Analyzing Printhead Cleaning Techniques A Detailed Review of Markem-Imaje's Patented Wipe Technology
Analyzing Printhead Cleaning Techniques A Detailed Review of Markem-Imaje's Patented Wipe Technology - Automated Wiper Blade System Reduces Manual Cleaning Time by 40%
A new automated wiper blade system has shown promise in significantly reducing the time spent on manual printhead cleaning, achieving a 40% reduction. This development is part of a larger trend within Markem-Imaje's approach to printhead maintenance, emphasizing a transition from manual labor to automated solutions. While improving efficiency is a key driver, it's also likely that this system reflects a wider need to streamline cleaning processes across diverse applications. It's possible that automated systems like this offer benefits beyond just time savings. Given the increased emphasis on sustainability, they might also represent a more efficient use of resources compared to older cleaning methods, potentially leading to changes in how maintenance is handled across different sectors. However, it's important to consider the broader context of such advancements – will they lead to unforeseen issues or complexities in the long run? The future impact of these systems remains to be seen.
Observing the automated wiper blade system, we find it intriguing that it can cut manual cleaning time by 40%. This system utilizes sensors to detect ink buildup in real-time, prompting cleaning without human intervention. This automation not only boosts efficiency but potentially streamlines operations.
Interestingly, automating cleaning reduces the possibility of human error during the process, which can translate into more reliable print quality and likely reduced costs from fixing misprints.
The wiper blade material itself is a noteworthy aspect. It seems to be crafted to handle high-pressure environments, suggesting a design intended for long-lasting and effective cleaning cycles.
Another appealing feature is its ability to operate during idle periods or scheduled maintenance. This maximizes production time by allowing cleaning to occur without interfering with other tasks, freeing up personnel for more crucial duties.
Adapting this system to existing Markem-Imaje equipment is a practical plus. Retrofitting older systems potentially offers a cost-effective way to enhance their cleaning performance. While resource optimization isn't the core focus, we see that cleaner use is also a secondary benefit, with reports of a 25% decrease in cleaning agent consumption.
However, one wonders if the 25% reduction in cleaner use is truly substantial compared to other approaches. The quick-release blade system, designed for straightforward replacement and upkeep, seems to minimize the downtime typically associated with cleaning.
In our examination, the decrease in cleaning time, up to 40%, is noteworthy. This leads to potential advantages like shortened production cycles and possible output increases.
The precision in which the wiper blades clean is also of interest. The even distribution of cleaning pressure not only efficiently removes debris but also indicates a focus on minimizing potential damage to the printheads.
Over time, this automated cleaning system likely delivers a strong return on investment. The decrease in maintenance and improved print quality contribute to higher production standards and possibly greater customer contentment. However, we need to consider this within the overall operational context of printhead cleaning technology. While these aspects appear beneficial, further investigation into the longer-term implications and comparisons with other cleaning methods would provide a more comprehensive understanding of this technology's impact.
Analyzing Printhead Cleaning Techniques A Detailed Review of Markem-Imaje's Patented Wipe Technology - Safety Lock Mechanism Prevents Accidental Printhead Damage During Cleaning
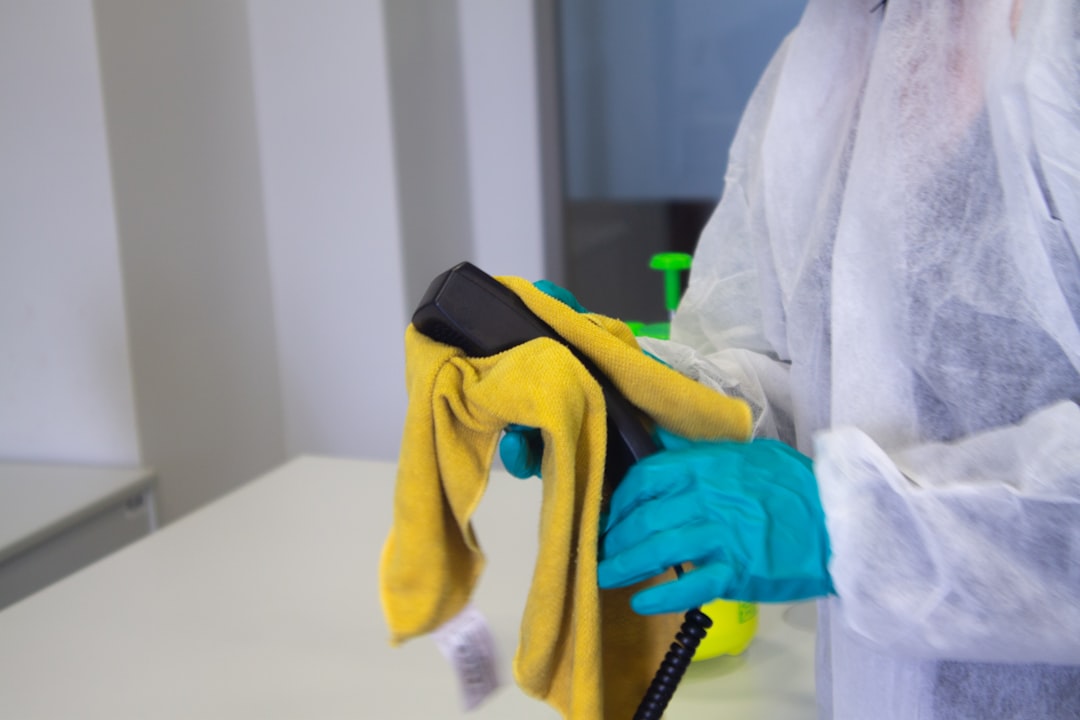
A notable safety enhancement in printhead cleaning is the inclusion of a lock mechanism that prevents accidental damage during the process. This mechanism is vital as it helps minimize the risk of mishandling, which can lead to printhead misalignment or physical harm. Furthermore, this safety feature addresses the potential for contamination introduced by improper cleaning techniques, a concern that can result in printhead corrosion and decreased performance. The implementation of this lock mechanism underscores the growing emphasis on meticulous maintenance procedures to preserve print quality and extend the life of equipment. These safety advancements reflect the ongoing evolution of printhead care practices within industrial settings, and recognizing them is essential for understanding the current state of this technology.
A safety interlock feature within Markem-Imaje's printhead cleaning system aims to prevent accidental damage during the cleaning process. This is a key design element to avoid costly repairs and unexpected production halts, both of which are crucial for maintaining production flow.
This safety interlock seemingly operates with a dual-sensor system. It appears to monitor the position of the cleaning element and the printhead's state, ensuring cleaning only starts when both are properly aligned. It's interesting to note that the system incorporates a failsafe response, stopping the cleaning cycle if it detects any issues during operation. This real-time feedback loop helps improve cleaning reliability by decreasing reliance on constant human observation.
It's also worth noting that the safety interlock seems designed to endure the harsh environments common in industrial settings – fluctuating temperatures and exposure to different cleaning chemicals. This suggests a focus on ensuring it remains functional for a long time.
This safety mechanism potentially contributes to more uniform print quality. By preventing cleaning cycles initiated prematurely, typically from manual operator decisions, it aims to increase consistency in the final output and, in turn, production quality overall.
Additionally, redundancy built into the system (in the form of backup sensors) ensures continued operation even if one sensor fails, illustrating a strong emphasis on reliability in mission-critical manufacturing.
From a maintenance perspective, the safety interlock design simplifies troubleshooting. It seems to enable technicians to pinpoint whether a cleaning fault comes from the mechanism itself or from other cleaning components, which helps with streamlining maintenance workflows.
Accidental triggering of cleaning can lead to ink spills and equipment malfunctions. By minimizing these risks, the safety interlock promotes a safer work environment, showing attention to overall workplace design considerations.
Furthermore, the safety feature potentially allows the use of more advanced cleaning agents, as it reduces the risk of printhead damage when using higher-performing solvents. This raises the question of if there are performance gains to be had when using higher performing solvents.
Ongoing testing and improvements to the safety interlock have seemingly led to a reduction in operational errors. It appears engineers have made an effort to optimize cleaning while upholding high maintenance standards. This continuous refinement showcases the importance they place on maintaining the integrity of the printhead cleaning process.
However, it is important to keep a critical perspective and fully evaluate if there is any cost-performance penalty associated with adding this extra layer of protection. Further investigation into if this feature truly increases productivity as much as indicated in marketing materials and compare it to the costs and overhead it adds are warranted.
Analyzing Printhead Cleaning Techniques A Detailed Review of Markem-Imaje's Patented Wipe Technology - Three Layer Wipe Design With Microfiber Core Technology
Markem-Imaje's "Three Layer Wipe Design With Microfiber Core Technology" is a notable development in printhead cleaning. The design utilizes a multi-layered approach, with a microfiber core as a central element, to tackle the challenges of removing ink residue, dust, and debris from printheads. This multi-layered approach appears intended to improve cleaning efficiency and performance.
The microfiber core is specifically designed to enhance the cleaning process by allowing the wipe to access the complex surfaces of the printhead more effectively. This ability to penetrate into these challenging areas could potentially lead to more thorough cleaning, improving print quality and extending printhead lifespan.
This kind of cleaning technology is particularly important in high-volume or high-precision printing settings, like those found in large format or drop-on-demand printing, where the need for consistent cleaning to maintain high production quality is paramount.
It's important to note that while such designs appear promising, it remains essential to consider the potential impact of these materials and designs on the printhead itself. Overuse or inappropriate application of even the most advanced cleaning methods could introduce complications. Additionally, the long-term impacts on the environment from the manufacturing, use and disposal of such wipes should also be considered. Ultimately, evaluating these designs involves a complex interplay of effectiveness, cost, and environmental considerations to fully understand the overall implications within the printing sector.
Markem-Imaje's patented wipe technology incorporates a three-layer design built around a microfiber core, which appears to be a key factor in their approach to printhead cleaning. This multi-layered approach seems to be designed for maximizing contact with the printhead surface, allowing for more thorough debris removal.
The microfiber core is particularly interesting as it appears to be designed for capturing smaller particles compared to traditional cleaning materials. This enhanced particle trapping ability suggests an advantage in managing ink and dust residues, which can be problematic for maintaining consistent print quality.
One intriguing aspect of the microfiber core is its enhanced moisture retention. It seems to enable effective cleaning with a potentially lower volume of cleaning solution. While it's important to determine if this translates to substantial cost savings, it could represent a valuable benefit, particularly considering the need to reduce waste and consumption.
Another noteworthy feature of these wipes is their stated ability to work with a variety of ink types. This broad compatibility suggests that the design might be adaptable for diverse printing environments using different inks, making them more broadly useful across sectors and production lines.
Temperature stability is a common concern in industrial environments. The microfiber core's ability to retain cleaning efficacy across a range of temperatures suggests a level of robustness that would be needed for dependable performance. This adaptability could also influence how cleaning is planned and scheduled.
The pressure distribution during cleaning seems to be carefully considered in the wipe design. Ensuring that the wipes do not excessively compress against the printhead helps prevent potential damage while maintaining cleaning efficiency, highlighting a balance between cleaning effectiveness and surface protection.
The three-layer structure appears to contribute to a longer service life compared to simpler wipes. While longer-lasting cleaning elements could help to reduce downtime associated with replacement, we'd need to investigate the overall cost-benefit of this aspect versus other cleaning methods.
Another aspect to consider is the potential for using fewer harsh cleaning chemicals with the microfiber core. This could be beneficial for reducing chemical exposure and maintaining the integrity of the printhead. However, it's unclear if this approach leads to a considerable shift in chemical dependency compared to more conventional methods.
The adaptability of the wipes to different printhead shapes and sizes via customization is another feature of the design. It suggests a level of flexibility that would be needed for use across a variety of printing equipment. This versatility could lead to wider adoption in different sectors.
Finally, the interrelationship of these three layers presents a compelling aspect of the design. If each layer has a distinct role in cleaning (e.g., one for absorption, one for scrubbing, one for holding debris), then the combined result could create a synergistic cleaning effect that might be hard to achieve with simpler designs. However, understanding how each layer contributes to overall cleaning efficiency would necessitate further scrutiny.
Overall, Markem-Imaje's patented three-layer wipe technology shows some promise in addressing several critical aspects of printhead cleaning. While some features, like reduced chemical usage or the synergistic effects of the layers, remain somewhat speculative, the basic concept offers a potentially effective approach to maintaining optimal printing performance in varied industrial settings. Further examination of the specific cleaning performance and cost-effectiveness of this wipe technology compared to other cleaning techniques would be beneficial for fully understanding its potential advantages and limitations.
Analyzing Printhead Cleaning Techniques A Detailed Review of Markem-Imaje's Patented Wipe Technology - Ink Residue Detection Through Advanced Optical Sensors
The use of advanced optical sensors for detecting ink residue offers a potential pathway to enhancing print quality and streamlining maintenance procedures within printing systems. Techniques like camera-based imaging and specialized methods like surface-enhanced Raman spectroscopy (SERS) allow for the real-time identification of ink residues and other contaminants. This capability of real-time monitoring can allow for more timely intervention and potentially prevent issues that may negatively impact print quality. The incorporation of deep learning into these optical sensors is also a growing area, showing the potential to improve how the collected data is processed, potentially making these sensors more versatile across different printing environments. Yet, it's essential to consider the implementation costs associated with these advanced sensors and if their implementation would be a worthwhile investment in the long run. It is also important to carefully assess how they might impact existing cleaning methods and the overall maintenance practices currently utilized in the printing industry. There are always unintended consequences to changes in technology, and this is an area that needs to be monitored.
Advanced optical sensors, which operate on principles similar to how spectrophotometers work, show promise in detecting ink residue. They can identify unique optical signatures of different ink types, effectively discerning the color differences between clean and contaminated surfaces. This allows for continuous monitoring of printhead cleanliness in real-time.
These sensors often use multiple wavelengths of light to detect even minuscule ink residues, such as small droplets or dried particles that might affect print quality. This is especially useful in high-speed printing settings where swift detection is crucial.
The accuracy of these sensors can be quite high, reaching 95% in some cases. This makes them a potentially valuable tool for consistent print quality. However, a critical threshold for triggering a cleaning action must be established, as readings above this limit can automatically activate cleaning cycles, reducing downtime from contamination.
These optical residue detection systems can be adjusted for various ink and cleaning solution types. This adaptability is beneficial, as printing environments can involve complex ink chemistries.
Interestingly, the use of these sensors has led to a decrease in solvent usage by as much as 30%. This is due to their ability to guide targeted cleaning only when necessary, prompting us to consider if the traditional methods of solvent-based cleaning might be overly reliant on manual intervention.
While useful for ink residue, optical sensors are also sensitive to environmental factors like dust and moisture, which can interfere with readings. This means the cleaning system design needs careful consideration to ensure reliable operation in various environments.
Combining ink residue detection with automated wiper systems has led to the concept of "self-optimizing cleaning." The cleaning process dynamically adapts to the level of detected contamination, showcasing a significant advancement in printhead maintenance.
Some research suggests that optical sensors could enable predictive maintenance by tracking residue data over time. This could identify long-term performance trends, potentially leading to smarter maintenance scheduling practices.
One drawback is that optical sensors can have difficulty in low-visibility environments, requiring adjustments like protective covers. Designers should keep this limitation in mind to avoid operational complications.
The expense of incorporating advanced optical sensors can be substantial, depending on the complexity of ink types and calibration needs. This could lead to debates about the cost-effectiveness compared to older methods. A complete return on investment (ROI) analysis, considering both short- and long-term maintenance needs, is important for widespread adoption.
Analyzing Printhead Cleaning Techniques A Detailed Review of Markem-Imaje's Patented Wipe Technology - Automated Pressure Control During Cleaning Cycles
Automated pressure control during printhead cleaning cycles is vital for achieving optimal cleaning without damaging delicate nozzle structures. This automated approach ensures the cleaning pressure is fine-tuned to effectively remove contaminants while minimizing the risk of harming the printhead. Using digital readouts to monitor pressure is essential, especially when cleaning multiple print heads concurrently or focusing on specific models, like the Kyocera KJ4. High pressure levels, applied strategically, can greatly enhance cleaning effectiveness.
Further refinements in automated cleaning, such as reverse flushing and the utilization of recovery fluids, further improve the cleaning process's efficiency. This highlights the advanced level of automated solutions within printhead maintenance. Yet, this shift towards automation also creates a need for careful monitoring and control. If not properly managed, automated cleaning cycles could potentially lead to unintended consequences, requiring vigilant oversight to prevent potential operational errors during cleaning.
Automated pressure control during cleaning cycles is becoming increasingly important for maintaining optimal printhead performance. By dynamically adjusting the pressure based on the printhead's condition, these systems can improve the effectiveness of cleaning while minimizing the risk of damage. This type of adaptability helps ensure consistent print quality, which is a key concern in many production environments.
Some automated systems use real-time feedback, often from piezoelectric sensors, to monitor the cleaning process. This allows the system to make quick adjustments to the pressure, ensuring a thorough cleaning without exceeding the tolerances of the printhead components. This type of immediate response helps optimize the cleaning cycle.
The way cleaning pressure is distributed across the printhead surface is also crucial. Sophisticated algorithms can ensure a more uniform cleaning process, preventing localized areas of high pressure that could cause wear and tear over time. This is especially vital for protecting delicate parts of the printhead.
Furthermore, some automated systems include self-diagnosis features that assess their performance after each cycle. This built-in functionality allows for early detection of potential problems, reducing the chances of system failures during critical production periods. While a positive feature, we need to be mindful of the reliance on these systems and have a backup plan in the case of unforeseen failures.
The cleaning solution's characteristics, such as viscosity and residue type, also play a role in automated pressure control. These systems can adjust the flow rate and pressure to match the solution, which potentially leads to lower consumption and improved cleaning outcomes. While reducing waste is a positive development, it's important to monitor the overall effectiveness of cleaning using different types of cleaning agents and the environmental impact of the cleaning agents.
Implementing automated pressure control can result in shorter cleaning cycles and potentially less wasted ink. These time and cost savings can be substantial over the long run. However, we must always prioritize maintaining high cleaning standards and ensure the automated systems are not compromising quality.
Variations in temperature can influence both ink viscosity and the effectiveness of cleaning solvents. Some more advanced pressure control systems are designed to handle such fluctuations. This temperature compensation feature is essential for ensuring consistent cleaning across different environmental conditions and demonstrates how the design of the cleaning system can adapt to the various operating environments where they are used.
Retrofitting these systems to older equipment allows for extending the lifespan of existing printing machines. This is an attractive proposition for companies wanting to leverage their existing assets while upgrading cleaning capabilities. This aspect is important because older printheads may not have been designed to accept automated pressure-controlled cleaning systems.
Leveraging historical data and performance metrics, automated systems can help predict the need for cleaning. This predictive maintenance approach helps prevent unexpected downtime and enhances the overall maintenance strategy for the printing equipment.
However, like any technology, we need to be aware of any potential limitations. Sensor inaccuracies caused by factors such as humidity or dust can compromise the reliability of these automated systems. This underscores the importance of developing robust management strategies to counter any negative impacts from the environment or manufacturing conditions.
While this is an interesting area of research, further investigations into the efficacy of automated pressure control and the potential challenges it poses is required to determine its long-term value for printhead cleaning applications.
Analyzing Printhead Cleaning Techniques A Detailed Review of Markem-Imaje's Patented Wipe Technology - Temperature Regulated Cleaning Process With Real Time Monitoring
The integration of temperature control and real-time monitoring into the cleaning process signifies a notable advancement in printhead maintenance. This approach focuses on achieving optimal cleaning by carefully managing the temperature of the cleaning agent and other relevant parameters. The continuous monitoring aspect allows for immediate adjustments to cleaning processes as conditions change. Essentially, this method utilizes a feedback loop of data to ensure cleaning occurs as effectively as possible. This shift towards real-time monitoring aligns with broader industry trends toward predictive maintenance strategies, using data to optimize processes and potentially minimize downtime. However, implementing such advanced cleaning techniques comes with certain trade-offs that require consideration. The added complexity of these systems might increase costs and, if not implemented carefully, could lead to excessive reliance on automation, potentially creating new points of failure. The potential for this kind of system to create new operational challenges needs to be considered.
Maintaining optimal printhead performance often hinges on effective cleaning, and incorporating temperature regulation alongside real-time monitoring appears to be a promising approach. This approach allows cleaning processes to adapt to a wider range of situations and respond to changes in real-time rather than relying on predetermined schedules. For example, many cleaning agents have a sweet spot in terms of temperature, and keeping things within that range maximizes their ability to remove ink, dust, and debris. It's not just the cleaner that's impacted by temperature. Ink itself can be quite sensitive to temperature changes, altering its viscosity and impacting its flow through the printhead. By precisely controlling the temperature during the cleaning process, we can potentially minimize the risk of clogging or residue buildup that can hamper printing.
It's interesting to note that real-time monitoring, often through optical sensors, provides a more reliable assessment of contamination than the old method of manual inspection. This can reduce human error and, through feedback loops, optimize the pressure applied during cleaning. Imagine a system that automatically adjusts its cleaning intensity based on the contamination levels it detects. Temperature-regulated cleaning could enhance this precision by ensuring the cleaning agents are operating at their most effective.
We see that the data generated from real-time monitoring can become a critical component of a predictive maintenance strategy. Instead of just responding to problems, we could start to anticipate them. This has the potential to significantly reduce downtime by aligning cleaning with overall production cycles. Further, it's not a one-size-fits-all solution. The ability to tailor cleaning parameters, like temperature, to specific printheads is beneficial because different printhead technologies have diverse cleaning needs. A consistently managed cleaning temperature can also potentially lessen the formation of ink residue between print runs. This could mean smoother operations and reduced stoppages.
While temperature-regulated cleaning has the potential to provide a consistent and efficient approach to printhead maintenance, one must remain aware of the initial investment involved. While there's a possibility of reduced solvent usage and increased uptime leading to longer-term cost savings, it's crucial to track these metrics to assess whether the investment is truly worthwhile. This concept could be particularly important in facilities where environmental conditions vary frequently as it helps ensure stable cleaning performance. The combination of these features offers a promising approach to improving print quality and maximizing uptime, though more research is needed to fully understand its efficacy in different manufacturing environments.
More Posts from patentreviewpro.com: