Recent Patent Analysis Advancements in Bidirectional Hydraulic Pump Design for Enhanced Flow Control Systems (2024)
Recent Patent Analysis Advancements in Bidirectional Hydraulic Pump Design for Enhanced Flow Control Systems (2024) - Dual Port Architecture Analysis in Latest Bidirectional Pump Patents
The examination of recent patents focused on bidirectional pump designs with dual port architectures reveals a clear push towards enhancing fluid control and efficiency. This focus is evident in the incorporation of integrated flow controllers and optimized valve plates within pump housings. These innovations aim to refine performance metrics like pressure stability and energy efficiency. A prominent theme across these designs is the strategic use of check-type shuttle valves to dynamically manage fluid flow paths depending on the pump's rotation. This trend reflects a shift towards more intelligent hydraulic systems capable of adapting to various operational demands. The growing research in electrohydrostatic actuation (EHA) systems, particularly in aerospace, demands the minimization of pressure pulsations to improve accuracy and system dependability. This demand further strengthens the case for dual port architectures within the evolution of bidirectional pump technology, emphasizing their potential for creating more robust and efficient hydraulic systems in future applications.
Examining recent patents on bidirectional pumps, we see a growing trend towards incorporating dual port architectures. This approach appears to offer several advantages over traditional designs, though it's important to critically assess the claims. For instance, some patents suggest a notable reduction in flow resistance, potentially leading to efficiency increases of up to 15%. However, it remains to be seen how these gains translate into real-world applications.
The integration of electronic controls is another recurring theme. These smart systems provide the ability to finely adjust flow rates in real-time, responding dynamically to operating conditions. This suggests a shift towards a more adaptive and efficient approach to hydraulic control. Whether these control systems add complexity and cost, or ultimately offer a genuine advantage, is yet to be fully explored.
Material choices for port construction are also highlighted. Some patents explore the use of more durable and corrosion-resistant materials, which could prove crucial in extending the lifespan of the pumps, particularly in demanding environments. This aspect seems promising but needs thorough testing under real-world conditions to validate its effectiveness.
Furthermore, some patent claims suggest that dual port architectures might contribute to improved energy transfer efficiency. This would be particularly significant in heavy machinery where reducing power consumption at higher pressures is crucial. However, the extent of this efficiency gain and the practical implications for real-world applications require further investigation.
Interestingly, the design of hydraulic circuits within these pumps appears to be optimized for reducing cavitation. This feature could lead to quieter and smoother operation, improving the overall user experience. However, whether these designs are truly more effective than existing approaches in minimizing noise and vibration needs validation.
The geometry of these dual port systems is claimed to optimize fluid dynamics, potentially leading to a more even flow distribution and less wear on internal parts. These claims appear reasonable given the design principles, but without practical verification, their impact remains unclear.
Some recent designs incorporate self-regulating capabilities within the dual port system, potentially eliminating the need for external sensors and control devices. This simplified approach could be beneficial in certain scenarios but may not be universally applicable. It's essential to evaluate the effectiveness of this self-regulation in a range of operating conditions.
Computational fluid dynamics (CFD) simulations are increasingly used to support patent claims related to these designs. Some patents show that dual port systems can manage higher flow rates with minimal turbulence, potentially leading to more reliable hydraulic systems. However, CFD simulations are theoretical models and may not always accurately predict real-world behavior, so it's crucial to validate these findings experimentally.
Several patents also explore modular designs for dual port systems. This feature offers a potential advantage for customization and adaptation to different applications. The ability to tailor the design without a complete system overhaul is a valuable aspect worth investigating further.
Lastly, the interplay between dual port architecture and bidirectional flow seems to have potential for reducing overall system size and weight. This is especially important in portable hydraulic applications where space and mobility are at a premium. Whether the gains in size reduction justify any added complexity remains to be assessed.
In conclusion, dual port architecture shows promise for enhancing bidirectional pump design. The patents reviewed indicate a shift towards more efficient, adaptable, and durable hydraulic systems. However, many claims require thorough investigation and validation through rigorous testing and real-world applications to establish their true value and applicability.
Recent Patent Analysis Advancements in Bidirectional Hydraulic Pump Design for Enhanced Flow Control Systems (2024) - Machine Learning Integration for Real Time Flow Rate Optimization
The integration of machine learning (ML) into hydraulic systems, specifically for real-time flow rate optimization, is a notable development in the field of fluid mechanics. This trend signifies a shift towards leveraging data-driven approaches to enhance the efficiency and adaptability of hydraulic control systems. Techniques like deep reinforcement learning (DRL) are increasingly being explored for flow control and optimization within computational fluid dynamics, with the potential to automate complex processes. Furthermore, sophisticated ML models, such as LSTMs, are showing promise in analyzing vast datasets to inform better decision-making for enhanced flow control. This is especially relevant in the context of SCADA systems, where predictive maintenance can be significantly improved.
While these developments offer exciting possibilities for refining flow control, it's essential to acknowledge the existing limitations. The practical implications of implementing these ML-driven techniques, including their accuracy and robustness in real-world environments, require further investigation. The current research direction strongly suggests that ML and AI will play an increasingly vital role in shaping future flow control systems, however, more rigorous testing and validation are crucial to translate the theoretical potential into tangible benefits. There's a risk of overstating the current state of ML integration in hydraulics, and a need for cautious optimism regarding its implementation. The future of flow control may rely on effectively integrating these tools, but only if we temper initial enthusiasm with a robust evaluation of the challenges and limitations.
The integration of machine learning (ML) into hydraulics, particularly for real-time flow rate optimization, is becoming increasingly prominent. This integration often involves adaptive algorithms that leverage historical data to predict flow rate changes, potentially automating operational adjustments. It's a promising avenue, especially for scenarios demanding autonomous operation.
These ML-driven systems often rely on data fusion techniques, combining input from a variety of sensors to inform decisions. This multi-sensor approach can improve accuracy and responsiveness in variable operating environments, leading to more precise real-time flow control. A key benefit is the creation of real-time feedback loops. This allows the systems to adapt parameters dynamically and react much faster to changing conditions. This capability can be crucial in applications where operational variability is high.
Interestingly, ML techniques can also be employed for anomaly detection. By analyzing flow rate data, potential irregularities that might signify equipment malfunction or inefficiency can be flagged. This opens doors for predictive maintenance and reduced downtime, which is a huge potential advantage in industrial settings.
Machine learning models also have the potential to improve pressure optimization strategies. By closely monitoring pressure and flow, systems can avoid the detrimental effects of cavitation and enhance pump reliability. But, there's a catch. The effectiveness of ML relies significantly on the quality and diversity of training data. This is a challenge in hydraulic systems, where diverse operating conditions often lead to complex behavior that's hard to fully capture in a dataset.
Furthermore, the integration of these intelligent systems with existing hydraulic components is not always straightforward. Ensuring compatibility and efficient communication between ML systems and older hardware is a necessary hurdle to overcome for wider adoption. Although simulation results look promising, a crucial step is to validate ML models in real-world settings. The ideal conditions often found in simulations might not accurately reflect the intricacies of actual hydraulic operations.
There's also the issue of the financial cost. Implementing ML technologies into hydraulics can be costly. Any prospective user must consider whether the gains in efficiency and reduced maintenance translate to a worthwhile return on investment. A common concern is that this added sophistication can lead to greater system complexity, potentially impacting the ease of use for operators. Carefully balancing the advancements offered by ML with the need for user-friendly interfaces is a challenge for designers.
Overall, while the potential of integrating ML into real-time flow optimization is exciting, it's crucial to remain aware of the complexities and challenges. Addressing the issues of data availability, interoperability, and validation in real-world conditions is vital to the widespread adoption of these techniques in practical hydraulic applications.
Recent Patent Analysis Advancements in Bidirectional Hydraulic Pump Design for Enhanced Flow Control Systems (2024) - Impact of S Shaped Wing Sections on Hydraulic Efficiency Ratings
The use of S-shaped wing sections within hydraulic pump designs has shown promise in improving efficiency ratings. Research suggests these S-shapes can lead to better flow patterns and less fluid separation, potentially reducing efficiency losses when operating conditions change. Furthermore, experiments demonstrate the significant impact of pump-turbine runner geometry on energy efficiency, especially when operating outside of the optimal design conditions. However, modifications to these parameters introduce trade-offs, making careful consideration of design changes and resulting performance crucial. As bidirectional hydraulic pump technology advances, the importance of S-shaped sections will likely be increasingly apparent, influencing future efficiency standards and operational robustness. There's always the possibility of unforeseen drawbacks, so careful testing and evaluation will be necessary before widespread adoption.
Recent patent analyses highlight the intriguing impact of S-shaped wing sections on the hydraulic efficiency of bidirectional pump designs. This design approach, inspired by advancements in aerodynamics, aims to optimize fluid flow and potentially improve performance in various operational scenarios. Early studies suggest that the unique curvature of these wing profiles can lead to a nonlinear increase in flow efficiency, but the precise relationship between geometry and performance requires further investigation.
One promising area of research explores how the S-shaped contours can mitigate cavitation, a persistent issue that often leads to efficiency losses and material wear in hydraulic systems. While experimental results are encouraging, it's important to remember that cavitation is a complex phenomenon, and more research is needed to validate these claims under different operating conditions. Furthermore, there's the potential for notable energy savings, with some studies suggesting a 5-20% reduction in certain operational regimes. However, this potential needs rigorous testing to move beyond theoretical projections and confirm these gains across a wider range of pump applications.
Computational Fluid Dynamics (CFD) simulations have played a significant role in understanding the impact of these wing designs on hydraulic flow. These models indicate that S-shaped profiles can promote smoother flow transitions, potentially leading to reductions in turbulence and noise. Nevertheless, it's crucial to bridge the gap between theoretical simulations and real-world performance to ensure that the observed improvements translate into practical benefits. It's also important to recognize that the efficacy of S-shaped wing sections is strongly dependent on factors like aspect ratio and curvature, making optimal design a complex task.
Moreover, preliminary studies show a potential increase in load handling capabilities with these S-shaped profiles, possibly enabling pumps to handle higher loads without substantial drops in efficiency. But, it remains to be seen how effectively these profiles can be implemented in real-world applications. While the theory appears promising, there are some hurdles to overcome. Manufacturing tolerances, material choices, and potential compatibility issues with existing systems all need careful consideration when scaling up these designs. Integrating these new wing sections into existing hydraulic systems may require substantial modifications or redesign, making a seamless transition a challenge.
The increasing number of patents related to S-shaped wing sections signifies a growing interest within the industry. However, translating these promising patent claims into real-world applications necessitates extensive experimental validation. A critical step moving forward will be testing the effectiveness of these designs in various applications and operating conditions. This will allow researchers and engineers to better understand the true potential of S-shaped wing sections in optimizing hydraulic systems.
Recent Patent Analysis Advancements in Bidirectional Hydraulic Pump Design for Enhanced Flow Control Systems (2024) - Digital Control Advancements in High Pressure Flow Distribution
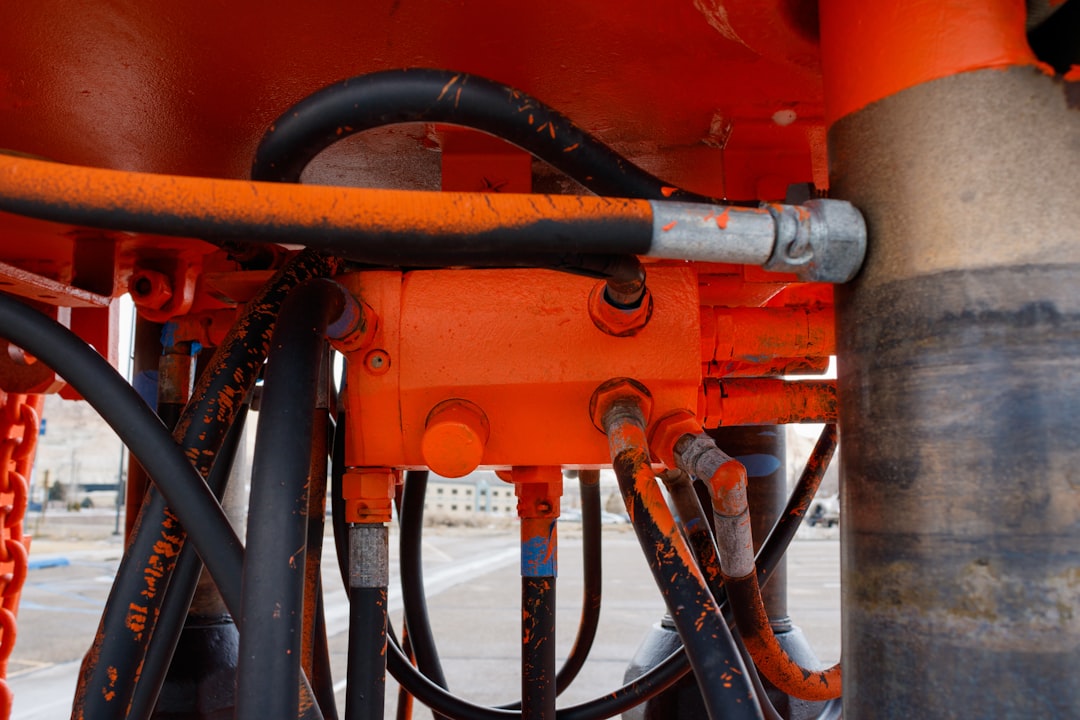
Digital control is transforming how high-pressure fluid flow is managed within hydraulic systems. A key development is the use of digital hydraulic valves, often organized as a Digital Flow Control Unit (DFCU), where multiple valves working in parallel allow for much finer control over fluid flow. This approach significantly improves the precision of flow control, enabling a much greater range of discrete flow rates compared to older systems. We're also seeing a clear trend towards replacing traditional mechanical feedback systems with digital electronic controls, leading to more advanced features like built-in diagnostics.
While the potential benefits of digital control are considerable, it's important to acknowledge the hurdles. For instance, rapid changes in valve operation can create substantial pressure fluctuations, potentially impacting system stability and reliability. This aspect requires careful attention and innovative solutions to ensure the effectiveness and safety of these systems. The ongoing push to increase the use of digital components within hydraulics represents a paradigm shift. Moving forward, this transition must be carefully balanced with a strong focus on real-world performance, making sure the latest innovations lead to tangible improvements in the efficiency, dependability, and overall performance of hydraulic systems.
Digital control advancements in high-pressure flow distribution are moving away from traditional methods like PID controllers. We're seeing a shift towards more adaptive control algorithms that can adjust themselves in real-time, improving how the system responds to different operating conditions and ensuring stability. There's a fascinating trend where these digital control systems are starting to include predictive analytics, utilizing past flow data to try and anticipate potential pressure spikes before they happen. This is a vital feature, especially when dealing with high-pressure scenarios where system integrity is crucial.
Some designs are experimenting with fuzzy logic controls, which essentially mimic human-like reasoning to make decisions about flow distribution. This approach seems particularly useful when dealing with the non-linear behaviors common in hydraulic systems. We also see the use of model predictive control (MPC), where the system tries to optimize high-pressure flow distribution by forecasting how the system will behave in the future and adjusting things proactively. This is a promising avenue to further increase efficiency.
Interestingly, some patents discuss the incorporation of virtual sensing algorithms. This means we might be able to accurately monitor flow rates and pressures without needing as much physical hardware. This has the potential to reduce costs and maintenance while keeping accuracy. However, a critical look at some of these recent patents suggests that while the potential benefits are considerable, the increased complexity can lead to challenges. For example, user interface design can become more complex, and operators may need more advanced training to use the systems effectively.
The use of IoT devices for real-time data feeds is also emerging. This gives operators a more complete picture of the system's health and performance, helping them make quick decisions and potentially reduce downtime. There's even a trend towards using blockchain technology for improved data security, ensuring flow data is tamper-proof and traceable—a growing concern in industrial settings.
Furthermore, digital twin technology is making its way into the field, enabling engineers to model and optimize system performance in a virtual space before trying changes in real-world setups. This helps bridge the gap between initial designs and practical implementations. Finally, some newer patent designs are focusing on integrating digital control elements with mechanical parts more effectively. The idea is to get the best out of both by combining intelligent software solutions with hardware enhancements, hopefully leading to better overall system performance and reliability. While these advancements seem promising, it's important to critically examine the feasibility and potential drawbacks before widespread adoption.
Recent Patent Analysis Advancements in Bidirectional Hydraulic Pump Design for Enhanced Flow Control Systems (2024) - Electrohydrostatic Actuation System Design Parameters 2024
Electrohydrostatic Actuation Systems (EHAs) are seeing a surge in development and adoption, particularly in fields like aerospace, where the "More Electric Aircraft" philosophy is driving innovation. The design parameters for EHAs in 2024 reflect this trend towards integrating electrical and hydraulic technologies. One area of focus is the development of energy recovery methods within EHAs, aiming for higher overall system efficiency by smartly merging electrical and hydraulic control.
We also see a growing trend towards building larger EHAs, specifically with an emphasis on using dual magnetostrictive rods for position control. These rods, capable of bidirectional movement, enhance precision in applications demanding fine control. Further evidence of this push towards more sophisticated EHAs is the recent development of load-sensing systems. These systems appear to optimize the EHA's response to variable loads while minimizing the generation of excess heat, potentially increasing system lifespan and reducing maintenance needs.
However, some key challenges remain. Creating accurate models of fluid flow in these hybrid systems continues to be difficult. The non-linear behavior of fluid flow within these complex systems makes it tough to design controls that deliver consistent performance. This is a hurdle that must be overcome if EHAs are to fulfill their promise in demanding applications. Further research into better flow models is crucial for achieving optimal control and maximizing the benefits of these advanced technologies.
Electrohydrostatic actuation (EHA) systems, particularly those with energy recovery capabilities, are increasingly being seen as a way to improve efficiency by merging electric and hydraulic control methods. Recent developments in valve-controlled EHA systems show that flow output can be regulated with electrical signals that adjust the size of the opening in a solenoid valve. However, the throttling that occurs in these valve-controlled systems can lead to efficiency losses, requiring additional oil sources for optimal performance.
There's a growing interest in building large-flow EHA systems, particularly those using bidirectional dual magnetostrictive rods for position control. This area is ripe for further investigation. The use of piezoelectric-hydraulic pumps with active valves is being explored in niche applications like helicopter flaps, highlighting the wider range of potential uses for EHA technologies.
Researchers are also exploring hybrid actuator designs combining electric and hydraulic components. These hybrid designs are a fascinating area as they could reduce both energy consumption and system weight, potentially boosting performance. One major hurdle that researchers are grappling with is accurate flow modeling in electric hydrostatic pump units. This is a challenging issue because accurate modeling is crucial for properly controlling electro-hydraulic servo pump systems.
EHA is becoming more common in aerospace, aligned with the “More Electric Aircraft” (MEA) design philosophy. A newly introduced load sensing electrohydrostatic actuation (LSEHA) system promises improved dynamic performance with less heat generation, which is particularly beneficial under heavy load and slow speed conditions. However, I remain curious about its practical efficacy in the field.
It's becoming clear that the valve plate design in bidirectional axial piston pumps needs to be carefully optimized. This is important for getting the best performance out of EHA systems for both military and civilian aircraft. It'll be interesting to see what improvements emerge as this area of research develops further.
The push towards more precise and efficient hydraulic control through these new EHA system developments raises concerns about the trade-off between increased system complexity and ease of use. Balancing innovation with practicality will be crucial for wider adoption. Similarly, the potential energy savings claimed for some EHA designs remain to be seen in real-world settings, and further testing is needed to validate these claims.
The move towards more complex EHA systems and the integration of digital controls presents both opportunities and challenges. The long-term durability of materials used in these systems, especially in harsh environments, needs to be rigorously investigated. Further, the reliability of new sensors used to monitor performance and the need for standardized communication protocols across different systems are open questions that will need solutions. It's a complex landscape that requires continued investigation to ensure that the promising advances in EHA technology translate into meaningful improvements in a variety of engineering applications.
Recent Patent Analysis Advancements in Bidirectional Hydraulic Pump Design for Enhanced Flow Control Systems (2024) - Valve Plate Engineering Solutions for Reduced Discharge Pulsation
Recent patent activity indicates a growing focus on refining valve plate designs within bidirectional hydraulic pumps to minimize discharge pulsations. This focus is driven by the need for enhanced flow control, particularly in demanding applications like aerospace. While past research often centered on unidirectional pumps, the unique challenges posed by bidirectional designs are now being directly addressed.
Innovations like carefully shaped valve plate slots and the integration of damping features, such as triangular grooves, demonstrate a move towards more sophisticated structural solutions to reduce pressure fluctuations. The idea is to achieve smoother flow and reduce the inherent pulsing associated with these pumps. There's also a growing interest in exploring alternative valve plate geometries like spherical designs. Advocates for this approach suggest it can address issues related to oil film distribution, leading to further improvements in pulsation control.
However, it's vital to remember that the claims made in these patents must be rigorously verified through real-world testing. It's not always easy to translate promising theoretical designs into practical applications, especially when it comes to complex hydraulic systems. Many factors, including operating conditions and the specific application, influence the efficacy of any valve plate engineering solution. This area requires further investigation and experimental validation before we can confidently conclude the true impact of these new designs. The optimization of key parameters impacting valve plate dynamics is also central to this discussion, but this area is still under development.
Bidirectional axial piston pumps are increasingly important, especially in applications like flight control systems, where precise flow management is critical. A key aspect in achieving this precision is the design of the valve plate, as it heavily influences how fluid is transferred and how much pressure fluctuation occurs. This is important because reducing pressure ripples is crucial for minimizing the pulsations that are sent to the output of the pump. Unfortunately, a lot of the research on valve plate design is focused on unidirectional pumps, which doesn't directly translate to the challenges found in bidirectional pumps. So, there's still a lot of untapped potential to optimize valve plates for these bidirectional systems.
A recent study focused on aerospace pump-controlled cylinders showed that creating a three-port valve plate could help manage both the flow rate and pressure more effectively. They ran simulations using advanced methods to see how the pump would behave under different conditions and showed that changes in the valve plate's structure can improve things. Similarly, the use of triangular grooves on the valve plate surface has been found to reduce pressure oscillations in other pump designs. So, it appears that optimizing the shape of these plates can have a positive effect on the system's overall operation.
The way a valve plate is structured affects many aspects of a pump's performance, and the development of tools like advanced simulations is helping researchers to test design ideas without needing to build every variation. This has revealed the benefits of using a spherical valve plate. Their ability to self-adjust helps counter issues caused by uneven pressure distribution of the fluid, which improves performance. In addition, the fluid leaks that happen in the gap between the valve plate and other components play a role in these pulsations, highlighting that very precise design and manufacturing is needed to get good results.
There's a consensus that research into valve plate design needs to continue. There's a lot more to be explored before we fully understand the best ways to control pressure and flow in bidirectional hydraulic pumps, especially if we're going to make better flow control systems for the future. It's a promising avenue, though the complexities associated with pump design mean we need to be cautious when interpreting the claims of any new designs and that extensive testing will be required to assess any claimed improvements. Developing better valve plate designs is one more piece in the puzzle of creating more efficient and responsive hydraulic systems.
More Posts from patentreviewpro.com: