Carburetor Choke Valve Innovations Recent Patent Developments in Cold Start Technology
Carburetor Choke Valve Innovations Recent Patent Developments in Cold Start Technology - Spring-Biased Choke Valve for Automatic Cold Starting

The spring-biased choke valve is a key component in achieving smooth cold starts by managing airflow into the carburetor. By restricting airflow, it increases the vacuum within the intake manifold, leading to a richer fuel mixture necessary for initial ignition in cold environments. Although other methods like mechanical or electric chokes exist, the simplicity of the spring-biased design promotes dependable operation and reduces the frequency of adjustments. The clever design leverages temperature sensitivity to gradually open the valve as the engine warms up, restoring the proper air-fuel ratio. This gradual adjustment is vital for ensuring a seamless transition from cold-start conditions to normal operating temperatures. The development of spring-biased and other choke valve technologies reflects ongoing efforts to improve cold starting capabilities. While there's no single perfect solution, these innovations offer a glimpse of how automakers are tackling the complexities of engine cold starts to ensure reliable operation.
1. Spring-biased choke valves rely on a spring's force to partially close the throttle when an engine is cold, supplying a richer air-fuel mixture for better starting. This is critical for cold engine conditions where the fuel needs to be more concentrated for easier ignition and smoother initial running.
2. The beauty of these systems lies in their responsiveness to temperature changes. Some utilize bi-metallic strips that physically alter their shape with temperature, indirectly adjusting the choke position without electricity. It's a clever way to make a purely mechanical system adaptive.
3. One appealing aspect is their potential for better fuel economy. Unlike older systems that fully blocked air, these can be designed to partially restrict it based on actual temperature. This reduces the amount of fuel wasted when warming up, which is beneficial for both the environment and drivers' wallets.
4. Their adaptability is another plus. Spring-biased systems are designed to be tuned with precision for various engine designs. This means they can be tailored to work well in many engines, from old-timers to modern cars, demonstrating their versatility.
5. A comparison to traditional designs often highlights a quicker and more reliable response with these valves. The simplicity of a spring-based system can be faster and more reliable than vacuum or manually-operated systems. This reduces the lag or inconsistency that older designs sometimes experienced.
6. Recent innovations, as seen in patents, center on using adjustable springs for specific performance needs. This level of tuning gives the ability to optimize cold start performance for different environments and engine types, making it very useful for the design of engines.
7. Unlike older choke designs known for their proneness to jamming and sticking, the simpler design of spring-based chokes is generally less susceptible to these issues. This simplicity, with improved material choice, results in a more durable and easier-to-maintain system.
8. Some newer designs incorporate temperature-sensing features that react to the actual engine's internal temperature, rather than just the outside air. This nuanced approach leads to more precise control and therefore a better engine performance during operation.
9. The relatively simple nature of spring-biased systems keeps costs down for manufacturers. While electronic systems are gaining popularity, spring-based chokes remain a compelling option for many applications due to their lower manufacturing costs, especially when it comes to mass production.
10. Advances in metallurgy and spring design mean that these components can withstand the rigors of repeated thermal cycles and stresses seen in modern engines. This makes them well-suited for engines that are under more extreme conditions and helps manufacturers meet the demands of performance optimization.
Carburetor Choke Valve Innovations Recent Patent Developments in Cold Start Technology - Bimetallic Spring Element in Cold Start Systems
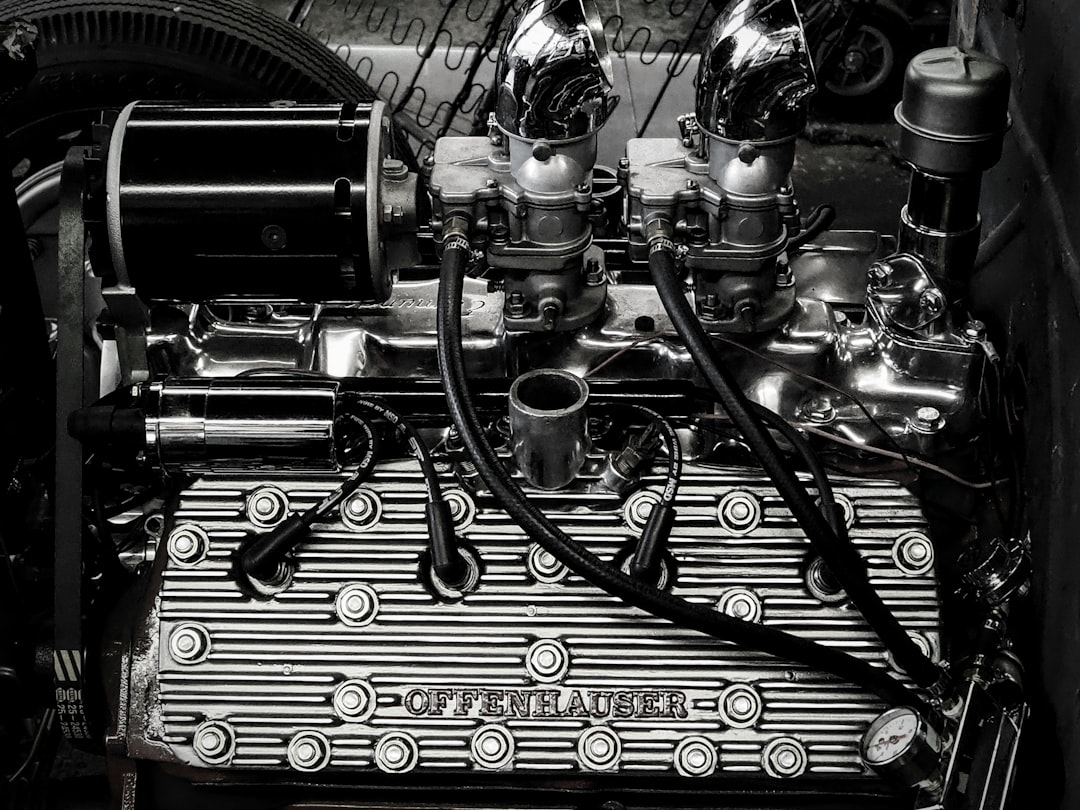
Within carburetor cold start systems, the bimetallic spring is a core element for managing the choke valve. Its ability to expand and contract with temperature changes allows it to precisely adjust the choke position, which controls airflow into the engine. This is particularly crucial for cold starts, as it helps to provide a richer fuel mixture for easier ignition and a smoother initial engine operation. Improvements in this area often focus on using Positive Temperature Coefficient (PTC) heating elements alongside the bimetallic spring, making the choke more responsive to temperature changes, and adapting to varying environmental conditions.
Compared to older choke designs, bimetallic springs offer a notable improvement by lessening the chances of issues like sticking, which could cause excessive fuel consumption. Sticking or jamming can severely hamper the engine's performance. The ongoing research and development efforts in this area continue to explore ways to optimize the bimetallic spring element for a broader range of engine types, showing that even simple, mechanical systems like this are still capable of refining their performance through design improvements. These advances refine the bimetallic spring's role in achieving efficient cold starts and help engines reach optimal operational temperatures faster.
1. Bimetallic springs in cold start systems rely on the principle of differential thermal expansion. They're made of two different metals bonded together, each expanding or contracting at a different rate when heated or cooled. This difference in expansion causes the spring to bend, creating a force that controls the choke valve's position.
2. One intriguing aspect of bimetallic springs is their ability to operate across a broader temperature range compared to simpler spring designs. This wider operating window makes them suitable for various climates, from frigid winters to surprisingly hot summer mornings, potentially extending their utility in different geographic regions.
3. A notable benefit of using bimetallic springs is their precision in achieving specific choke valve closure temperatures. This is particularly advantageous for engines demanding exact air-fuel mixtures during cold starts, a feature often crucial for higher performance engine designs.
4. A crucial concern with bimetallic springs, however, is the potential for material fatigue over time. Repeated heating and cooling cycles can gradually alter the spring's properties, potentially leading to inconsistencies in operation. Engineers must carefully select materials and design the spring to withstand these thermal cycles and ensure longevity.
5. The responsiveness of bimetallic springs adds to their efficiency. They react quickly to temperature fluctuations, which translates to a more immediate and efficient adjustment of the choke. This quick response helps mitigate the delays that can affect engine starting efficiency in cold conditions.
6. Recent patents reveal clever innovations in this space. Some designs combine bimetallic springs with electronic sensors, blending classic mechanical control with modern electronic feedback. This marriage of technologies could potentially enhance the engine's cold-start performance through more intricate control.
7. It's interesting that some researchers are investigating using shape memory alloys alongside bimetallic springs. Shape memory alloys 'remember' their original shape and can return to it when heated, potentially offering a more refined way to control the choke valve's position. This area of research could yield innovative choke designs in the future.
8. Fatigue testing on bimetallic springs has shown that extreme temperature cycling results in distinct wear patterns, which can impact the long-term reliability of these systems. Understanding these wear patterns could be valuable for predictive maintenance programs that anticipate potential component failures in engineered systems.
9. The manufacturing of bimetallic springs involves specialized techniques like welding or bonding two different metals, each with specific thermal properties. Achieving a reliable bond in the fabrication process is crucial for consistent performance. This detailed production process can involve advanced manufacturing technology, contributing to higher component quality.
10. While electronic chokes are gaining traction, the mechanical simplicity and compact size of bimetallic springs remain attractive in engine compartments where space is at a premium. This makes them well-suited for use in a wide range of modern engines, particularly those in smaller automobiles where space is limited.
Carburetor Choke Valve Innovations Recent Patent Developments in Cold Start Technology - Dual PTC Heating Resistors for Enhanced Choke Response
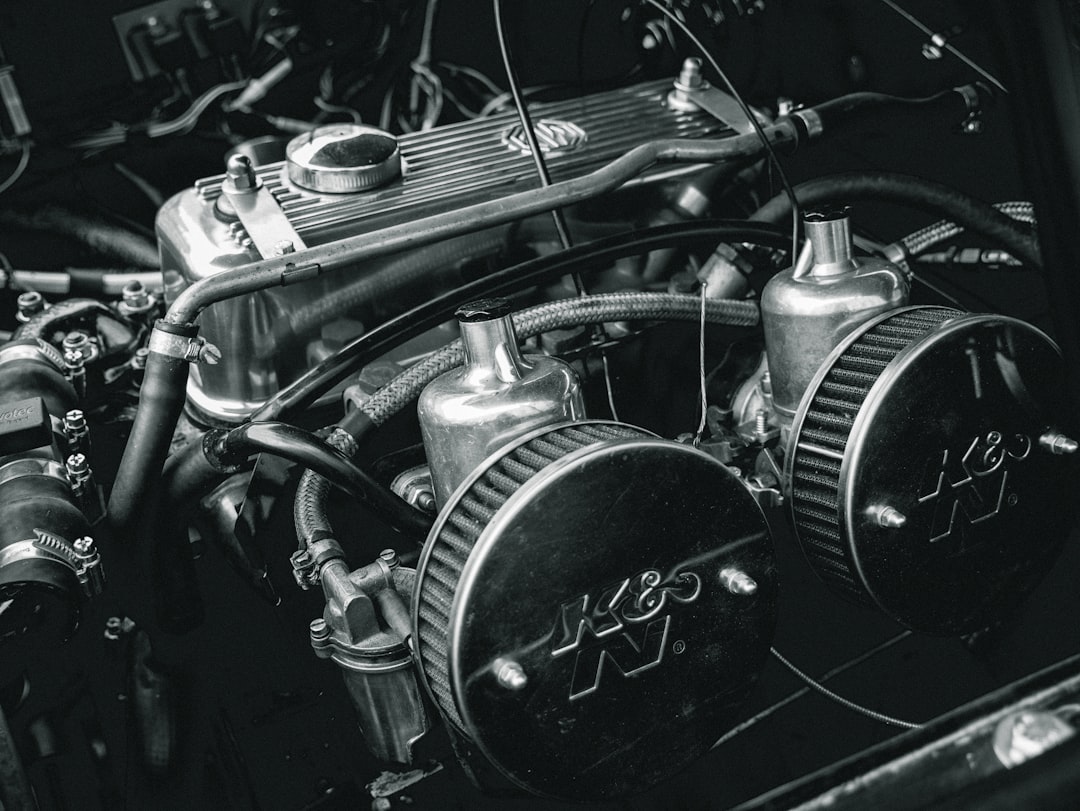
Recent patent applications highlight a new approach to improving carburetor choke valve response, particularly during cold starts: dual Positive Temperature Coefficient (PTC) heating resistors. These resistors are intended to boost the speed and reliability of the choke system, addressing shortcomings of older systems. The focus is on incorporating electric choke conversions, simplifying installation and making them usable with a wider range of carburetors. The faster heating and greater adaptability of PTC resistors are anticipated to lead to more consistent and trouble-free cold starts. However, as with any new technology, it is important to thoroughly assess their long-term durability and overall consistency before widespread adoption. Continued research in choke valve design will be key to ensuring that these systems deliver a reliable and effective cold start experience for all types of engines and conditions.
1. Utilizing two Positive Temperature Coefficient (PTC) heating resistors seems like a clever approach to making carburetor choke valves react faster, especially when starting a cold engine. The localized heating they generate should allow the choke to adjust more rapidly to temperature changes, potentially leading to quicker and smoother engine starts.
2. The faster heating from dual PTC resistors could lead to better fuel mixing during cold starts. If the fuel vaporizes and mixes with air more efficiently, the engine's combustion process should be optimized right from the beginning, which is critical when the engine is cold. This could potentially improve the efficiency of the initial cold starts.
3. Having two PTC resistors introduces a degree of redundancy into the system. If one were to fail, the other could still provide enough heat for the choke to work correctly. This is a nice safety feature that ensures the cold-start process isn't completely reliant on a single component.
4. A fascinating aspect of PTC materials is that their resistance goes up as they get hotter. This means the resistors essentially self-regulate their heat output, which is a valuable safety measure. This built-in safeguard reduces the risk of the choke overheating and potentially causing damage to nearby components.
5. The flexibility to position these resistors in different parts of the carburetor is quite interesting. It suggests that the choke's responsiveness can be tailored for specific engine designs. Depending on how the carburetor is built, you can likely adjust the resistor placement to optimize the choke's response for particular engine types.
6. If the choke opens more quickly due to faster heating, it might mean shorter engine warm-up times. A faster warm-up could have positive implications for fuel efficiency, as the engine gets to its optimal operating temperature sooner. It also seems that the smoother transition from the cold start to normal operation could improve efficiency as a whole.
7. Compared to traditional heating elements, which often rely on complex electrical control circuits, PTC resistors are incredibly simple. Their reliance on temperature changes for operation simplifies the integration into a carburetor system. This simpler approach can contribute to a more reliable and potentially cheaper system.
8. The possibility of more fine-tuned choke response with dual resistors is intriguing. Adjusting the performance of each resistor could allow the choke to better accommodate a wider range of ambient temperatures. This could be particularly useful in regions with highly variable climates.
9. Some research suggests that dual PTC resistors could lead to lower emissions during cold starts. By getting the engine to its optimal operating point more quickly, the amount of incomplete combustion that occurs during the initial cold start can be potentially reduced. That's certainly a desirable outcome from an environmental perspective.
10. The use of dual PTC heating resistors in choke applications is a sign of the ongoing improvements in thermal management within internal combustion engines. It showcases a move away from solely mechanical systems towards more sophisticated and adaptable technologies. This evolution could contribute to both better engine performance and increased reliability.
Carburetor Choke Valve Innovations Recent Patent Developments in Cold Start Technology - Spring-Loaded Choke Lever Release Mechanism
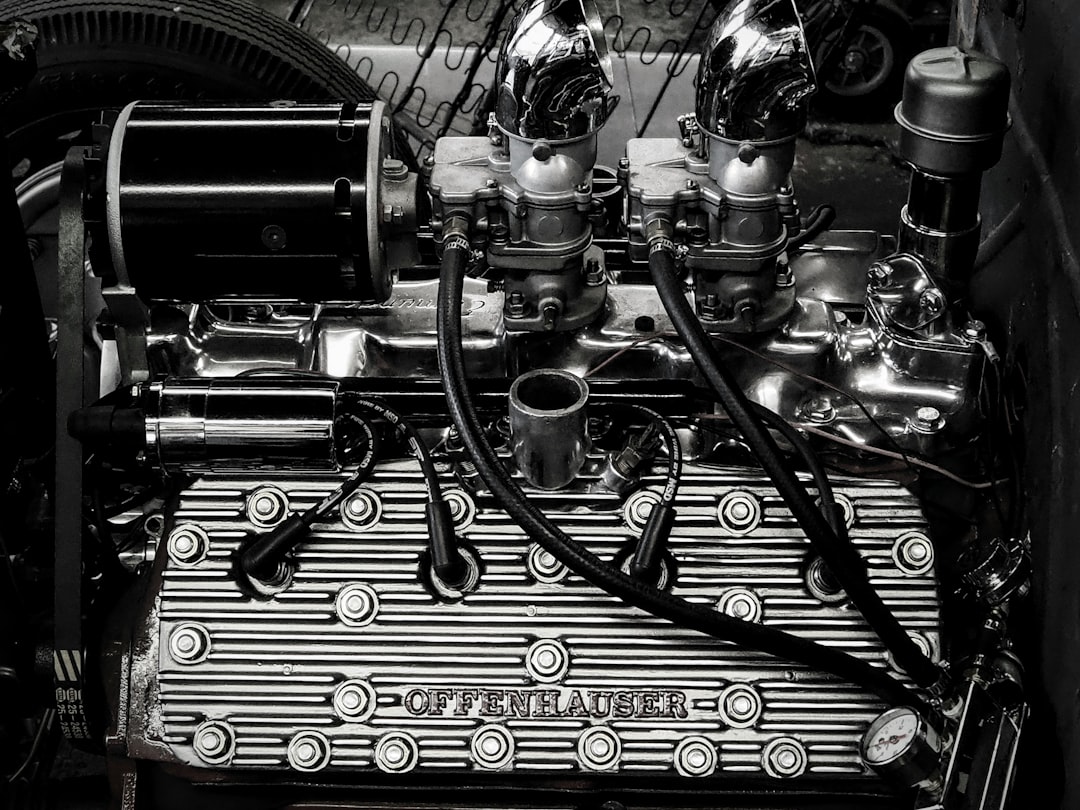
The spring-loaded choke lever release mechanism offers a refined approach to controlling the choke valve in carburetors, primarily focused on improving cold-start performance. This mechanism uses a spring to regulate the choke's position in response to temperature changes, thereby adjusting the air-fuel mixture during engine startup. This mechanical solution addresses concerns related to manual or inaccurate choke settings, which can lead to overly rich fuel mixtures and subsequently, poor engine performance when warming up. The straightforward design of the spring-loaded system promotes dependable operation, reducing the frequency of adjustments and potential maintenance issues, in contrast to more intricate electronic choke systems. It demonstrates a continued pursuit of optimizing carburetor function, especially during the critical cold-start phase, where optimal fuel delivery is essential for reliable engine ignition and smooth operation. While the core concept is relatively simple, this type of mechanism shows the continuing efforts to improve engine performance, specifically when the engine faces the challenge of cold starting.
1. Spring-loaded choke lever mechanisms can be engineered for a quicker response compared to older systems, which sometimes experience delays due to mechanical limitations. This swift action is especially helpful in cold conditions where a fast, efficient start is crucial.
2. Unlike electronic choke systems that can be vulnerable to harsh environments due to their complex wiring and circuitry, the basic mechanical nature of spring-loaded levers makes them dependable in cold, wet, or icy conditions where electronics might falter.
3. Some spring-loaded choke designs allow for adjusting the spring tension. This flexibility gives engineers the ability to fine-tune the choke's response based on the specific engine or the environment it will be used in, optimizing performance in different applications.
4. The strength of the spring can be precisely tuned to deliver various degrees of choke closure. This means the system can be customized for both high-performance engines that need very specific fuel mixtures and those designed for fuel economy, highlighting a wide range of application potential.
5. Modern manufacturing methods allow the use of advanced materials in the spring mechanism, resulting in springs that are both stronger and lighter. This not only boosts durability but also can reduce overall engine weight—a significant consideration for performance-oriented engines.
6. Compared to electronic choke systems, spring-loaded mechanisms are often more compact, which provides more freedom when designing the layout of engine compartments. This makes them appealing for applications where space is limited, like compact vehicles or high-performance designs.
7. A possible drawback in spring-loaded systems is the impact of temperature changes on the spring's behavior, leading to a potential for hysteresis (delay in response). Engineers must be careful in choosing the spring materials and design to minimize any sluggishness caused by heating and cooling cycles, making it a challenging aspect of the engineering process.
8. The simplicity of the spring-loaded mechanism makes it easier to maintain and repair. Fewer moving parts and components mean lower potential for wear and tear over time compared to more complex systems with sensors or other electronic elements. This can translate into reduced maintenance costs in the long run.
9. Some recent patent applications show systems with dual springs, which are meant to provide more refined control over choke positioning by using springs with different characteristics. This dual spring approach could lead to better control during cold starts and potentially reduce over-choking issues.
10. When integrating spring-loaded choke levers, engineers must consider not only the spring's properties but also how it affects airflow into the intake manifold. This interdisciplinary approach of spring dynamics and airflow creates an intriguing optimization challenge for improving fuel delivery and engine starting performance.
Carburetor Choke Valve Innovations Recent Patent Developments in Cold Start Technology - Temperature-Sensitive Choke Valve Positioning
Temperature-sensitive choke valve positioning has emerged as a noteworthy development in carburetor design, particularly in addressing the challenges of cold engine starts. The core idea is to automatically adjust the choke valve's position based on the engine's temperature. This is achieved using mechanisms like bimetallic springs or adjustable tension systems, which react to temperature changes and regulate the flow of air into the engine. By controlling the air-fuel mixture in this way, the engine can achieve the ideal ratio needed for easy ignition and smoother operation when it's cold.
Recent innovations, like spring-loaded choke lever release mechanisms, seek to streamline choke control and reduce the need for manual adjustments. This simplified design can improve reliability and potentially lessen maintenance compared to traditional choke systems. However, there are some potential drawbacks to consider. For example, the materials used in temperature-sensitive mechanisms can degrade over time with repeated heating and cooling cycles. Furthermore, ensuring a fast and consistent response to temperature changes can be a complex engineering challenge. It will be crucial for future research and development to address these challenges to ensure that temperature-sensitive choke valve systems provide consistently reliable and efficient cold start performance across a wide range of conditions.
1. It's interesting that temperature-sensitive choke valve positioning seems to improve cold start emissions by finely tuning the air-fuel mixture when the engine first starts. This suggests that engineering a precise temperature response could benefit both engine performance and reduce pollution during initial engine operation.
2. A common way to enhance the temperature sensitivity of choke valves is to use materials with varying responses to heat. This lets engineers control how the choke reacts to temperature changes very precisely. It shows that materials science plays an increasing role in improving these mechanical systems.
3. Lots of recent designs use adjustable links to control the choke lever, which gives engineers a way to fine-tune how the choke responds based on the engine type and the temperature ranges the car might experience. This customization is really valuable in locations with big differences in weather.
4. Temperature-sensitive chokes often have safeguards that limit how much they can close. This stops the engine from getting too much fuel if the sensors make a mistake about the temperature. These safety elements are becoming more important as they contribute to a more dependable engine.
5. Since temperature changes wear down mechanical parts, some makers are looking into using springs that are treated with extremely cold temperatures (cryogenics) in their choke systems. This treatment can potentially make the springs last longer, especially in places with really hot or cold weather.
6. In more advanced systems, the choke can be linked to other engine control systems. This creates a complex feedback system that can adjust other factors, like the timing of the spark, based on where the choke is. This can improve the engine's overall performance and how well it starts in the cold.
7. While automated choke systems are good, it's tricky to make them very reliable. Some engineers are looking into ways to create backup systems that keep the cold start feature working even if the primary sensors fail. This ensures reliable cold starts in various situations.
8. Even though temperature-sensitive chokes are dependable, they can sometimes struggle to react quickly to rapid temperature changes because of their basic mechanical design. This is prompting some to explore combining mechanical and electronic elements for more adaptability.
9. Some recent improvements involve using computer simulations (finite element modeling) to predict how the choke's parts will react to different temperatures. This helps engineers make better design choices and pick materials that optimize how the choke works.
10. One of the big challenges is getting the temperature-sensitive systems to respond consistently in different conditions. Even small changes in the spring stiffness can affect the choke valve's behavior quite a bit, so there's a lot of research focused on making the parts incredibly accurate and precise.
Carburetor Choke Valve Innovations Recent Patent Developments in Cold Start Technology - Exhaust-Heated Bimetallic Coil for Gradual Choke Opening
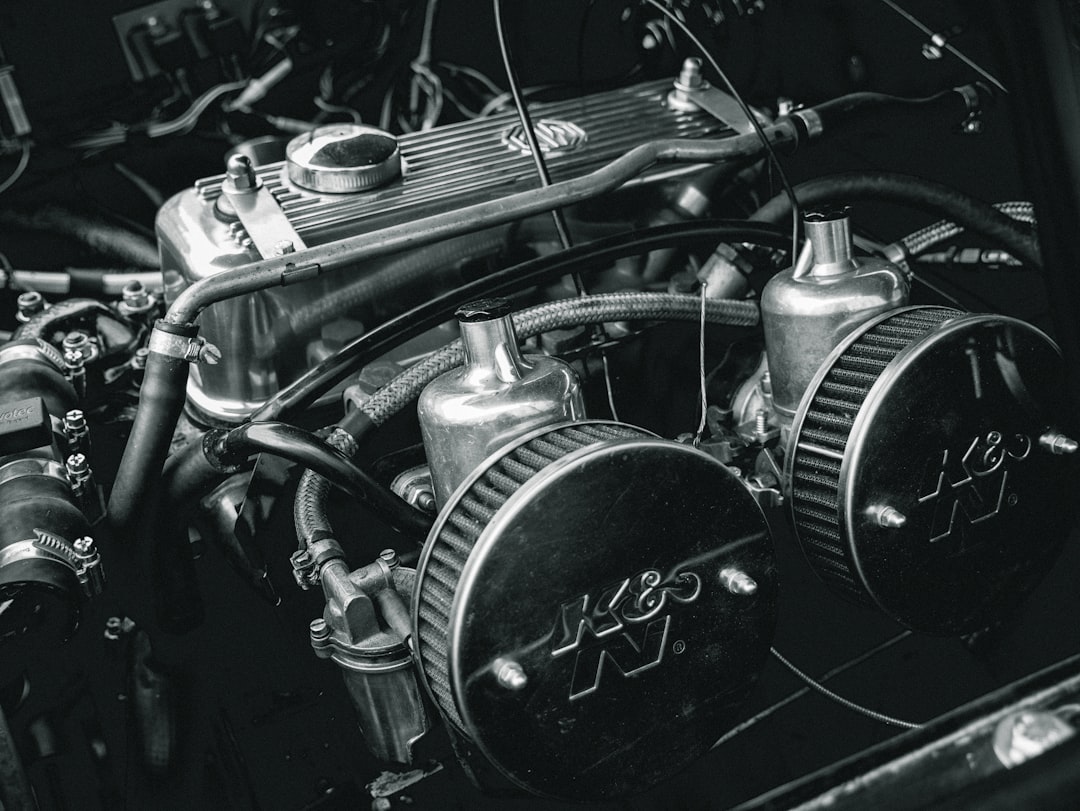
In carburetor design, the "Exhaust-Heated Bimetallic Coil for Gradual Choke Opening" offers a way to refine the cold start process. The core of this system is a bimetallic coil designed to react to the heat from the engine's exhaust. This clever approach helps the choke valve open slowly as the engine warms up, leading to a more controlled adjustment of the air-fuel mixture. By achieving a smoother transition from the initial, rich fuel mixture needed for cold starts to a more balanced mixture as the engine warms, it can improve how smoothly the engine runs and help reduce pollution from excess fuel. It also tackles a weakness of standard systems: reliability in cold environments. The exhaust heat helps the choke operate more consistently in colder conditions.
However, any mechanical system faces challenges, and this one is no different. The materials in the coil can degrade with repeated temperature changes, leading to potential inconsistencies. Keeping the choke's performance steady over time is an engineering problem that needs ongoing attention. There is always a need for more refinement to ensure it delivers consistently reliable cold start performance in a variety of environments.
1. Using the engine's exhaust heat to warm a bimetallic coil is a clever way to make the choke open gradually as the engine warms up. This seems like a more effective approach to cold starts, potentially leading to better fuel economy compared to systems that just rely on the ambient air temperature.
2. It's interesting how this design reuses waste heat from the exhaust. It's a good example of how engineers can make better use of the energy that's already being generated by the engine, potentially improving efficiency in the process.
3. One benefit of using the exhaust for heating the bimetallic coil is that the choke's operation is tied to the engine's actual temperature, rather than just the outside air. This could be very helpful in places with big variations in weather because the system is more adaptive.
4. The way the two different metals in the bimetallic coil expand at different rates when heated creates a controlled force that adjusts the choke position. It's a good illustration of how a simple, purely mechanical system can be made to react to temperature changes without needing any electronics.
5. Compared to older choke designs that were more prone to getting stuck or jamming, the use of exhaust heat might help reduce these problems. It's likely that the more consistent heating from the exhaust improves the movement of the coil over time compared to systems that rely on more basic spring mechanisms.
6. The slow opening of the choke with this design seems like it would be less prone to flooding the engine with too much fuel during a cold start. That gradual control is important for smoother engine starting, since quick adjustments can lead to problems with the air-fuel mixture.
7. Having the choke opening controlled in this way likely helps control emissions, especially during cold starts. By managing the air-fuel mixture carefully as the engine warms up, it could help meet stricter emissions standards and improve air quality in the process.
8. There's potential to tailor the response of this system by choosing specific materials for the bimetallic coil. It seems like the design could be optimized for different engine types and driving conditions by carefully selecting the metals used in the coil.
9. One of the strengths of this system seems to be its simplicity. It's made up of fewer parts than some electronic choke systems, which potentially improves reliability and reduces the chances of failures that might interrupt engine operation.
10. Some of the patent applications in this field hint at making the coil design more complex, perhaps with some kind of variable geometry. This suggests that engineers are working towards even more precise control of the air-fuel mixture as engines warm up, which could potentially improve overall engine performance.
More Posts from patentreviewpro.com: