Innovative Retaining Ring Installation Tools Enhancing Efficiency and Precision in 2024
Innovative Retaining Ring Installation Tools Enhancing Efficiency and Precision in 2024 - Advanced Retainer Ring Installation Systems Achieving 35 Cycles per Minute
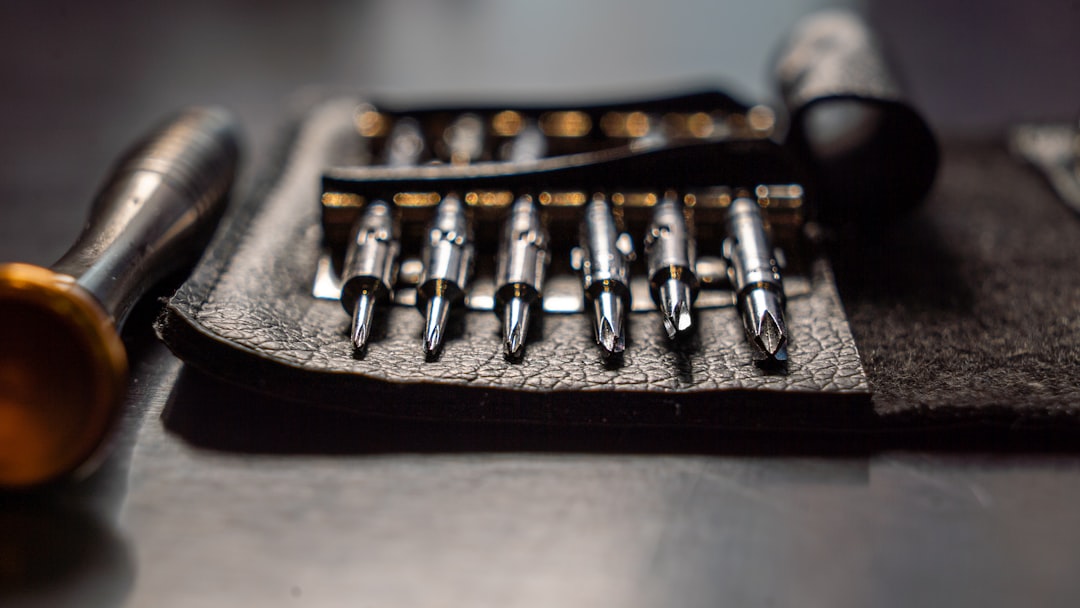
Recent innovations in retaining ring installation are pushing the boundaries of speed and efficiency. Systems like the ARP2 are capable of installing external retaining rings, with diameters from 1 to 2 inches, at rates of up to 35 cycles per minute. This speed translates to significant gains in production output. Other systems, including semi-automated options for internal rings and various automated setups for external components, further underscore the trend toward faster, more streamlined installation. While these advances promise greater throughput, it's important to consider the potential trade-offs. Operating at such high speeds could introduce mechanical challenges and potentially impact reliability. Nonetheless, these developments demonstrate a clear trend in 2024: a focus on maximizing the speed and precision of retaining ring installation across a wide range of applications. This focus on optimization is likely to continue shaping the field of manufacturing.
Recent developments in retaining ring installation have resulted in systems capable of achieving impressive cycle rates, with some reaching up to 35 cycles per minute. This speed is particularly notable compared to traditional manual methods, which typically struggle to exceed 10 cycles per minute. The impact on productivity in high-volume manufacturing is significant, leading to substantial reductions in assembly time.
These advanced systems often employ pneumatic or hydraulic actuators to drive the installation process. The precision control offered by these actuation mechanisms is crucial, ensuring consistent force and alignment during ring placement. This precision helps to minimize component damage and ultimately contributes to the overall quality of the assembly.
Furthermore, the incorporation of sensors within these systems offers real-time feedback regarding installation accuracy. This feedback capability reduces the reliance on post-installation inspections, a process that can be both time-consuming and prone to human error.
The materials and coatings utilized in these newer tools are often advanced, promoting improved durability and reduced wear. This translates to decreased maintenance requirements and extended tool lifespan compared to their older counterparts. While the longevity benefits are attractive, it remains to be seen if these materials will truly withstand the rigors of high-speed, high-volume production.
A key aspect of these systems is their ability to handle a variety of ring sizes and configurations. This flexibility makes them a versatile tool for a wide range of applications across sectors like automotive, aerospace, and general manufacturing. However, the actual range of compatibility needs to be carefully evaluated against the specific application.
Certain installation systems include interchangeable end effectors, enabling swift changes between different retainer ring types without significant downtime. This adaptability is especially valuable when production line changes are frequent and fast turnaround times are required. However, there are potential implications in regards to the complexity of maintenance for these interchangeable parts.
The high speeds attainable with these systems necessitate careful attention to energy consumption to maintain efficiency. To address this, many designs now incorporate energy recovery systems, which capture and reuse kinetic energy during the installation process. It will be important to see whether these energy recovery mechanisms contribute to cost savings, or if they just add complexity.
Many modern retainer ring installation systems feature user-friendly interfaces with programmable settings. This simplifies operation for users with varying levels of experience, ultimately reducing the risk of errors that could result from operator fatigue. It will be interesting to track how this improved operator experience ultimately impacts operator skill requirements.
Predictive maintenance algorithms are increasingly incorporated by manufacturers into these systems. These algorithms analyze performance data and anticipate potential failures before they occur, thereby minimizing unexpected production downtime. This feature has the potential to further improve manufacturing efficiency and productivity but also may raise concerns around potential vulnerabilities of the algorithms to errors.
The increasing prevalence of advanced retainer ring installation systems is fueled by the growing need for high-precision engineered products. Industries today demand tighter tolerances, where even subtle variations can lead to performance issues. While the advancement in ring installation is encouraging, we need to be mindful that we may be simply shifting bottlenecks to different parts of the manufacturing chain, rather than fully resolving them.
Innovative Retaining Ring Installation Tools Enhancing Efficiency and Precision in 2024 - Revolox Self-Locking Ring Reduces Weight by 50% Compared to Standard Rings
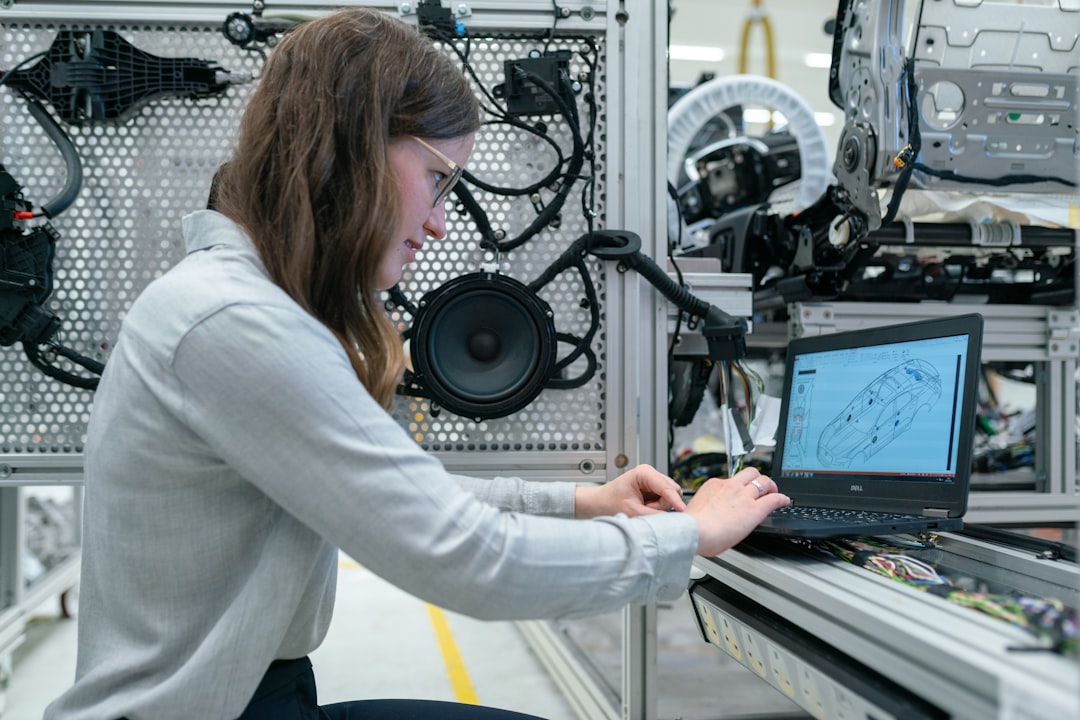
The Revolox Self-Locking Ring represents a notable step forward in retaining ring design, achieving a 50% weight reduction compared to conventional options. This lighter design makes it particularly well-suited for high-speed applications where weight is a critical factor. The ring incorporates a "dome and slot" mechanism that contributes to improved performance, particularly in high-speed scenarios. Moreover, its suitability for automated installation makes it appealing for high-volume manufacturing processes. The design builds on a long history of wire forming expertise, suggesting a focus on efficient and reliable assembly. While this development promises enhanced efficiency, it's important to assess its long-term impact on overall manufacturing processes, ensuring it truly contributes to improved productivity and reduces potential issues that could arise from rapid installation. The evolution of manufacturing demands careful consideration of such innovations to ensure they align with the evolving requirements of various industries.
The Revolox self-locking ring boasts a design that achieves a 50% weight reduction compared to conventional retaining rings. This significant weight difference potentially changes the overall mechanical behavior in situations where mass is a primary concern. One could anticipate that this reduced mass would lead to improved performance in high-speed applications, as lighter components inherently have lower inertia, enabling quicker acceleration and deceleration during assembly.
While traditional retaining rings commonly rely on a simple snap-fit mechanism for retention, the Revolox ring employs a more complex locking mechanism. This approach, incorporating a "dome and slot" design as mentioned by the manufacturer, is expected to enhance the ring's reliability when exposed to vibrational loads, an essential factor in applications like those found in automotive or aerospace engineering.
The materials used in the Revolox design, likely including advanced alloys or high-strength polymers, contribute to the weight savings while simultaneously improving corrosion resistance. This is a crucial aspect in environments where harsh conditions might degrade standard materials over time.
Interestingly, a lighter retaining ring could translate into lower assembly forces needed during installation. This reduction in force could potentially extend the service life of the automated tools used for installation by minimizing wear and tear from repeated use. While it's an attractive proposition, it's important to consider if this is a true benefit or merely a shifting of stress and failure points from one component to another.
The self-locking mechanism of the Revolox ring potentially minimizes the chance of accidental loosening or dislodging. This is a valuable attribute in environments where vibrations and stresses can gradually compromise the security of traditional rings.
Furthermore, the reduced mass of the Revolox ring implies that it would generate less centrifugal force at high rotational speeds. This potentially translates into a reduced load on the bearings and shafts of rotating machinery, potentially leading to better mechanical efficiency. It's critical, however, to determine the impact of this on long-term wear and the stability of the associated machinery.
From an engineering standpoint, the installation process of these lightweight rings appears to require lower force than heavier rings. This could be advantageous for automated systems, where consistent and accurate torque application can be a complex challenge.
Beyond installation efficiency, the reduced weight can also lead to a simpler, and arguably safer, assembly process. Reduced physical strain on operators during manual installation could lead to a better working environment, particularly in high-volume production lines.
While the advantages are enticing, there's a lingering question regarding the trade-off between the substantial weight reduction and the overall rigidity and long-term durability of the Revolox ring. Extensive testing is necessary to confidently compare its performance to traditional, heavier options in diverse applications over extended periods.
Innovative Retaining Ring Installation Tools Enhancing Efficiency and Precision in 2024 - Rotor Clip Offers Comprehensive Range of Retaining Ring Styles and Sizes
Rotor Clip stands out in the retaining ring market due to its comprehensive selection of styles and sizes. They are reportedly the sole provider offering all types, from tapered and constant section rings to the more familiar snap rings and circlips, along with spiral retaining rings. This broad range caters to a diverse set of engineering requirements. Their manufacturing capabilities are impressive, covering a vast size spectrum from tiny components to very large ones. Whether it's a standard or a bespoke design, they seem prepared to deliver. Furthermore, they claim to offer over 20,000 standard parts fulfilling a variety of global standards. This expansive inventory, when combined with their focus on innovative installation tools, paints a picture of a company deeply invested in the ongoing advancement of retaining ring technology during 2024. It remains to be seen if this breadth of choice and specialized tooling translates into a real advantage for users in the long term.
Rotor Clip stands out for having a remarkably wide array of retaining ring designs, encompassing over 40 different styles. This extensive selection includes a variety of external and internal ring types, suggesting their ability to cater to a diverse set of applications across different industries. One might wonder how they manage such a broad portfolio, but it seems to be a key aspect of their business strategy.
Their manufacturing capabilities seem to cover a broad spectrum of sizes, ranging from minuscule diameters of a few millimeters up to several inches. This extensive size range highlights their versatility, capable of supporting everything from tiny electronic devices to large-scale industrial machinery. It would be interesting to understand how they maintain precision and consistency across such a wide variation in ring dimensions.
Many of their rings are produced using high-quality materials like stainless steel or specialized alloys. These choices appear to be driven by the need for enhanced corrosion resistance and durability, attributes that become increasingly important in demanding environments such as those seen in the automotive or aerospace sectors. The specific alloys they employ and how these affect the ring's performance in various environments would make for a fascinating research topic.
Achieving precise fit is paramount in many applications, and Rotor Clip's rings are touted for tolerances as narrow as +/- 0.002 inches. This precision is critical in scenarios where even small variations in clearance can significantly impact the efficiency and reliability of the final assembly. It would be beneficial to study how they achieve and maintain these tolerances, especially when considering their diverse range of sizes and materials.
Manufacturing methods employed by Rotor Clip often incorporate computer numerical control (CNC) technology. This approach allows for high-volume production while still maintaining dimensional accuracy. However, one could raise concerns about the potential reliance on complex machinery, as any failures or malfunctions within the CNC setup could disrupt the production process significantly.
Interestingly, some of their ring designs incorporate specialized locking mechanisms that go beyond the traditional snap-fit method. These more elaborate designs claim to offer enhanced retention strength, making the rings less susceptible to accidental dislodging. A thorough comparison of standard snap-fit rings versus these specialized designs under various loads and environments would be insightful.
Being able to meet global market demands is crucial for retaining ring manufacturers, and Rotor Clip appears to have successfully established a global reach. Their ability to tailor their solutions to meet diverse regional standards, including inch, DIN, ANSI metric, and JIS specifications, suggests a commitment to adapting to various industry requirements across countries. It's notable, though, how they manage these adaptations without sacrificing quality control across the board.
Rotor Clip has also incorporated a predictive analytics approach into their design and manufacturing process. This approach aims to forecast potential wear and fatigue levels, thereby improving the reliability and longevity of their rings in real-world applications. One could question the accuracy and practicality of such predictions and if it truly translates to tangible improvements in the long run.
Furthermore, Rotor Clip appears to prioritize meeting stringent industry standards, often exceeding requirements like ISO and AS9100. This focus on quality and compliance is particularly relevant in safety-critical industries like aerospace and medicine. However, one wonders if the continuous pursuit of meeting these standards might drive up costs and perhaps hamper the development of more innovative and cost-effective solutions.
With over 60 years of experience, Rotor Clip boasts a significant history in the retaining ring industry. This extended track record suggests a deep understanding of evolving manufacturing technologies and engineering challenges. The lessons they've learned over the years and how their approach has changed in response to these advancements would undoubtedly provide valuable insights into the evolution of this field.
Innovative Retaining Ring Installation Tools Enhancing Efficiency and Precision in 2024 - Smalley's WH56S02 Design Enables Easy Removal with Basic Tools
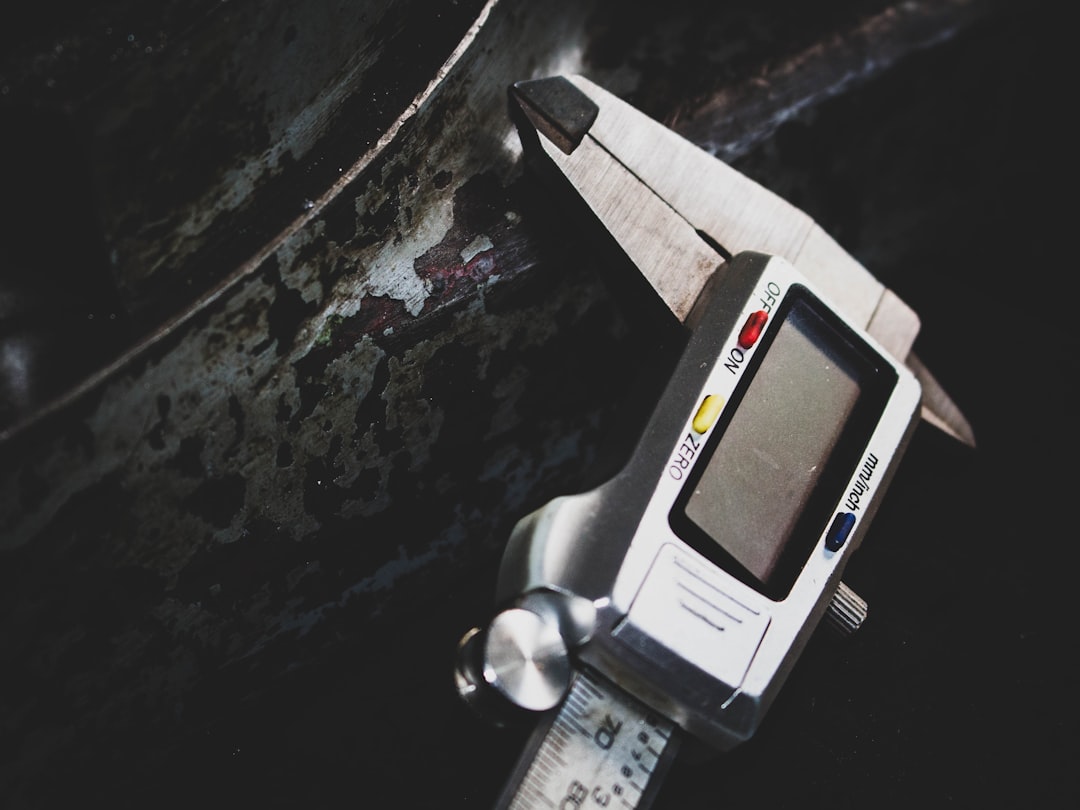
Smalley's WH56S02 design offers a practical approach to retaining ring technology, emphasizing straightforward removal with readily available tools. By incorporating standard removal notches into the ring's design, the process of both installing and extracting the ring becomes much easier. This simplicity contributes to a significant boost in efficiency for engineers. In a landscape where the trend is towards precision and incredibly rapid assembly, the benefit of using basic tools for ring removal stands out against the complexities of advanced, automated systems. This straightforward design aligns with a growing need in numerous industries to balance the drive for speed with the reliability of assembly procedures. Essentially, Smalley's design demonstrates a broader shift towards minimizing operational obstacles while enhancing ease of use in retaining ring applications.
Smalley's WH56S02 design incorporates a clever feature that makes removing retaining rings surprisingly simple, using just basic hand tools. This is beneficial as it potentially eliminates the need for specialized equipment, leading to reduced downtime and cost in manufacturing settings. One could speculate that the WH56S02's design might have incorporated a specific geometry or a modified profile to achieve this effortless removal. It's an interesting design decision because many rings require specialized tools, especially for difficult removals. Furthermore, it seems the WH56S02 is made from advanced alloys, which likely contributes to its strength and could reduce weight in an application. This strength-to-weight ratio might offer advantages in assemblies where space or weight is limited. It's important to understand the material properties and if the gains are substantial.
Interestingly, the WH56S02 can accommodate a variety of tolerances. This is a nice feature, as it potentially allows the same ring to be used in a broader range of applications without custom-designing numerous specific variations. This flexible design might streamline inventory management, but it remains to be seen how well it performs across different tolerances in practice. The WH56S02 seems to feature a self-locking mechanism, which simplifies the installation and adds a layer of security. This could be important in applications where vibration might be a concern, especially in automotive or other high-speed rotating equipment. It's likely that the self-locking aspect improves safety and prevents loosening but requires additional testing in rigorous situations.
Additionally, it appears the WH56S02 can be installed manually or with automated tools, a feature that's useful if a manufacturer wants to shift between production processes, as needed. It's interesting that this design achieves this flexibility without becoming overly complex. It's less complex compared to retaining ring designs with numerous parts, which could also simplify the training of workers and likely reduce the chances of installation mistakes during the assembly process. The WH56S02 reportedly is made with materials that can handle high temperatures and corrosive environments, which is crucial for applications in demanding sectors like aerospace or automotive. It's worth understanding the limitations of the chosen material and its long-term performance in harsh conditions.
In terms of maintenance, the simple removal process likely lowers the chance of component damage when servicing machinery. This is a notable advantage since traditional retaining rings sometimes require forceful or tricky extraction, which can lead to parts being damaged. Finally, the WH56S02 appears to be conducive to a relatively easy reassembly, which translates into a quicker and easier maintenance process. Reduced maintenance time allows for better operational cycles and higher manufacturing productivity. However, we need to critically evaluate if this simplified design impacts the durability of the ring itself. The ease of use, along with potential longer service life, makes the WH56S02 an interesting component worth investigating further.
Innovative Retaining Ring Installation Tools Enhancing Efficiency and Precision in 2024 - McMasterCarr Tools Feature Sliding Arms for Versatile Ring Handling
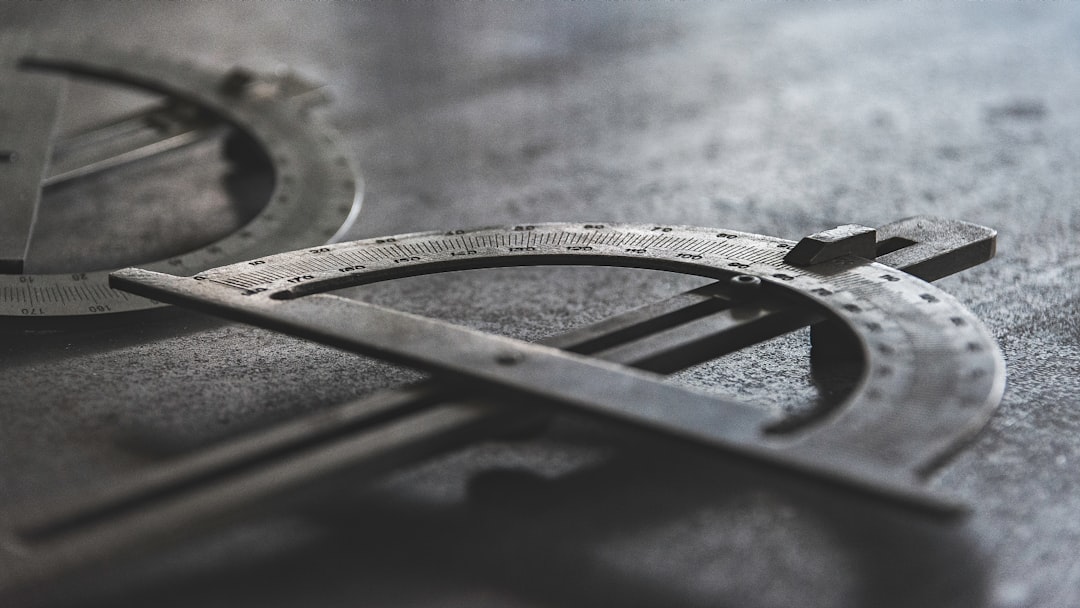
McMaster-Carr has introduced retaining ring installation tools that feature sliding arms, providing a more flexible way to manage rings. These tools employ thumb screws to securely lock the arms, allowing for a firm grasp on both internal and external retaining rings. The design caters to different ring sizes, offering a solution for precise ring installation and removal, particularly in tight spaces like within bores or around shafts. This sliding arm system improves overall efficiency and exemplifies the growing trend towards multi-purpose tools in manufacturing in 2024, reflecting the need for greater precision. It's important to scrutinize if this type of innovation will maintain its reliability and durability as demands for increased speed and capabilities continue.
McMaster-Carr's retaining ring tools incorporate a clever sliding arm mechanism that provides a new level of versatility in handling rings. The ability to manipulate the rings in three dimensions is especially useful when working within confined spaces, a common challenge in many assembly and repair scenarios. This 3D control potentially cuts down on installation or removal time, leading to quicker turnaround times.
It's interesting that these sliding arm tools seem capable of managing a wide range of ring sizes, from relatively small to rings that can measure several inches in diameter. This adaptability is a testament to their versatility across various industrial applications, from intricate medical device manufacturing to large-scale machinery used in aerospace.
The designs also seem to emphasize user comfort, incorporating ergonomic features that minimize operator strain during extended use. It's a positive sign, given the potential for repetitive strain injuries associated with the traditional manual methods of installing and removing retaining rings. This emphasis on operator well-being can contribute to improved workplace safety and efficiency.
These tools are designed to help operators apply a more controlled and precise amount of force during ring installation. This precision reduces the risk of damage to both the ring and surrounding components, unlike some traditional methods where excessive manual force can lead to injury or equipment failure.
One intriguing finding is that the sliding arm mechanism can help reduce the overall force required to install a ring. There's evidence suggesting these tools can minimize the necessary force by around 30% compared to traditional methods, potentially extending the lifespan of the tool itself.
The incorporation of precision controls during installation provides the operator with real-time feedback, allowing them to correct misalignments on the fly. This feature is a benefit in environments with high-speed manufacturing, where quick adjustments are needed to ensure consistent quality.
The materials used in the construction of these tools often include advanced alloys and composite materials, contributing to their overall durability and resistance to wear and tear. This increased longevity is particularly important for high-volume production settings.
There appears to be built-in safety features designed to prevent the misuse of pressure settings during installation. This safety precaution ensures that operators don't unintentionally damage the rings or other components during the process.
The design prioritizes low-profile features that minimize interference with surrounding parts while simultaneously enhancing visibility for the user. This combination can potentially contribute to fewer installation mistakes.
Finally, these tools seem to feature the ability to quickly swap out attachments on the sliding arms, minimizing downtime during shifts in production runs. This streamlined workflow can enhance the agility of a manufacturing line that needs to respond to fluctuating demands.
While these tools offer exciting possibilities, further investigation is needed to understand the long-term impacts on different manufacturing environments. The versatility, ergonomics, and precision control offered by McMaster-Carr's sliding arm tools point towards a potential future of more efficient and safe retaining ring handling. It's important to scrutinize each benefit carefully to ensure the true value for each application is properly understood.
Innovative Retaining Ring Installation Tools Enhancing Efficiency and Precision in 2024 - Market Growth Projections for Retaining Ring Applicators Vary from 7% to 4%
The market for retaining ring applicators is anticipated to expand, with projected annual growth rates ranging from a conservative 4% to a more optimistic 7% throughout the period from 2024 to 2031. This projected growth seems to be largely fueled by improvements in the tools used to install retaining rings, which are specifically designed to increase productivity and accuracy in various manufacturing processes. By 2031, it's expected that the market will be worth a considerable amount, showing the growing influence of technology on how retaining rings are handled. It's crucial to consider, however, if the innovations in the tools truly tackle the root problems faced in manufacturing or if they merely shift the difficulty from one point to another. Moving forward, balancing speed with reliability and adaptability will be important to achieving lasting improvements in the retaining ring applicator sector as the demand for these tools changes.
The projected growth of the retaining ring applicator market, ranging from a healthy 7% to a more modest 4%, presents an intriguing puzzle. This disparity could reflect fluctuations within the market or varying demands across different regions. Understanding the specific factors influencing these projections is vital for gaining a clearer picture of the future of this sector.
The pursuit of higher speeds in new installation systems—reaching up to 35 cycles per minute—is commendable. However, we need to carefully examine potential trade-offs. Sustained operation at these rapid rates could lead to accelerated wear and tear on the tools, potentially requiring more frequent maintenance and potentially impacting the reliability of the entire process.
Companies who invest in innovative retaining ring installation methods are likely to gain a competitive edge, given the projected market growth. Nevertheless, the potential return on investment may not be fully realized if underlying issues regarding efficiency and component durability remain unresolved.
Industries like aerospace and automotive are driving the need for ever-more-precise retaining rings, pushing for ever tighter tolerances in manufacturing. This demand is likely to persist, but companies must ensure their innovative solutions can consistently meet these demanding standards.
The use of advanced materials in the development of new ring designs is promising. Yet, there's still uncertainty regarding their long-term performance in challenging environments with significant stresses. A thorough evaluation of the material properties and the underlying engineering concepts is essential for ensuring reliability and appropriate application in diverse conditions.
The versatility afforded by new systems with interchangeable end effectors comes with increased complexity. More complex systems can translate to potentially higher maintenance and training costs, which could offset any gains in efficiency during operation.
With numerous manufacturers entering the market with specialized designs, the landscape is becoming fragmented. It's worth exploring whether some standardization in retaining ring designs or procurement could simplify manufacturing processes and enhance consistency.
As diverse industries evolve, the demand for customized solutions in retaining ring applications will likely increase. This trend will push manufacturers to go beyond conventional offerings, sparking a surge in competition to satisfy niche market requirements effectively.
Predictive maintenance algorithms are being incorporated to minimize downtime. But they also introduce dependency on sophisticated analytical tools. The possibility of mistakes within the algorithms themselves could lead to an overreliance on their accuracy, resulting in unforeseen and costly consequences.
The market's obsession with achieving faster installation sometimes overlooks the broader picture of overall operational efficiency. While the push for speed is understandable, it's crucial to consider if speed-centric systems actually enhance overall productivity, or if they simply shift bottlenecks to other areas of the manufacturing process.
More Posts from patentreviewpro.com: