Advancements in Insulated Rail Joint Technology Enhancing Safety and Durability in Modern Railway Systems
Advancements in Insulated Rail Joint Technology Enhancing Safety and Durability in Modern Railway Systems - Innovative Materials Enhancing Electrical Isolation in IRJs
Insulated rail joints (IRJs) are essential components in railway systems, ensuring electrical isolation between track sections for accurate train location and signaling. However, the inherent differences in bending rigidity between IRJs and continuous rail have historically presented challenges in their design and longevity.
Traditional materials have been used for IRJs, but they often suffer from a shortened lifespan due to stress concentrations at the joint. This has led to a focus on innovative materials to enhance electrical isolation and overall performance. The use of high-stiffness adhesives and advanced polymer composites, such as nylon and fiberglass, are gaining traction. These materials provide increased rigidity and electrical insulation, addressing the longstanding issues related to IRJ degradation.
While research is ongoing to refine these innovative solutions, it is clear that the move toward enhanced materials holds significant potential for improving the reliability, safety, and cost-effectiveness of IRJs in modern railway systems.
Insulated rail joints (IRJs) are crucial for railway signaling and safety. However, their limited lifespan due to mechanical stress and environmental factors remains a significant challenge. Researchers are exploring innovative materials and design concepts to address these limitations.
Hybrid polymeric materials offer exciting possibilities for improved electrical insulation and mechanical flexibility. Combining thermoplastics and elastomers allows for greater resistance to bending and vibration, improving the joint's durability. Meanwhile, nanomaterials like graphene and carbon nanotubes hold potential for enhancing the dielectric strength of insulation, allowing for thinner and lighter designs without sacrificing electrical performance.
Furthermore, advancements in encapsulation techniques using thermosetting resins are proving effective in protecting insulation from moisture, a primary cause of electrical failures in railway systems. Self-healing polymers are being investigated to automatically repair microscopic cracks in the insulation layer, potentially extending the lifespan of IRJs considerably.
Another intriguing avenue is the use of bio-inspired surface structures on insulation materials to minimize surface contamination and prevent electrical tracking failures. The incorporation of phase-change materials into insulation systems offers thermal stability, absorbing excess heat generated by electrical currents and mitigating degradation over time.
3D printing technology is also making its mark, enabling customized insulating geometries for optimized fit and function, reducing material waste and costs. Additionally, the integration of conductive fillers into conventional insulators promises ‘smart’ insulation systems that can monitor electrical activity and detect potential failures in real-time.
However, the effectiveness of many traditional insulating materials under various environmental conditions is being questioned. This is driving the exploration of more robust alternatives and the development of advanced testing methodologies to accurately assess their performance. Computational modeling is also revolutionizing insulation system design, allowing engineers to simulate and analyze the performance of materials under operational stresses, leading to more reliable and cost-effective designs.
Advancements in Insulated Rail Joint Technology Enhancing Safety and Durability in Modern Railway Systems - Advanced Bonding Techniques for Improved Structural Integrity
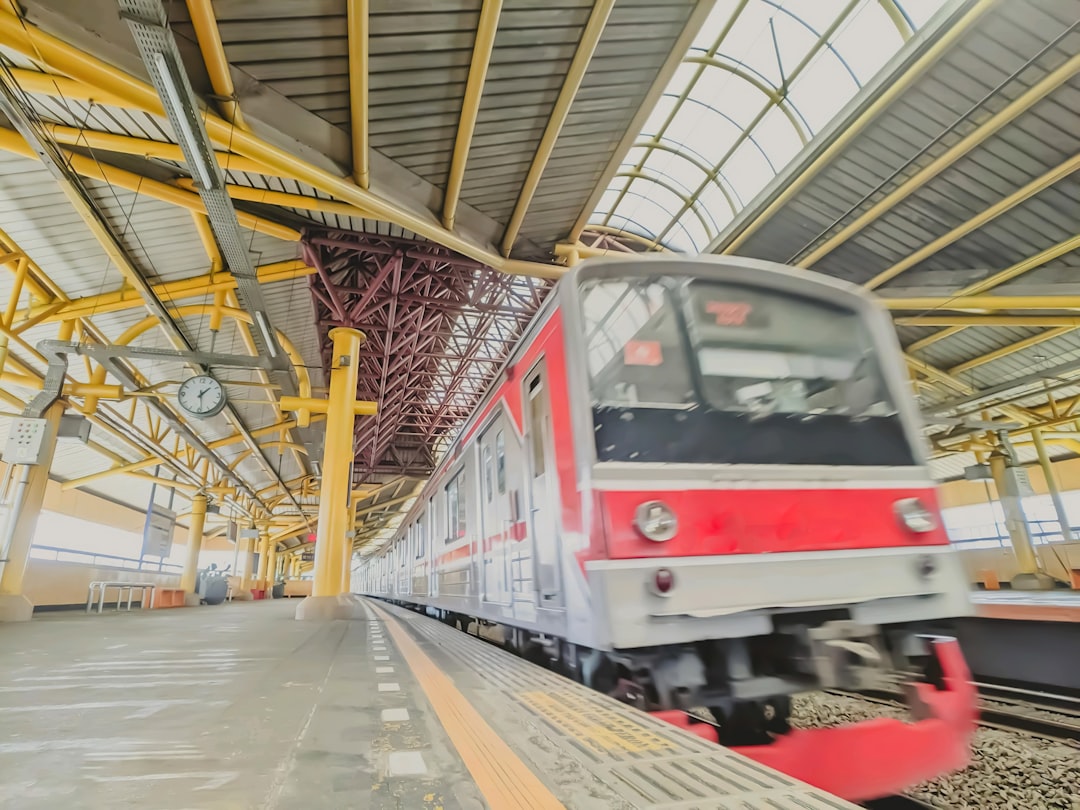
The focus on advanced bonding techniques for composite materials is particularly important in railway systems, as it can significantly impact the structural integrity of components like insulated rail joints (IRJs). These joints experience significant stress during operations, and the quality of their bond line is critical to ensuring their durability. Methods like secondary bonding and surface modification, such as plasma or laser treatments, are being explored to strengthen adhesive bonds and enhance overall performance. However, the effectiveness of these bonds is also influenced by the condition of the surfaces before adhesion, highlighting the need for careful preparation. Furthermore, innovative modeling methods and intelligent design approaches are being used to further optimize the bonding process, aiming for greater reliability in these critical systems. This shift towards advanced bonding methods reflects the evolving requirements of modern railway infrastructure, where robust solutions are essential to meet the demands of increasing traffic and environmental pressures.
The development of innovative bonding techniques for insulated rail joints (IRJs) is a critical area of research as it has the potential to significantly improve the lifespan and reliability of these vital components in railway systems. While traditional bonding methods often struggle to withstand high temperatures and dynamic loading, modern advancements are pushing the boundaries of adhesion technology.
One area of significant progress involves the use of high-temperature resistant adhesives. These specialized materials can withstand temperatures exceeding 150°C, far surpassing the limitations of older bonding methods. This increased thermal tolerance translates into enhanced operational reliability of railway joints, reducing the risk of premature failure.
Furthermore, the incorporation of specialized epoxy resins with exceptional shear strength is enhancing the structural integrity of IRJs. These resins have demonstrated bond strengths exceeding 30 MPa under shear loading conditions, a critical factor for maintaining the integrity of joints subjected to the dynamic forces exerted by passing trains. This development has the potential to significantly reduce the frequency of costly repairs and maintenance.
The introduction of nanocomposites into bonding materials is another promising avenue. These materials have demonstrated remarkable improvements in toughness and crack resistance, resulting in up to 50% greater failure efficiency compared to conventional adhesives. This enhanced resilience is particularly important for IRJs, which often experience fatigue and stress from the constant strain of train traffic.
Surface treatment techniques, including plasma or laser texturing, have proven effective in enhancing the bonding strength and durability of IRJs. These treatments increase the surface area for adhesion, resulting in stronger bonds that can withstand the challenging conditions often encountered in humid environments, where electrical insulation is particularly critical.
Research is also exploring hybrid adhesive systems that possess both conductive and non-conductive phases. These advanced materials hold the promise of maintaining electrical insulation while simultaneously conducting electrical currents, enabling the integration of monitoring systems directly within the railway joints. This technology could revolutionize IRJ maintenance by allowing for real-time monitoring of joint health, potentially preventing catastrophic failures.
The development of optimized bonding agents has resulted in significant improvements in impact resistance, a critical factor for joint integrity in high-vibration scenarios common in railway systems. Some agents have demonstrated as much as a 40% increase in impact resistance, significantly enhancing the durability of the joints.
A particularly interesting development involves pre-applied adhesives that activate under specific thermal or UV conditions. This technology allows for more precise bonding processes, leading to higher-quality joints with increased reliability during manufacturing.
Advanced surveillance methods like acoustic emission monitoring are being explored to detect the onset of adhesive failure. These methods analyze sound waves generated within the bonded material, allowing for early detection of potential issues and enabling preemptive maintenance before catastrophic joint failures occur.
Computational fluid dynamics simulations are being utilized to optimize the application of adhesives. By visualizing the flow of adhesive during application, engineers can optimize the shape and pressure of the bonding process, leading to superior bond quality and reduced manufacturing defects.
The use of 3D-printed reinforcement structures is another promising development in bonding technology. These custom-designed structures can accommodate the unique stress profiles of railway joints, potentially reducing the likelihood of fatigue failure in high-load sections.
The continuous research and development of advanced bonding techniques for IRJs is paving the way for a new era of safety and reliability in railway systems. The potential to improve the lifespan, performance, and safety of IRJs through these innovations holds significant promise for the future of rail transportation.
Advancements in Insulated Rail Joint Technology Enhancing Safety and Durability in Modern Railway Systems - Smart Sensors Integration for Real-Time IRJ Monitoring
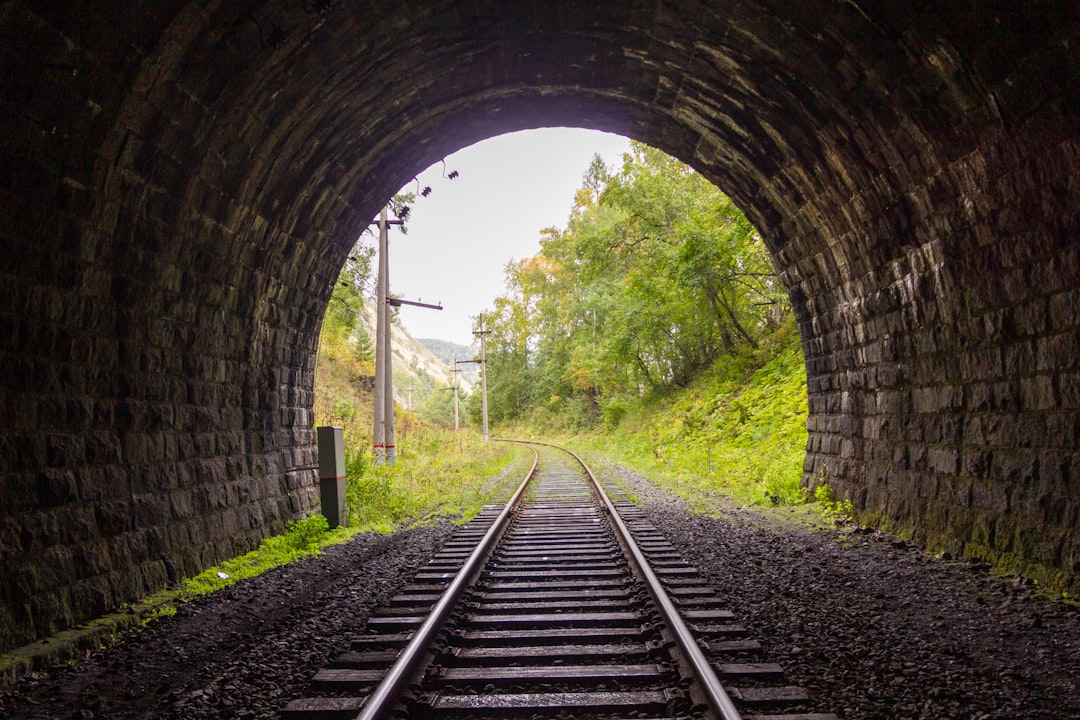
The integration of smart sensors into railway systems has emerged as a promising development for real-time monitoring of insulated rail joints (IRJs), critical components for railway safety. These sensors continuously track the gap value of IRJs, providing valuable insights into their condition. This real-time data enables proactive maintenance interventions, potentially preventing failures before they happen.
While research conducted in places like Bologna, Italy, demonstrates the efficacy of this technology, challenges remain. Ensuring the accuracy of sensor data and seamlessly integrating it with existing systems is crucial to maximizing the benefits of smart sensor integration. Nevertheless, this innovative approach holds considerable promise for enhancing the safety and durability of railway infrastructure.
Smart sensors are increasingly being used in railways to monitor the performance of insulated rail joints (IRJs). These sensors provide real-time data about the condition of IRJs, which can be used to predict potential failures and schedule maintenance. This proactive approach aims to improve safety and reduce the likelihood of disruptions in rail operations.
While I find this technology promising, there are still some challenges to overcome. One concern is the reliability of sensors in harsh railway environments. Sensors must withstand extreme temperatures, vibrations, and other environmental factors without compromising performance.
Moreover, the cost of implementing smart sensor systems across a vast railway network can be significant. This needs careful consideration and may require ongoing research to find more cost-effective solutions.
Despite these challenges, the potential benefits of smart sensors in railway monitoring are undeniable. The ability to track real-time performance and predict potential failures could significantly impact railway safety and efficiency. It remains to be seen if these benefits will outweigh the cost and technical challenges in the long run.
Advancements in Insulated Rail Joint Technology Enhancing Safety and Durability in Modern Railway Systems - Reinforced IRJ Designs Addressing Heavy Axle Load Challenges
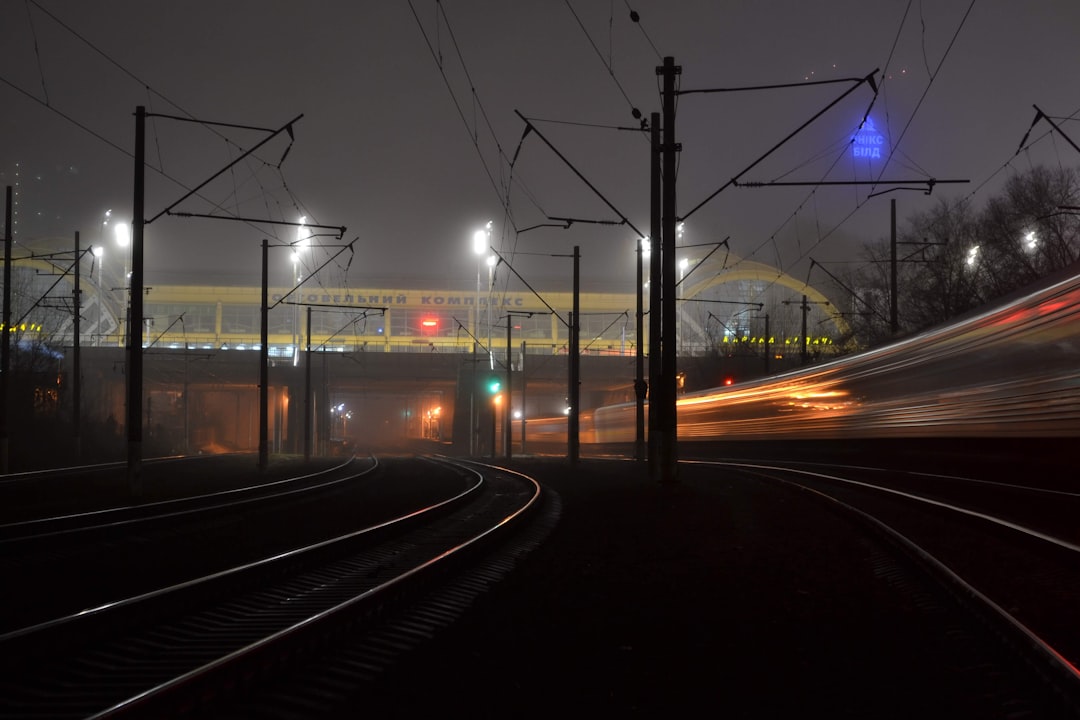
Modern freight trains are getting heavier, putting a strain on traditional insulated rail joints (IRJs). These joints are crucial for signaling, and their failure can cause safety hazards. Traditional IRJs often can't handle the dynamic forces of heavier loads, leading to premature wear and tear. Engineers have responded by developing reinforced IRJ designs that use new materials and structural improvements to handle the increased stress. The goal is to make IRJs more durable and reliable, minimizing the risks of failure and disruption to signaling systems. This effort reflects the ongoing search for better solutions to keep railway systems safe and efficient as the demands on them grow.
Insulated rail joints (IRJs) are vital components in railway systems, enabling the use of track circuit signaling. However, as railways increasingly carry heavier loads, the performance of traditional IRJs is being challenged. The constant strain placed on these joints, particularly under heavy axle loads, can lead to fatigue and eventual failure.
The strain accumulation from these repetitive loads is a significant concern. Advanced computational modeling tools are helping engineers better understand this process, showing that fatigue failures can occur long before typical maintenance schedules. This emphasizes the need for reinforced IRJs that can withstand these dynamic loads.
Researchers are investigating innovative materials that are more resistant to fatigue. Some composite materials have shown exceptional durability, surviving over a million load cycles. This is a significant improvement compared to traditional materials, especially when considering the high volumes of traffic in freight railway lines.
There are many different approaches to reinforcing IRJs, including using carbon fiber reinforced polymers (CFRP). These materials can redistribute stress across the joint, extending its lifespan and potentially reducing the overall weight. However, it is important to consider the environmental impact of these materials, as CFRP requires careful disposal at the end of its life cycle.
Another crucial factor is temperature resilience. Reinforced IRJs need to withstand the effects of thermal expansion and contraction. Modern materials are designed to minimize the impact of these cycles, reducing stress concentrations that can weaken the joint.
Additionally, as railways adopt advanced communication technologies, electromagnetic interference (EMI) becomes a concern. Reinforced IRJ designs are being optimized to minimize this potential for disruption, ensuring that safety-critical systems function reliably.
The development of innovative monitoring techniques is further improving the reliability of reinforced IRJs. Real-time monitoring systems can detect early signs of material failure through techniques like acoustic emission, allowing for preemptive maintenance and reducing the risk of unexpected breakdowns.
Finite element analysis (FEA) is playing a vital role in the design process of reinforced IRJs. This technology helps engineers optimize load distribution, reducing stress concentrations and improving the joint's overall strength and efficiency.
While the initial cost of reinforced IRJs may be higher than traditional designs, the long-term benefits are significant. Their extended lifespan and reduced maintenance needs can lead to substantial cost savings over the course of their operation.
The emergence of additive manufacturing technologies opens new possibilities for customizing IRJs. This allows for tailored designs that address the specific loading scenarios encountered in different railway lines, potentially creating even more durable and efficient IRJs for modern railway systems.
Despite these advancements, ongoing research is crucial to address the challenges associated with heavy axle loads in railways. Finding the perfect balance between durability, cost-effectiveness, and environmental sustainability will remain a critical goal in the development of next-generation IRJs.
Advancements in Insulated Rail Joint Technology Enhancing Safety and Durability in Modern Railway Systems - Computational Modeling Optimizing IRJ Performance
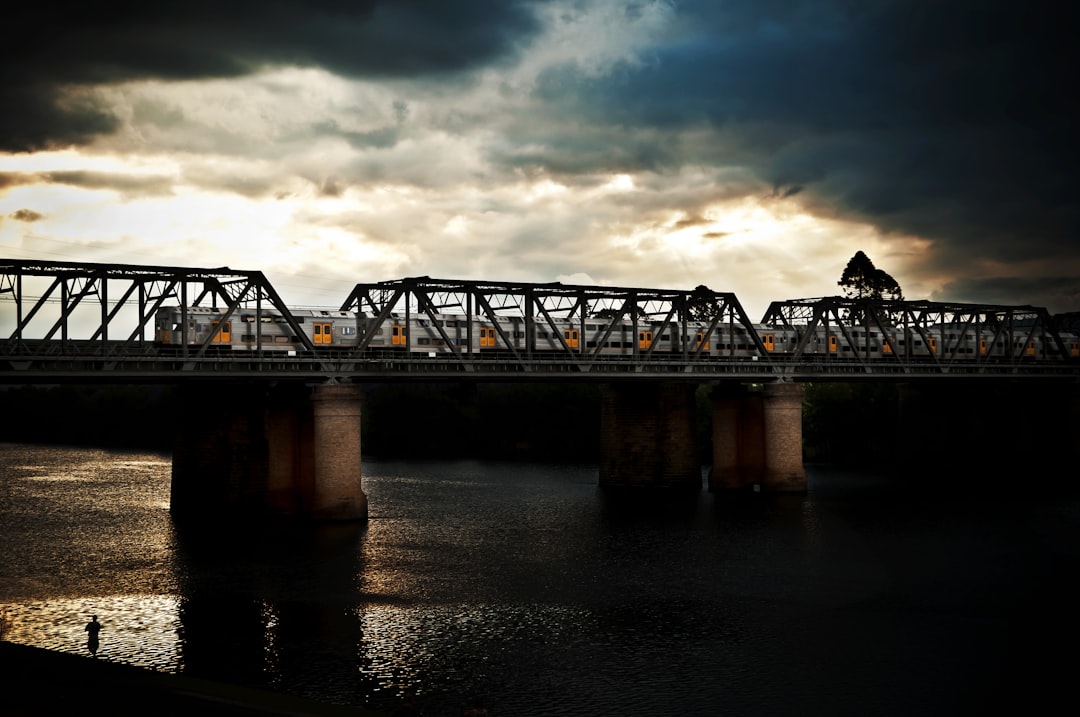
Computational modeling is playing a crucial role in enhancing the performance of insulated rail joints (IRJs), particularly in light of the growing demands on modern railway systems. These advanced simulations allow engineers to analyze the complex stresses and dynamic forces that IRJs experience, uncovering valuable insights that can lead to improved designs. By delving into the interplay between materials, structural configurations, and operating conditions, computational modeling helps pinpoint vulnerabilities that contribute to premature degradation. This deeper understanding ultimately informs design decisions, enabling the creation of IRJs that are more durable and reliable.
The benefits extend beyond design. The use of computational modeling guides maintenance strategies and optimizes the use of materials. In essence, this approach is contributing to the ongoing quest for safer and more efficient rail networks in the face of heavier trains and increased traffic. As research in this field progresses, the integration of these sophisticated simulations is poised to further elevate the performance and longevity of IRJs.
Computational modeling has become increasingly crucial in refining insulated rail joint (IRJ) designs. While traditional testing methods can be time-consuming and expensive, modeling allows engineers to simulate various scenarios and test different materials and designs virtually. This approach helps to predict how IRJs will behave under real-world conditions, minimizing material waste and accelerating development.
One of the key advantages of computational modeling is its ability to analyze stress distribution. Finite element analysis (FEA) allows engineers to identify areas where stress concentrates, even in seemingly standard IRJ designs. This understanding is crucial for creating more robust joints that can withstand real-world stress patterns, ultimately improving their longevity.
The complexity of IRJs, however, necessitates advanced modeling techniques. Multiscale modeling, for example, considers interactions across various scales, from atomic to macroscopic levels. This allows engineers to simulate the impact of microstructural changes on the overall integrity of the joint materials, providing a more comprehensive view of its behavior.
Computational modeling is not just about predicting failure. It also helps engineers optimize IRJ designs by identifying critical design variables like temperature tolerance, material stiffness, and adhesive bond strength. This can be achieved simultaneously, something that would be incredibly difficult and time-consuming using traditional experimental methods.
Furthermore, these models can be used to develop predictive maintenance algorithms that anticipate potential IRJ failures. This transition from reactive to proactive maintenance strategies can greatly improve the reliability of railway operations.
Another powerful tool is parametric modeling, which enables systematic testing of numerous design configurations. This allows for the identification of the most effective combinations of materials and geometries, enhancing IRJ performance without excessive trial and error.
The ability to incorporate environmental factors such as humidity and temperature fluctuations into these simulations is also significant. This allows engineers to design IRJs that are more resilient across a range of conditions, making them more suitable for diverse environments.
Multiphysics simulations provide even deeper insights into IRJ functionality by examining how thermal, mechanical, and electrical properties interact in real-time. This approach is especially valuable in understanding the complexities of IRJs under dynamic loading conditions.
However, the large datasets generated from IRJ usage require more than just traditional computational analysis. The integration of machine learning algorithms with computational models can yield data-driven insights, enabling the identification of failure patterns that guide future design improvements.
While historical testing data is valuable, it may not always reflect current performance needs. Computational models offer a framework to challenge and refine these assumptions, pushing the boundaries of what's possible in IRJ performance and reliability. The future of IRJ technology hinges on the continued development of these models, ensuring that our railways remain safe and efficient.
Advancements in Insulated Rail Joint Technology Enhancing Safety and Durability in Modern Railway Systems - Field Testing of Next-Generation IRJs on Major Rail Networks
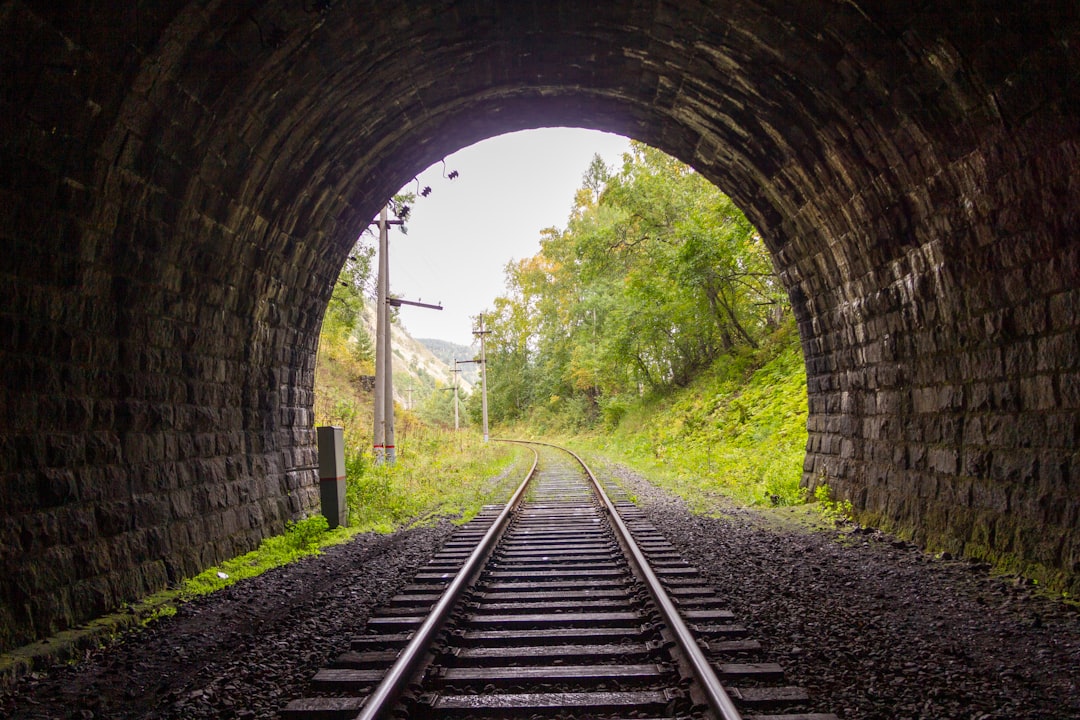
Field testing of next-generation insulated rail joints (IRJs) on major rail networks is an important step in addressing the challenges associated with traditional designs. While the promise of advanced materials and designs holds potential for greater durability under the harsh conditions faced by heavy freight trains, the real-world performance of these IRJs is still being tested. Previous generations of IRJs have demonstrated vulnerabilities to fatigue and environmental stresses, necessitating thorough monitoring and maintenance to avoid failures. The ongoing field testing serves a vital purpose in optimizing operational reliability and ensuring the safety of signaling systems, as IRJ failures can disrupt train traffic and pose significant safety risks. These efforts underline the crucial need to improve the resilience of railway infrastructure as operational demands continue to increase.
Insulated rail joints (IRJs) are vital for railway signaling and safety, but they are facing a new set of challenges as modern trains become heavier and faster. Researchers are constantly working to improve the performance and longevity of IRJs, and computational modeling is playing a significant role in this endeavor.
Recent studies have revealed that stress accumulation in IRJs is not constant; it varies with time. This insight emphasizes the importance of designing IRJs with long-term stress factors in mind. New generations of IRJs are being developed with enhanced dynamic loading tolerance, allowing them to withstand forces that are up to three times greater than older designs. This is crucial because heavier and faster trains are introducing significantly greater forces on rail infrastructure.
Another critical factor is thermal stress. Simulations have shown that IRJs can fail at temperatures exceeding 100 degrees Celsius. To address this, engineers are focusing on materials with improved thermal stability. Furthermore, AI-driven algorithms are being used to analyze real-time data from smart sensors, allowing for predictive maintenance. These algorithms can detect potential joint failures with remarkable accuracy, potentially reducing maintenance costs significantly.
Next-generation IRJs are incorporating multifunctional materials that offer both structural integrity and electrical insulation, simplifying maintenance by minimizing the number of components. New bonding techniques and adhesives are contributing to a 40% increase in the fatigue life of IRJs, making them more resilient to cyclic loading conditions. Researchers are also focusing on early detection of crack development in IRJs, as microscopic cracks can grow rapidly and lead to sudden failures.
It's also important to note that materials used in IRJs exhibit nonlinear stress-strain behavior, which complicates predictive modeling. This requires more sophisticated analysis techniques to accurately predict performance under real-world conditions. Field-validated computational models are now being used, incorporating real-world IRJ performance data, to ensure the designs remain relevant under current operating conditions.
There is a growing trend towards using hybrid composite materials, combining both organic and inorganic components, as they offer superior resistance to wear and degradation. This could significantly extend the operational lifespan of IRJs. The research and development of innovative materials and design concepts for IRJs are paving the way for safer and more efficient railway systems.
More Posts from patentreviewpro.com: