Nickel The Metal Powering Advanced Alloys and Industrial Innovation
Nickel The Metal Powering Advanced Alloys and Industrial Innovation - Nickel's Role in Additive Manufacturing Techniques
Nickel's importance in additive manufacturing stems from its role in high-performance alloys, specifically superalloys. These alloys are prized for their ability to withstand extreme temperatures, resist corrosion and oxidation, making them ideal for demanding applications. Additive manufacturing processes, such as Selective Electron Beam Melting (SEBM) and Selective Laser Melting (SLM), have become key to creating complex shapes and geometries previously difficult or impossible with conventional techniques. These methods address the cost and limitations of subtractive manufacturing approaches for nickel-based materials.
Furthermore, the Direct Energy Deposition (DED) process within additive manufacturing opens doors to repairing and enhancing existing components crafted from nickel-based alloys. This capability extends the lifespan and utility of parts, providing significant value across various industries. The design freedom and flexibility offered by additive manufacturing are a major reason why nickel alloys are becoming a material of choice for intricate structures, like turbine blades with integrated cooling channels. Ongoing research and development continues to improve the microstructure and mechanical properties of nickel-based parts produced through additive manufacturing. The advancements made in this area highlight the integral role of these alloys in sectors including aerospace and energy, paving the way for innovation and pushing the boundaries of engineering and design.
Nickel's role in additive manufacturing extends beyond its use in superalloys. It's increasingly seen as a vital component in various additive manufacturing techniques, influencing the properties of the final product in subtle and significant ways. For instance, in titanium-based powders, nickel boosts strength and temperature resistance—a boon for aerospace components. Similarly, in cobalt-chromium alloys often used in medical implants, nickel contributes to better wear and corrosion resistance.
Additive manufacturing methods like Selective Electron Beam Melting (SEBM) and Selective Laser Melting (SLM) are well-suited to produce complex parts from nickel-based alloys. While these techniques are advantageous, they present a unique set of challenges. The fusion process itself impacts the material's microstructure, leading to phase transformations and solidification patterns that significantly affect the resulting mechanical properties. Understanding these complexities is crucial for producing consistent and reliable results.
The freedom offered by additive manufacturing enables the creation of intricate geometries, especially in aerospace applications like jet engine turbines with internal cooling channels. However, developing optimized alloy compositions and implementing precise defect control are key to fully realizing the potential of these design possibilities. Further, it seems the ability to lower density in nickel-containing alloys during SLM is worth exploring, as it could lead to lighter components without compromising structural integrity.
Interestingly, it seems nickel's impact goes beyond strength and temperature resistance. Research suggests that adjusting nickel content can impact grain size and texture, influencing the final mechanical properties. Similarly, nickel seems to play a crucial role in the layer adhesion within powder bed fusion techniques, directly affecting the final printed part's overall strength. This area, though, warrants further exploration.
The field is moving toward exploring nickel-based metal matrix composites, which could lead to exceptionally durable materials for demanding environments. One could say the unique melting characteristics of nickel in processes like laser sintering contribute to a more controlled and uniform microstructure, making it a potentially preferable alloying element in some scenarios. Though still nascent, this avenue could be pivotal for pushing the boundaries of material performance within additive manufacturing.
Nickel The Metal Powering Advanced Alloys and Industrial Innovation - Applications of Nickel-based Superalloys in Aerospace
Nickel-based superalloys are crucial for aerospace applications, especially within the demanding environment of jet engines. These alloys are particularly important in the construction of turbine disks and blades, which experience incredibly high temperatures and stresses. The remarkable combination of high-temperature strength and toughness found in these alloys is what makes them suitable for these demanding roles, contributing to enhanced gas turbine efficiency.
The pursuit of greater engine performance has driven the development of advanced nickel-based superalloys. Single-crystal superalloys, such as LEK94 and MC2, are designed specifically to maximize mechanical properties for high-pressure turbine blades. This targeted development exemplifies the continuous efforts to improve the performance of these alloys.
Beyond established alloy types, research continues to push the boundaries of superalloy capabilities. Current research is exploring local phase transformation strengthening methods as a promising path towards even more resilient and efficient nickel-based alloys. As aerospace engineering continues to advance, the development and implementation of novel superalloy compositions are expected to remain paramount in enabling future advancements in aircraft engines.
Nickel-based superalloys are indispensable in aerospace, particularly within the demanding environment of jet engines, due to their ability to maintain structural integrity at extremely high temperatures, often exceeding 1000°C. This remarkable performance is a consequence of their composition, typically featuring over 50% nickel, which contributes to their exceptional microstructural stability. The presence of gamma (γ) and gamma prime (γ') phases plays a vital role in resisting deformation under stress, ensuring the material's reliability.
Furthermore, these alloys exhibit excellent resistance to oxidation and corrosion. This is largely attributed to the formation of a protective oxide layer during high-temperature exposure. This layer acts as a shield against the harsh environments encountered in aerospace applications, significantly reducing material degradation and ensuring longer component lifespans. We see evidence of this in commercial aircraft engines where alloys like Inconel and Rene are extensively used in critical components like turbine blades, combustion liners, and casings. These components are exposed to cyclic thermal and oxidative stresses, and the alloys' resilience in these conditions is crucial for engine reliability.
Manufacturing these alloys into complex shapes, like turbine blades with intricate cooling channels, requires advanced techniques such as investment casting. These processes are essential for optimizing thermal efficiency and improving engine performance, but they highlight a drawback. Nickel-based superalloys, while incredibly useful, are quite challenging to machine due to their inherent toughness and high work-hardening tendencies. This can result in increased tool wear and contribute to higher manufacturing costs.
To address the need for ever-improving performance in aerospace applications, researchers have invested heavily in understanding the behavior of these materials under cyclic loading. Creep and fatigue resistance are of particular interest because they are crucial factors determining long-term component durability. This research often involves exploring the effects of trace elements like aluminum and titanium, which are added to enhance high-temperature strength. However, careful control is essential to avoid the formation of detrimental phases that could negatively impact the alloys' overall mechanical integrity.
Casting practices have seen notable advancements, with techniques like directional solidification and single-crystal casting gaining prominence. These methods enhance mechanical properties while simultaneously reducing defects, thus extending the service life of these critical components. The need for improved performance in existing and future aircraft designs, particularly with advancements in aerodynamics and propulsion technologies, continues to drive the development of new nickel-based superalloys. The quest for greater efficiency and performance remains a significant driving force in this field.
Nickel The Metal Powering Advanced Alloys and Industrial Innovation - Nickel-containing High-Entropy Alloys Pushing Material Science Boundaries
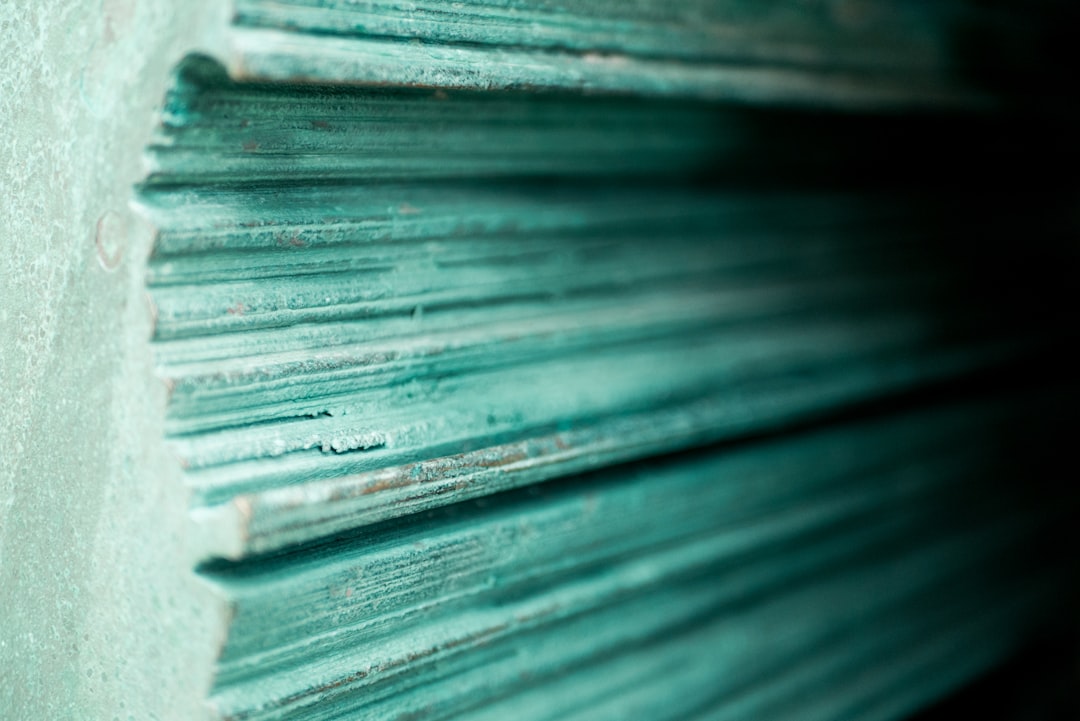
Nickel-containing high-entropy alloys (HEAs) represent a significant advancement in materials science, showcasing exceptional mechanical performance. Their strength, toughness, and resistance to corrosion are notable features, making them a focus of research and development. The concept of HEAs, introduced around 2004, has gained traction due to their unique ability to exhibit a combination of desirable properties, stemming from their intricate atomic structures. The diverse design possibilities within HEAs have led to classifications like complex concentrated alloys and medium entropy alloys, each impacting how these materials are processed and the resulting microstructure.
Recent breakthroughs have shown that modifying nickel content within HEAs can influence their microstructure and mechanical characteristics, while also creating possibilities for manufacturing nanostructured versions of these alloys. These developments have implications for a variety of applications, including the development of more efficient catalysts and even components within the aerospace industry. Despite the promising potential of HEAs, their complex nature necessitates continued research to fully understand and optimize their fabrication and performance, thereby unlocking their true potential for future innovations. The challenges of working with these complex materials and developing reliable processing methods are hurdles that need to be addressed for these alloys to fully realize their potential.
Nickel-containing high-entropy alloys (HEAs) are gaining traction in materials science due to their unique combination of elements in roughly equal proportions. This composition leads to a high degree of randomness in the atomic arrangement, which helps stabilize both body-centered cubic (BCC) and face-centered cubic (FCC) crystal structures. This, in turn, can result in improved strength and ductility compared to conventional alloys.
Many nickel-based HEAs demonstrate excellent resistance to wear and tear, even outperforming some established nickel superalloys in certain applications. It seems this enhanced wear resistance might stem from the alloy's complex microstructure and the formation of specific phases that impede surface degradation.
Interestingly, some nickel-containing HEAs display remarkable fatigue resistance. This is particularly intriguing because cyclic loading can be a significant challenge for materials in aerospace or automotive applications. The fine-grained microstructures present in some of these HEAs could play a role in hindering crack propagation and thus boosting fatigue resistance.
The ability of nickel-based HEAs to withstand high temperatures is another interesting characteristic. They can often maintain their mechanical properties at temperatures that exceed those of conventional superalloys. This enhanced thermal stability offers potential for applications in demanding environments, such as gas turbines, where materials experience extreme temperatures without significant degradation.
The versatility of nickel HEAs also extends to compositional design. Researchers are exploring ways to incorporate lighter elements into the mix, aiming for a good balance between strength and weight. This is a crucial area, particularly for applications where reducing component weight without sacrificing structural integrity is a primary design constraint.
Processing methods for nickel HEAs like laser powder bed fusion are enabling the production of parts with complex shapes while maintaining control over the microstructure. This combination of design flexibility and processing control could be a game-changer, leading to both improved design and enhanced mechanical performance.
It seems nickel's presence in HEAs influences the stability of phases and encourages the formation of desirable microstructural features, like precipitates that increase strength. Understanding the specific role of nickel in these alloys is essential for tailoring their properties to meet the requirements of various applications.
Some studies have found that certain nickel-containing HEAs can exhibit superelasticity—a feature not commonly found in traditional nickel alloys. If this characteristic is indeed present, it could be very beneficial in applications requiring large deformation prior to failure. This property could be helpful in areas such as automotive crash components or in anti-vibration technologies.
Unlike some traditional alloys, nickel HEAs can form a relatively homogeneous structure during solidification, thereby reducing defects and improving overall mechanical performance. This homogeneity is advantageous when high reliability is a major requirement in final components, which could prove valuable in a range of manufacturing processes.
Research is ongoing into the behavior of nickel-containing HEAs in hydrogen-rich environments. These alloys' potential resistance to hydrogen embrittlement could provide a considerable edge in future energy technologies. This is especially important for materials used in fuel cells or hydrogen storage systems where maintaining material integrity under challenging conditions is crucial.
Nickel The Metal Powering Advanced Alloys and Industrial Innovation - Direct Energy Deposition for Repairing Nickel-based Components
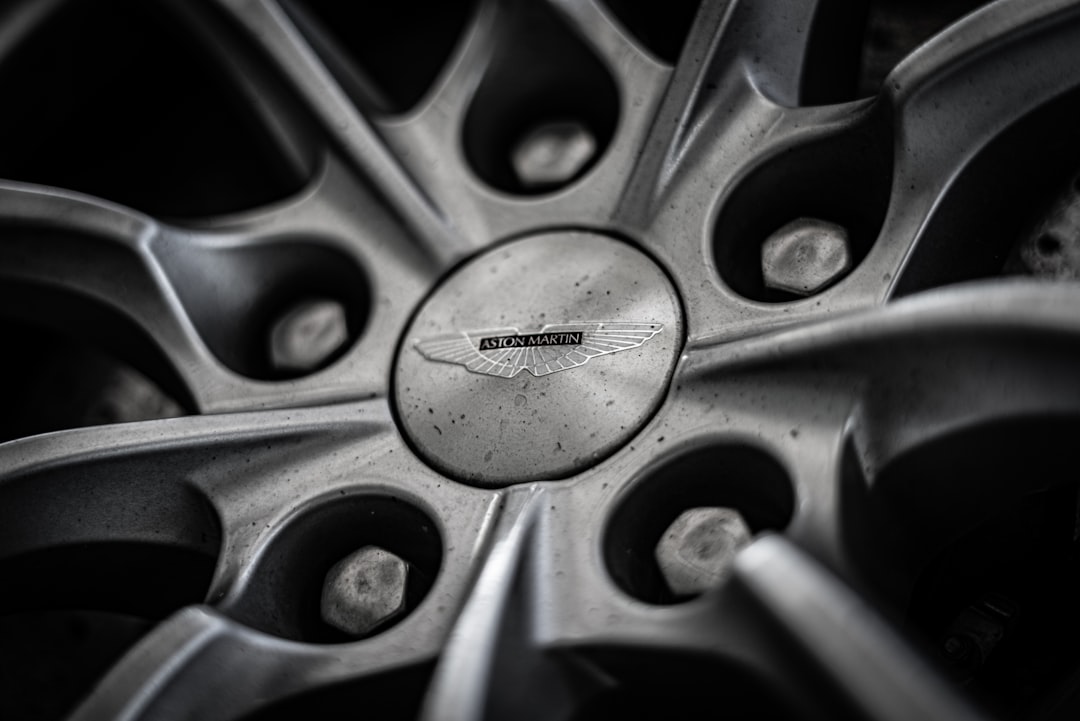
Direct Energy Deposition (DED) stands out as a promising method for repairing components made from nickel-based alloys. Compared to traditional repair techniques, DED offers increased efficiency, making it a compelling alternative. Beyond simply repairing, DED also helps improve the performance of these components while potentially lowering costs, making it attractive across many industries. Despite the benefits, DED faces challenges, particularly with cracking. Understanding how and where cracks form during the DED process remains a key area of research. DED's ability to create complex, nearly-final-shape parts from nickel superalloys highlights its potential within advanced manufacturing. Further research will be needed to ensure DED-repaired parts meet rigorous quality and performance standards, optimizing the material's microstructure and its overall mechanical integrity.
Direct Energy Deposition (DED) stands out as a promising additive manufacturing approach, particularly when compared to powder bed fusion techniques, offering greater efficiency in the process. Its utility extends beyond creating new parts, proving quite valuable for repairing nickel-based components. This not only enhances their performance but can also lead to substantial cost reductions.
However, a major hurdle in DED of nickel-based superalloys is crack formation. Researchers are actively trying to understand where and how these cracks form. It seems the solidification process, the evolving microstructure, and stress concentration all play a big part in the initiation of cracks.
One exciting application of DED is the creation of almost fully-formed components using nickel superalloys. The superior properties of these alloys, including their ability to withstand high temperatures, make them ideal candidates for this approach.
DED's influence extends into advanced manufacturing, playing a key role in the so-called fourth industrial revolution by allowing us to fabricate complex metallic parts. There's a growing body of work exploring wire-arc DED for producing hybrid structures using nickel-based superalloys, notably IN718 and IN625.
It appears the specific microstructural features of some nickel-based superalloys, like IN718, contribute to their weldability, making them particularly suitable for additive manufacturing. This is important since only a small fraction (roughly 10%) of nickel-based superalloys produced actually end up as finished products, underscoring the need for efficient manufacturing approaches like DED.
DED provides a powerful tool for repairing existing nickel-based components, making it a broadly applicable technology across a variety of engineering fields. This is intriguing, considering the cost and time it can take to produce and fabricate new parts.
While promising, there are many aspects of the DED process which need further investigation and optimization. Achieving the best results relies heavily on managing the process carefully and ensuring the desired mechanical properties are achieved. Understanding the interplay of various parameters during the DED process—like laser power and metal feed rates—will continue to drive innovation in this field.
Nickel The Metal Powering Advanced Alloys and Industrial Innovation - Challenges in Processing Nickel-based Superalloys
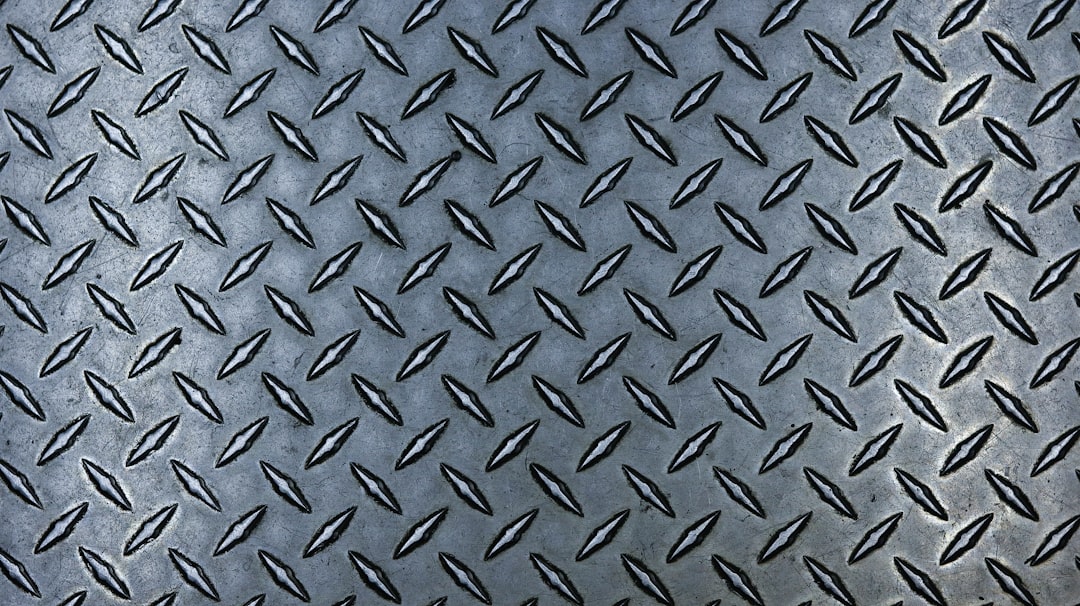
Nickel-based superalloys, while offering exceptional properties like high-temperature strength and corrosion resistance, present unique challenges during processing, impacting their overall efficiency and cost-effectiveness. Machining these materials is particularly problematic due to their inherent toughness, leading to increased tool wear and manufacturing expenses. This difficulty can be a major obstacle when producing complex shapes needed for demanding applications, like aerospace components.
Although additive manufacturing methods like Direct Energy Deposition offer promise in repairing and producing components with complex designs, they introduce new challenges. For example, the rapid solidification during these processes can result in crack formation, which requires careful process control and ongoing research to mitigate. Moreover, the overall yield of nickel-based superalloys into usable parts is surprisingly low—only a fraction reaches the stage of finished products. This highlights the significance of improving processing methods and further understanding the alloy's behavior during manufacturing. Overcoming these hurdles through continued innovation is crucial to ensuring nickel-based superalloys can fulfill their potential in high-performance applications, especially in industries like aerospace where reliability is paramount.
Nickel-based superalloys, while remarkably robust, present unique challenges during processing due to their complex behavior. The solidification process often results in the formation of unexpected phases, which can alter key mechanical characteristics like strength and creep resistance, making it difficult to predict and control their performance.
The high work-hardening tendency of these alloys contributes to increased tool wear during conventional machining, requiring specialized techniques and materials. This factor leads to extended processing times and higher costs, reducing the overall efficiency of traditional subtractive manufacturing methods.
Furthermore, the microstructure of nickel-based superalloys, especially during additive manufacturing, is greatly influenced by the cooling rate. Achieving consistent mechanical properties across components becomes a challenge due to the variations in cooling experienced during the process, highlighting the need for meticulous thermal management throughout fabrication.
The composition of these alloys plays a crucial role in determining their performance at high temperatures. While elements like aluminum and titanium improve high-temperature strength, they can also make the alloys more prone to brittle fracture if not carefully balanced. Optimizing the alloy composition is critical for achieving superior performance without compromising integrity.
Another processing concern stems from the residual stresses that build up during additive manufacturing. These stresses can lead to unwanted warpage or distortion in the final components, demanding careful consideration during the design and process phases. Often, additional steps like post-heat treatment are required to relieve these stresses and maintain the desired shape and dimensions.
An intriguing area of research is utilizing nickel's distinctive melting behavior in laser-based processes. This enables better control over microstructural features, but it also increases the complexity of reliably predicting the material's behavior. Developing more advanced models becomes critical to ensure consistency and performance.
In Direct Energy Deposition (DED), managing heat input is paramount to minimizing defect formation. Excessive heat can lead to excessive dilution of the substrate material, potentially compromising the alloy's performance. Understanding and controlling these thermal effects is vital for maintaining component integrity.
Interestingly, nickel-based superalloys can undergo phase transformations that influence their mechanical properties irrespective of the fabrication method. This inherent unpredictability underscores the need for a comprehensive understanding of the underlying thermodynamic principles to effectively tailor the materials' behavior.
The remarkable performance of nickel-based alloys in extreme environments comes at a cost. Processing them often requires specialized equipment that can withstand high temperatures and prevent oxidation during the fabrication stage. This aspect of processing increases both the capital costs and the operational complexity of using these materials.
Finally, incorporating rare earth elements into nickel-based superalloys has shown promise in enhancing their resistance to high-temperature oxidation, an important attribute for aerospace applications. However, the limited availability and cost of these elements pose challenges for large-scale adoption.
Nickel The Metal Powering Advanced Alloys and Industrial Innovation - Nickel's Contribution to Clean Energy Technologies
Nickel's role in the shift towards cleaner energy sources is becoming increasingly prominent. Its high purity and unique characteristics, such as its resistance to corrosion and its ability to withstand high temperatures, are vital for technologies aiming to reduce carbon emissions. This includes applications in electric vehicle batteries, hydrogen production, and geothermal energy systems. The anticipated surge in demand for nickel by 2030 underscores its importance in the future of energy, but also highlights the need for responsible practices in mining and refining. Sustainable extraction and processing methods are crucial to minimize the environmental footprint of nickel production, as it becomes more central to a sustainable energy future. The diverse ways nickel can be utilized in clean energy generation and storage emphasize the importance of developing innovative approaches to its supply chain. It's clear that nickel is a crucial metal in the world's transition to cleaner and more sustainable energy systems.
Nickel's role in the burgeoning clean energy sector is becoming increasingly prominent, primarily due to its unique blend of properties. For instance, nickel has long been a core component in battery technologies like nickel-cadmium (NiCd) and nickel-metal hydride (NiMH) systems. The high energy density and cycle stability of these batteries make them important players in energy storage, though perhaps not as prominent as lithium-ion batteries in today's market.
In the realm of fuel cells, nickel's catalytic capabilities, particularly within alkaline fuel cells, are essential. It effectively facilitates the chemical reactions needed for hydrogen generation and usage, potentially improving overall energy conversion rates. Its application in water electrolysis for hydrogen production is similarly crucial. Nickel alloys prove particularly valuable here, resisting harsh operating conditions and ensuring the durability of these systems.
Nickel's high thermal conductivity lends itself well to technologies like concentrated solar power (CSP). Heat transfer is critical for efficiently harnessing solar energy, and nickel's inherent ability to conduct heat can contribute to improved performance.
Moving beyond these established applications, research shows that incorporating nickel into certain lithium-ion battery formulations can boost energy density and efficiency, potentially leading to lighter and more potent batteries. This could have substantial impacts across a variety of applications including electric vehicles and portable electronics. Nickel also finds use in hydrogen storage, often as part of metal hydride systems. Here, it helps improve the hydrogen absorption and release process, leading to more effective energy storage solutions.
It is interesting that nickel-based superalloys exhibit a high resistance to hydrogen embrittlement. This is particularly valuable in the context of hydrogen fuel systems as it aids in maintaining the structural integrity of components operating in harsh environments, boosting reliability and safety. Beyond this, nickel's magnetism could play a role in emerging green energy technologies, such as magnetic refrigeration, providing a potentially more eco-friendly approach to cooling.
Nickel's catalytic properties further extend to methanol reforming, a process that transforms methanol into hydrogen. This serves as a useful method for providing hydrogen to fuel cells. The broader utility of nickel within fuel cell technologies through different processes shows its versatility.
Finally, nickel's contribution isn't limited to chemical or energy-related processes. It helps strengthen alloys used in wind turbine components, allowing for the robust construction of structures that can endure fluctuating wind loads while maximizing energy capture.
Despite the exciting prospects for nickel's use in clean energy, there are aspects that warrant caution and further research. Supply chain challenges and the environmental impact of nickel mining are critical considerations as the demand for nickel surges. Exploring more sustainable extraction and refining methods is key to ensuring that nickel continues to play a vital part in shaping a cleaner energy future.
More Posts from patentreviewpro.com: