical requirements of these systems is crucial for engineers seeking to optimize steam flow.
Optimizing Steam Flow for Enhanced Heating Capacity A Thermodynamic Analysis - Overcoming Common Challenges in Steam Flow Regulation
Managing steam flow effectively is key to optimizing heating capacity, but it's not without its hurdles. Efficient control of steam flow relies heavily on the performance of turbine valves. These valves play a crucial role in both turbine cycle efficiency and the overall power plant's ability to generate power, making precise control paramount. However, developing accurate models for valve operation is a challenge, especially under varying conditions. Furthermore, in ultra-supercritical power plants, the drive towards higher steam parameters can result in operational bottlenecks due to thermodynamic limitations and substantial system losses. These challenges point towards the need for a thorough review and refinement of thermodynamic cycles to avoid these inefficiencies. Implementing sophisticated control strategies like fractional-order proportional-integral-derivative (FOPID) controllers can offer improvements to pressure regulation in heat exchangers, allowing for better heat transfer and more efficient energy use. Lastly, using techniques like computational fluid dynamics (CFD) to analyze unsteady, compressible steam flow provides a path to understand the impact of system design on performance, ultimately contributing to more effective heating capacity. Understanding and addressing these aspects is vital for achieving optimal heating capacity from steam systems.
1. The distinction between saturated and superheated steam has a major impact on thermal efficiency. Superheated steam offers more energy, but it requires careful management to prevent overheating during heat transfer. This is something that needs to be understood in a variety of process conditions.
2. The way steam changes phases, especially near its critical point, can be rather unexpected. At the critical point, the liquid and gas phases merge, creating unique thermodynamic opportunities for developing more energy-efficient steam-based systems. This point needs further examination.
3. Even a small pressure drop in steam pipes can lead to significant energy loss over time and increase operating costs. This suggests that careful system design and maintenance are important for overall efficiency and economic considerations.
4. At high pressures, steam behaves in a non-linear way, with small changes in pressure leading to substantial variations in density and volume. This creates complexities in designing efficient piping systems because of the variable flow characteristics.
5. A 10°C rise in steam temperature can boost heat transfer by 5-10%. However, this also increases the risk of thermal stress and potential material failure, making operational procedures more complex.
6. Managing condensate effectively is crucial for optimal steam system performance because water buildup can significantly reduce the efficiency of heat transfer. Furthermore, if condensate isn't removed properly, it can cause downtime and substantial energy losses.
7. The Joule-Thomson effect allows for energy recovery during pressure drops in steam systems, contributing to overall efficiency. However, it requires careful management to avoid cavitation and other related problems that can damage a system.
8. While higher steam velocities enhance heat transfer rates, they can also cause destructive water hammer effects. Balancing these factors in the design process is essential for maximizing heating capacity while mitigating the risks of high-pressure conditions.
9. Ensuring uniform heating in large systems can be difficult since variations in steam velocity profiles can lead to uneven heating (hot and cold spots). This issue highlights the importance of sophisticated design methods to distribute heat effectively.
10. Achieving thermal efficiencies above 30% in steam systems is often challenging due to factors such as friction, imperfect fluid flow, and other losses within the system. To push towards the theoretical efficiency maximum of 40-50%, we need designs that factor these challenges into the equation.
Optimizing Steam Flow for Enhanced Heating Capacity A Thermodynamic Analysis - Advanced Techniques for Maximizing Heating Capacity
Beyond the foundational principles of steam flow optimization, researchers and engineers are exploring more advanced techniques to further enhance heating capacity. Methods like adjusting pressure within Heat Recovery Steam Generators (HRSGs) are being explored to minimize energy losses and refine heat transfer. Implementing cutting-edge combustion technologies holds the potential for boosting the efficiency of steam boilers, contributing to a more sustainable energy future. Interestingly, genetic algorithms are being used to fine-tune the design of steam flow nozzles, an effort to create better atomization of steam, minimizing the energy losses that arise from droplet formation. Additionally, the development of systems like High-Temperature Cascade Heat Pumps (HTCHPs) highlights a growing desire to make better use of low-grade heat sources, a move towards more sustainable steam applications. While these advanced strategies provide pathways for improved heating capacity, the complex interactions within these systems necessitate ongoing research to understand the limitations and potential downsides of each method. The goal is to tailor these techniques to specific contexts and diverse operational environments for maximum benefit.
1. The Joule-Thomson effect, where steam cools during expansion in turbines, can significantly impact its heat transfer capability. Understanding this effect is crucial when optimizing thermodynamic cycles for better efficiency, particularly in systems designed for peak performance. It's an aspect that's often not fully considered in basic thermodynamic models.
2. While superheated steam carries a higher energy content due to its increased temperature, it also loses its moisture content, which can affect heat exchange rates considerably. This transformation highlights the need for precise thermal management in applications requiring specific heat transfer behaviors. One might need to adjust the materials or components accordingly to ensure the system performs as intended.
3. Maintaining the right pressure and temperature profiles is central to maximizing the thermodynamic efficiency of a steam system. However, the strong correlation between these parameters is sometimes overlooked, leading to suboptimal system operation and potentially higher energy consumption. This indicates that engineers should not approach pressure and temperature adjustments in isolation, but instead optimize them in tandem to maximize overall system efficiency.
4. Rapid steam expansion during pressure drops can cause issues like cavitation and component cycling, which are important safety considerations. This underscores the need for careful system design and operational procedures to mitigate such risks. These issues can lead to rapid degradation of equipment or can even lead to outright failure of certain parts of the system, so it is best to consider these things during the initial design stage.
5. The critical point of water, where the liquid and gas phases merge, represents a unique opportunity for optimizing steam systems. At this point, steam's properties change in ways that could lead to higher efficiency in advanced systems. It appears to be a frontier of steam system design, requiring novel approaches to system design and operation. Further research and experimentation will likely reveal new techniques for leveraging these changes.
6. Even slight impurities in the steam can cause scaling in heat exchanger tubes, which hinders heat transfer. Regular cleaning and maintenance procedures are crucial to prevent the formation of these deposits and preserve the heat transfer capabilities of a steam system. The importance of this point can't be understated as the cost of this type of maintenance can be quite high if it is neglected.
7. The design of steam piping systems needs to carefully consider variations in steam density resulting from temperature and pressure fluctuations. Failure to do so can make flow management more complex and introduce inefficiencies that might be avoided with a more comprehensive approach to piping system design. We need more rigorous computational tools that can assist engineers in design and operations.
8. Advanced CFD simulations offer valuable insights into the complex dynamics of steam flow, which can lead to improvements in system design and potentially prevent the development of problematic behaviors. These techniques may play a major role in optimizing future generations of steam-based heating systems. The accuracy and robustness of these computational tools need ongoing scrutiny, though.
9. Thermal siphoning, a consequence of poor steam venting, can cause localized overheating and result in energy losses. Appropriate venting strategies can mitigate this issue, but understanding the causes and effects of this problem is key to preventing it. These sorts of problems are difficult to diagnose, but their adverse effects can be quite costly.
10. Insulating steam lines is a straightforward yet often overlooked way to improve efficiency. Reducing heat loss from steam pipes can increase the overall thermal efficiency of a plant. The potential gains suggest that thermal management is an essential aspect of steam system design, especially when operating costs are a concern. While improvements seem obvious, the practicality of implementation can vary widely between different applications.
More Posts from patentreviewpro.com: