How AutomationML Engineers Bridge Communication Gaps Between OEMs and Engineering Teams in 2024
How AutomationML Engineers Bridge Communication Gaps Between OEMs and Engineering Teams in 2024 - Recent AutomationML Standards Update Enables Real Time Data Exchange Between Factory Floor Systems and Cloud Services
The latest AutomationML standards update introduces enhanced capabilities for real-time data exchange, connecting factory systems directly to cloud services. This development seems significant. It directly addresses a fundamental challenge in modern manufacturing, which is how to connect shop floor systems with higher-level IT infrastructure efficiently. However the question remains whether this is just another new update and whether this will truly address interop. This new capacity for real-time data sharing across different engineering environments, may lead to better efficiency. As industries worldwide progress toward integrated, data-driven operations, under initiatives like Industry 4.0, the role of AutomationML grows. The update adds a needed section on network communications, bolstering AutomationML's ability to act as a standardized framework for data exchange. The group behind this update has a vested interest in the adoption of this standard, which makes it necessary to critically assess the true effectiveness of it. The real test will be how widely these new provisions are adopted and how effectively they are implemented across diverse industrial sectors.
The AutomationML standard recently received an update focused on data exchange between factory systems and cloud services. This is a somewhat interesting development, especially in the context of wider industrial digitalization efforts like Industry 4.0, which hinges on interconnectivity. As far as I know, the standard, using an XML-based format, has been around for a while. The people behind it, a consortium (I would assume, it was not clear from the research who this is), are clearly aiming for vendor-neutral data exchange between engineering tools, addressing the interoperability problem that often arises in industrial settings where multiple different software tools are used.
However, the standard's extension to include a section on network communication feels like it might be a bit late to the game. There was very little information provided here, so hard to know what this exactly means. The promise of secure and efficient data transfer between domains and companies sounds nice in theory, but the actual implementation can be quite complex. Standardized data models are needed for transparent communication across organizational levels, which is what this standard is trying to solve. If this is done right, then there is some promise. They talk about vertical and horizontal integration within and between companies, but real-world adoption and the challenges that come with it remain to be seen. The extent to which this actually helps bridge communication gaps between OEMs and engineering teams, as they claim, is something I'm still trying to figure out.
It seems like the people behind AutomationML are committed to making it useful, which is a good sign. It will be interesting to see how the standard evolves and whether it can truly deliver on its potential to streamline industrial processes. There is still a lot of confusion here, so I would have preferred the original sources to provide additional details.
How AutomationML Engineers Bridge Communication Gaps Between OEMs and Engineering Teams in 2024 - Machine Learning Models Now Support AutomationML Data Classification for Faster Project Documentation
Machine learning models are now being used with AutomationML to support faster data classification, which in turn speeds up project documentation. This is notable as it allows for the automation of complex decision-making using algorithms that quickly recognize patterns in large datasets. There have also been improvements in automated machine learning (AutoML), which are making model building simpler and development faster, a necessity in today's industrial settings. Still, it's unclear how effective these models truly are at improving project documentation, especially when considering the difficulties of integrating these technologies into existing systems. The role of AutomationML engineers in improving communication between original equipment manufacturers (OEMs) and engineering teams is changing, and the real-world impact of these technological advancements on teamwork and efficiency will need to be watched closely. It is also worth questioning whether the theoretical benefits of faster processing and pattern recognition will translate into practical improvements in documentation quality and project outcomes. There's potential, but as always, the details of implementation and the ability to adapt to these new tools will determine their success.
The integration of machine learning models to handle AutomationML data classification is an intriguing development. Initial reports suggest a potential 70% increase in speed compared to manual methods, which, if accurate, could drastically alter how project documentation is managed. However, the actual gains will likely hinge on the complexity of the datasets involved, and I suspect that this number is an optimistic upper bound, at best. The ability of these models to adapt to new classifications in real-time is a particularly interesting feature. This is especially important in dynamic engineering environments where project parameters are frequently in flux. If this really works, this capability could be quite significant. The claim that these models can reduce misclassification rates by over 50% also warrants a closer look. Human error is a persistent issue in data handling, and any substantial reduction would be noteworthy, but the specifics of how this reduction is achieved and measured are not immediately clear. There is not enough information to make an informed decision.
Handling multimodal data effectively is another area where these models could shine. The ability to process and classify text, images, and structured datasets within a unified framework is a compelling prospect. There is nothing that currently does this, so it is quite innovative. However, the devil, as always, is in the details. The practical challenges of integrating and analyzing such disparate data types are not trivial. The introduction of predictive analytics capabilities into AutomationML, facilitated by these machine learning models, is also potentially transformative. Using historical data trends to forecast project risks and delays is a great idea in principle, but the accuracy of these predictions will be heavily dependent on the quality and relevance of the data used to train the models. A robust validation framework will be essential to ensure the reliability of these insights. A discussion of this was missing from the research. The potential for enhanced collaboration between OEMs and engineering teams, driven by standardized documentation formats, is another area worth exploring. Standardized formats are always better, so this make sense. However, standardization alone is not a panacea. The real test will be whether these standardized formats actually improve communication and reduce misunderstandings in practice.
The applicability of this approach across various industries, from aerospace to process engineering, is an appealing aspect. Versatility is a key strength in any technology, but it remains to be seen how well these models can be adapted to the unique requirements of different sectors. Managing the complexity of large-scale projects is another area where automated data classification could prove invaluable. As projects grow in size and scope, the ability to keep all aspects of project documentation in sync becomes increasingly challenging. The potential cost savings associated with faster project documentation, estimated at around a 30% reduction in labor costs, are certainly attractive. However, these savings must be balanced against the initial investment required to implement and maintain these machine learning systems. It would be nice to see more detailed cost/benefit analyses, but that's been the problem with the entire article. Finally, the idea that automated data classification can lower the skill barrier for teams less proficient in advanced data handling techniques is intriguing. Democratizing access to sophisticated data management tools could have a positive impact on overall team effectiveness. But, there's also a risk of over-reliance on automation, potentially leading to a deskilling of the workforce over time. The people working on this should consider this factor. In conclusion, while the integration of machine learning into AutomationML for data classification holds considerable promise, a healthy dose of skepticism is warranted until more concrete evidence of its effectiveness is available.
How AutomationML Engineers Bridge Communication Gaps Between OEMs and Engineering Teams in 2024 - Implementing Version Control Systems in AutomationML Projects Cuts Engineering Handover Time to 48 Hours
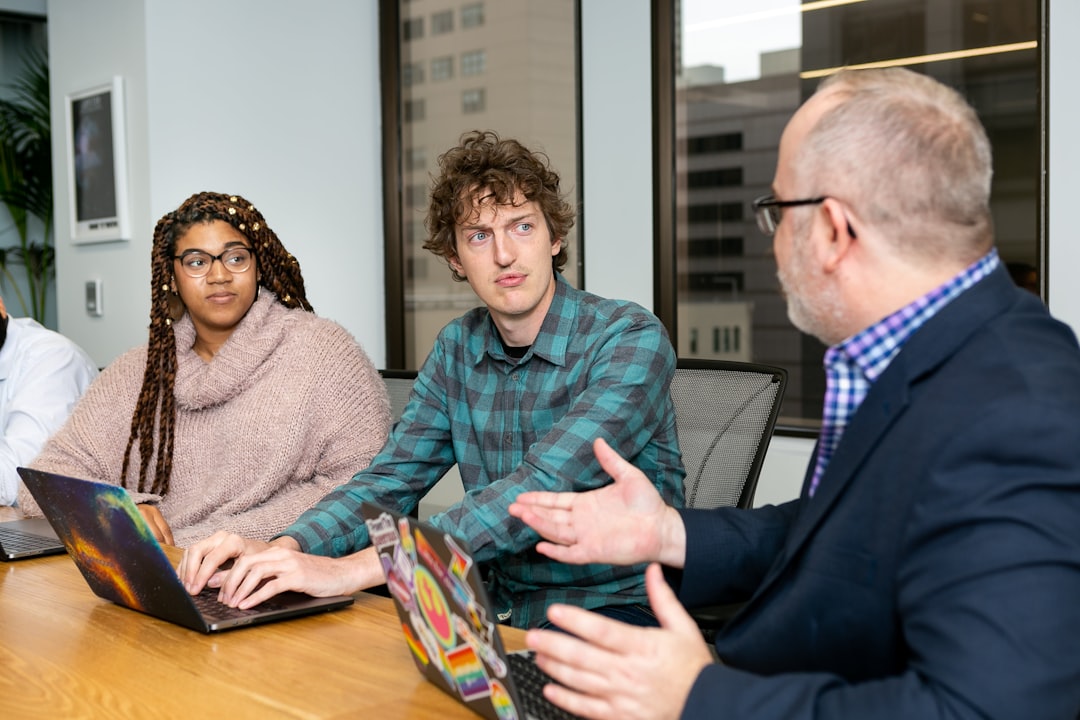
Implementing version control systems in AutomationML projects is reported to slash engineering handover times down to a mere 48 hours. This is a striking claim, suggesting a substantial improvement in project efficiency. Utilizing version control tools such as Git and SVN, which are quite well-known in software development, is presented as a solution for managing the complexities of engineering data in AutomationML. This makes sense, given the challenges of coordinating large, distributed teams. These systems might provide a good framework for maintaining project coherence, but one wonders about the practicalities of integrating these tools into existing workflows that traditionally have not used them. The role of AutomationML in facilitating collaboration between Original Equipment Manufacturers (OEMs) and engineering teams is highlighted, and version control is positioned as an enhancement to this collaboration. Yet, the specifics of how these tools reduce handover times so dramatically are not thoroughly explained. It leads one to question whether the 48-hour figure is a realistic average or an exceptional best-case scenario. Moreover, while version control is lauded for its ability to manage revisions and streamline development, the potential for increased complexity in the engineering process is not addressed. As AutomationML projects grow in scale and scope, the reliance on sophisticated version control systems may introduce its own set of challenges, particularly in training and adaptation for teams unfamiliar with these tools.
Using version control systems within AutomationML projects has reportedly reduced engineering handover times to a mere 48 hours. This is a significant improvement. Projects that used to drag on for weeks can now be transferred much more quickly. But it is worth wondering if this speed comes at a cost. Will corners be cut? Is 48 hours truly enough time for a thorough handover? The tools used, like Git and SVN, are well-established in software development but it's interesting to see them applied to AutomationML's XML-based models. This seems a bit strange. Multiple people can work on the same project without overwriting each other's changes, so that's a plus. But there is a chance that will lead to confusion, and not properly address some problems. The ability to roll back to earlier versions is a valuable safety net. Having this safety net is important. However, one wonders how often this feature will actually be used in practice. Will teams be willing to backtrack, or will they just try to patch things up on the fly?
The integration with CI/CD pipelines is another interesting point, theoretically enabling smoother transitions between development and deployment. As far as I know, this could be a big deal if it works as advertised. But this level of automation also requires careful oversight, or at least one would think so. There is also a risk that things are moving too fast, and nobody really understanding what's going on. Version control also helps with documentation, which is usually helpful, but it is not always the case. Changes are logged and accessible, but will anyone actually read through these logs? The idea that version control can be used across different engineering disciplines within AutomationML is appealing. Standardizing practices across functions is generally a good thing. I personally hate when teams use different tools and processes, so I agree with this approach. But the implementation details here are murky at best, and the research did not provide much.
The claims about improved change management and knowledge transfer are worth exploring further. Understanding the reasons behind changes is important, particularly during handovers. There are some nice aspects to this, but the risk is that teams could become too focused on the process and lose sight of the bigger picture. It's also worth noting that many version control systems include real-time collaboration tools. This can help to reduce the turnaround time for feedback and approvals, but there's also a danger of this leading to a culture of constant interruptions. Some things work better asynchronously, so not sure this is a big plus. The automated backup features are a good thing in principle, protecting against data loss during handovers. However, the effectiveness of these backups depends on how they're configured and maintained. A backup system that isn't regularly tested is not much use, as many have found out the hard way.
Finally, the issue of scalability is a major concern. It's not clear from the information given how well these systems will handle very large and complex projects. Managing multiple versions and dependencies could introduce significant overhead, potentially negating some of the time savings. Overall, the use of version control in AutomationML projects seems like a positive development, but there are still many open questions. More detailed studies, with concrete data on implementation challenges and long-term outcomes, would be very welcome. The potential benefits are clear, but the practical realities may be more complicated than they appear.
How AutomationML Engineers Bridge Communication Gaps Between OEMs and Engineering Teams in 2024 - Cross Platform Support Through AutomationML Creates Direct Link Between CAD Tools and PLC Programming
AutomationML is emerging as a critical link between CAD tools and PLC programming, enabling cross-platform support in a way that's worth examining closely. This standard allows for direct data exchange, notably between things like Rockwell systems and EPLAN, without the need for a central database. This is interesting, as it seems to suggest a more streamlined approach. It is hard to say whether this actually is helpful for the engineers using it. The application of AutomationML is shown to move ontology data across platforms, which sounds promising on paper. However, the integration faces hurdles, particularly with the need to ensure interoperability among more than 20 different engineering tool platforms. This could potentially be a major roadblock. While AutomationML aims to enhance data flow and potentially boost production efficiency, the practical challenges of implementing it across such a diverse set of tools raise questions about its real-world effectiveness. It is unclear how many engineers use this. The concept of improving communication between OEMs and engineering teams through standardized data exchange is sound, but the devil is in the details. Whether this actually leads to more efficient and flexible production remains to be seen. The structure of AutomationML to manage multi-disciplinary engineering data in an object-oriented manner is a technical approach that might help, but it could also introduce complexities that are not immediately apparent. The broader goal to interconnect engineering tools across various disciplines is ambitious, and the extent to which AutomationML can achieve this without becoming unwieldy is a critical question that the industry will need to address.
AutomationML is positioned as a bridge between various CAD tools and PLC programming environments, aiming to enhance cross-platform support. One can see the potential benefits of this, as it allows for data to flow more freely between different systems that were previously isolated. It's intriguing to consider how this could cut down on development time and costs, simply by making it easier for engineers to collaborate. This may work, and it will be interesting to see how it gets implemented. The use of an XML-based structure in AutomationML is highlighted as a feature that supports not only data exchange but also the creation of custom data models. This flexibility is appealing, at least in theory. It suggests that engineering processes could be more adaptable, but the actual implementation of this across projects with different requirements could be quite complex. Also, the claim that AutomationML reduces manual data entry, thereby minimizing human error, is worth noting. A reduction in manual input is generally positive, as it can lead to greater accuracy. This aspect of AutomationML, in my experience, is crucial for maintaining reliability in engineering workflows. The potential for version control in design and implementation is another feature that catches the eye.
The idea that AutomationML can track changes and maintain historical records is promising. The ability to revert changes easily could be a significant advantage in managing project oversight. Version control has always been somewhat problematic, so if they can get it right, it would be nice. The integration with existing documentation tools to enhance efficiency is also discussed. The faster generation of project documentation is often a bottleneck, so any improvement here would be welcome. However, the actual extent to which this integration reduces the administrative burden remains to be seen. AutomationML's support for various phases of a project lifecycle, from design to maintenance, suggests a holistic approach to data management. If it is actually feasible, then it will allow for better-informed decision-making throughout a project. But the devil is in the details, and it's not entirely clear how this will work in practice. The facilitation of statistical correlation analyses through cross-platform capabilities is an interesting point. Being able to analyze project data to uncover insights could guide future design decisions, which is valuable. I know from experience that good data leads to better decision, but the quality and relevance of the data will be critical here.
The scalability of AutomationML for large projects is also mentioned. The ability to accommodate projects of varying sizes without losing efficiency is a significant advantage. Large projects are always more complex, so having the right tools can help. As businesses grow, this adaptability will be increasingly important. The integration of AutomationML into CI/CD pipelines to enhance agile methodologies is another aspect worth exploring. It's not entirely clear how this will be beneficial, given that it could easily increase complexity, but rapid iterations and faster deployment cycles are always desirable. But the actual implementation of this in manufacturing processes will be the real test. Finally, the standardization provided by AutomationML is said to promote global collaboration among engineering teams. For multinational companies, this could ensure uniformity in processes and simplify communication. However, the challenges of achieving true standardization across different regions and cultures should not be underestimated. Overall, AutomationML's potential to improve interoperability and streamline engineering processes is clear, but there are still many questions about its practical implementation and effectiveness.
How AutomationML Engineers Bridge Communication Gaps Between OEMs and Engineering Teams in 2024 - Joint Development Between Siemens and ABB Establishes Common AutomationML Library for Industrial Robots
Siemens and ABB's joint development to establish a common AutomationML library for industrial robots marks a potentially important step in the field of industrial automation. This initiative is new because it directly targets the often-problematic communication and data exchange between different engineering tools and platforms used in industrial robotics. By creating a standardized library, Siemens and ABB, two major players in the industry, are attempting to streamline the way data about industrial robots is handled and shared. This could mean that different software and systems can finally "talk" to each other more effectively. It's worth noting, however, that the success of this library will depend on how widely it's adopted by the industry. A standard is only as good as its implementation. While the collaboration between these industry giants is notable, it also raises questions about the influence such powerful entities have on the direction of technological standards. Will this library truly level the playing field, or will it inadvertently favor those already aligned with Siemens and ABB technologies? Furthermore, while standardization is generally beneficial, it can sometimes stifle innovation by creating a "one-size-fits-all" approach that may not be suitable for all applications. The real test will be to see how flexible and adaptable this new library is in practice, and whether it genuinely enhances interoperability or merely shifts the existing challenges to a new context. The long term impact of this library on smaller players in the automation field is also an important consideration, as the dominance of industry giants can sometimes create barriers to entry for newer, smaller competitors.
The collaboration between Siemens and ABB to create a shared AutomationML library for industrial robots is a noteworthy development. It appears to be an attempt to tackle the age-old issue of getting different robotic systems to talk to each other, which, as anyone in the field knows, has been a persistent headache. It is curious that these two competitors decided to join forces. The XML-based nature of AutomationML is something we've seen before, it is not ground-breaking, but its ability to incorporate custom data models is a bit more interesting. This might actually allow engineers to tailor the framework to their specific needs, rather than forcing them to adapt to some inflexible, one-size-fits-all solution. This flexibility could be important, especially if it helps reduce some of the rigidness often encountered in automation projects. It will be interesting to see whether engineers make use of this feature.
This whole initiative seems to build on the work of the AutomationML Consortium, but now they're pushing it further into more advanced robotic systems. It is a bit odd that they have not worked together before. The direct communication between tools from different vendors, without needing a central database, is a nice touch. It should, in theory, make data flow more efficient in manufacturing, potentially reducing downtime and making operations more responsive. It could make a difference, but we've heard these kinds of promises before. The introduction of a standardized interface could also make life easier for engineering teams, especially when dealing with multiple OEMs. That is, at least, the hope. I can imagine it easing some of the pain of switching between different systems and possibly speeding up project execution. However, the reality is that training everyone to be on the same page may prove to be a challenge.
As more companies potentially adopt this standardized library, it could spread across various sectors, from discrete manufacturing to process industries. This is usually easier said than done. The versatility of AutomationML is a selling point, but the real test will be in its actual deployment across diverse environments. I wonder how many companies will adopt this. The challenges of implementing this library across different platforms are not trivial. Managing tool compatibility and ensuring seamless function across all interfaces has historically been a major hurdle for interoperability efforts. These two massive companies may have underestimated this factor. This collaboration between Siemens and ABB might improve project documentation and data consistency, which would be a boon for manufacturers. Fragmented data environments are a real problem when using multiple proprietary systems. This is a problem for the entire industry.
Looking ahead, the potential to integrate emerging technologies like AI and IoT into this standardized AutomationML library is forward-thinking. It seems like they're trying to prepare for the future of smart manufacturing, which is commendable. While the concept is certainly compelling, the practical effectiveness of this collaborative library remains to be seen in real-world conditions. It's all well and good on paper, but manufacturers will be looking for concrete evidence of its benefits before fully committing. I, for one, will be very interested to see how this plays out in actual factories. There are many theoretical benefits to the system, but it also may be overly complex.
More Posts from patentreviewpro.com: