New Developments in Adjustable Friction Flange Bearings for Industrial Applications
New Developments in Adjustable Friction Flange Bearings for Industrial Applications - Evolution of Adjustable Friction Flange Bearings since 2020
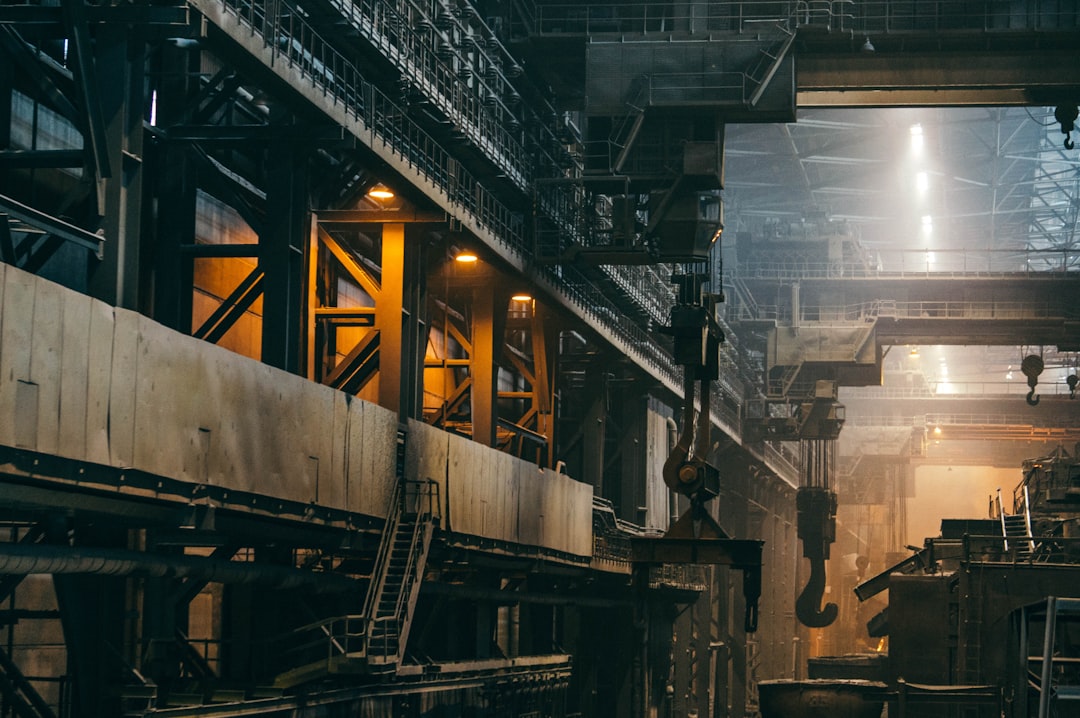
Since 2020, the landscape of adjustable friction flange bearings has been reshaped by a drive towards heightened performance and flexibility. This shift has spurred the development of bearings that can better handle the demanding conditions of modern industrial applications. A key focus has been on utilizing materials that are both durable and efficient, with new polymers and composites proving to be particularly effective. These advancements are evident in the rise of active bearing control technologies, which allow for real-time adjustments that further improve efficiency and performance. The increasing customization of these bearings reflects a growing awareness of the unique challenges presented by specific applications. This trend allows manufacturers to tailor bearings to the needs of individual industries, providing optimal solutions for specific high-speed and high-load requirements. This emphasis on customization and enhanced performance represents a clear commitment to the advancement of adjustable friction flange bearings and their integral role in modern industrial settings.
The last few years have seen a fascinating shift in the development of adjustable friction flange bearings. It’s not just about pushing load limits; there's a real focus on refining performance in nuanced ways.
One of the most striking changes is the use of nanotechnology to create friction materials with incredible wear resistance. It's quite remarkable how this translates into longer service lifespans for the bearings. It's a huge step forward for reliability in demanding industrial applications.
Another interesting development is the use of computer simulations to fine-tune designs. This helps engineers to precisely predict how the bearings will perform under a wide range of loads. It's incredibly efficient and reduces the need for extensive physical testing. This approach has drastically shortened the development cycle for new bearing designs.
The integration of smart sensors within these bearings is also a key trend. Real-time monitoring is becoming increasingly crucial for industrial operations, and these sensors allow for predictive maintenance, minimizing downtime. It’s like having an early warning system for potential problems, allowing for interventions before they become major issues.
It’s quite surprising how 3D printing has come to the fore in this field. It’s offering a great deal of flexibility for designing custom flange configurations, leading to more optimized solutions. Plus, the ability to reduce material waste is a major advantage in the current climate.
We are also seeing the emergence of hybrid lubrication systems, combining oil and grease for optimized performance. These systems seem to improve performance and significantly extend the time between maintenance cycles. It's a clever solution that potentially improves both efficiency and cost-effectiveness.
The use of CAE tools has allowed for much more thorough analysis of complex loading scenarios. This has led to more robust designs that can withstand dynamic forces, making the bearings even more reliable.
Finally, there's a growing interest in using bio-based lubricants in conjunction with adjustable friction flange bearings. This approach could lead to lower friction and enhanced performance, while also addressing concerns about traditional lubricant selection. It's an exciting development that could potentially revolutionize the industry.
Overall, the field of adjustable friction flange bearings is moving beyond traditional load-carrying capabilities and focusing on innovations that deliver greater efficiency, durability, and precision. It will be interesting to see what further developments emerge in the years to come.
New Developments in Adjustable Friction Flange Bearings for Industrial Applications - Key Design Improvements in Water and Dirt Resistance
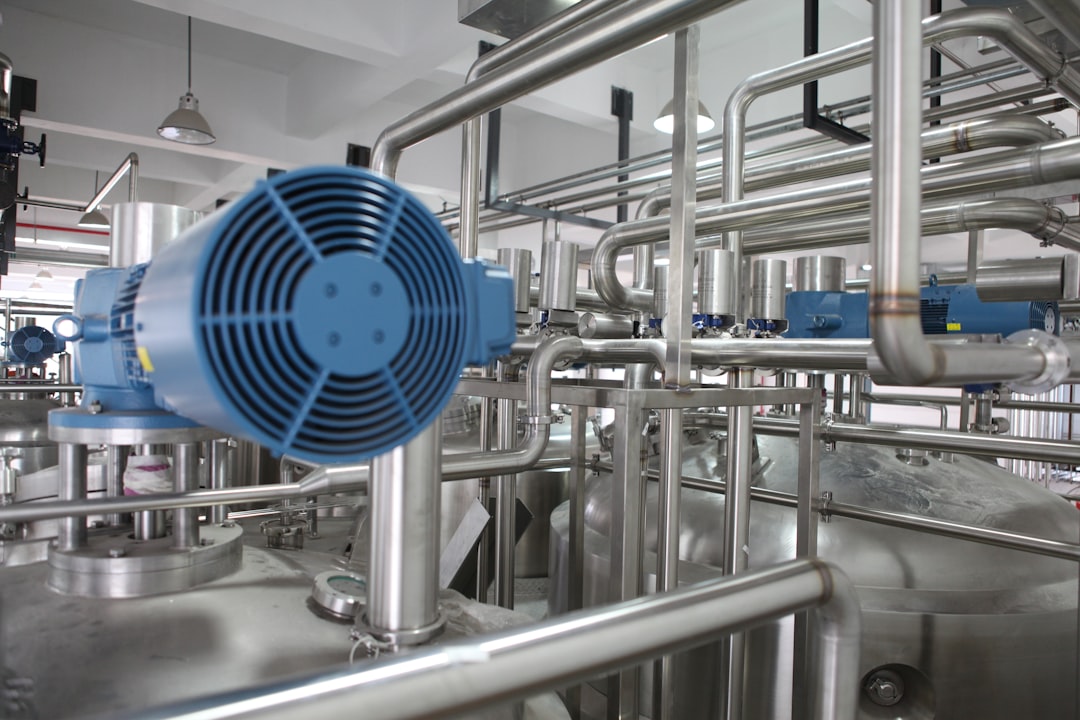
The pursuit of improved performance in adjustable friction flange bearings extends beyond simply increasing load limits. A key focus is on enhancing water and dirt resistance, critical in many industrial environments.
Engineers are developing sophisticated surface treatments and coatings to address the challenges posed by water and dirt. These modifications not only lengthen the lifespan of the bearings but also ensure consistent operation by minimizing the ingress of contaminants. Emerging innovations like reactive wear protection strategies and advanced lubrication systems are helping to address the wear and tear caused by exposure to water and dirt. These developments are essential for ensuring that adjustable friction flange bearings can perform reliably in demanding conditions, while maintaining operational efficiency.
The quest for more robust and adaptable adjustable friction flange bearings continues to drive innovations in water and dirt resistance. It's not just about keeping the elements out; it's about ensuring that these bearings can withstand even the most demanding environments while maintaining peak performance.
One interesting development is the emergence of new polymers for sealing. These materials are being engineered with unique molecular structures, offering greater flexibility and resilience against extremes of temperature and corrosive chemicals. This translates to significantly longer bearing lifespans, especially in harsh environments.
Another intriguing aspect is the redefinition of IP ratings. Advanced bearings are now able to resist not only water and dust but also a range of potentially hazardous substances. This opens up new possibilities for their application in industries like food processing and pharmaceuticals where contamination control is critical.
The incorporation of hydrophobic coatings has also been a significant breakthrough. These coatings use surface tension to repel water and dirt, making the bearings easier to clean and reducing wear. This is especially valuable in industries where dirt and moisture are prevalent.
Self-healing materials represent another fascinating development. These polymers can autonomously repair minor abrasions, effectively extending the lifespan of bearings exposed to abrasive environments. This technology is particularly promising for applications that would traditionally result in rapid material degradation.
Further exploration into micro-textured bearing surfaces is yielding positive results. By creating a labyrinth effect on the surface, these micro-textures trap dirt particles and water, preventing them from entering critical areas. This approach minimizes maintenance needs and improves reliability.
Electrochemical treatments are being employed to enhance the rust and corrosion resistance of bearing materials. These treatments are crucial for applications in marine and other moisture-rich environments where traditional bearings are prone to failure.
There are also innovations in pressure-responsive bearing designs. These bearings can automatically adapt to changes in environmental pressure, adjusting their sealing force accordingly. This adaptability ensures enhanced water and dirt resistance under fluctuating operating conditions.
Fluoropolymer lubricants are making their mark on the industry. They not only minimize friction but also enhance hydrophobicity, further reducing the risk of contamination from external substances.
The use of specific additives, such as graphene or ceramic particles, in bearing construction is adding another layer of protection. These additives enhance both mechanical strength and resistance to chemical and environmental wear, setting a new standard for industrial applications.
Finally, temperature-activated sealing systems are being developed. These systems respond to temperature fluctuations by expanding and contracting to enhance the barrier against dirt and moisture. This ensures optimized performance across varying operating climates.
While these are just a few of the exciting developments in water and dirt resistance for adjustable friction flange bearings, the future promises even more innovative solutions. The focus is on enhancing durability and reliability while minimizing maintenance needs, allowing for greater productivity and efficiency in industrial operations. It's a dynamic field that promises to deliver even more groundbreaking solutions in the years to come.
New Developments in Adjustable Friction Flange Bearings for Industrial Applications - Integration of Active Bearing Technology for Enhanced Rotor Dynamics
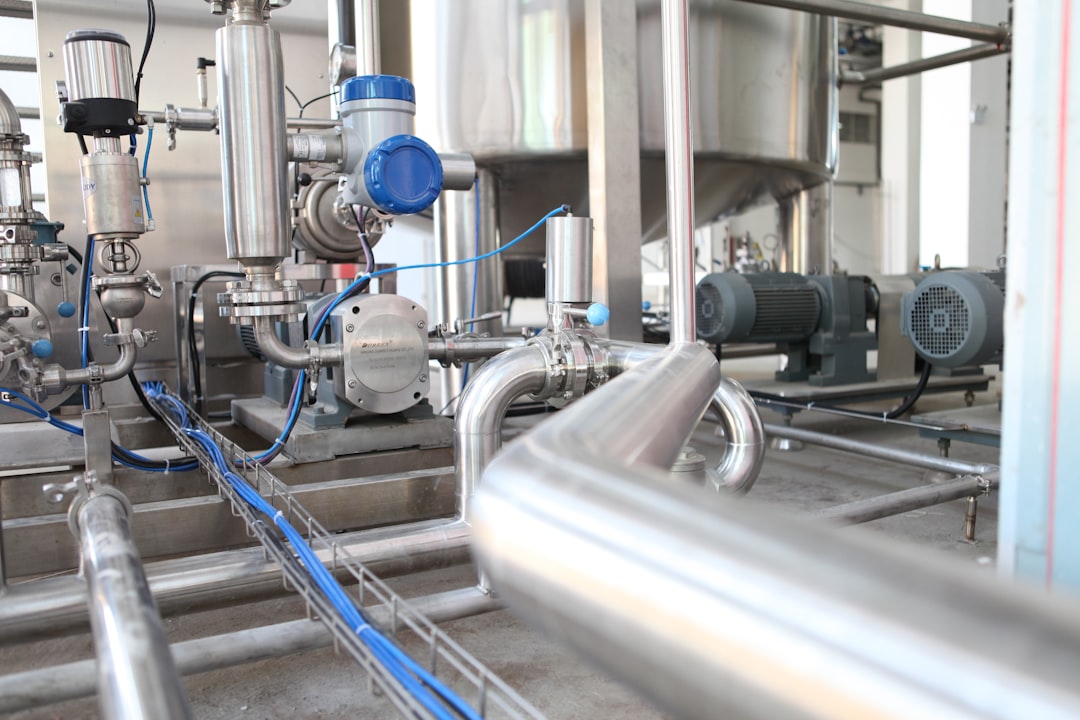
Active bearing technology, primarily utilizing Active Magnetic Bearings (AMB), is transforming the way we think about rotor dynamics. This is especially true in high-speed machinery. By eliminating contact between the bearing and the rotor, AMBs reduce friction and minimize maintenance needs. This leads to a significant improvement in overall efficiency and reliability. The development of a two-coil design further simplifies these systems, making them more suitable for high-speed applications. However, these benefits come with the challenge of controlling these complex systems. Maintaining precise rotor positioning within the air gap requires sophisticated digital control strategies, especially given the inherently non-linear nature of AMBs. Current research is focused on tackling these challenges through robust control mechanisms and addressing vibration issues, ultimately paving the way for a future where active bearing technologies significantly improve the stability and reliability of rotor systems in a range of industrial applications.
Active bearings are becoming increasingly important in modern engineering, particularly for high-speed machinery. They offer exciting opportunities for improving rotor dynamics by providing a more dynamic and adaptable control over the bearing system. Active Magnetic Bearings (AMBs), in particular, are gaining traction due to their ability to reduce friction and maintenance needs. This is achieved by providing contactless support for rotors, improving both the dynamic performance and operational success of the machine.
The design of AMBs can be further optimized using a two-coil system which simplifies the system and increases efficiency, especially in high-speed applications. However, AMBs require sophisticated control mechanisms to ensure precise rotor positioning within the air gap, particularly in rapidly rotating machines. This is challenging as the systems are inherently nonlinear and unstable, requiring careful modeling and digital control strategies.
Recent research has focused on developing innovative AMB designs, specifically for supporting thin-walled rotors. This includes incorporating distributed actuation and addressing the vibration issues that can arise from manufacturing asymmetries.
There's also significant ongoing research into adaptive and robust control systems for AMBs to improve the stability of rotor systems. The goal is to develop systems that can handle varying load conditions and environmental factors. For example, vibrational dynamics in active magnetic bearing systems are affected by the additional excitations introduced when supported on moving bases such as ships and vehicles.
The future of active bearing technology likely lies in developing multicoil AMB systems. This research aims to further enhance the overall performance of rotating machinery. It will be fascinating to see how these innovations impact the field of adjustable friction flange bearings in the years to come.
New Developments in Adjustable Friction Flange Bearings for Industrial Applications - Advancements in Lubrication Methods for Industrial Applications
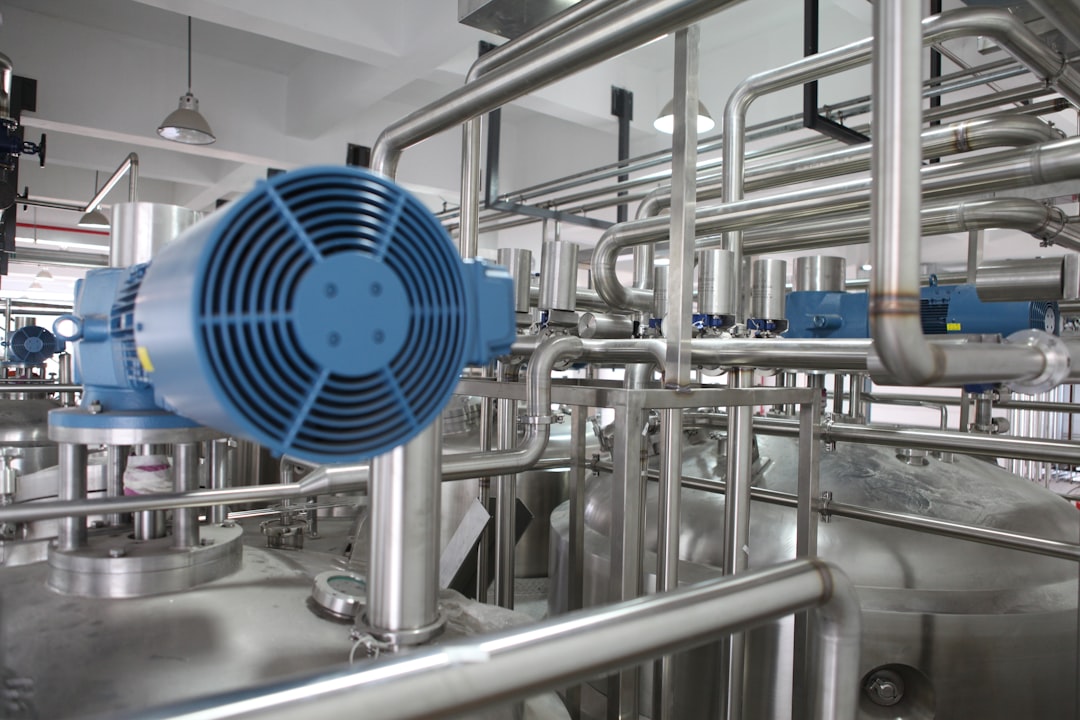
Advancements in lubrication methods are key to boosting the performance and longevity of industrial equipment. Recent developments are making waves with new technologies, from active lubrication using magnetic fluids to nanotechnology, which dramatically improves wear resistance in parts that rub together. But there are hurdles, like the cost of these advanced lubricants, which can make them a tough sell, and the need to make sure they work with existing materials. Innovations like bio-based lubricants and superlubricity techniques have the potential to totally change the game, but we're still figuring out how to use them in real-world situations. Overall, these new developments signal a major shift in lubrication technologies, promising better efficiency and a greener approach to industrial operations.
The field of industrial lubrication is experiencing a surge in advancements, pushing beyond conventional methods and exploring more sophisticated and efficient techniques. This quest for improved lubrication is driven by the need for greater performance, reduced maintenance needs, and optimized resource utilization. While traditional lubricants have served us well, the increasing demands of modern machinery and the push for environmental sustainability have created a need for innovation.
One of the most promising developments is the rise of molecularly engineered lubricants. These synthetic lubricants have a precisely tailored friction coefficient, leading to significant reductions in energy consumption – as much as 10% in some applications. This meticulous fine-tuning allows for the optimization of performance according to specific machinery and operating conditions, resulting in a more efficient and adaptable lubrication system.
Magnetic fluid lubrication is another captivating area of development. These systems rely on ferrofluids, fluids with magnetic properties, which can be manipulated with magnetic fields. This technology offers several benefits: it reduces friction, adapts to varying operating conditions automatically, and requires less manual intervention.
The integration of smart sensors into lubricants is revolutionizing how we approach lubrication monitoring. These "smart" lubricants contain micro-sensors that continuously monitor their viscosity and composition. This real-time monitoring ensures optimal lubrication properties, significantly extending the life of bearings and industrial machinery.
Artificial Intelligence (AI) is making its presence felt in the field of lubrication as well. AI algorithms analyze operational data, identifying patterns and predicting lubrication needs based on factors such as load and temperature. This predictive analysis promises to significantly reduce maintenance costs and the likelihood of unplanned downtime.
Bio-inspired lubrication techniques, drawing inspiration from natural lubricants like synovial fluid, are demonstrating outstanding performance. These bio-inspired lubricants offer superior lubricating properties, demonstrating significantly longer-lasting performance in extreme conditions – up to 50% longer than traditional lubricants.
Phase-change lubricants, materials that change phase from liquid to solid depending on temperature, represent another exciting development. This unique property provides enhanced performance stability under varying thermal conditions, especially crucial for high-speed applications where thermal fluctuations are common.
Electrorheological and magnetorheological fluids offer unprecedented customization in lubrication performance. These fluids react to electric and magnetic fields, respectively, allowing for on-demand adjustments of viscosity. This dynamic adjustability allows for the optimization of friction reduction during machine operation, resulting in a highly responsive and adaptable lubrication system.
Nanoparticles are proving to be highly effective in tailored friction management. These engineered nanoparticles, incorporated into lubricants, enhance load-bearing capabilities and dramatically reduce wear, proving particularly effective in high-stress environments.
Hybrid lubrication systems are showcasing their efficiency by combining the best of both worlds: conventional oils and modern greases. This approach allows for the utilization of the advantages of each type, ultimately extending the lifespan of bearings by as much as 30% compared to traditional methods.
Significant advancements are being made in optimizing cold start performance. Specialized low-temperature lubricants maintain fluidity, minimizing startup friction and wear – critical for equipment exposed to extreme temperature fluctuations.
The ongoing research and development in the field of industrial lubrication is generating a plethora of innovative approaches. These developments are set to revolutionize how we approach lubrication, leading to more efficient, reliable, and environmentally conscious industrial operations. It will be fascinating to witness what the future holds in this rapidly evolving field.
New Developments in Adjustable Friction Flange Bearings for Industrial Applications - Impact of New Materials on Bearing Performance and Durability
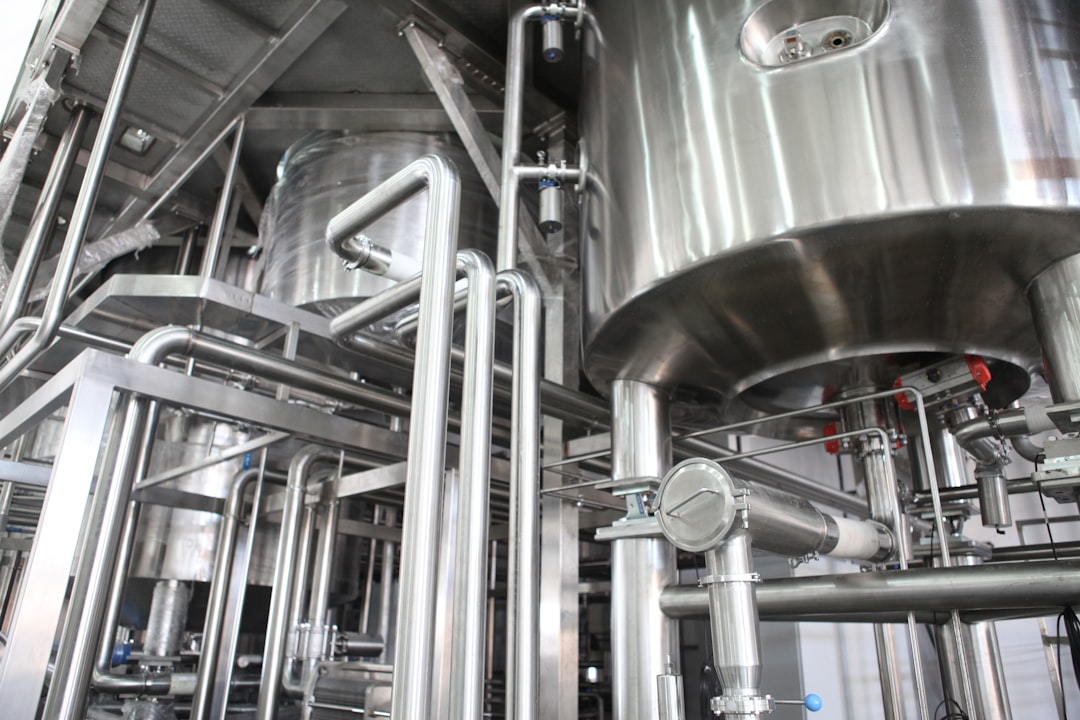
New materials are playing a crucial role in pushing the boundaries of bearing performance and durability. The use of advanced coatings like Diamond-Like Carbon and Zirconium Carbonitride has led to a significant increase in wear resistance and a reduction in friction, which translates to bearings that last longer and operate more smoothly. The introduction of surface texturing techniques is another game-changer, allowing bearings to operate effectively in harsh environments and even under dry lubrication conditions. These innovations not only improve efficiency but also enable bearings to withstand extreme operating conditions. It's clear that materials science is at the forefront of designing reliable bearings that can meet the increasing demands of today's industrial applications.
The quest for better bearing performance is driving exciting innovations in materials science. It's not just about strength and durability, it's about optimizing every aspect of the bearing's function, even in the most extreme environments.
One area of focus is thermal expansion. The way different materials react to temperature changes can be quite different. A metal bearing might expand and contract at a different rate than a polymer or composite one, causing misalignment or fitting problems. This can be especially challenging in applications involving high temperatures.
Another fascinating development is the use of nanostructured materials. These materials have properties that can enhance load-bearing capacity by as much as 300%. This improvement is due to the increased surface area and stronger molecular bonds at the nanoscale. It's remarkable how these minuscule changes can lead to such significant increases in strength.
The roughness of bearing surfaces is also a crucial factor. Recent research has shown that altering the surface texture at the microscale can significantly reduce friction. This can be achieved by creating a hydrophobic effect, which minimizes contact between the bearing and the lubricant.
Advanced polymers are playing a significant role as well. Some newer polymers have dissipative properties that can absorb energy and reduce vibration, extending the lifespan of bearings in dynamic environments. This is particularly important for applications where vibration is a major concern.
Another clever trick is to reinforce polymers with fibers like carbon or aramid. These composites have significantly enhanced wear resistance due to the fibers' exceptional tensile strength. This can help to reduce fatigue in high load-bearing applications.
Thermal conductivity also plays a role. Advanced materials like ceramics and composites can conduct heat much better or worse than traditional metals, leading to localized heating or cooling in bearings. Understanding how these materials transfer heat is critical to optimizing their performance in demanding environments.
Self-lubricating materials are another exciting innovation. Some new materials include solid lubricants like graphite or molybdenum disulfide, which can reduce wear even in extreme conditions where traditional lubrication methods fail.
Biodegradable polymers are a promising development for environmental reasons. They offer similar wear resistance to traditional materials but break down over time, minimizing environmental impact.
New cross-linking techniques for polymers are improving their strength and flexibility. These advancements allow for bearings that can sustain heavier loads while maintaining flexibility, making them suitable for demanding applications.
Electrospun fiber technologies are producing strong, lightweight bearing materials. These fibers are carefully aligned and oriented at the microscopic level, leading to enhanced durability and performance under load.
These are just some of the many fascinating developments in bearing materials. It's a dynamic field with the potential to revolutionize industrial applications. The future promises even more innovative solutions as we continue to push the boundaries of materials science in the pursuit of better bearing performance.
New Developments in Adjustable Friction Flange Bearings for Industrial Applications - Emerging Trends in Friction Management for Power Transmission
Emerging trends in friction management for power transmission are driven by a desire for improved efficiency and performance in both traditional and electric vehicle applications. A key focus is on developing innovative friction-reducing materials. Low-viscosity lubricants have shown promise in reducing friction and improving energy efficiency, but there are still challenges to overcome.
The use of smart technologies, such as AI and responsive lubrication systems, allows for real-time monitoring and adjustments, which can significantly minimize energy losses in powertrains. Advancements in materials science are also playing a role, with self-lubricating polymers and coatings being developed to address friction while enhancing durability and wear resistance.
Overall, the future of friction management in power transmission is closely linked to ongoing innovations in materials science and automation technologies. However, some of these solutions face challenges in terms of cost and practicality, and further research is needed to make them more widely applicable.
The landscape of friction management in power transmission is evolving rapidly, driven by the need for improved efficiency and reliability in demanding industrial applications. While traditional approaches have focused on minimizing friction through lubrication and material selection, emerging trends are pushing the boundaries of what's possible.
One notable development is the shift toward adaptive friction management systems. These systems can automatically adjust friction levels based on operating conditions, offering a dynamic solution for high-speed machinery where precise control is crucial.
Microtextured surfaces are also gaining traction in friction management. By creating carefully designed textures on the bearing surface, engineers can trap lubricants and dissipate heat, leading to significant reductions in friction and wear. This innovation is particularly promising for applications where harsh environments or dry lubrication conditions are a challenge.
The integration of smart sensors and predictive analytics is transforming the way we manage friction. Algorithms can now analyze operational data to identify potential problems and predict maintenance needs, minimizing unplanned downtime and ensuring smooth, continuous operations.
Materials science is another area of innovation. Hybrid materials, combining the strength of metals with the flexibility of polymers, are leading to bearings that can withstand heavier loads and tolerate wider temperature ranges. This opens up new possibilities for applications in harsh environments and heavy-duty machinery.
Magnetorheological fluids, fluids that change viscosity in response to applied magnetic fields, are introducing a new dimension of dynamic friction management. By adjusting the fluid's viscosity, engineers can fine-tune bearing performance to optimize for specific operating conditions.
The use of engineered nanoparticles as additives in lubricants is also gaining traction. These particles enhance lubricity and wear resistance, resulting in significant performance improvements across a wide range of applications.
Temperature-responsive materials, which adjust their friction properties based on temperature changes, are becoming increasingly popular. This adaptability ensures consistent performance in environments with fluctuating temperatures, making these materials ideal for a range of industrial applications.
Research into bio-inspired lubrication systems is showing promise in developing high-performance lubrication solutions with less environmental impact. By mimicking natural lubrication processes, these systems can outperform traditional lubricants while minimizing environmental footprint.
Advanced Computer-Aided Engineering (CAE) tools are enabling engineers to simulate complex loading scenarios with greater precision. This allows for the design of more robust bearings that can withstand unpredictable industrial loads, leading to improved performance and reliability.
Finally, the development of layered coatings, such as Diamond-Like Carbon (DLC) or Molybdenum Disulfide (MoS2), is revolutionizing friction management in bearings. These coatings dramatically reduce friction and wear, leading to exceptional performance and longevity, even under demanding conditions.
The ongoing innovations in friction management are ushering in a new era of high-performance bearings. As these trends continue to develop, we can expect to see significant advancements in efficiency, reliability, and sustainability in industrial applications, driving innovation across a range of industries.
More Posts from patentreviewpro.com: